Die perfekte Verbindung
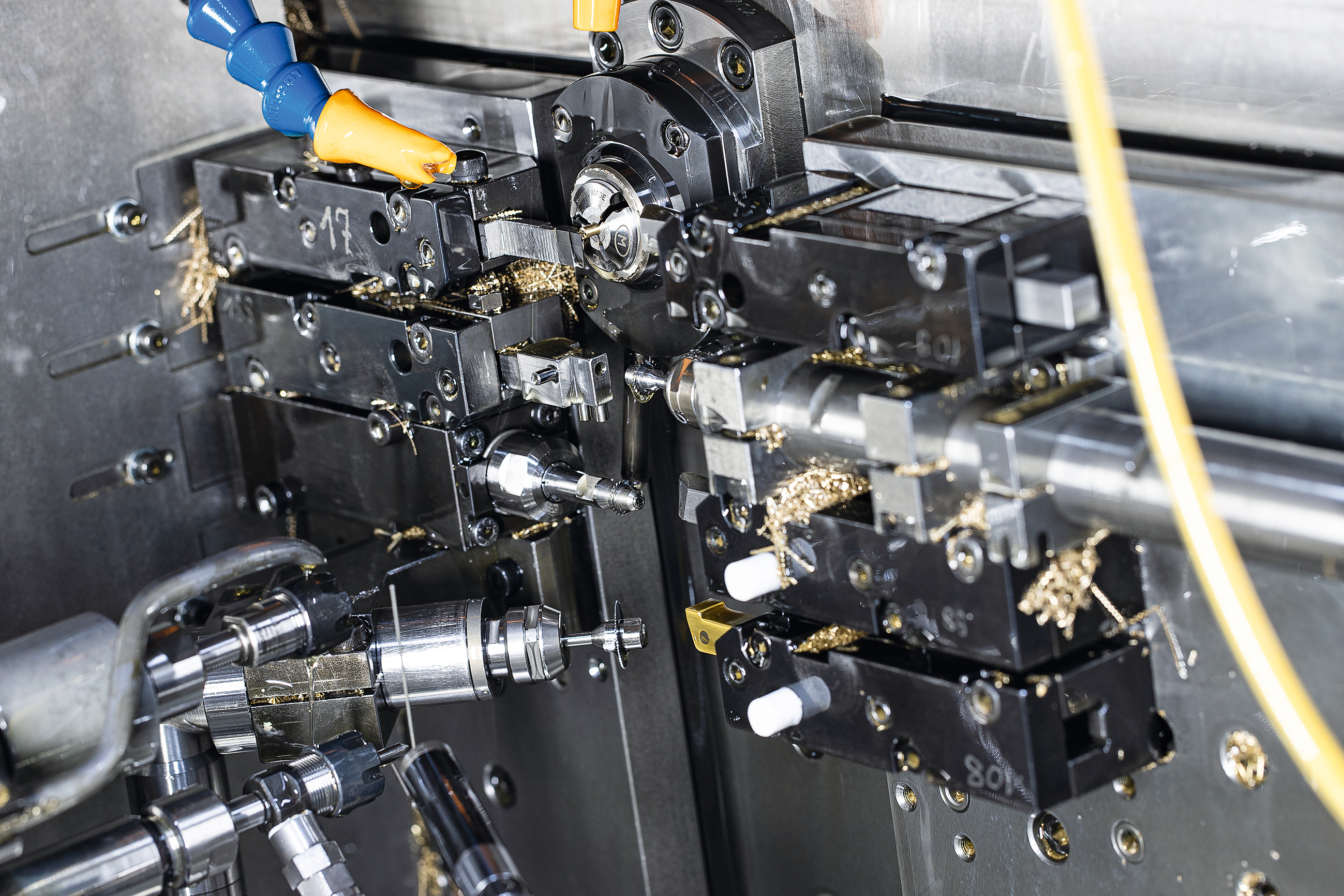
Es war im Herbst 1955. Der Wind fegte das letzte braune Laub von den Bäumen. Als Otto Dunkel beim Laub kehren seinen Strauchbesen beobachtete kam ihm eine geniale Idee. Dies war die Geburtsstunde des Drahtfederkontaktes. Heute zählt die ODU GmbH & Co.KG (Otto Dunkel) zu den weltweit führenden Unternehmen zur Entwicklung und Produktion von Steckverbindungssystemen. Für die Fertigung der Highend-Verbindungen setzt das Unternehmen auf präzise schweizer Maschinen und Werkzeuge der Paul Horn GmbH. Seit rund 20 Jahren arbeiten die beiden Unternehmen eng zusammen, um die anspruchsvollen Zerspanaufgaben für die perfekte Verbindung sicherzustellen. Auch in der Zukunft stehen die Weichen auf eine enge Partnerschaft - gerade in Bezug auf die Zerspanung von bleifreiem Messing und anderen Legierungen.
Analog zu den einzelnen Reisig-Zweigen seines Besens teilte Otto Dunkel die Kontaktflächen in einzelne Federn auf, wodurch sich eine Vielzahl von Kontaktpunkten ergab. Das Ergebnis war eine Revolution: Ein konstanter Übergangswiderstand und gleichbleibender Andruckkontakt. Damit war eine Schwachstelle von Nachrichtensendeanlagen, nämlich der unzuverlässige Steckkontakt, endlich überwunden. Gegründet im Jahr 1942, zählt die ODU Firmengruppe heute weltweit 2.500 Mitarbeiter. Der Hauptsitz des bayrischen Unternehmens liegt rund 80 Kilometer östlich von München in Mühldorf am Inn. ODU liefert die Steckverbindungssysteme unter anderem an die Medizintechnik, Mess- und Prüf-Industrie, Industrieelektronik, Militärtechnik sowie in der Automotive-Industrie. So entwickelte man bei ODU beispielsweise die ersten Hochstrom-Steckverbinder für die Elektromobilität.
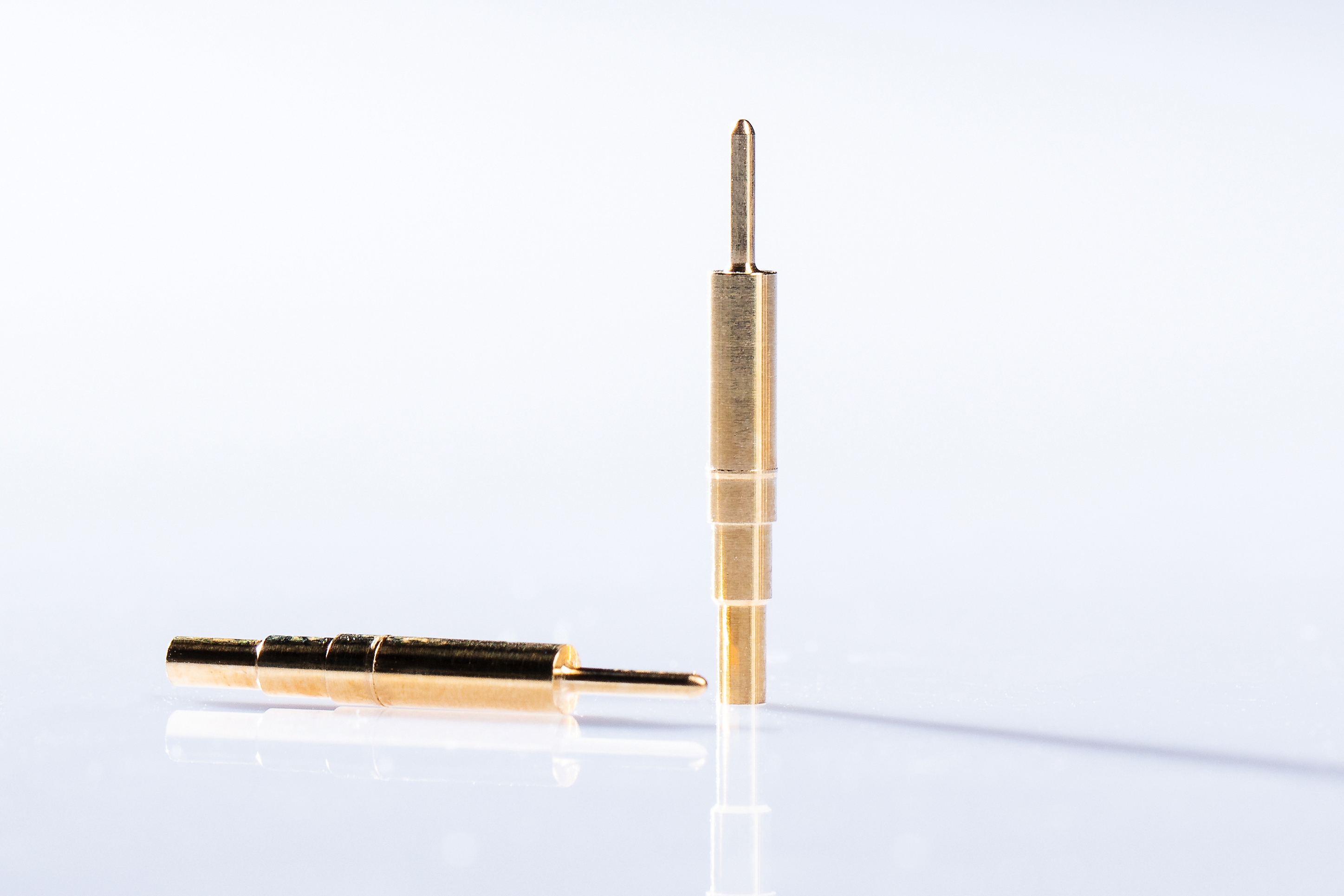
Bei Kontakten ist eine hohe Oberflächengüte ein entscheidendes Qualitätsmerkmal einer Steckverbindung. Quelle: HORN/Sauermann
Werkzeuge von Horn
„Für spezielle Bearbeitungen und Sonderverbindungen haben wir früher unsere Werkzeuge oft selber geschliffen. Bei Stückzahlen von mehreren Hunderttausend pro Jahr benötigen wir jedoch prozessichere und produktive Werkzeugsysteme“, erzählt der ODU-Werkzeugmanager, Tobias Fuchshuber. Die Zusammenarbeit mit Horn besteht seit rund 20 Jahren. Von Anfang an dabei war auch der Horn-Außendienstmitarbeiter Michael Götze: „In der langen Zeit konnten wir schon zahlreiche Zerspanaufgaben bei ODU lösen. Die Mitarbeiter haben auch für neue Werkzeugtechnologien immer ein offenes Ohr und wir können dadurch neue Werkzeuge testen.“ Bei ODU setzt man auf zahlreiche Horn-Werkzeugsysteme. „Die Zerspanungsaufgaben bei uns im Haus sind sehr vielfältig. Mit über 175 Langdrehmaschinen bearbeiten wir Mikrobauteile mit wenigen Zehntel Durchmesser bis hin zu Teilen mit 30 mm Durchmesser“, so Fuchshuber. Werkzeuge von Horn kommen in allen Bereichen zum Einsatz. Vom µ-Finish System S274 zum Langdrehen von Mikrobauteilen, über das Nutstoßen bis hin zum Innenausdrehen und Stechdrehen. Bei ODU verarbeitet man zu 80 Prozent den Werkstoff Messing. Die restlichen 20 Prozent teilen sich in die Werkstoffe Aluminium, Kupfer und Edelstahl auf.
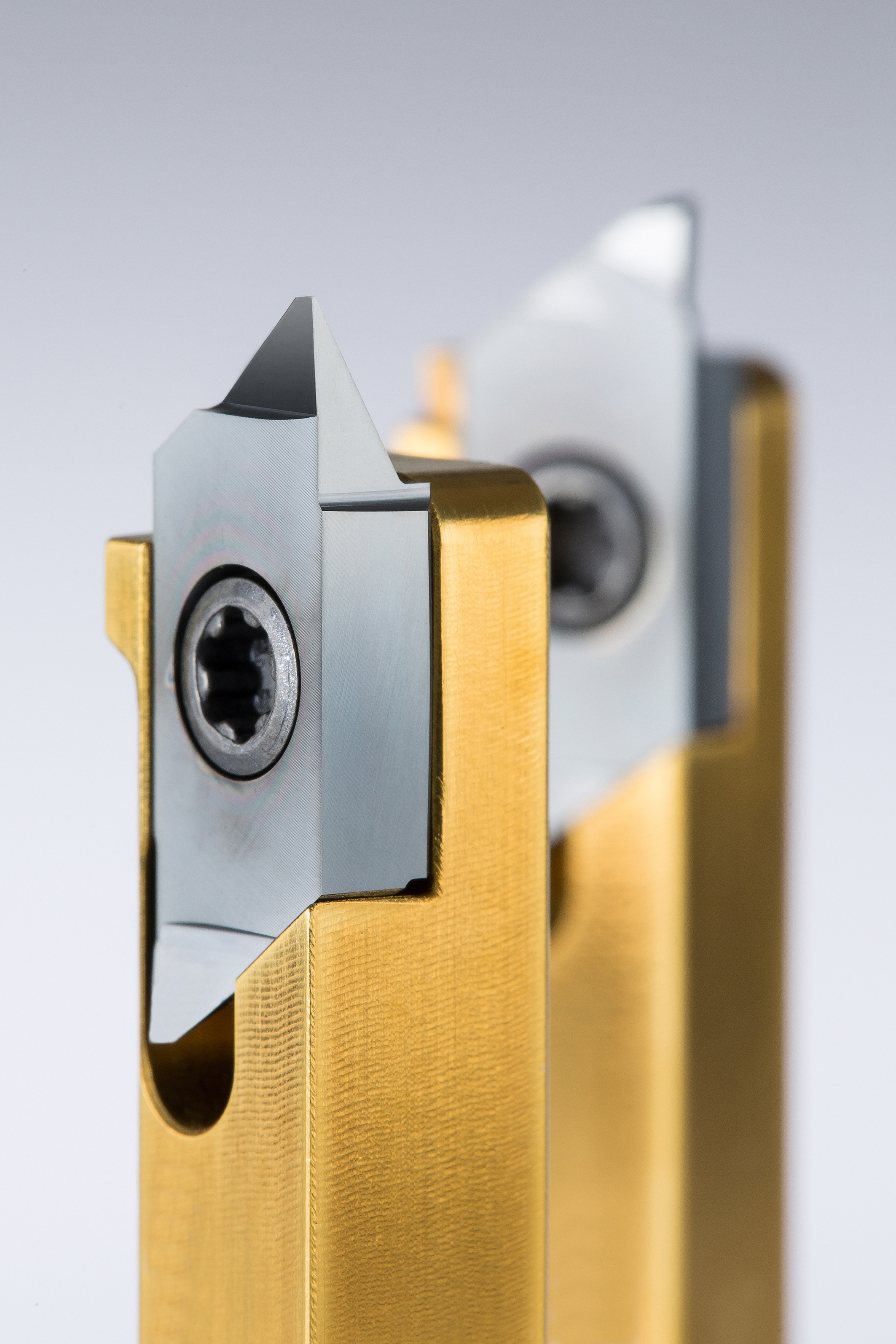
Das System S274 µ-Finish zeigt in der Mikrobearbeitung von Bauteilen seine Stärken.Quelle: HORN/Sauermann
Auf die Oberfläche kommt es an
Gerade bei Kontakten ist eine hohe Oberflächengüte ein entscheidendes Qualitätsmerkmal einer Steckverbindung. Für die Drehbearbeitung von Kontaktstiften setzt man bei ODU unter anderen auf das Horn-Werkzeugsystem S274 in der Variante µm-Finish. Der Schliff einer scharfen und nahezu makellosen Werkzeugschneide erfordert viel an Know-how. Schleifscheiben mit feinsten Körnungen, spezielle Schleiftechniken und ein Mikroskop mit 400-facher Vergrößerung sind nötig, damit das Werkzeug im späteren Einsatz die geforderte Leistung bringt. Dabei unterliegt jede gefertigte Charge des µ-Finish Systems einer 100 Prozent-Kontrolle. Wichtige Kriterien der Qualitätssicherung sind die eng tolerierte hohe Oberflächengüte der Span- und Freiflächen, die Spitzenhöhe und insbesondere die Schartigkeit der Schneidkante. Hierbei gilt: Unregelmäßigkeiten an der Schneidkante über 0,003 mm sind bei dem µ-Finish System schon außerhalb der Toleranz.
Für die Herstellung einer Kupplung eines Drahtfederkontaktes suchte Fuchshuber nach einer neuen Werkzeuglösung. „Das Problem bei der Bohrung des Bauteils liegt an der besonderen Form des Bohrungsgrundes“, erzählt Fuchshuber. Das Messing-Bauteil fertigt man bei ODU in sieben verschiedenen Varianten. Vom Bohrungsdurchmesser 1,43 mm bis 3,6 mm. „Vor der Umstellung auf das Horn-Werkzeug haben wir die Bohrungen vorgebohrt und danach mit einem selbst geschliffenen Werkzeug ausgedreht“, so Fuchshuber.
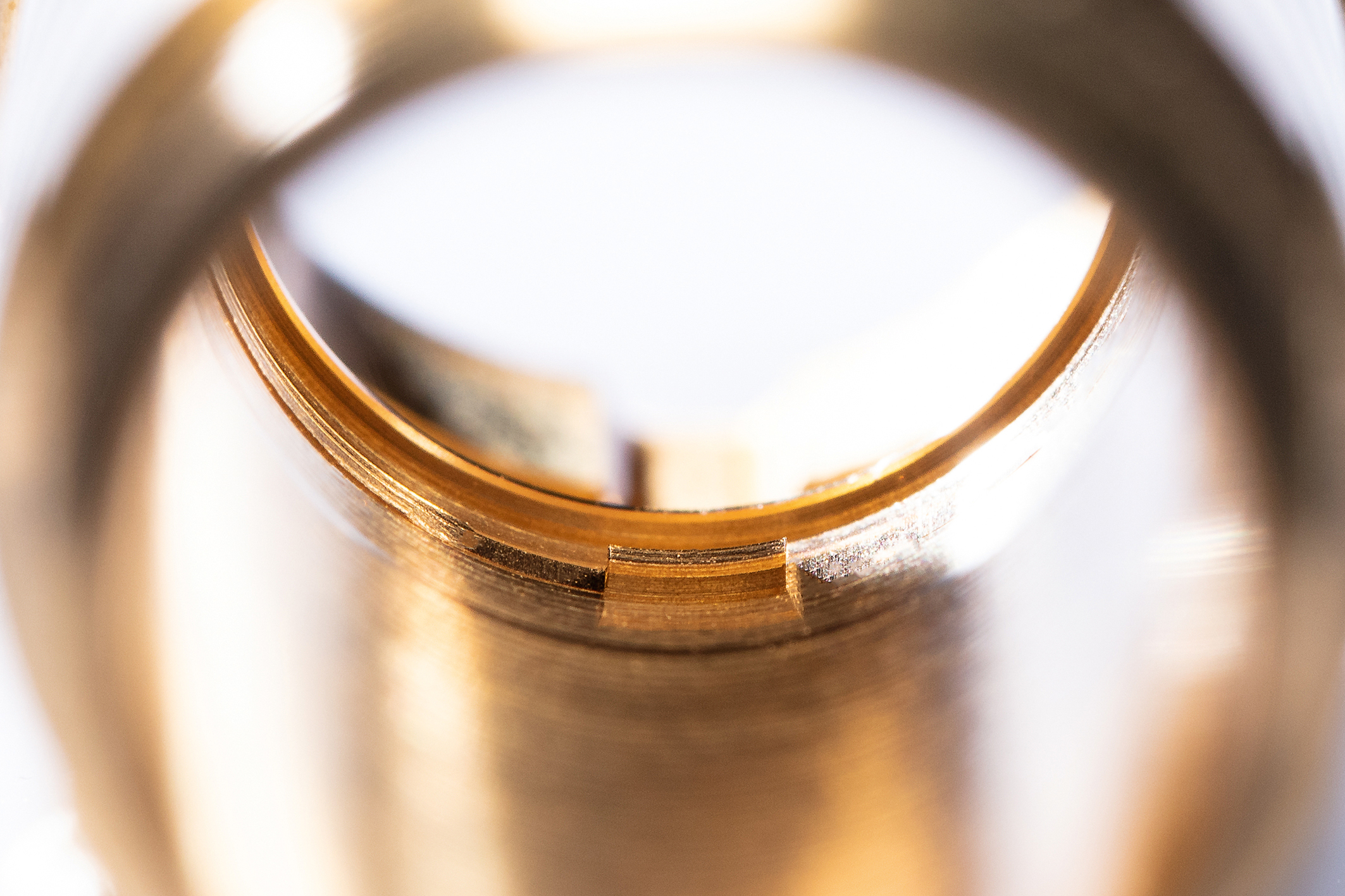
Das Stoßen der Positioniersicke war eine Herausforderung in der Werkzeugauslegung. Quelle: HORN/Sauermann
DS-Fräser mit Sonderform
In der Serienfertigung traten jedoch Probleme durch den gestörten Spanfluss auf. Darüber sah man bei der Bearbeitungszeit das Potential zu einer Optimierung. Bei mehreren Hunderttausend Teilen pro Jahr ein entscheidender Faktor. Die Lösung brachte Horn mit dem Frässystem DS mit innerer Kühlmittelzufuhr. Die Fräser sind mit einer Sonderform geschliffen. Durch das einmalige Eintauchen ins Volle wird die Bohrung mit der speziellen Form am Bohrungsgrund gefertigt. Alle der sieben Fräservarianten sind schleifscharf und unbeschichtet. Durch die Umstellung auf die Fräswerkzeuge ergab sich zum einen die Einsparung eines Arbeitsganges und zum anderen die Erhöhung der Prozesssicherheit durch den kontrollierten Spanfluss. Darüber hinaus konnte die Bearbeitungszeit deutlich verkürzt werden. „Die Umstellung der sieben Varianten dauerte nur rund zwölf Wochen. Die Reaktionszeit sowie die kurzen Lieferzeiten von Horn verkürzen die Umstellungen unserer Bearbeitungsprozesse merklich“, so Fuchshuber. Für die Fertigung des Bauteils setzt Fuchshuber auf eine Tornos Langdrehmaschine des Typs DECO 10.
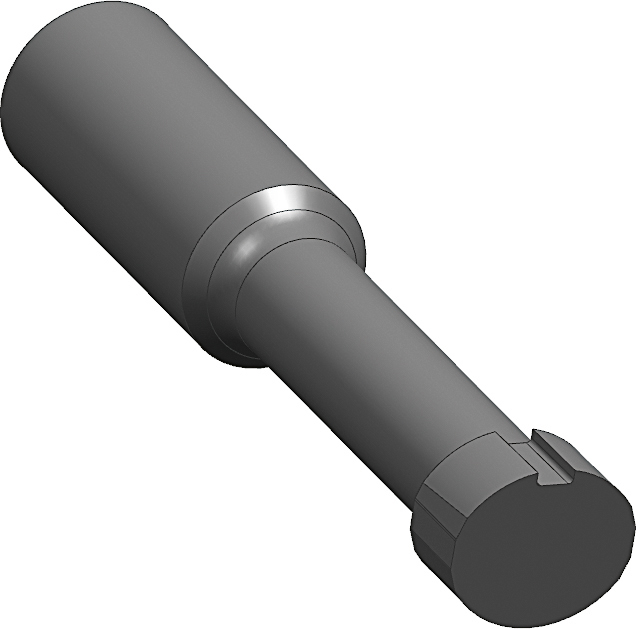
Das Sonderwerkzeug zum Stoßen der Positioniersicke. Quelle: HORN
Bei der Zerspanung einer Gehäusebuchse kommen weitere Sonderwerkzeuge von Horn zum Einsatz. Für zwei Axialeinstiche setzt Fuchshuber auf das System Supermini des Typs 105. Die Einstiche haben die Durchmesser von 11 mm und 7,7 mm. Das Spezielle ist, dass zwischen den beiden Einstichen ein dünnwandiger Steg von 0,2 mm stehen bleiben muss. Die geforderten Toleranzen sind sehr eng. Auch hier kommt ein auf die Anwendung in Messing optimiertes Sonderwerkzeug zum Einsatz. Das Werkzeug ist schleifscharf, unbeschichtet und mit einer polierten Spanfläche. Im inneren des Drehteils stößt ein Werkzeug des Typs Supermini eine 20 mm lange Codiernut. Die Nut dient dazu, dass der Stecker nur in einer Position in die Buchse geschoben werden kann. Die 1 mm tiefe Nut wird in vier Hüben fertig gestoßen. Am Ende der Nut dient ein Inneneinstich als Auslauf des Stoßwerkzeugs. Dieses Bauteil wird bei ODU ebenfalls auf Tornos-Maschinen gefertigt. Hier setzt in der Produktion auf die Maschinentypen des Typs DECO 13 und DECO 20.
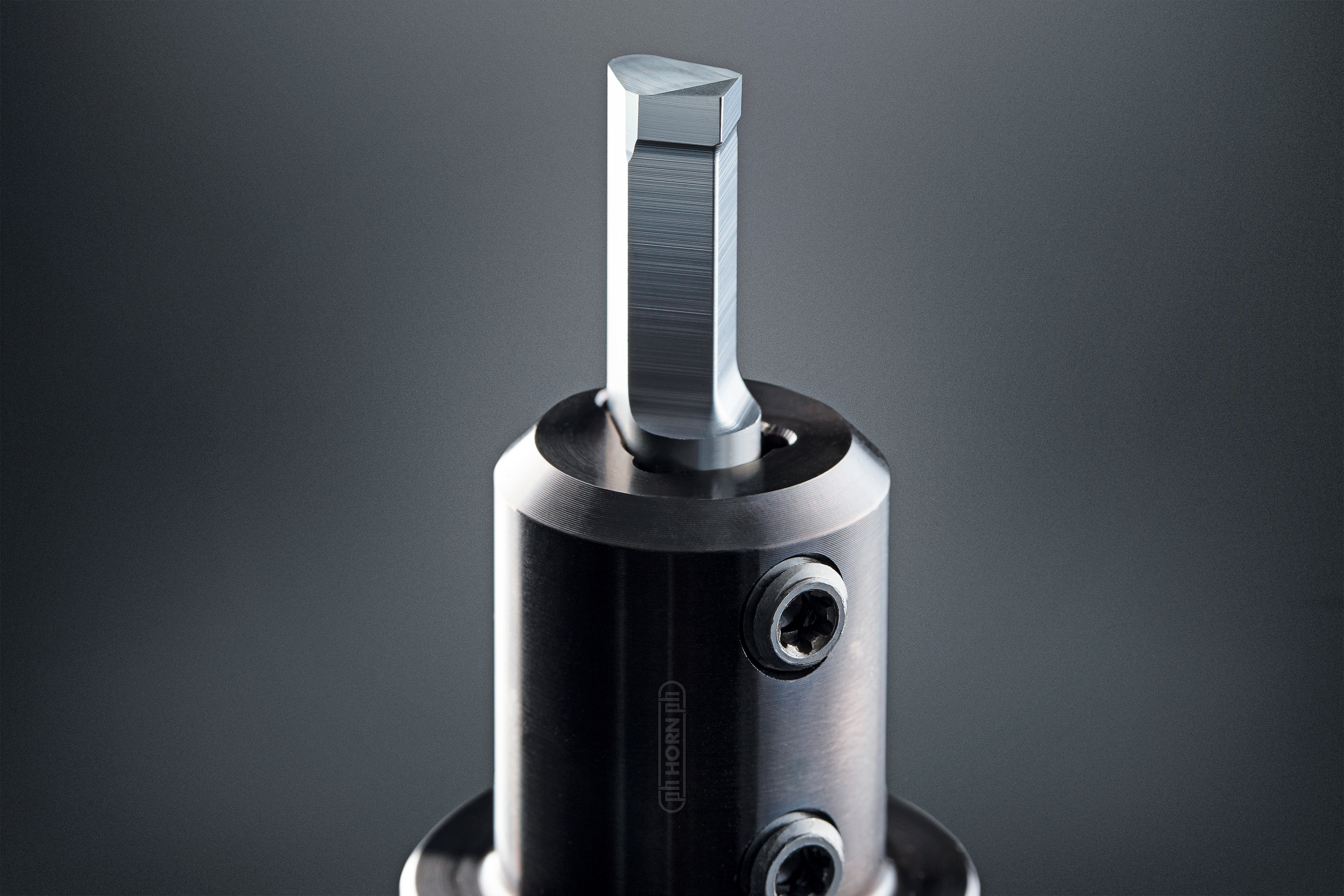
Das Stoßsystem N105 lässt sich auf viele Stoßoperationen anpassen. Quelle: HORN
Stoßen einer Positionssicke
„Für das Stoßen eines Steckergehäuses bekamen wir eine besondere Aufgabenstellung. Hier sollten wir nicht eine Nut stoßen, sondern kreisrund. In dem Durchmesser von 13 mm muss jedoch eine Positioniersicke mit einer Breite von zwei Millimeter stehen bleiben“, erklärt Götze. „Wir hatten die Sicke vorher von außen geprägt. Diesen Arbeitsgang galt es einzusparen“, ergänzt Fuchshuber. Die Lösung brachte ein Stoßwerkzeug mit einer ovalen Form. Auf einer Seite ist die Form der Sicke ausgespart. Zur Bearbeitung wird zuerst innen ausgedreht damit ein Ring stehen bleibt. Dann fährt das Werkzeug in das Werkstück ein und beginnt mit dem Stoßvorgang. Es wird an einer Position angefangen zu stoßen. Sobald der Durchmesser erreicht ist, dreht die Spindel das Werkstück in die neue Stoßposition. Dieser Vorgang wiederholt noch weitere viermal, bis der Innendurchmesser kreisrund ist und die Positioniersicke an der richtigen Stelle stehen bleibt. Die gesamte Bearbeitungszeit für den Stoßvorgang liegt bei rund 20 Sekunden.
Die erfolgreiche Zusammenarbeit zwischen ODU und Horn wächst auch in der Zukunft noch enger zusammen. Gerade im Hinblick auf die Zerspanung von bleifreiem Messing. Durch den Entfall des Legierungsbestandteil Blei wird die Zerspanbarkeit des Werkstoffs entscheidend verschlechtert. Dies stellt Anwender sowie Werkzeughersteller vor neue Herausforderungen. „Bleifreies Messing wird uns in naher Zukunft vor neue Herausforderungen in der produktiven Zerspanung unserer Bauteile stellen. Mit Werkzeugpartnern wie Horn an unserer Seite sehen wir uns dieser Sache jedoch gut betreut“, so Fuchshuber.
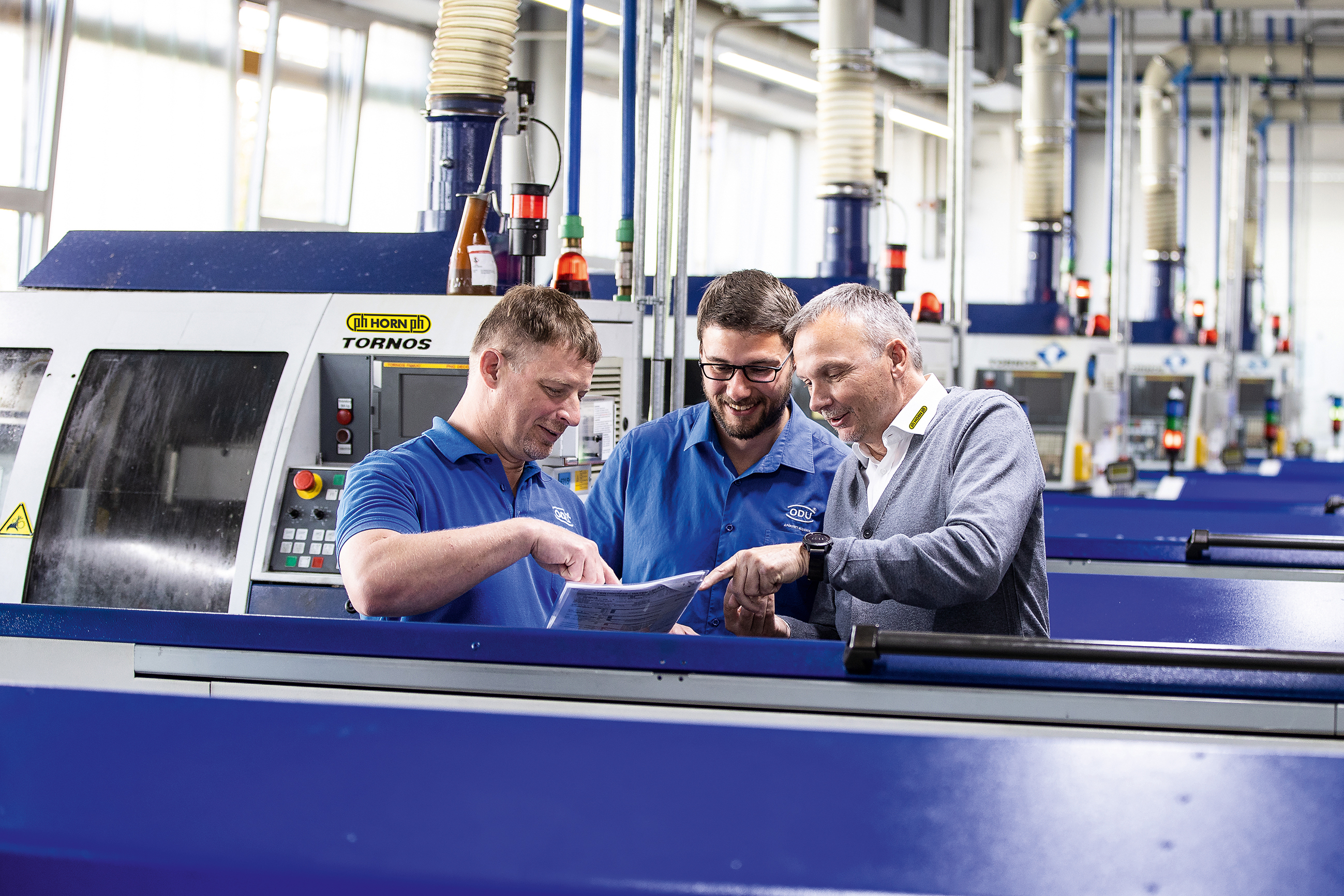
Arbeiten seit 20 Jahren eng zusammen: Peter Ortmaier, Tobias Fuchshuber und Michael Götze. Quelle: HORN/Sauermann
