Rapides Testverfahren für Werkzeuge
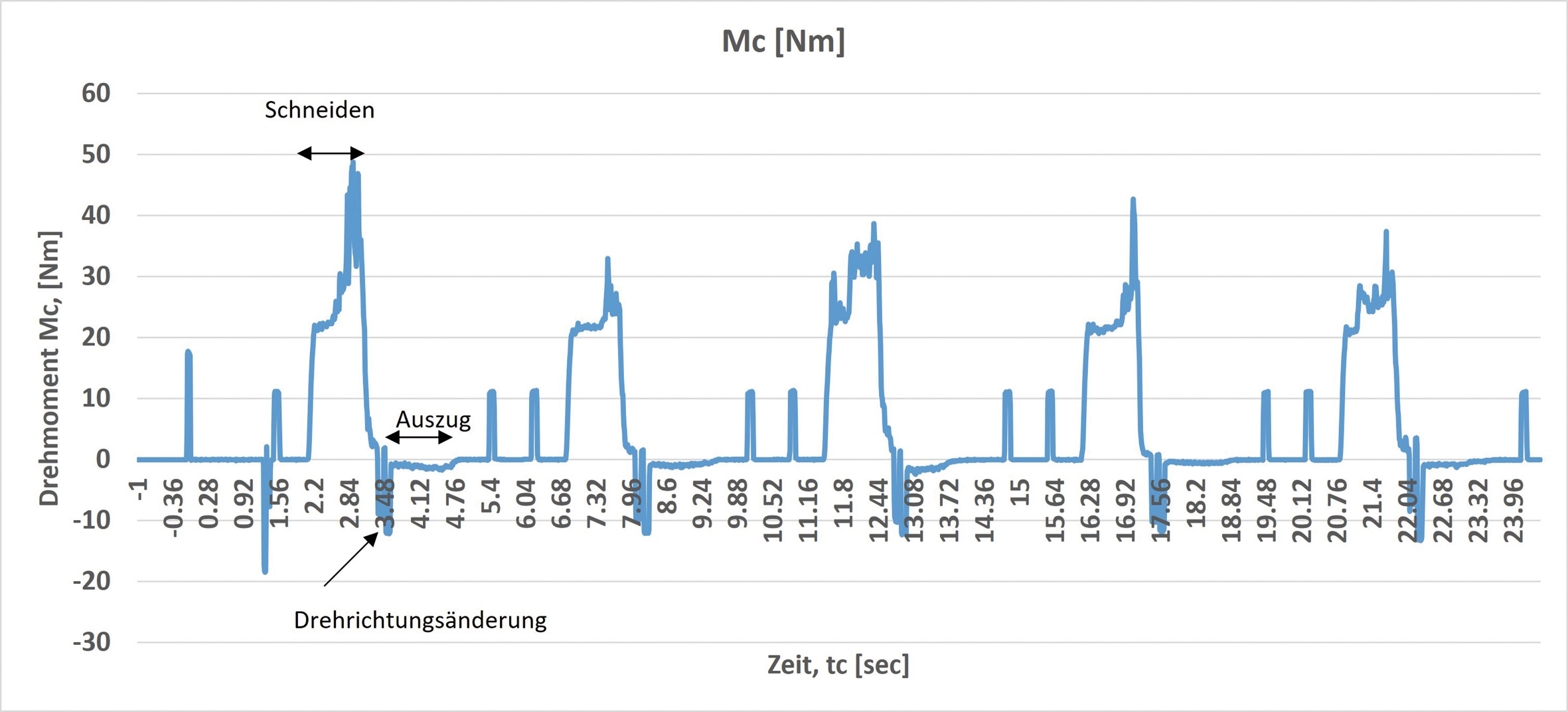
In diesem Beitrag werden wir eine neue Methode vorstellen, die die Wirksamkeit neuartiger Beschichtungen auf Gewindeschneid- und Formwerkzeugen bewertet, ohne langwierige und teure Standzeitversuche [1] fahren zu müssen. Die Methode basiert auf der Messung und Auswertung der gemessenen Kraft- und Drehmomentabläufe während der Zerspanungs- bzw. Formvorgänge (Bild 1 und 2).
- Qualifizierung
der Wirksamkeit von Beschichtungen mit einem komplexen Indikator
Die kurzfristige (schnelle) Qualifizierung rotierender Werkzeuge wird durch den Einsatz von mindestens zwei Werkzeugen (Paaren) gleicher Bauart und durch Herstellung von mindestens 5-5 Flächen (bzw. Gewinden) durchgeführt. Es ist ratsam, die Bohrungen in einem eindeutigen Punktmuster zu platzieren, einerseits zur Kraftmessung, andererseits um die Auswertung der Messmaschine zu beschleunigen, um die Gewindelöcher leichter zu schneiden und Material zu sparen. Mit Ausnahme des unregelmässigen Auftretens von Verschleißprozessen, lassen sich die wesentlichen zur Effizienzmessung geeigneten Effekte bereits während der Bearbeitung messen und analysieren oder registrieren.
Der komplexe Effizienzindex (HKM) ist definiert als Quotient [2]. Im Zähler stehen die positiven Parameter (z.B. Zeitspanvolumen), im Nenner die negativen Faktoren für den Werkzeugbetrieb (hohe Kräfte, geometrische Ungenauigkeiten, ungünstige Spanform, Materialhaftung). usw.). Beim Bohren ist dieser Indikator beispielsweise:
V ‘ – Materialabtragsrate [mm3 / min],
Mc – Drehmomentbedarf [Nm],
Ff – Vorschubkraft [N],
g – Spanformindex
∝1, ∝2, ∝3 – Proportionalitätsfaktoren.
Das Hauptziel unserer aktuellen Untersuchung war herauszufinden, wie die schützende und reibungsmindernde
Wirkung von Schichten unterschiedlicher Zusammensetzung und Schichtaufbau beim Gewindebohren und Gewindeformen nachgewiesen werden kann.
Kurzfristige Tests von Beschichtungen, Auswahl und Quantifizierung von Leistungsparametern gehörten zu den Zielen, da nur eine quantitative Analyse jede Option vergleichen und einstufen kann.
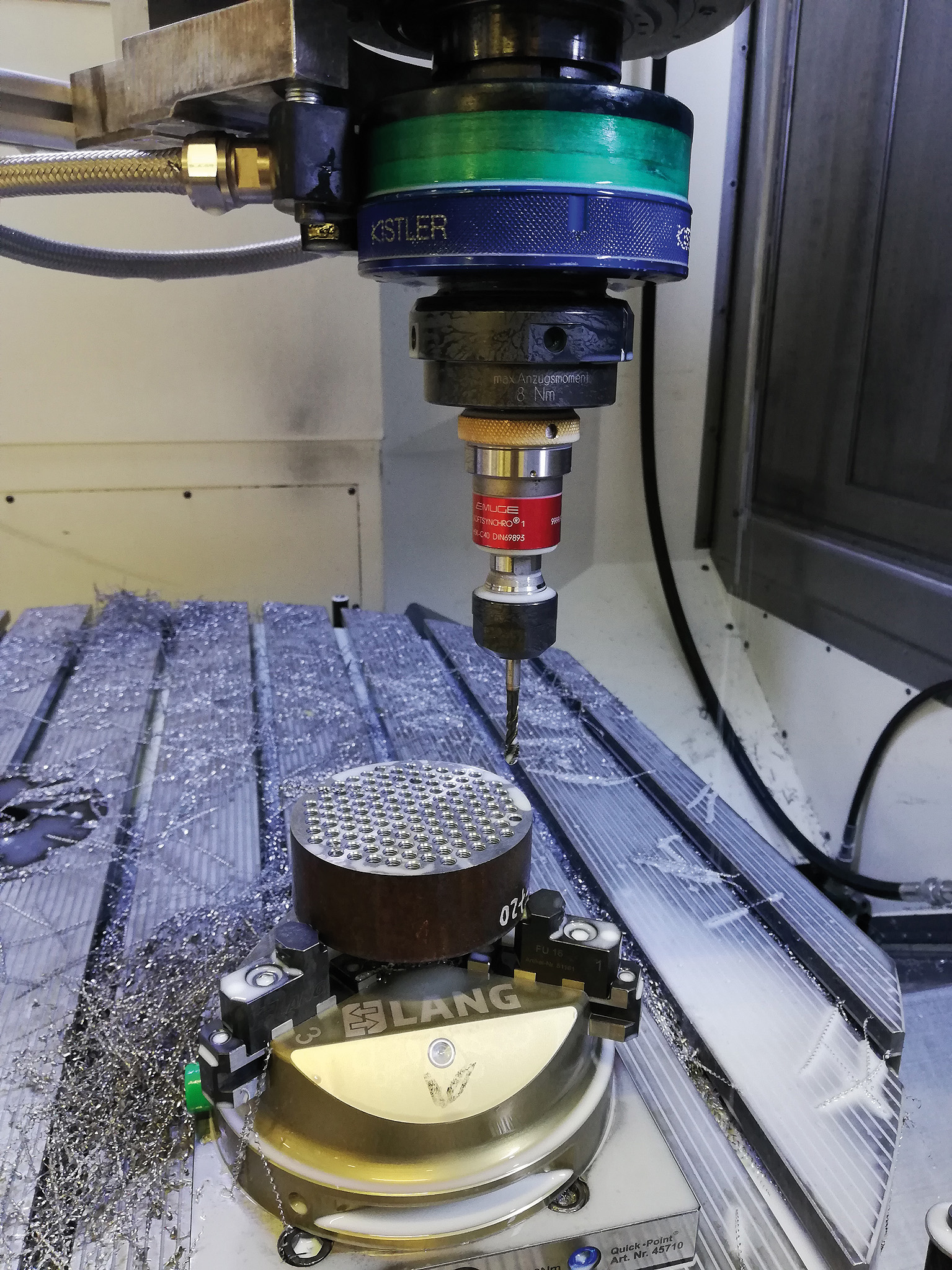
Bild 2
Die Randbedingungen:
- Versuchsort: GFE, Schmalkalden, DE.
- Werkzeugmaschine: DMU 125, vertikales Bearbeitungszentrum.
- Messgerät: Kistler rotierendes 3D-Dynamometer.
- Werkstückmaterial: 42CrMoS4+QT (1.7225), Rm=980 N/mm2, Ø130×13 mm.
- Gewinde: M6x1 (p=1mm) Durchgangsbohrungen.
- Aussenkühlung: Emulsion 7% - 30 l/min.
- Werkzeuge: Emuge HSSE-PM im SoftSynchro Ausgleichsfutter.
- Gewindebohrer: Enorm 1-VS – Code: B050C400.0060, z=3 – 45°.
- Kernloch: Ø5 mm, vc= 15 m/min, n=796 min-1.
- Gewindeformer: InnoForm 1-Z-SN – Code: B521E900.0060GJ, z=4 – 0°.
- Kernloch: Ø5.5 mm – vc= 20 m/min – n= 1060min-1.
Die getesteten Schichten wurden in der Beschichtungsanlage π411PLUS abgeschieden:
- Cr-Ti basierte Nanolayer-Schicht (HUpl = 30 GPa – µ=0.4 – T-max: 600°C).
Im Weiteren: CrTiN-Schicht.
- Ti-Al-Cr-Si basierte Nanocomposite Schicht (HUpl= 40 GPa – µ=0.45 – T-max: 1000 °C).
Im Weiteren: nc-Schicht [3].
- ta-C tetrahedral-gebundener, wasserstofffreier amorpher Kohlenstoff (HUpl = 37 – 50 GPa – µ=0.15 – T-max 400 °C).
- a-C tetrahedral-gebundener, wasser- stofffreier amorpher Kohlenstoff. (HUpl = 30 – 45 GPa – µ = 0.15 – T-max 400 °C).
Als Kantenvorbereitung vor dem Beschichten und nach dem Beschichten wurde Nassstrahlen (Hochdruckluft-/
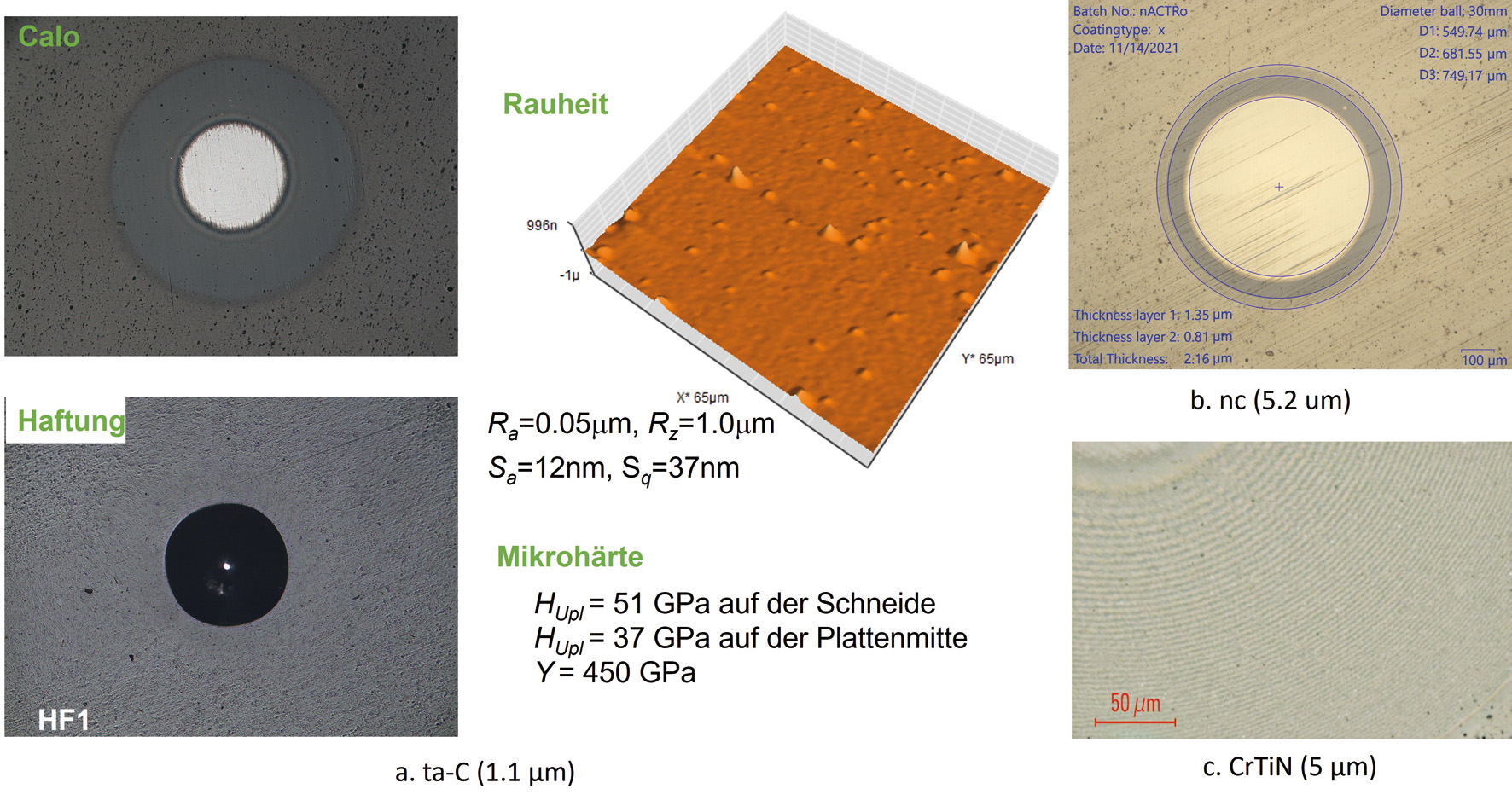
Bild 3: Die Strukturen der 3 Hauptschichten.
Flüssigkeitsdüse) verwendet. Die vier aufgeführten Grundschichten wurden als Basecoat und die DLC-Schichten auch als zusätzliche Deckschichten verwendet. Bild 3 zeigt den Schichtaufbau der 3 Hauptschichten.
Beim Herstellen von Gewinden muss die Spanform nur dann berücksichtigt werden, wenn die gerade genuteten Gewindebohrer Wickelspäne bilden. Bei den von uns getesteten Gewindebohrern mit 45° Steigungswinkel war die Spanform günstig und die Gewindegenauigkeit sehr gut. Selbstverständlich entstehen beim Umformen keine Späne, die Genauigkeit ist günstig und – durch die richtige Kernlochgröße – auch die Ausformung regelmäßig.
Die Effizienz von unseren Testwerkzeugen wird hauptsächlich durch das Eingangsdrehmoment und seine Schwankung (d. h. relative Standardabweichung) beeinflusst. Das für unsere Berechnungen relevante Drehmoment lässt sich aus dem Mittelwert der positiven Drehmomente ermitteln (Bild 1 (Mc)). Der Schwankungswert wird als Normabweichung der gemessenen Drehmomentwerte (sMc) relativ zum Mittelwert (in Prozent) berechnet:
Die Testergebnisse eignen sich zum Vergleich und zur Einordnung von Beschichtungstypen. Die Bewertung endet mit einem Ranking der Effizienz
der einzelnen Schichten.
- Bewertung der Effizienz verschiedener Schichten
2.1 Ergebnisse bei Gewindebohrern
Die Eingangsdrehmomente der 14 Gewindebohrer wurden mit sieben verschiedenen Beschichtungen verglichen und analysiert. Die Ergebnisse sind im Bild 4 dargestellt.
Die Mittelwerte der Drehmomente (Bild 4a) zeigen, dass die einzelnen Basisschichten (nc, ta-C, a-C und CrTiN) und die als Topschichten verwendeten DLC-Schichten (ta-C und a-C) deutliche Unterschiede verursachen. Dies lässt sich nicht nur durch Reibung erklären, sondern auch durch die unterschiedlichen Schichtdicken, durch die Droplets, sowie durch die unzureichend abgedeckten Schleifspuren (Bild. 3b).
Durch die Einteilung der durchschnittlichen Drehmomente in vier Kategorien gemäß der Sturges-Regel (N = 14; Spaltennummer = 4, [4]) erhielten wir, dass die Mehrheit der Werkzeuge (~79%) mit geringem oder sehr geringem Drehmomentbedarf arbeitete (Bild 4b). Nur die Drehmomentverläufe von 3 Werkzeugen können als hoch angesehen werden. Das in Formel beschriebene Histogramm der relativen Standardabweichungen ist ebenfalls durch vier Spalten gekennzeichnet. Acht Werkzeuge (~57%) erwiesen sich als günstig (vMc ≤ 4%), aber fast die Hälfte der getesteten Gewindebohrer zeigte eine große Standardabweichung im Vergleich zu ihrem durchschnittlichen Drehmoment.
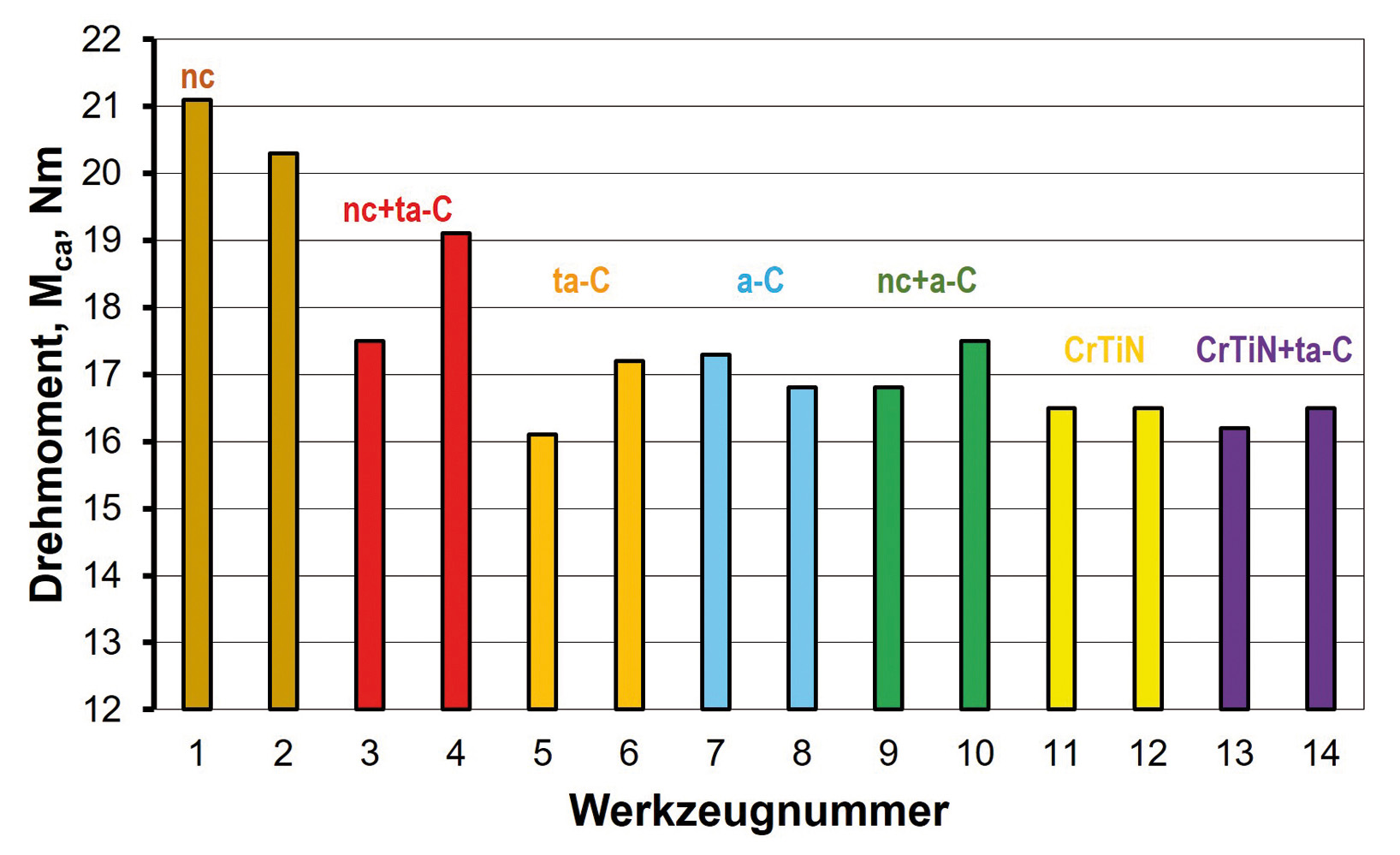
Bild 4: Ergebnisse der Drehmomentuntersuchungen von Gewindebohrern. 4a. Drehmomente beim Gewindebohrer
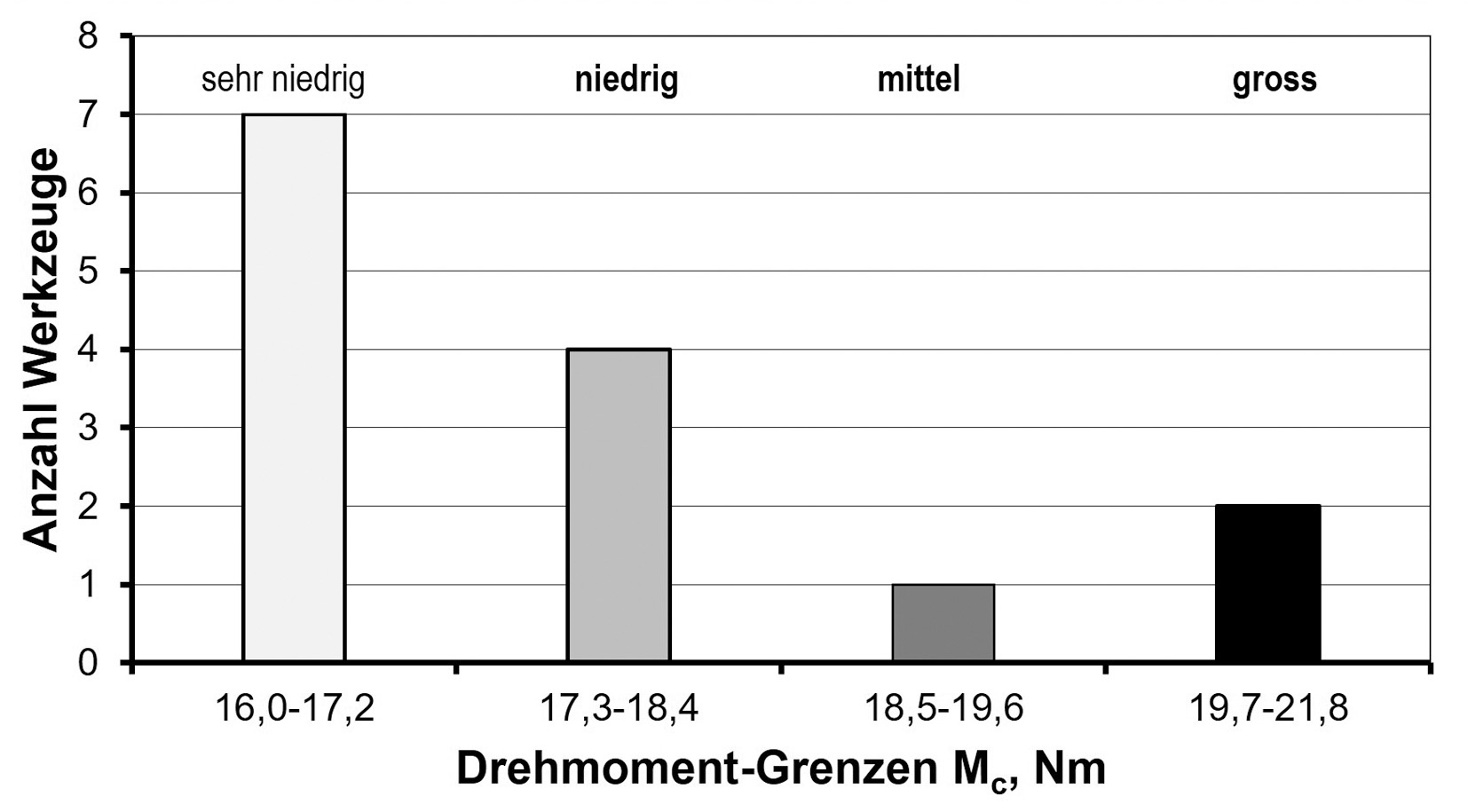
4b. Verteilung der Drehmomente

4c. Verteilung der Streuungen
Zur Bestimmung der Effizienz wird eine „Klassifizierung“ (1 … 4) eingeführt. Das Werkzeug (bzw. die Beschichtungskombination) mit den niedrigsten Werten wird sowohl in Bezug auf die Drehmomente als auch auf die relativen Standardabweichungen als „sehr klein“ bewertet. Dementsprechend ist die Schicht mit der niedrigsten Gesamtbewertung die effizienste. Durchschnittliche Drehmomente werden doppelt gewichtet. Mit dieser Methode lässt sich nicht nur die Leistung jedes einzelnen Werkzeugs ermitteln, sondern gleichzeitig auch die Effizienzreihenfolge zwischen den Beschichtungen ermitteln.
Die Aggregation und Kategorisierung der nach obigem Verfahren errechneten Noten sind im Bild 5 dargestellt.
Aus der Zusammenfassung der erhaltenen Ergebnisse lassen sich folgende Schlüsse ziehen:
- Die Rangfolge der Gewindebohrer-Schichten ist für einige Werkzeuge eindeutig (sehr gut oder sehr schlecht).
Für andere Zusammensetzungen lieferten die Schicht-Paare widersprüchliche Ergebnisse (Bild 5/a).
- CrTiN und seine mit ta-C-überbeschichtete Version sind hochwirksam.
- Die DLC-Beschichtungen und die mit a-C-Deckschicht versehene nc’s sind günstig wirksam.
- Die nc+ta-C erreichte die vierfache Standzeit der nicht überbeschichteten nc-Version. Aber diese blieb hinter den hohen Erwartungen trotzdem zurück (Bild. 5).
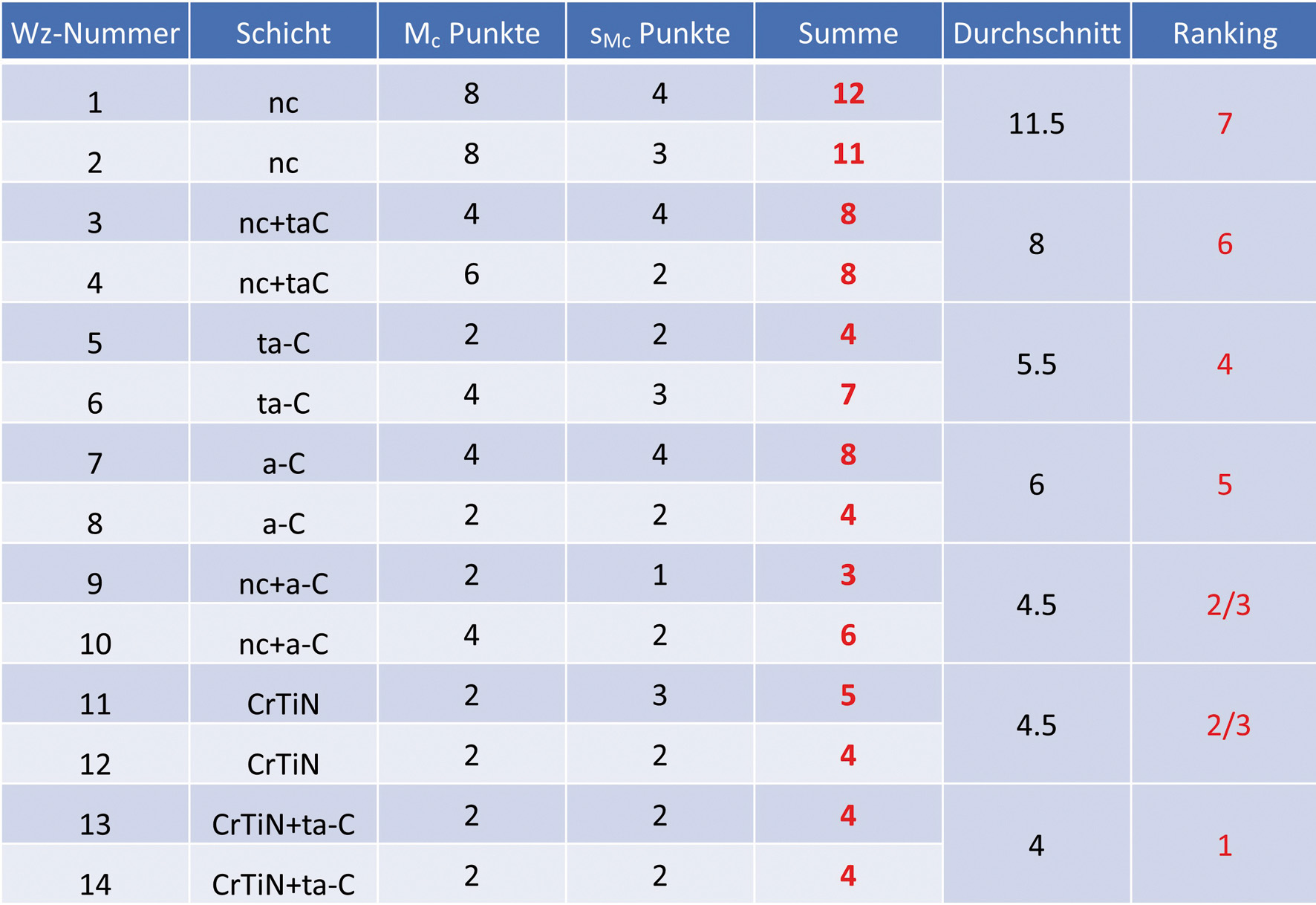
5a. Zusammengefasste Punktzahlen und Ranking
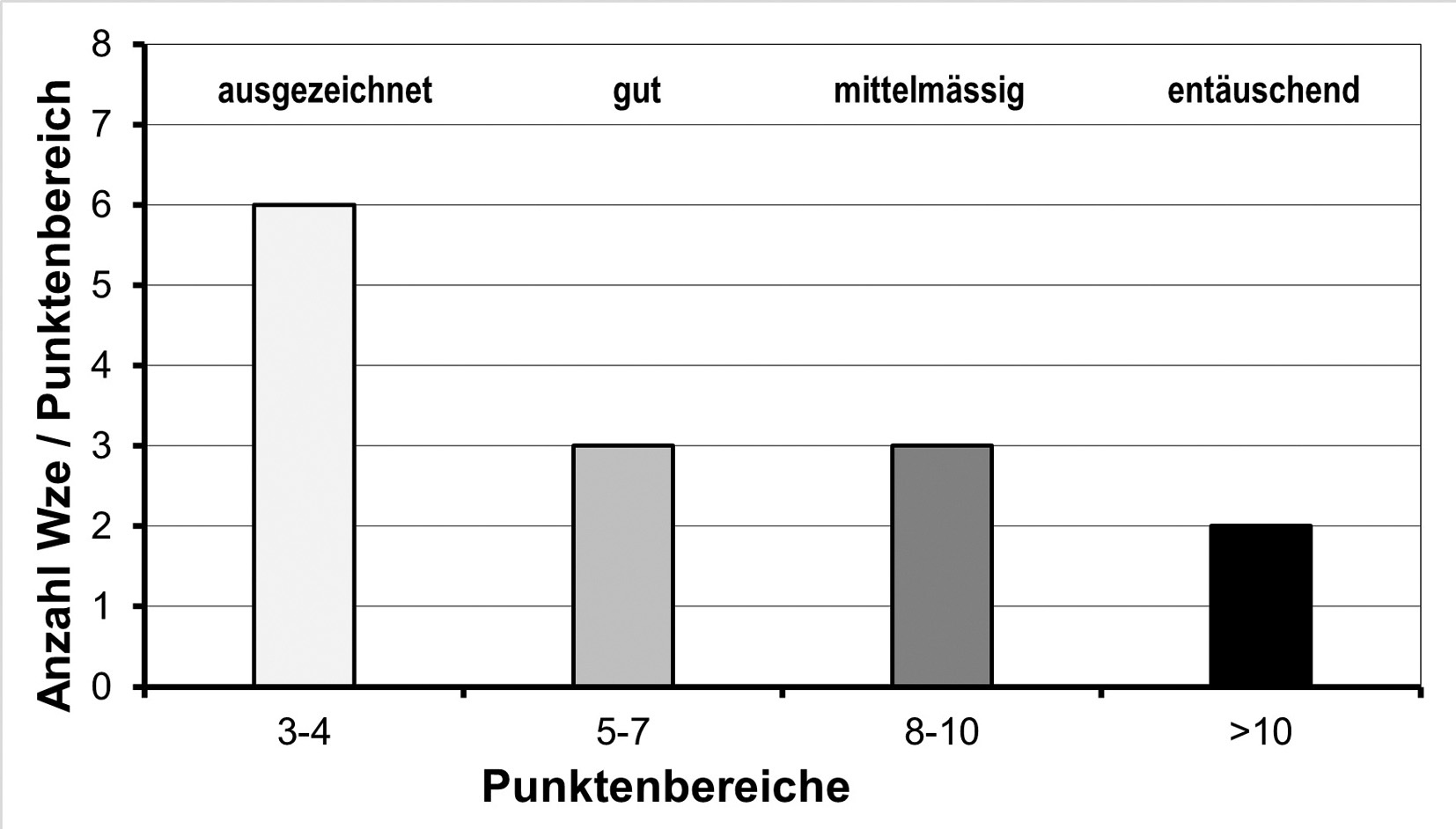
Bild 5: Bewertung der getesteten Beschichtungen und Reihenfolge ihrer Effizienz beim Gewindebohren. 5b. Verteilung der Punkte
2.2 Ergebnisse beim Gewindeformen
Völlig identisch war die Prüfmethode bei den Versuchen mit 10 Gewindeformern, deren Ergebnisse in Bild 6 zusammengefasst sind.
Aufgrund der Besonderheiten des plastischen Umformprozesses schwanken trotz optimaler Größe und Genauigkeit der Kernlöcher die Mittelwerte der Drehmomente (Bild 6a) über einen größeren Bereich als beim Gewindebohren.
Zur einfacheren und einheitlicheren Bewertung wurden auch die Gewindeformer in vier Kategorien untersucht. Betrachtet man das Balkendiagramm, so scheint es, dass die Versionen ohne DLC-Überbeschichtung deutlich höhere Drehmomente benötigten. Die überwiegende Mehrheit der Werkzeuge (70 %) erforderte ein geringes Drehmoment, wobei die Drehmomente von nur 3 Werkzeugen als groß angesehen werden können (Abbildung 6b). Da die mittleren Drehmomente bei den meisten Werkzeugen geringer waren, kann nur die Hälfte der Former bezüglich der Streuungen als günstig bezeichnet werden (Bild 6c).
Zur Bestimmung der Effizienz der Former wurde die Einstufung zwischen
1 und 4 beibehalten und die Aggregation und Gewichtung analog zu den Gewindebohrern durchgeführt. So konnten wir uns ein realistisches Bild von der Leistungsfähigkeit der Beschichtungen der einzelnen Werkzeuge machen und die nach deren Effizienz einordnen. Die erhaltenen Ergebnisse sind im Bild 7 dargestellt.
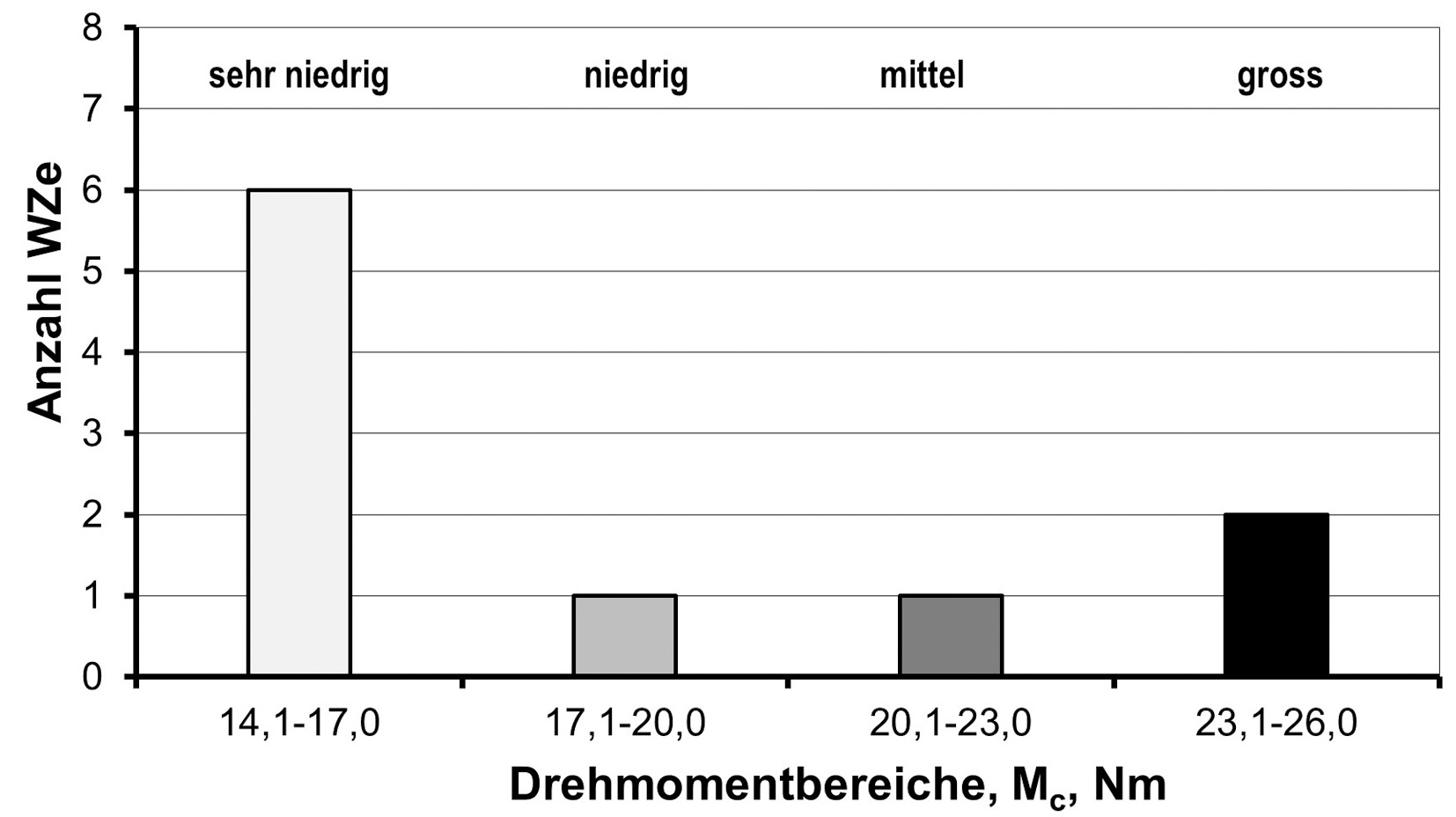
6b. Verteilung der Drehmomente
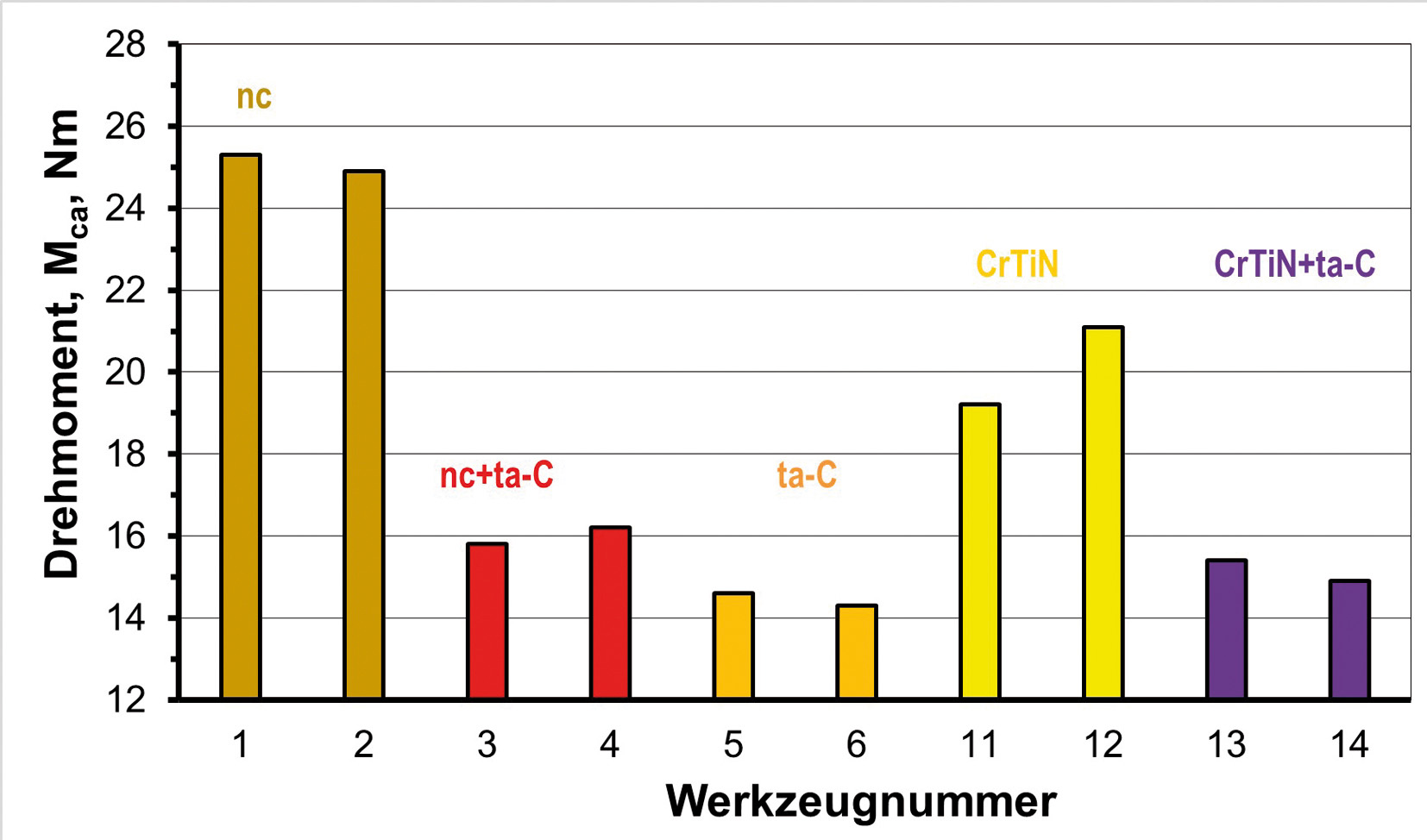
Bild 6: Ergebnisse der Gewindeformer.
6a. Drehmomente beim Gewindebohrer
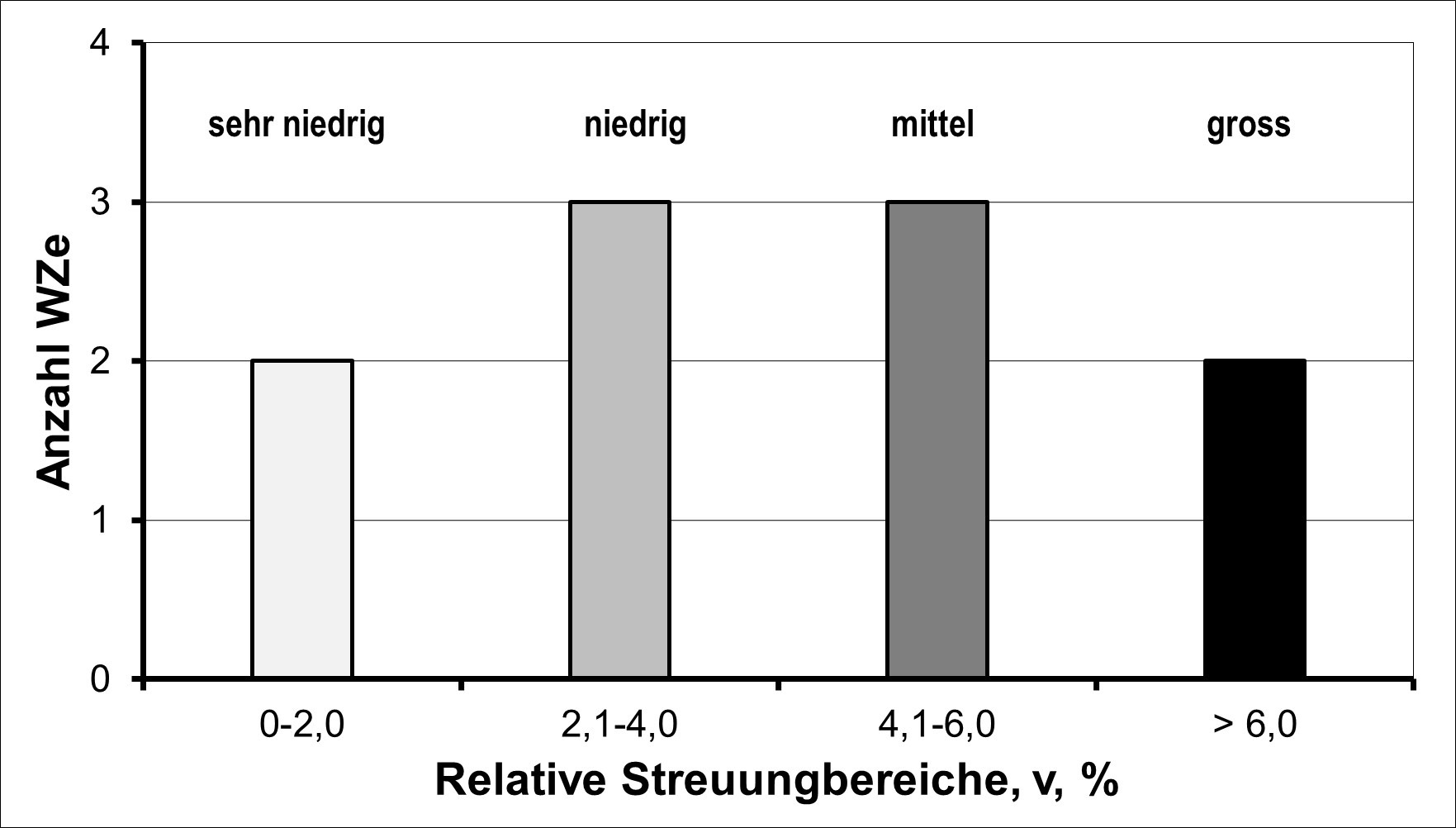
6c. Verteilung der Streuungen
Aus den erhaltenen Ergebnissen können wir die folgenden Schlussfolgerungen ziehen:
- a) Die Auswertung der Versuche der Gewindeformer ist sicherer, da der Unterschied zwischen den Werkzeugpaaren viel kleiner ist (Bild 7a).
- b) Die ta-C Basecoat oder alle ta-C Topcoat-Varianten sind hervorragend, also sie haben eine gute Effizienz.
- c) Die nc- und CrTiN-Basisschichten erreichten eine mittlere bis ungünstige Bewertung (Bild 7).
Das Bild 7 zeigt, die drei Beschichtungen mit ta-C schnitten nach der Auswertung der Drehmomentverläufe hervorragend ab. Für eine klare Ranking wurden die Vorschubkraft-Verläufe herangezogen. Anhand der Messergebnisse konnte festgestellt werden, dass zwischen dem Verhalten der getesteten Beschichtungen
und der am Einlauf auftretenden Vorschubkraft (Ffin) ein signifikanter Zusammenhang besteht: Günstigere Beschichtungsreibung bedeutet geringere Krafteinwirkung. Bild 8 zeigt die wichtigen Werte der Vorschubkräfte (Mittelwert, Standardabweichung, relative Standardabweichung). Die Auswertung der Verläufe nach der vorgestellten Formel ergibt das Ranking der ta-C Schichten für Gewindeformer.
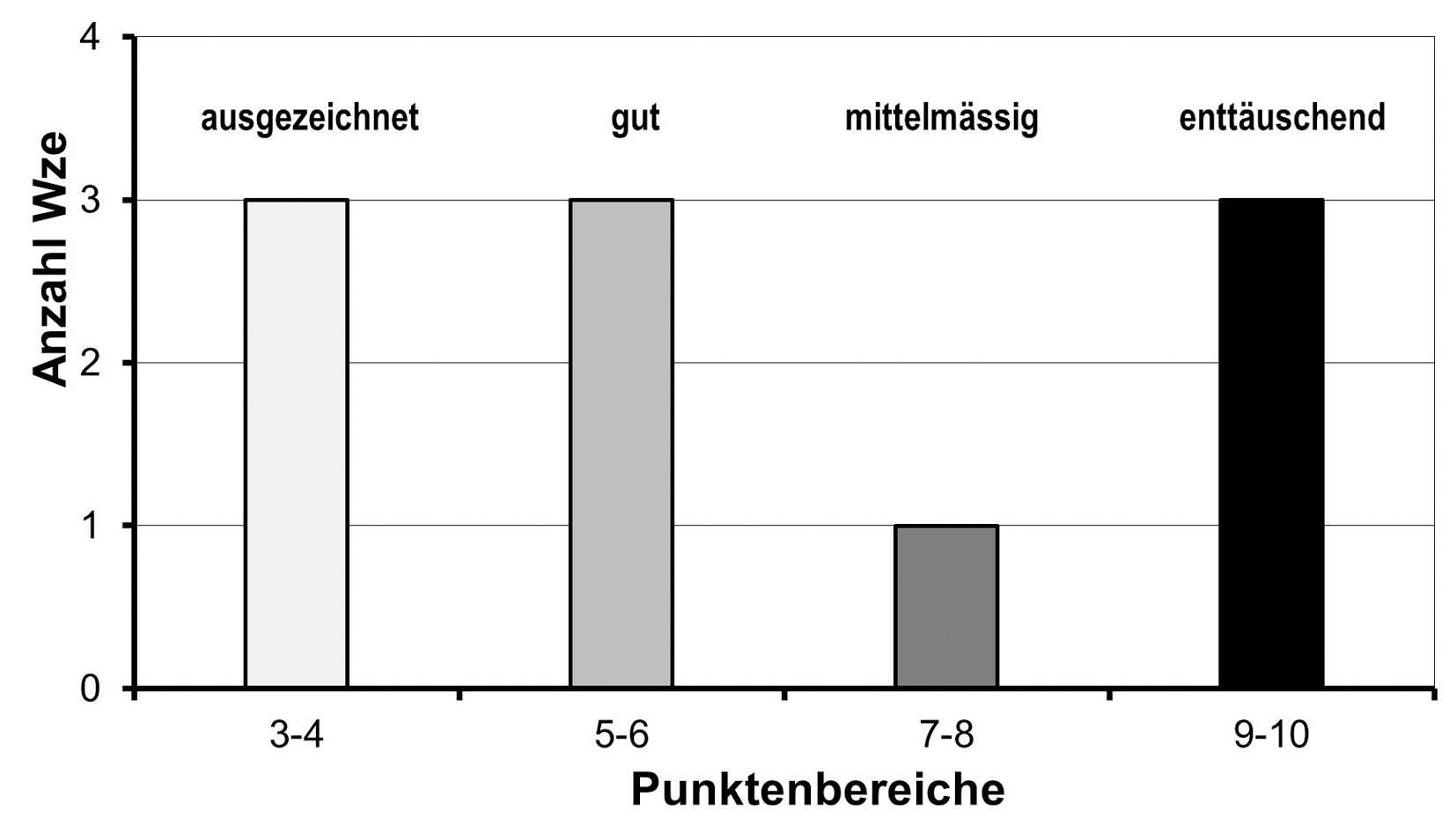
7b. Verteilung der Punkte
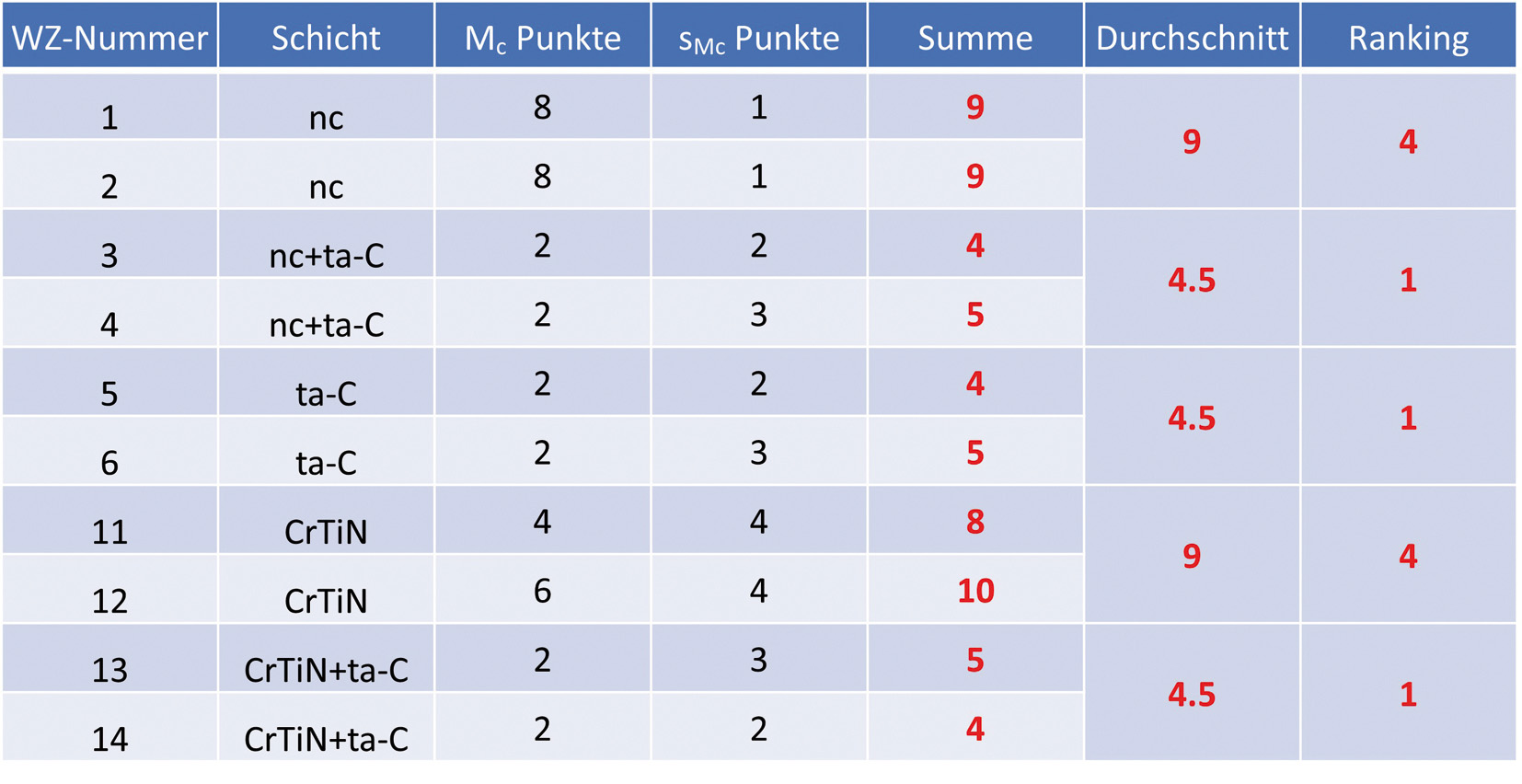
Bild 7: Qualifizierung von Beschichtungen und ihr Ranking für Former.
7a. Zusammengefasste Punktzahlen und Ranking
Aus dem Bild 8 lässt sich eindeutig ableiten, dass CrTiN+ta-C die günstigste Beschichtungskombination ist.
2.3 Schlussfolgerungen
Die Ergebnisse beider Verfahren zur Gewindeherstellung unterstreichen die wichtige Rolle der Beschichtung.
Entscheidend für die Effizienz sind die Qualität der einzelnen Schichten, die Auftragsreihenfolge und die Kombinationsmöglichkeiten. Beim Gewindebohren dominiert die Schutzwirkung der Beschichtung, während beim Formen die Reibungsminderung im Vordergrund steht. Daher erfüllen die getesteten Beschichtungstypen unterschiedliche Funktionen. Bild 9 hilft bei der Auswahl der verschiedenen Qualitäten.
Die Abbildung zeigt, dass reibungsarme DLC-Deckschichten mit unterschiedlichen Härten für beide Werkzeugtypen sinnvoll sind. So wurde beispielsweise bei einem Standzeitversuch von nc-beschichteten Gewindebohrern die vierfache Gewindezahl erreicht, wenn das Werkzeug mit einer zusätzlichen ta-C-Außenschicht verwendet wurde.
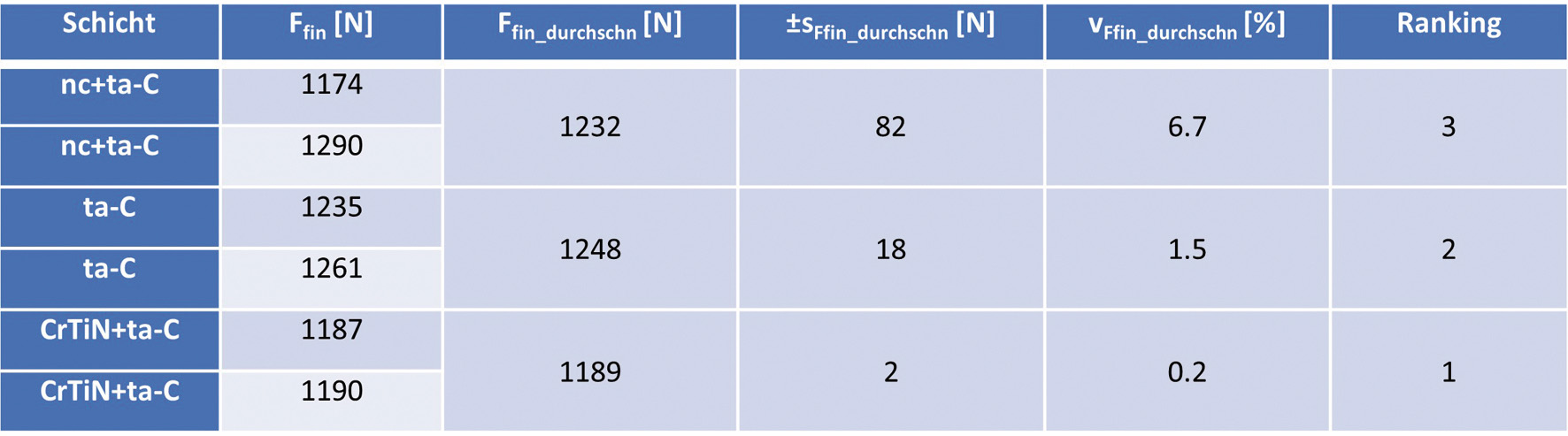
Bild 8: Zusammenstellung der signifikanten Vorschubkraftwerte beim Gewindeformen.
Zusammenfassung
Die hiesige Analyse moderner Beschichtungen für Gewindewerkzeuge basiert auf Untersuchungen eines unabhängigen Versuchslabors. Die Ergebnisse der Studie sind im Folgenden zusammengefasst:
- Unser primäres Ziel war die Auswahl und konsequente Anwendung objektiver, messbarer Parameter zur Charakterisierung der Beschichtungseffizienz. Die erhaltenen Daten wurden durch ein neuartiges Verarbeitungsverfahren untersucht. Die Inputs wurden aus den beschriebenen Kurzzeittests erhalten. Die Eingangsdrehmomente eignen sich zur Bestimmung und Einstufung der Leistung der aufgebrachten Schichten (oder Kombinationen davon) mit Hilfe des von uns entwickelten Bewertungssystems. Die Zuverlässigkeit der Versuche wurde durch den Einsatz von Werkzeugpaaren gewährleistet. Die Schwankungen in den Drehmoment-Abläufen lassen sich durch die nicht messbaren, individuellen Unterschiede zwischen Probe, Werkzeug und Kernloch erklären.
- Die Schutz- und/oder Gleitwirkung der Beschichtungen wurden eindeutig nachgewiesen. Die Art (Schneiden oder plastisches Umformen) und die Eigenschaften des Gewindeschneidvorgangs (z. B. Spanbildung und deren Störeffekt) interagieren eindeutig mit den Schichten. Aus den Schlussfolgerungen lässt sich leicht die einfache Aufgabe jeder Beschichtung erkennen: Bohren = Schutz, Formgebung = Reibungsminderung.
- Die an die nc-Beschichtung gesetzten Erwartungen wurden nicht erfüllt. Die für diese Anwendung dedicated (angepasste) Version von CrTiN schnitt jedoch in beiden Verfahren gut ab. Beim Formen ragen alle Schichten heraus, die ta-C-Schicht (auch) enthielten. Die Effizienzerhöhung ist so hoch, dass man mit ruhigen Gewissen sagen kann, die Gewindeformer für Stahlbearbeitung müssen mit ta-C beschichtet werden.
- Die effizienteste Beschichtung für beide Werkzeugtypen ist die CrTiN + ta-C.
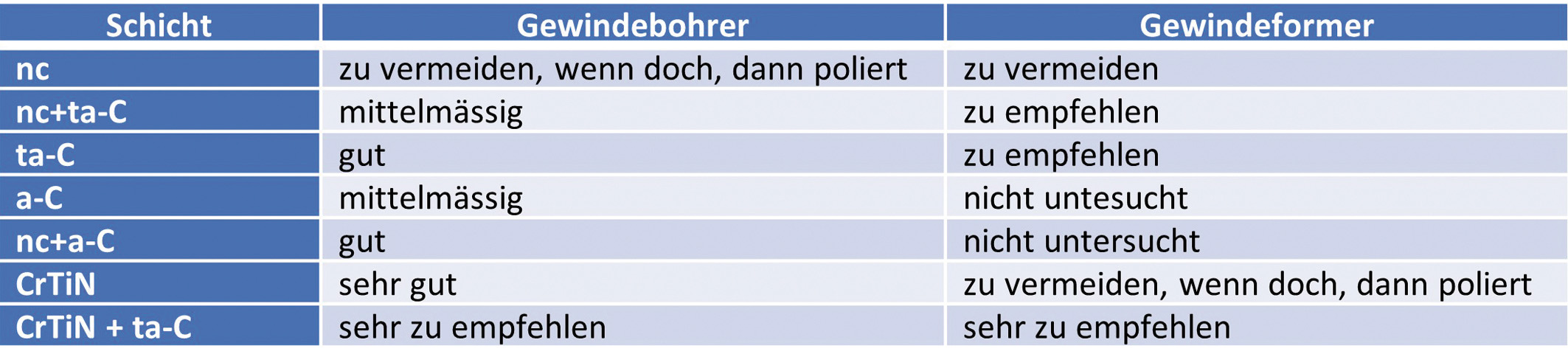
Bild 9: Auswahl der Schicht nach den Ergebnissen der Untersuchungen.
Literatur
[1] Cselle, T.: Tool life comparison at Thread Forming Werkzeug-Technik, Nr. 127/2012), p. 29-30.
[2] Sipos, S., Tállai, P.: Thread Forming Tools with Optimised Coatings Acta Polytechnica Hungarica (Journal of Applied Sciences), Vol. 12./No1., 2015. p. 55-66. ISSN 1785-8860
[3] Cselle, T., Rabel, G., u.a.: Flexibler Service mit Hochleistungschichten Werkzeug-Technik, Nr. 182/2020
[4] Sturges, H.: The choice of a class-inter- val, J. Amer. Statist. Assoc., 1926, 21., p. 65–66.
Autoren: T. Cselle PLATIT (CH), GFE (DE) – S. Sipos – Uni Obuda (H) – F. Welzel, GFE (DE)
