Werkzeug-Beschichtungen für die Mikrozerspanung: Dünne Schichten, starke Wirkung
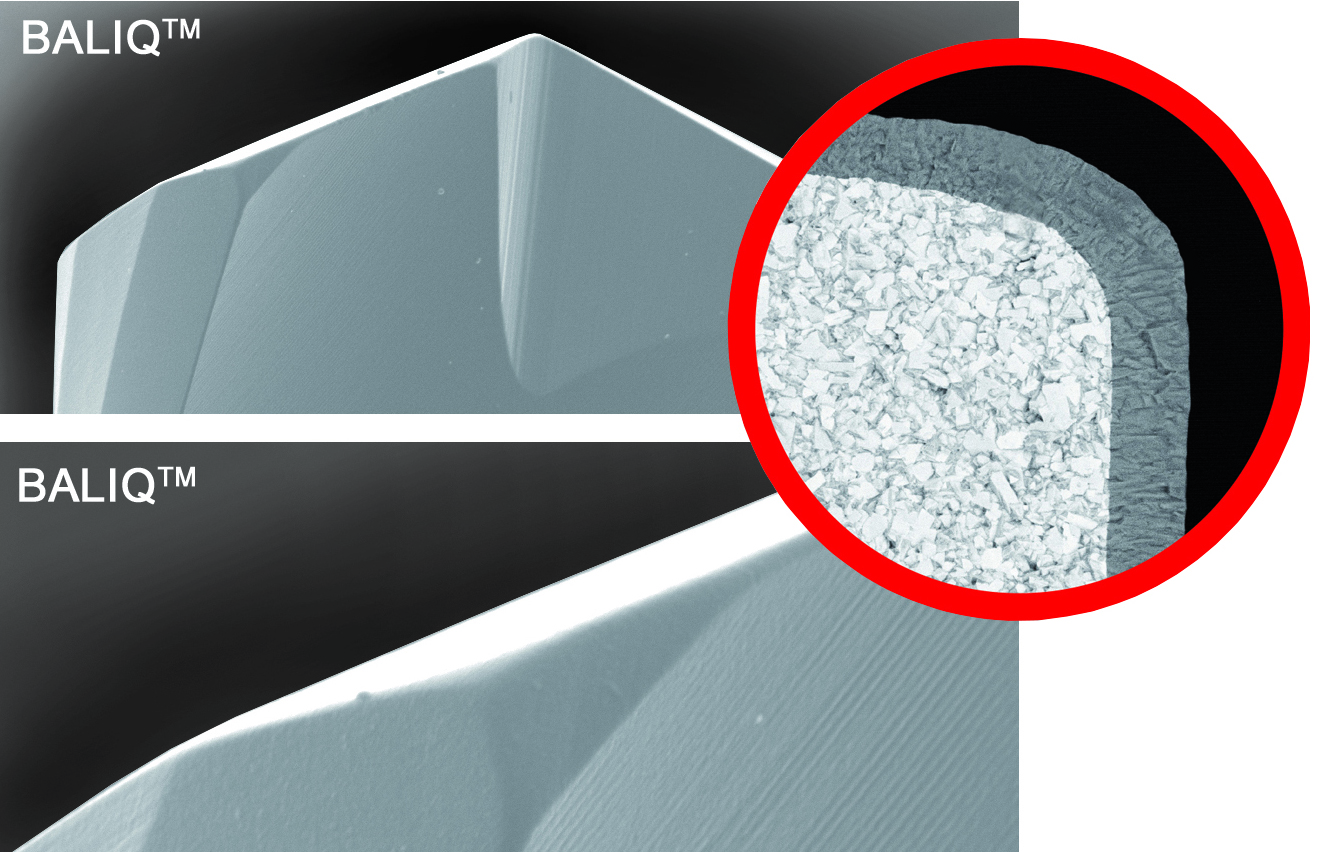
Die Mikrozerspanung anspruchsvoller Werkstoffe hat in zentralen Schlüsselindustrien Einzug gehalten. Hochleistungs-Beschichtungen spielen im Wärme- und Verschleißmanagement filigraner Werkzeuge unter extremen Einsatzbedingungen eine unverzichtbare Rolle.
In der Mikrozerspanung bearbeiten heute Werkzeuge mit einem Durchmesser von etwa 1 bis 0,03 mm Bauteile mit Maßen von knapp 1 mm bis 1 cm. Sie bohren oder fräsen Strukturen von rund 5 bis 0,03 mm Größe. Dabei gelten Toleranzen von rund 1 Mikrometer bis 100 Nanometer und einzuhaltende Oberflächen-Rauigkeiten von 1 bis 600 nm am Werkstück. Diese mikroskopischen Dimensionen bergen ein enormes Potenzial. Die Mikrozerspanung ist damit unverzichtbar in Schlüsselindustrien wie Medizintechnik, Automobilindustrie, Elektronik und Formenbau geworden. Dank ihr lassen sich kleinste Komponenten und Strukturen für Endoprothesen und medizinische Instrumente ebenso wie Bauteile für das elektrifizierten Automobil und deren Infrastruktur wirtschaftlich fertigen – und dies auch in kleinen Stückzahlen.
Nicht nur damit hat sich die Mikrozerspanung zunehmend Vorteile gegenüber anderen Methoden der Mikrobearbeitung wie Erodieren oder Lasern verschafft. Ihre Trümpfe liegen vor allem in ihrer vielfältigen Formgebung. Jedoch wachsen mit den Anforderungen auch die Herausforderungen in der Zerspanung. Insbesondere bei der Bearbeitung ohnehin anspruchsvoller Werkstoffe wie rostfreie Stähle, Inconel, Kobalt-Chrom, Titan oder NE-Metalllegierungen sind sichere und produktive Prozesse in der Mikrobearbeitung oft noch ein schwer erreichbares Ziel. Zumal der Trend in so gut wie allen Bereichen in Richtung HSC (High Speed Cutting)-Bearbeitung geht. So haben es Mikrobohrer und -fräser trotz ihrer geringen Durchmesser bei der Zerspanung moderner Materialien zunehmend mit hohen Schnittgeschwindigkeiten zu tun, denn moderne Maschinenspindeln erreichen Drehzahlen bis zu 60.000 U/min. Dadurch ergeben sich hohe thermische Belastungen für Werkzeuge und Schneiden.
Hinzu kommt, dass sich Know-how aus der konventionellen Zerspanung oft nicht auf die Mikrobearbeitung übertragen lässt. So können die winzigen Werkzeugdurchmesser durchaus den Dimensionen der Gefüge-Bestandteile des zu bearbeitenden Werkstoffes entsprechen. Je nachdem führt dies zu größeren Unterschieden in Bezug auf Zerspanungskräfte und -verhalten im selben Bearbeitungsprozess. Dabei sind die präzisen Mikrowerkzeuge sehr empfindlich und brechen schnell. Vor diesem Hintergrund steht und fällt der Erfolg in der Mikrozerspanung mit der richtigen Auswahl und dem präzise abgestimmten Zusammenspiel aller Komponenten – von Bearbeitungszentrum, Spindel und Spannsystem bis zu Werkzeug, Schneidkantenausführung sowie Beschichtung und Kühlschmiermittelversorgung.
Beschichtungen sind dabei unerlässlich, um Werkzeuge vor Hitze, abrasivem und adhäsivem Verschleiß zu schützen, entstehende Kräfte in der Balance zu halten und damit Prozesse sicherer zu machen. Sie können viel bewirken, wenn sie optimal auf die sehr feinen Geometrien der Werkzeuge angepasst sind. Denn schon kleinste Abweichungen, beispielsweise im Schichtaufbau der Schneidkante, können zum sofortigen Werkzeugbruch führen. Entscheidend ist daher die hohe Reproduzierbarkeit der Schichtqualität, um bereits kleinste Defekte und den daraus folgenden Werkzeugbruch zu verhindern. Dafür hat der Oberflächenspezialist Oerlikon Balzers Hochleistungsschichten seiner BALIQ®-Familie sowie außerdem spezielle Kohlenstoffschichten entwickelt, die auf Mikrowerkzeugen in zentralen Anwendungsbereichen für höchste Sicherheit sorgen.
Schichten schützen in der Medizintechnik
Bei der Fertigung von Zahnersatz in der Dentalmedizin oder von Endoprothesen für Hüft- oder Kniegelenke geht es um biokompatible, nicht-korrosive sowie langlebige Materialien wie etwa Kobalt-Chrom-Legierungen. Durch die geringe Wärmeleitfähigkeit treten bei deren Zerspanung treten jedoch hohe Temperaturen an der Schneide und adhäsiver Verschleiß durch Anhaftungen auf.
Mit BALIQ® MICRO TISINOS steht eine Schicht zur Verfügung, die Mikrowerkzeuge für diese Anforderungen optimal ausstattet und sehr hohen Temperaturen widersteht. Sie bringt zum einen alle Vorteile der fortschrittlichen S3p-Beschichtungstechnologie mit, vereint höchste Härte, Glätte und Dichte und trägt damit zur Reibungsminimierung und Isolierung der sehr harten Feinkornhartmetalle im Material bei, um dieses gegen hohe Wärmeentwicklung zu schützen. Die Schichtzusammensetzung aus AlTiSiN hält den hohen thermischen Belastungen stand und schützt damit den Binder Kobalt im Hartmetallsubstrat vor thermischer Korrosion. Die genaue Abbildung der Schneidkanten und eine konstante Schichtdicke von 1 bis 2 Mikrometern resultieren in sehr scharfen Schneiden auch nach der Beschichtung. Dies führt zu geringeren Schnittkräften verbunden mit einer höheren Prozessstabilität. Durch dieses hochwirksame Wärme- und Schnittkraftmanagement sinkt auch die Neigung zur Adhäsion.
Lösungen für gehärtete Stähle im Formenbau
BALIQ®-Schichten wie BALIQ® MICRO TISINOS oder BALIQ® MICRO ALCRONOS eignen sich auch für den Werkzeug- und Formenbau, wo es auf feinste Strukturen und hohe Oberflächenqualitäten ankommt. Hier werden Stähle in der Weichbearbeitung bis 50HRC und in der Hartbearbeitung bis zu 70 HRC zerspant. Im Anwendungsbeispiel eines Werkzeugherstellers werden die Vorteile einer BALIQ-Beschichtung für die Mikrobearbeitung deutlich. So zeigte sich etwa für die Bearbeitung eines 1.2379 Stahls mit 58 HRC eine erhebliche Steigerung der Oberflächenqualität des Produktes.
In Sachen Werkzeugverschleiß wird ein signifikanter Unterschied gegenüber herkömmlichen PVD-Schichten oder auch HIPIMS-Schichten von Marktbegleitern deutlich. Dies führt die Bearbeitung eines gehärteten Stahls (1.2379 mit 62 HRC) mit einer Vorschubgeschwindigkeit von vc=130m/min vor Augen. Bei immer gleicher Standzeit weist der herkömmlich beschichtete Fräser (Durchmesser 2 mm) mit 62 Mikrometern eine stark ausgeprägte Verschleißbreite an der Werkzeugschneide auf. Mit Einsatz von BALIQ® MICRO TISINOS jedoch ist der Verschleiß mit einer Breite von lediglich 15 Mikrometern an der Werkzeugschneide kaum zu erkennen. Die Schicht lässt sich einsetzen zur Fertigung von Mikrostrukturierungen bis zu 30 Mikrometern und Oberflächenzielen mit Rauheitswerten von Rz 1. Dies ist mit alternativen Fertigungskonzepten wie Erodieren oder Lasern derzeit nicht zu realisieren und erspart zukünftig aufwändige Polituren.
NE-Metalle sicher mikrozerspanen
Ein Zukunftsthema ist die Mikrozerspanung von NE-Metallen, vor allem angesichts der wachsenden Industrie rund um die Elektromobilität. Steckerkontakte und Sensoren für Elektrofahrzeuge oder Ladesäulen sind Beispiele für die Vielzahl an Komponenten, die hauptsächlich aus NE-Metallen wie bleifreiem Kupfer oder Messing entstehen und mikrobearbeitet werden. Dafür eignet sich als Werkzeugbeschichtung BALINIT® HARD CARBON, eine wasserstofffreie, kohlenstoffbasierte (ta-C) Schicht. Sie ist chemisch hoch inert und bringt eine hohe Härte von 5.000 HV sowie eine äußerst geringe Reibung mit und verhindert somit Aufschmierungen. Zudem ist sie deutlich hitzebeständiger als andere Kohlenstoffschichten und hält Temperaturen bis 500 Grad Celsius stand. Durch ihre geringe Dicke von 0,5 bis 1 Mikrometer ermöglicht sie sehr scharfe Schneidkanten und eignet sich sehr gut für kleinste Abmessungen in der Mikrobearbeitung insbesondere von Nichteisenmetallen wie Kupfer und Messing sowie Aluminiumlegierungen mit einem Siliziumanteil von unter 12 Prozent.
„Unsere Beschichtungslösungen zielen auf immer bessere Oberflächen ab. Das ist auch nötig, denn in der teuren Mikrobearbeitung sollten Politurprozesse künftig gänzlich entfallen. Auf diesem komplexen Einsatzgebiet haben wir bereits viel Know-how aufgebaut: wir kooperieren mit den Marktführern der Branche. Mikrozerspanung ist ein wichtiges Zukunftsthema für uns und wir möchten auch morgen auf alle Fragen passende Antworten parat haben“, resümiert Rico Fritzsche, Segment Manager Cutting Tools bei Oerlikon Balzers.
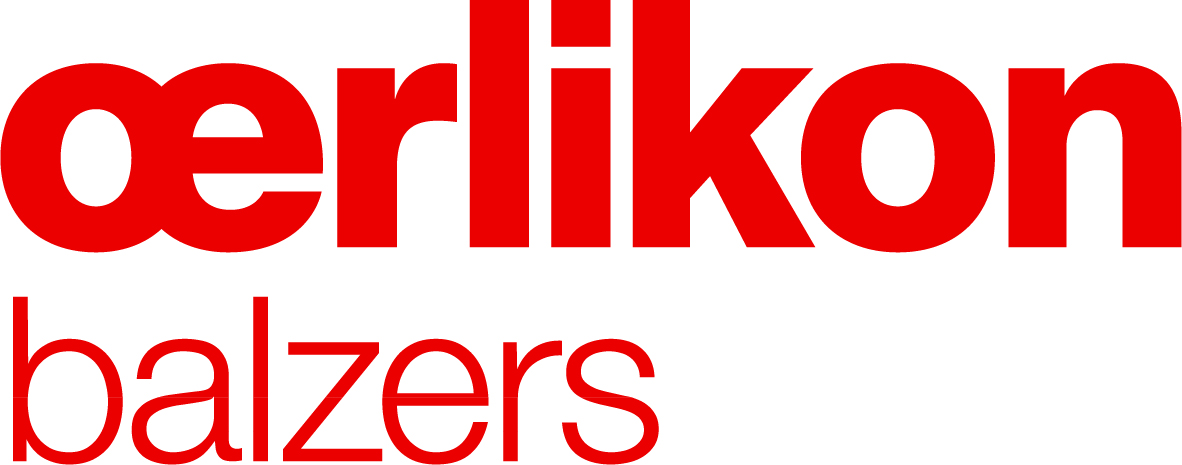