Prozesse beherrschen: Kugelbahnfräsen
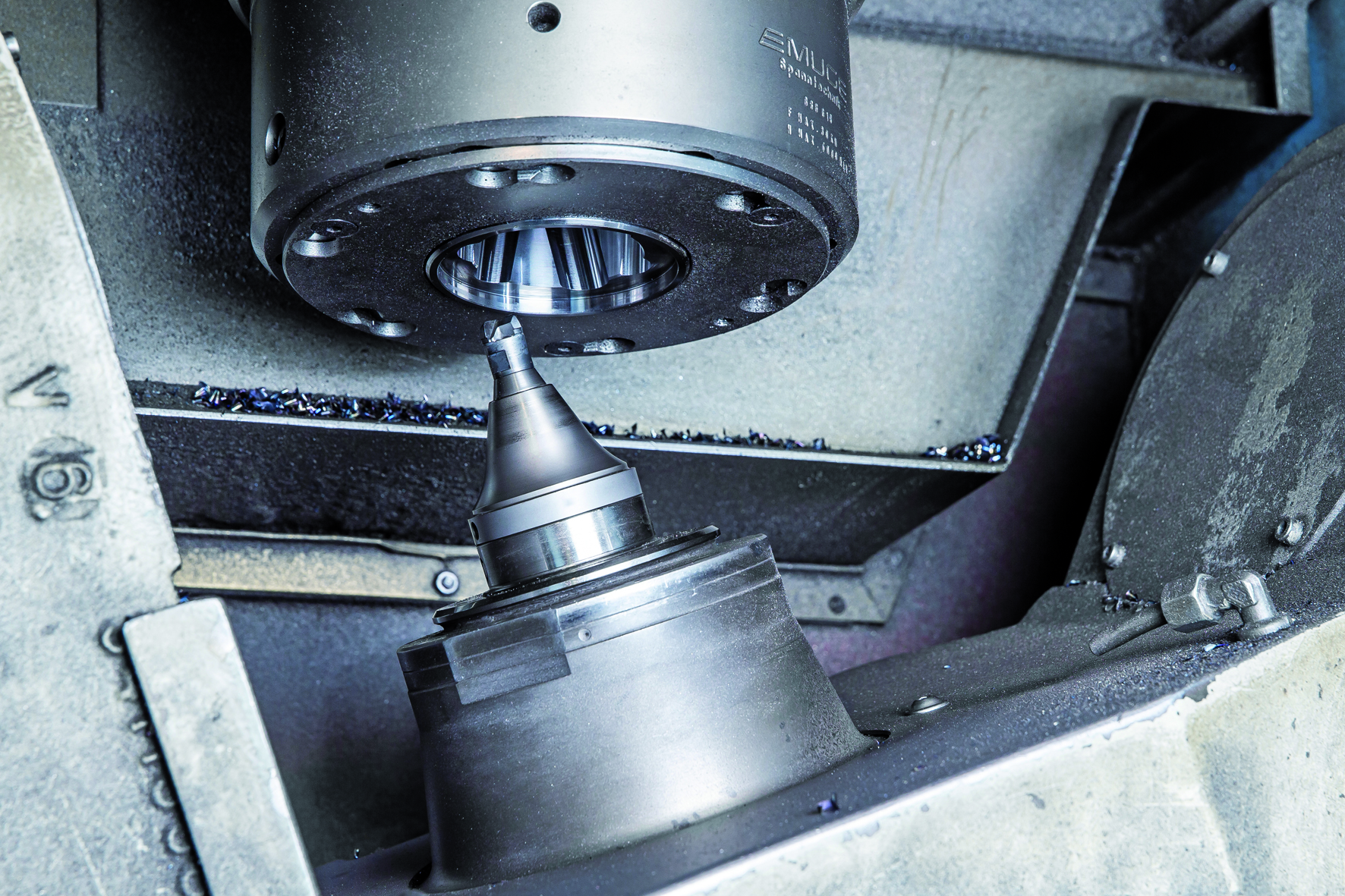
Hohe Fräsleistungen, hohe Standzeiten und ständige Optimierungen der eingesetzten Werkzeugsysteme. Die Paul Horn GmbH zeigt beim Prozess des Kugelbahnfräsens für homokinetische Gelenke ihr Know-how in der Werkzeugtechnologie. Mit hohen Zustelltiefen und Vorschubgeschwindigkeiten liegen die erreichbaren Fertigungstoleranzen im Bereich von Mikrometern. Horn erreicht diese Ergebnisse mit dem Wechselkopfsystem des Typs SX, einem sehr präzisen Schliff des Schneidenprofils und der Leidenschaft, immer das maximale aus dem Fräsprozess herauszukitzeln.
In jedem Automobil kommen sie zum Einsatz: Homokinetische Gelenke oder auch Gleichlaufgelenke genannt. Das Gelenk dient zur gleichmäßigen Übertragung des Drehmoments und der Winkelgeschwindigkeit von der Antriebswelle auf eine dazu im Winkel angebrachte zweite Welle. Gleichlaufgelenke übertragen die Drehbewegung gleichförmig auf die nächste Welle. Die größte Verbreitung haben die Gelenke im Fahrzeugbau bei der Kraftübertragung vom Getriebe zu den Antriebsrädern. Gleichlaufgelenke können Drehbewegungen bis zu einem Winkel von bis zu 50 Grad übertragen. Neben Kugel-Festgelenken kommen auch Gleichlauf-Verschiebegelenke zum Einsatz. Sie ermöglichen neben der Winkelbewegung auch eine Axialbewegung, damit die Kraftübertragung beim Einlenken oder Federbewegungen der Räder nicht unterbrochen wird.
Das Herzstück eines homokinetischen Gelenkes sind die Kugeln, welche sich in präzise gefrästen Kugellaufbahnen abrollen. Die Kugellaufbahnen weisen eine sehr geringe Fertigungstoleranz und eine hohe zu erreichende Oberflächengüte auf. Die engen Toleranzen und die Fertigungsqualität bestimmen die hohe Lebensdauer der Gelenke. Die einzuhaltenden Formtoleranzen bei der Fertigung der Laufbahnen liegen darüber hinaus im Mikrometerbereich. In einem Antriebsstrang kommen Kugel-Festgelenke und Kugel-Verschiebegelenke zum Einsatz. Die Kugelbahnen werden in den Gelenkzapfen, in das Gelenkstück und in die Kugelnabe gefräst.
Das Horn-Werkzeugsystem SX ist die Weiterentwicklung der Horn-Kugelbahnfräser der Typenfamilie 42X. Das System 42X war durch eine zentrische Spannschraube jedoch in der Frästiefe begrenzt. Durch die Weiterentwicklung entstand das Wechselkopfsystem SX. Der Schneidenkopf ist über ein stabiles, robustes aber dennoch hochgenaues Gewinde mit der Anlagefläche des Werkzeuggrundkörpers verbunden. Diese Schnittstelle bringt mehrere Vorteile: Hohe Stabilität durch das großzügige Passgewinde, eine breite Abstützung durch die große Anlagefläche sowie eine präzise Wechselgenauigkeit, welche sich immer in der Mitte des Toleranzfeldes einstellt. Darüber hinaus gestaltet sich der Wechsel des Schneidkopfes einfach und bedienerfreundlich.
Jede Kugelbahn wird meist in zwei Zustellungen gefertigt. Mit einer Schnittgeschwindigkeit von 200 bis 300 m/min schruppt und schlichtet das Werkzeug fünfachs-simultan jede Kugelbahn. Die Werkzeuge sind vier- oder fünfschneidig ausgeführt. Die Bearbeitungszeit eines Bauteils mit sechs, acht oder zehn Kugellaufbahnen liegt im Schnitt bei 40 Sekunden, je nach Bauteilgröße. Die Bahnen werden in das noch weiche Bauteil gefräst. Der Härteverzug der induktiv gehärteten Kugellaufbahnen ist in dem vorgehaltenen Profil des Werkzeugs verrechnet. Die geforderte µm-genaue Bahnkontur wird somit erst nach der Wärmebehandlung erreicht. Das elliptische Schneidenprofil der Kugelbahnfräser schleifen die Spezialisten bei Horn mit einer Formtoleranz von unter 0,005 mm (+/- 0,0025 mm). Dies ermöglicht die genaue Anpassung der Schneidenform an den zu erwartenden Härteverzug.
Durch die Umstellung auf das Horn-SX-System konnte ein Anwender die Ausbringung seiner Bauteile um ein Drittel erhöhen. Die Einsparung von einem Bearbeitungsschritt, dem Schruppen mit einem anderen Werkzeug, addierte sich mit den deutlich höheren Standzeiten der SX-Werkzeuge. Neben den Werkzeugen aus Hartmetall bietet Horn die Fräswerkzeuge CBN-bestückt an. Diese zeigen hohe Fräsleistungen und die Präzision bei der Bearbeitung von gehärteten Werkstoffen.

Hohe Leistungen in gehärteten Werkstoffen zeigt das Werkzeugsystem mit einer CBN-Bestückung.
Bild: HORN/Sauermann
