Digitale Transformation in der Verzahnungsbearbeitung
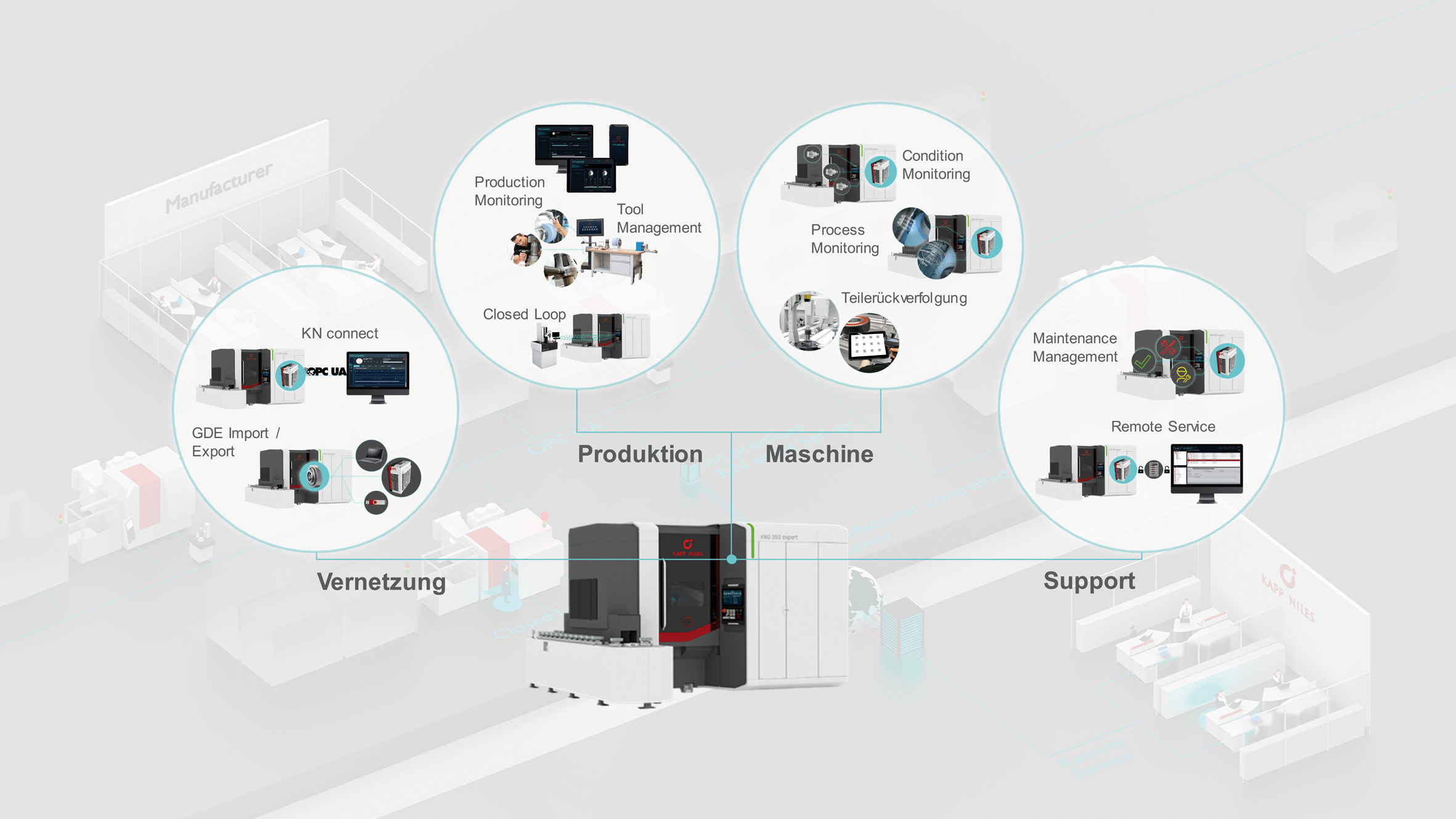
Zeit- und kostenintensive Operationen waren der Auslöser bei KAPP NILES die Digitalisierung, Einzug in Bearbeitungs- und Unterstützungsprozesse halten zu lassen.
Den Rüstprozess auf ein neues Level heben
Rüstvorgänge sind zeitintensiv und bergen die Gefahr von Fehlern. Da Tooling oft vielschichtig eingesetzt wird, ist das Tracking der bearbeiteten Werkstücke oder der Spannzyklen schwierig.
Durch das Kapp Niles Tool Management mit geführten Wechselsequenzen an der Anlage wird der Mitarbeiter Schritt für Schritt durch den Rüstvorgang geführt. Innerhalb der Sequenzen erfolgt die Abfrage zur Identifizierung. Die Maschine erkennt, ob es sich um eine für das Schleifprojekt korrekte Komponente handelt, sodass die geometrischen und prozessrelevanten Informationen an die Steuerung übertragen werden. Über den KN extender werden außerhalb der Maschine alle relevanten Daten der hinterlegten Komponenten in einer lokalen Datenbank abgebildet. (Siehe Bild 1)
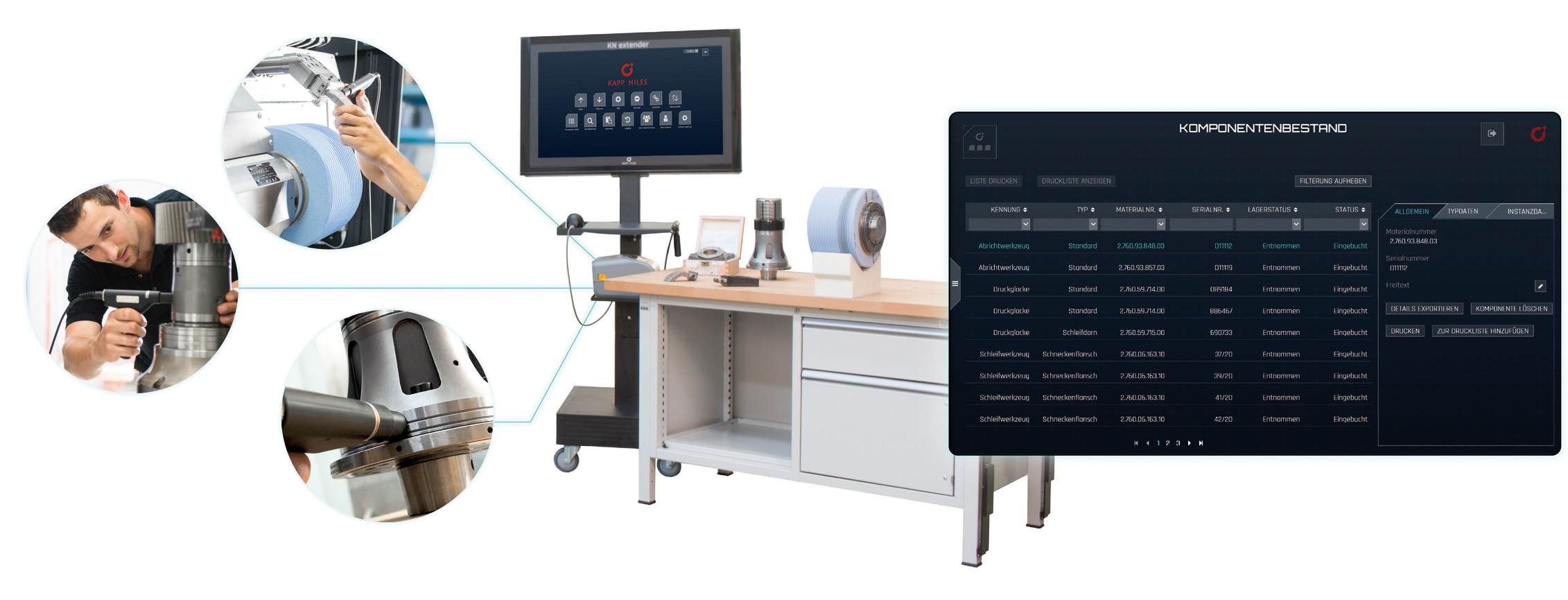
Bild 1: KN extender verwaltet den Komponentenbestand.
Der Einsatz und die Qualität von Tooling können über gespeicherte Daten, wie z.B. Spann- und Abrichtzyklen besser geplant werden.
Transparenz in der Produktion
Gemeinsam mit seinen Kunden hat Kapp Niles einen Weg gesucht, die Overall Equipment Effectiveness (OEE)-Kennzahlen transparent an der Maschine und an mobilen Endgeräten darzustellen. Der Anspruch ist die relevanten KPIs (Key Performance Indicators) übersichtlich und einfach zu visualisieren.
Mit dem so konzipierten Kapp Niles Production Monitoring System lassen sich alle angeschlossenen Maschinen in einem Dashboard darstellen.
Zwei Anzeigen sind auswählbar. (Siehe Bild 2)
Innerhalb der Maschinenübersicht ist erkennbar, welchen Status eine Maschine hat. In der Einzelmaschinenansicht werden überwachte Zustandswerte, OEE-Kennzahlen, relevante Produktionsdaten und die Anzahl der bearbeiteten Werkstücke angezeigt. Die Job-Historie gibt einen Überblick der am meisten genutzten Schleifprojekte. Über das Tooling-Dashboard werden in Verbindung mit dem Tool Management System Informationen zum jeweils im Einsatz befindlichen Tooling visualisiert. Ebenfalls ermöglicht das System eine Übersicht aller anstehenden Serviceanfragen. Ebenso können auch neue Anfragen direkt ausgelöst werden.
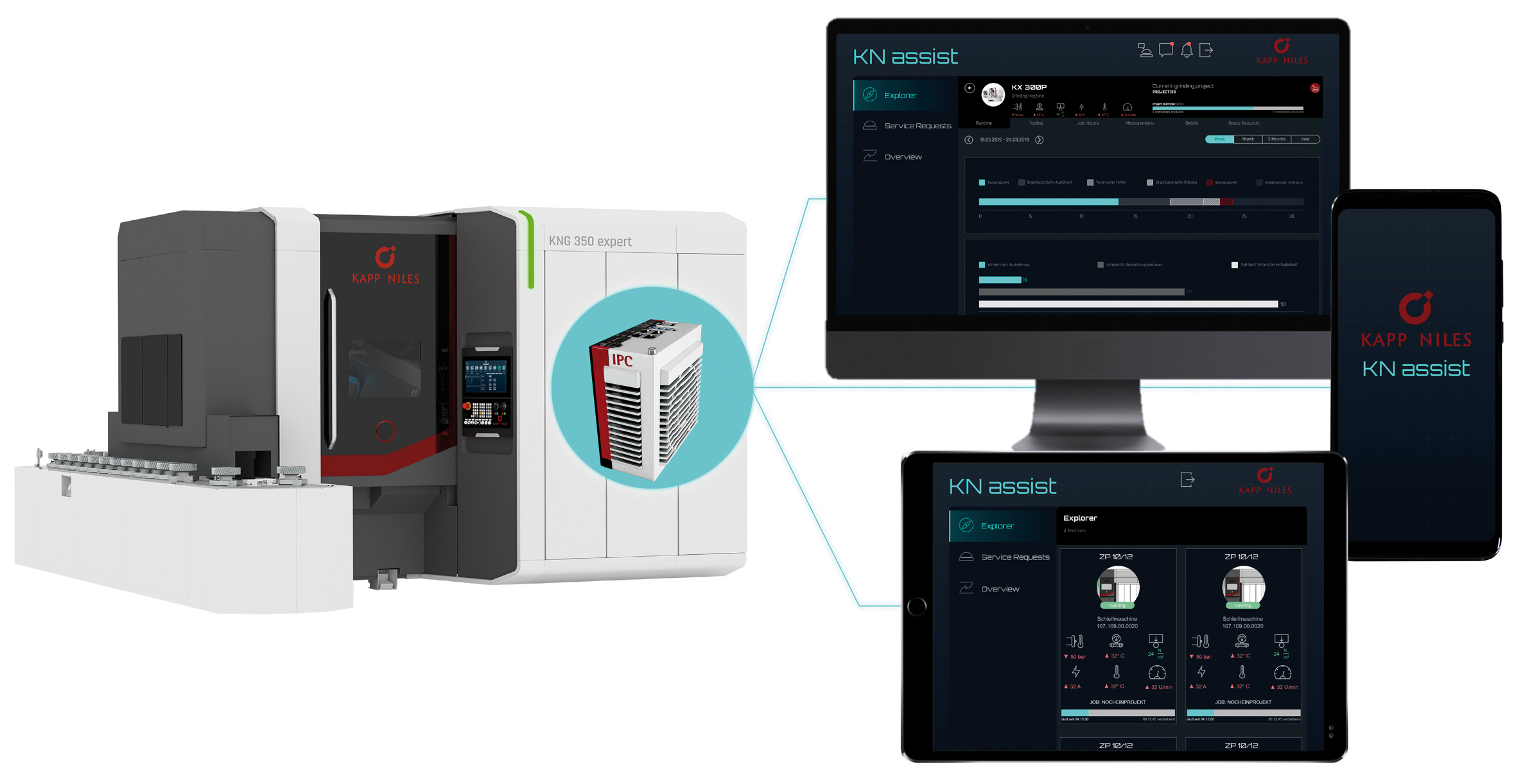
Bild 2: Dashboard-Ansichten.
André Wetz, Produktmanager bei Kapp Niles, beschreibt weitere Vorteile des Production Monitoring Systems. „OEE-Kennzahlen werden einfach zugänglich und anschaulich. Die optimierte Darstellung der KPIs und der am meisten genutzten Schleifprojekte zeigen gezielt Potenziale im Fertigungsablauf und -umfeld auf. Der geräteunabhängige Zugriff auf alle relevanten Produktionsdaten ermöglicht, zu jederzeit und von überall aus, eine transparente Darstellung. Reaktionszeiten können dadurch minimiert werden. Die optimierte Kommunikation führt zu einer schnelleren Problemlösung und dadurch zu geringeren Maschinenstillstandszeiten.“
Überwachung des Bearbeitungsprozesses in Echtzeit
Um den stetig steigenden Qualitätsanforderungen am Bauteil und einer hohen Produktivität Rechnung zu tragen, hat Kapp Niles nach einer Lösung für die Überwachung des Schleif- und Abrichtprozesses gesucht. Auch hier stand das Unternehmen im engen Austausch mit seinen Kunden, um Auffälligkeiten bereits im Prozess zu detektieren und zu vermeiden. Damit wird eine aufwändige 100 %-Prüfung im Nachhinein umgangen.
Mit dem Kapp Niles Process Monitoring System wird der Schleif- und Abrichtprozess analysiert. Der Werkzeugzustand wird überwacht und eine Auswertung von Welligkeiten bzw. Ordnungen am Bauteil durchgeführt. Anhand der analysierten Daten wird der Bearbeitungsprozesses ermittelt und am HMI visualisiert. Mittels einstellbarer Grenzen werden frühzeitig Meldungen ausgegeben, welche auf Abweichungen hinweisen. Eine Schnittstelle bietet die Möglichkeit Daten über eine Teilerückverfolgung jedem gefertigten Werkstück mitzugeben. Ebenfalls können über Exportfunktionen Daten außerhalb der Maschine detailliert analysiert werden. (Siehe Bild 3)
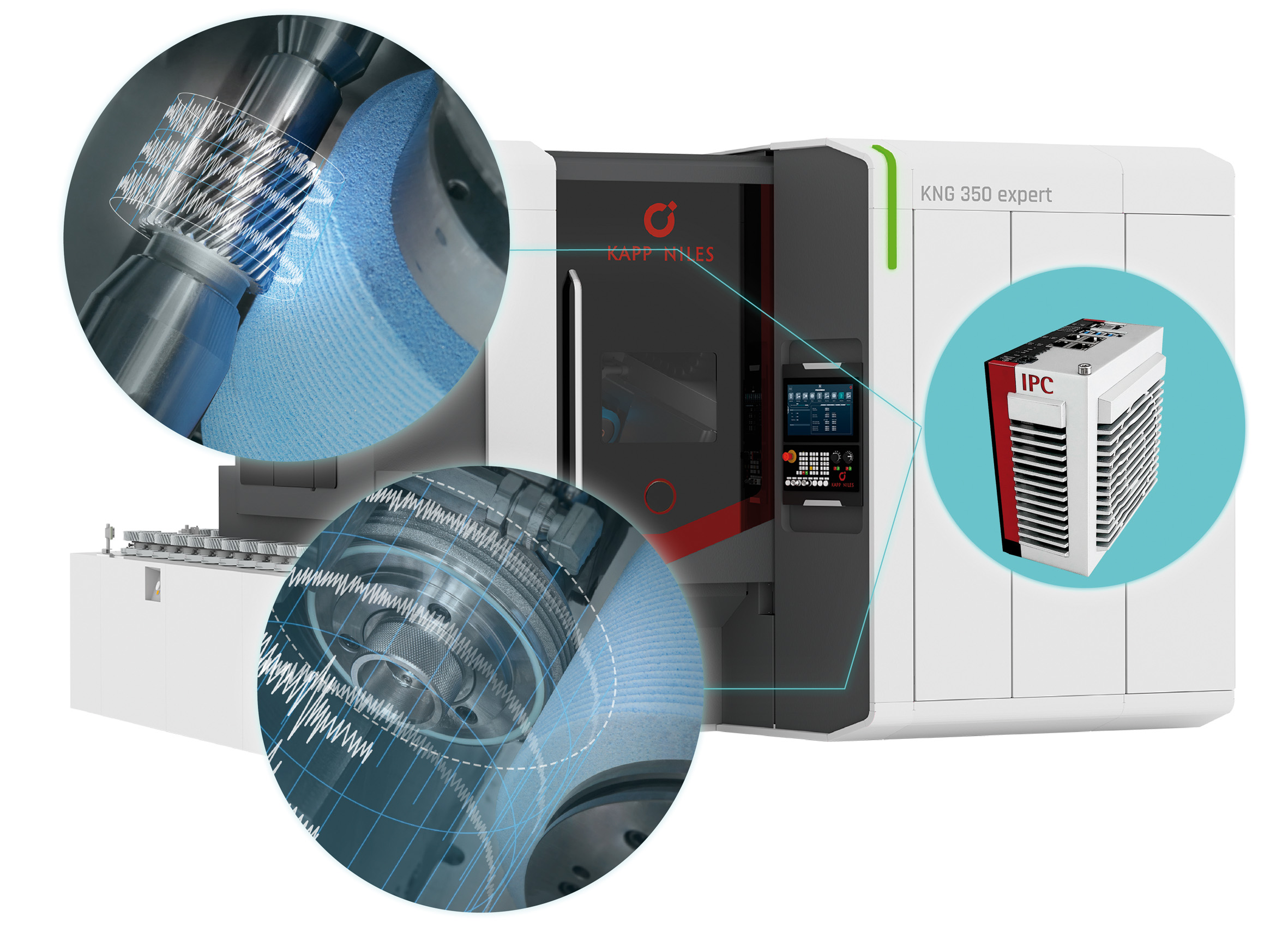
Bild 3: Exportfunktionen erleichtern die Analyse von Maschinendaten
Andreas Paatz, Bereichsleiter Service und Werkzeuge bei Kapp Niles, erläutert: „Dieses System gewährleistet eine umfassende Prüfung einschlägiger Merkmale während des Schleif- und Abrichtprozesses. Dadurch können Fehler oder Trends frühzeitig erkannt und Ausschuss- sowie Nacharbeitsquoten reduziert werden. Durch die Überwachung des Bearbeitungsprozesses können ebenfalls Rückschlüsse über den Zustand der Maschine gewonnen werden. Ein weiterer Vorteil ist, dass ein Ausschleusen von geräuschauffälligen Werkstücken nach dem Bearbeitungsprozess ermöglicht wird. Mittels Teilerückverfolgung besteht die Möglichkeit, kritische Werkstücke auch rückwirkend zu detektieren. Da die Anzahl der nachträglich zu messenden Werkstücke reduziert werden kann, wird eine Zeit- und Kostenersparnis erreicht.“
Von der Prävention zur Prädiktion
Tritt ein ungeplanter Maschinenstillstand auf, kann dieser je nach Ursache große Auswirkungen auf verschiedene Faktoren wie Produktivität und die Termintreue haben und letztendlich Mehrkosten nach sich ziehen. Das Kapp Niles Condition Monitoring System überwacht den Verschleißzustand der linearen und rotatorischen Achsen der Bearbeitungsmaschine. Durch gezielte Referenzfahrten wird während des Betriebs der Maschine der Zustand aufgenommen. Der Verschleißgrad der Achsen wird visuell am HMI der Maschine dargestellt. Neben einer Prognose der Lebensdauer werden durch voreingestellte Grenzen Trends an der Maschine ausgegeben. Schnittstellen zur Übertragung von relevanten Daten an weitere kundenspezifische Produktionssysteme sind vorhanden. Des Weiteren können die Daten über eine Teilerückverfolgung jedem gefertigten Werkstück mitgegeben werden. Zur Überwachung der Achsen wird analog zum Process Monitoring System die Maschine mit zusätzlicher Sensorik und einem leistungsstarken IPC zur Auswertung der aufgenommenen Daten ausgestattet. (Siehe Bild 4)
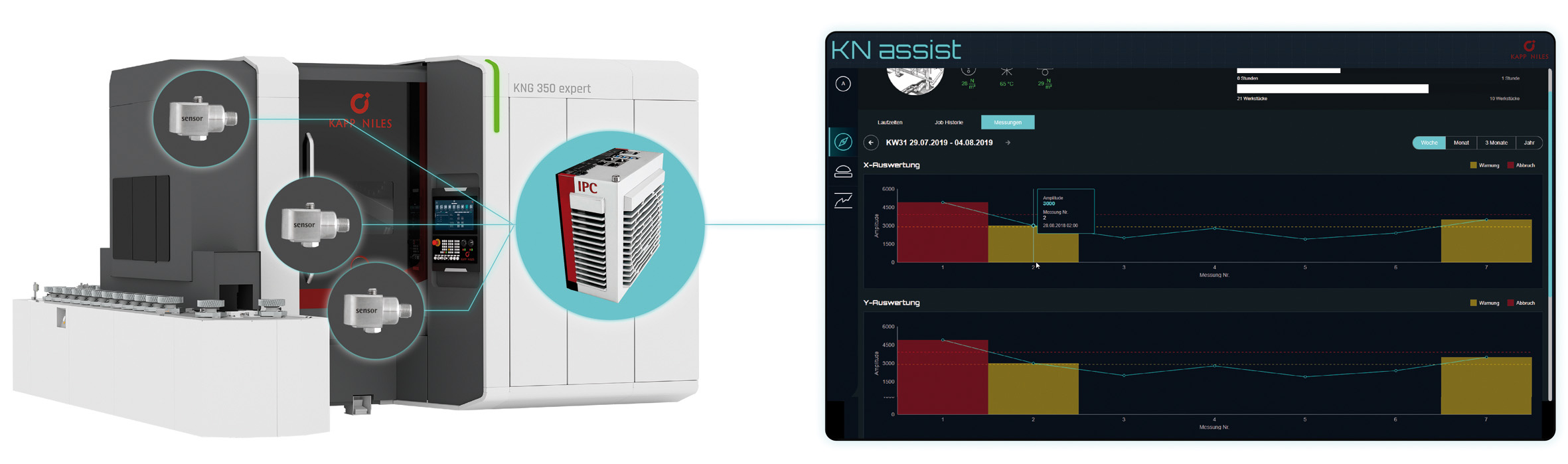
Bild 4: Leistungsstarker IPC wird für das Monitoring eingesetzt.
Andreas Paatz: „Ziel ist es, ungeplante Maschinenausfallzeiten signifikant zu reduzieren. Das ermöglicht eine bessere Planung von Instandhaltungsintervallen und verhindert einen unnötigen oder verfrühten Tausch von Maschinenkomponenten. Begründet wird dies dadurch, dass weniger Verschleißteile auf Vorrat gehalten werden müssen und zustandsbasiert bestellt werden können. Der Trend in modernen Produktionsbetrieben geht zu zustandsorientierter Wartung und Instandhaltung. Kapp Niles bietet hier ein leistungsfähiges Produkt.“
Instandhaltung transparent machen
Unvorhergesehene Wartungseinsätze machen das Leben schwer. Unkalkulierbarer Produktionsausfall kann zu verringerter Produktivität und erhöhten Kosten führen. Ist eine Wartung notwendig, führen fehlende Informationen zu Mehraufwand.
Mit dem Maintenance Manager von KAPP NILES werden alle Wartungspläne und -anleitungen in digitaler Form abgebildet. Die Datenbank bietet ein komplettes Wartungsmanagement mit Trigger, Verbrauchsmaterialien, Zeitaufwänden, Zuständigkeiten und Prioritäten. Dadurch wird eine nutzungsbasierte Wartung ermöglicht. Über eine Ampelfunktion werden die fälligen Wartungen angezeigt. Alle durchgeführten Aktivitäten werden im Anlagenarchiv hinterlegt.
Dieses Archiv (Siehe Bild 5) dient als Unterstützung bei der Planung für Instandhaltungsprozesse.
Kapp Niles bietet mit der Softwareplattform KN assist eine praxisnahe Lösung. Hauptaugenmerk wurde auf eine lokale Einbindung aber gleichzeitig auch auf die Möglichkeit zu Schnittstellen in Kundensysteme gelegt. Damit ist eine einfache Installation und Integration in die bestehende Industrie 4.0-Landschaft gewährleistet.
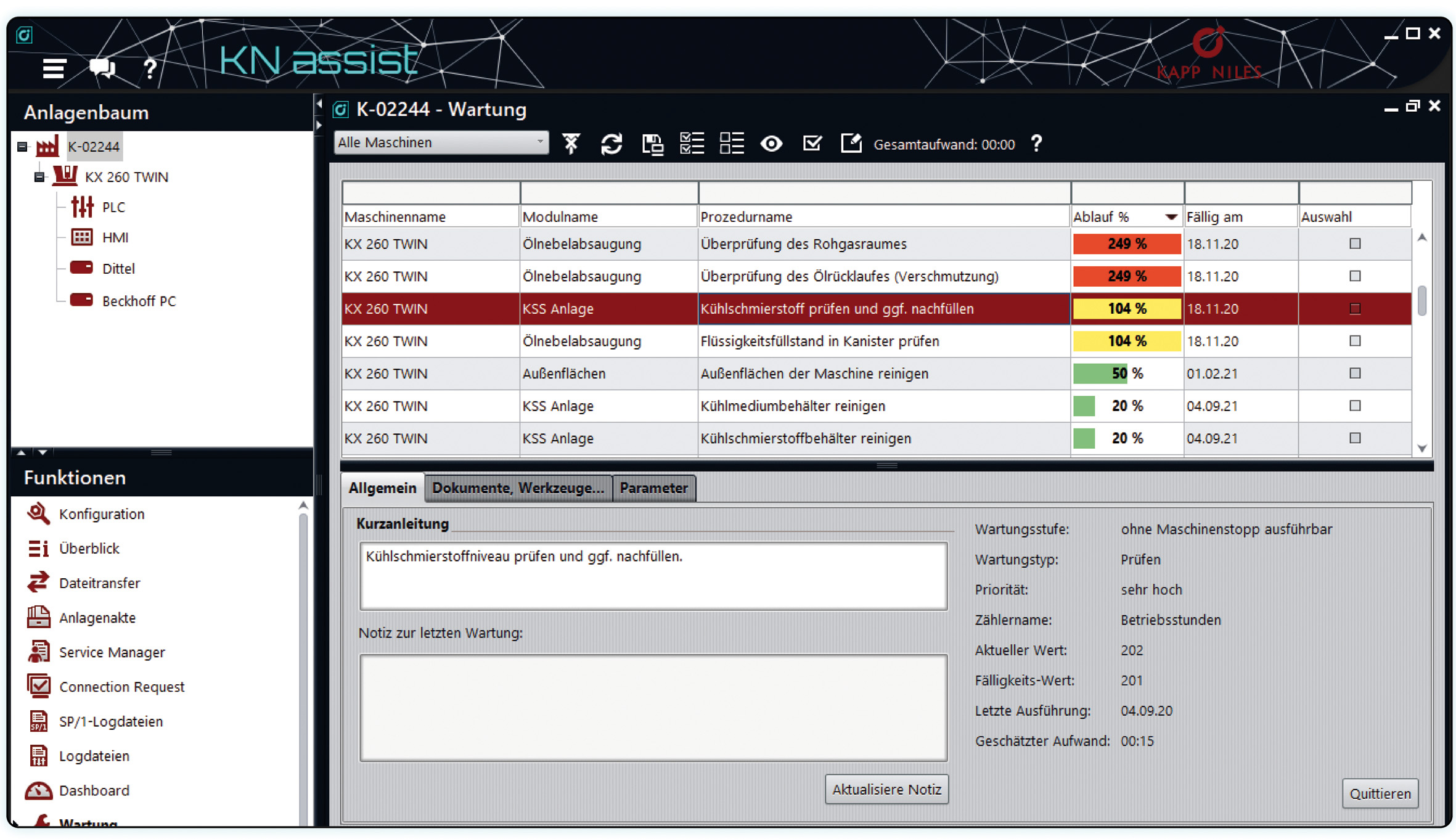
Bild 5: Planungstool für Instandhaltungsprozesse.
