Problemlöser aus dem 3D-Drucker Abstechen mit dem CutSFeed von INGERSOLL
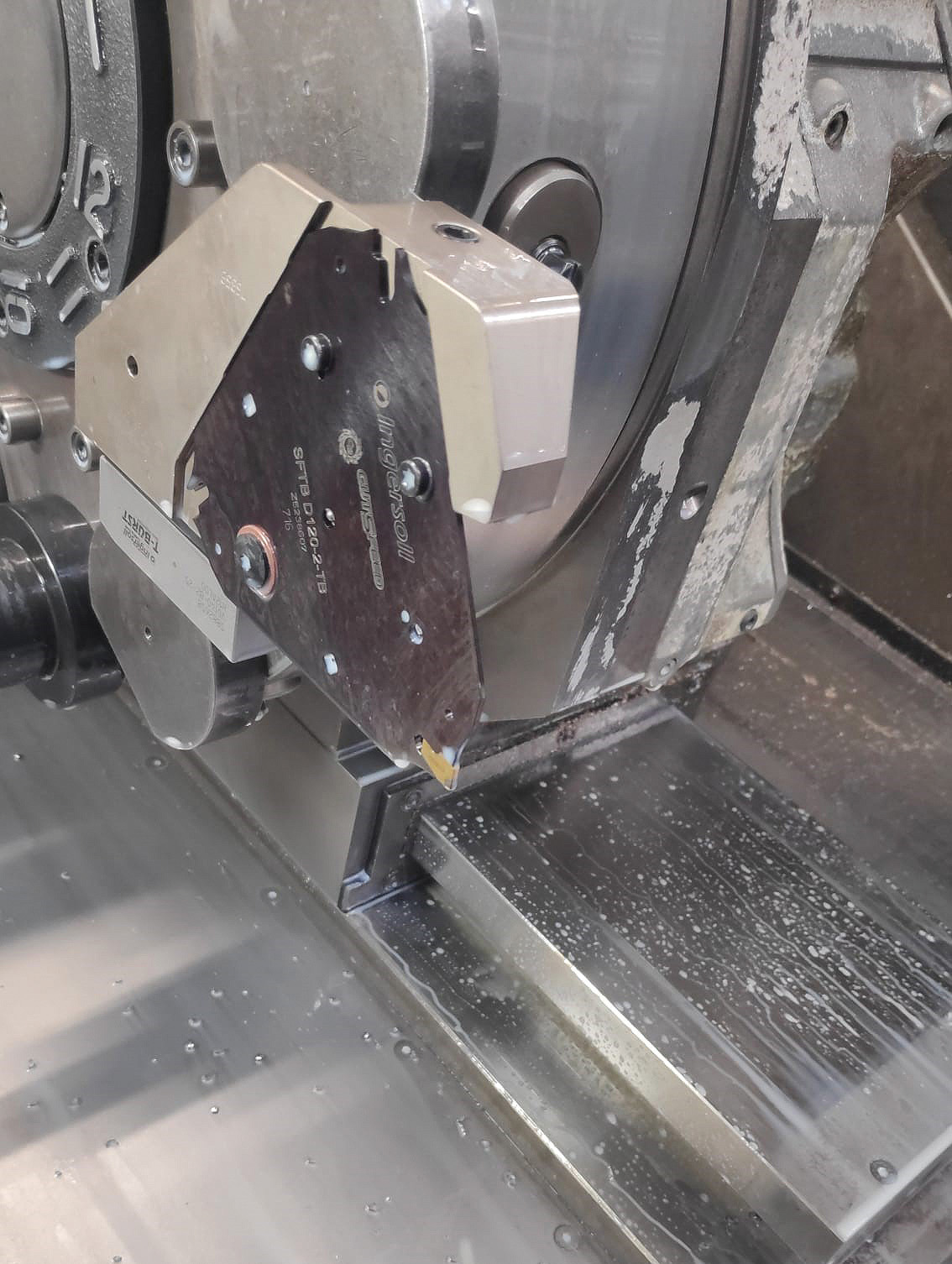
Als die Weikmann GmbH in Illertissen Probleme mit dem Abstechen eines Bauteils hatte, kam eine Neuentwicklung der INGERSOLL WERKZEUGE GMBH gerade recht. Das per 3D-Druck hergestellte Stechwerkzeug CutSFeed bewährte sich nicht nur bei der aktuellen Herausforderung, sondern wird dank seiner hohen Produktivität inzwischen universell im Unternehmen eingesetzt
Josef Weikmann, der Großvater des heutigen Geschäftsführers Maximilian Kristen, startete das Unternehmen mit einer konventionellen Drehmaschine in der Garage. Über die Jahre entstand ein moderner Maschinenpark den Weikmann ständig erneuerte und ausbaute.
Heute ist das seit 2021 in dritter Familiengeneration von Maximilian Kristen geleitete Unternehmen mit seinen 50 Mitarbeitern ein führender Hersteller für Präzisionsdrehteile und Frästeile, der vor allem Lohnaufträge für Maschinenbau und Agrarwirtschaft ausführt. Mit einem Anteil von insgesamt rund 50 Prozent sind verschiedene Werke von Liebherr der größte Kunde. Weitere Auftraggeber sind ebenfalls renommierte Unternehmen aus der Region.
Präzisionsdrehteile produziert Weikmann überwiegend von der Stange. Damit sind Durchmesser von 4 mm bis 70 mm und Bauteillängen bis 250 mm möglich. Neben elf Maschinen mit Stangenladern verfügt die Fertigung noch über fünf weitere Maschinen, auf denen auch Teile mit größeren Durchmessern und Längen hergestellt werden. Das Produktspektrum umfasst viele sicherheitsrelevante Teile, unter anderem auch Bolzen, die in Windkraftanlagen verbaut werden. Hinzu kommen Gewindefittings, Ösenfittings und verschiedene Bauteile für Hydraulikkomponenten. Verarbeitet wird vorwiegend Stahl, aber auch Edelstähle, Aluminium, weitere Nichteisenmetalle und Kunststoff dienen als Ausgangsmaterialien. Insgesamt hat es Weikmann mit rund 1.000 verschiedenen Bauteilen zu tun. Die Losgrößen schwanken zwischen 1 und 20.000 Stück. Weil der Hersteller immer wieder Bauteile erhielt, die nicht auf den vorhandenen Drehmaschinen gefertigt werden konnten, entstand auch ein Fräsbereich. Unter anderem fertigt Weikmann Verteilerblöcke für den Maschinenhersteller Grob.
Bei den Werkzeugen fehlten Standards
Im Maschinenpark in Illertissen dominiert der Maschinenhersteller Okuma. Weil man mit dem Hersteller sehr zufrieden war, wurden sowohl für das Drehen und Fräsen immer wieder Maschinen von Okuma angeschafft. Bei den Werkzeugen war die Strategie über lange Zeit hinweg längst nicht so konsequent. „Wir hatten hier ein sehr breites Spektrum an Werkzeuglieferanten, was mir stets ein Dorn im Auge war“, berichtet Maximilian Kristen. Weil jeder Mitarbeiter in der Fertigung seine bevorzugten Werkzeuge hatte, sammelten sich viele unterschiedliche Schneidplatten und Halter verschiedenster Hersteller im Werk an. Von Standardisierung war die Produktion weit entfernt und für Optimierungen war man kaum aufgeschlossen.
Das änderte sich, als der Fertiger kurz vor Weihnachten 2017 Kontakt mit INGERSOLL aufnahm, weil er mit den bisherigen Werkzeugen und Strategien ein bestimmtes Problem nicht lösen konnte. Damals ging es um M20 Innengewinde für Edelstahlteile, bei denen Weikmann den enormen Werkzeugverschleiß nicht in den Griff bekam. Die Aufgabe landete bei Markus Wiedemann, technischer Berater und Vertriebsmitarbeiter bei INGERSOLL. Er war gleich am folgenden Tag mit Gewindefräsern vor Ort, die es Weikmann ermöglichten, bis zu 1.000 Bauteile ohne weiteres herzustellen.
Nicht nur die wesentlich höheren Standzeiten überzeugten die Fertiger bei diesem Erstkontakt zu INGERSOLL, sondern auch die um ein mehrfaches höhere Produktivität. In der Folge wurden weitere Werkzeuge geordert. „Heute kommt ein großer Teil der bei uns eingesetzten Werkzeuge von INGERSOLL“, stellt Maximilian Kristen fest. „INGERSOLL ist bei uns für die Werkzeuge zu dem geworden, was Okuma zuvor bereits für die Maschinen war. Wir haben festgestellt, dass wir mit diesen Werkzeugen am effektivsten arbeiten.“
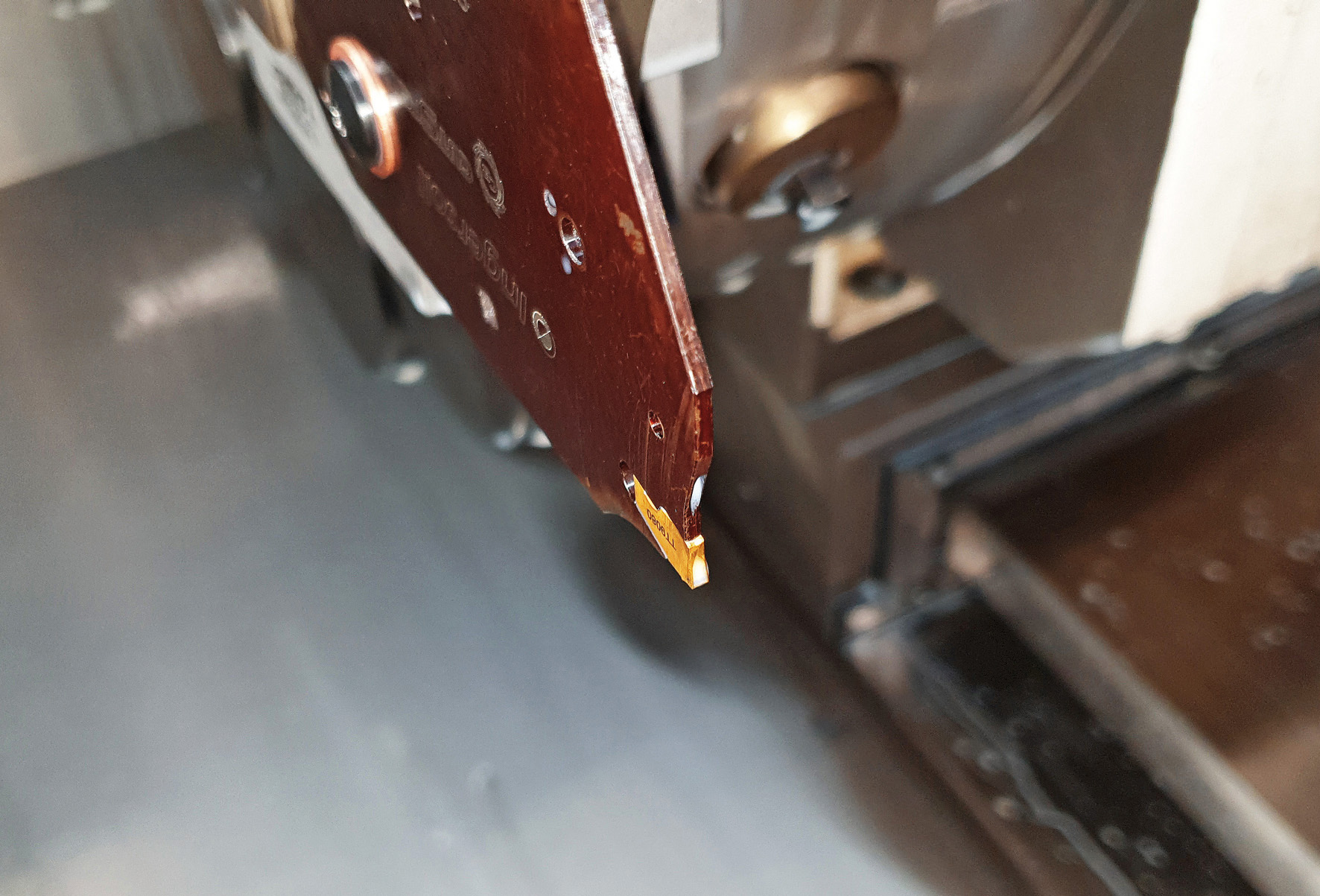
3D-Druck macht es möglich, mit den internen Kühlkanälen die Bohrungen im Schneidenträger zu umkurven und den Kühlstrahl gezielt auf die Schneide zu richten.
Mitarbeiter auf dem aktuellen Stand
Entscheidend für den Erfolg war neben den Werkzeugen auch die Schulung der Mitarbeiter. Diese Schulungen fanden entweder vor Ort bei Weikmann oder im TechCenter von INGERSOLL in Haiger statt. „Uns ist es sehr wichtig, dass unsere Mitarbeiter geschult und informiert sind“, versichert Kristen. „Es gibt immer wieder neue Entwicklungen, die ein Unternehmen vorwärts bringen. Um bei der Werkzeugtechnologie auf dem aktuellen Stand zu sein und auch mit den optimalen Schnittwerten zu arbeiten, muss man flexibel sein.“
Die Betreuung durch die INGERSOLL Anwendungstechnik hat Maximilian Kristen schätzen gelernt, zumal er schon erfahren hat, dass es bei den verschiedenen Werkzeuglieferanten große Unterschiede gibt: „Nicht jeder schickt mit einem neuen Werkzeug gleich einen Anwendungstechniker. Viele stellen uns nur ein Werkzeug zur Verfügung, und wir müssen allein damit zurechtkommen. Das ist bei Ingersoll ganz anders, hier passt das Gesamtpaket sehr gut.“ Vor diesem Hintergrund ist man in Illertissen auch stets gerne bereit, neue Werkzeuge von INGERSOLL zu testen.
Den guten Kontakt, den Markus Wiedemann zu seinem Kunden aufgebaut hat, zahlte sich aus, als der Werkzeughersteller INGERSOLL ein neues Stechwerkzeug entwickelt hatte, für das der technische Berater gleich an Weikmann als möglichen Anwender dachte. Dort war es immer wieder zu Problemen gekommen, wenn es darum ging, Bauteile mit größeren Durchmessern abzustechen. Neben schlechten Oberflächengüten wurden häufige Werkzeugbrüche bemängelt. Zudem stellten die Fertiger fest, dass die Kühlmittelzufuhr an die Schneide nicht immer optimal ausgeführt war. Mit dem neuen CutSFeed konnte Wiedemann diese Probleme auf Anhieb lösen.
Stabilität über große Anlageflächen
Michael Reifenrath, Anwendungstechniker bei INGERSOLL, erläutert die Besonderheiten des Werkzeugs: „Das CutSFeed-System ist vom Aufbau her komplett anders als ein herkömmliches Stechschwert, wie es zuvor auch bei Weikmann verwendet wurde. Während ein Standardschwert in der Regel nur geklemmt wird, ist dieses neue Blade fest mit dem Halter verschraubt. Damit kann es sich also nicht nach hinten wegdrücken. Da es wesentlich stabiler ist, kommt es auch kaum zu seitlichen Abdrängungen.“ Das Werkzeug verfügt über größere Anlageflächen, denn die Plananlage sorgt dafür, dass Hebelwirkungen, wie sie vor allem bei Schwertern mit größerer Auskraglänge auftreten können, komplett im Werkzeughalter aufgefangen werden.
Die Schneideinsätze verfügen über eine spezielle Klemmung über drei Kontaktflächen am unteren Absatz, die robuster als eine herkömmliche Selbstklemmung sind und damit zur Stabilität des Systems beitragen. Dies ermöglicht eine bessere Oberflächenrauheit, Wiederholbarkeit der Schneideinsatzposition und längere Werkzeuglebensdauer auch unter schwierigen Bearbeitungsbedingungen.
Mit der dadurch gegebenen Stabilität sind je nach Werkstückstoff deutlich höhere Schnittparameter möglich, die wesentlich zur Produktivitätssteigerung beitragen. Weikmann setzt das CutSFeed-System für Stahl und Kunststoff ein und konnte dabei die Vorschubwerte verdoppeln. Zudem entfällt die Nachbearbeitung des Werkstücks, die immer wieder nötig wurde, weil es zu Balligkeiten durch seitliche Abdrängung gerade bei großen Einstechtiefen kam. Nun kann gleich prozesssicher auf das Endmaß abgestochen werden.
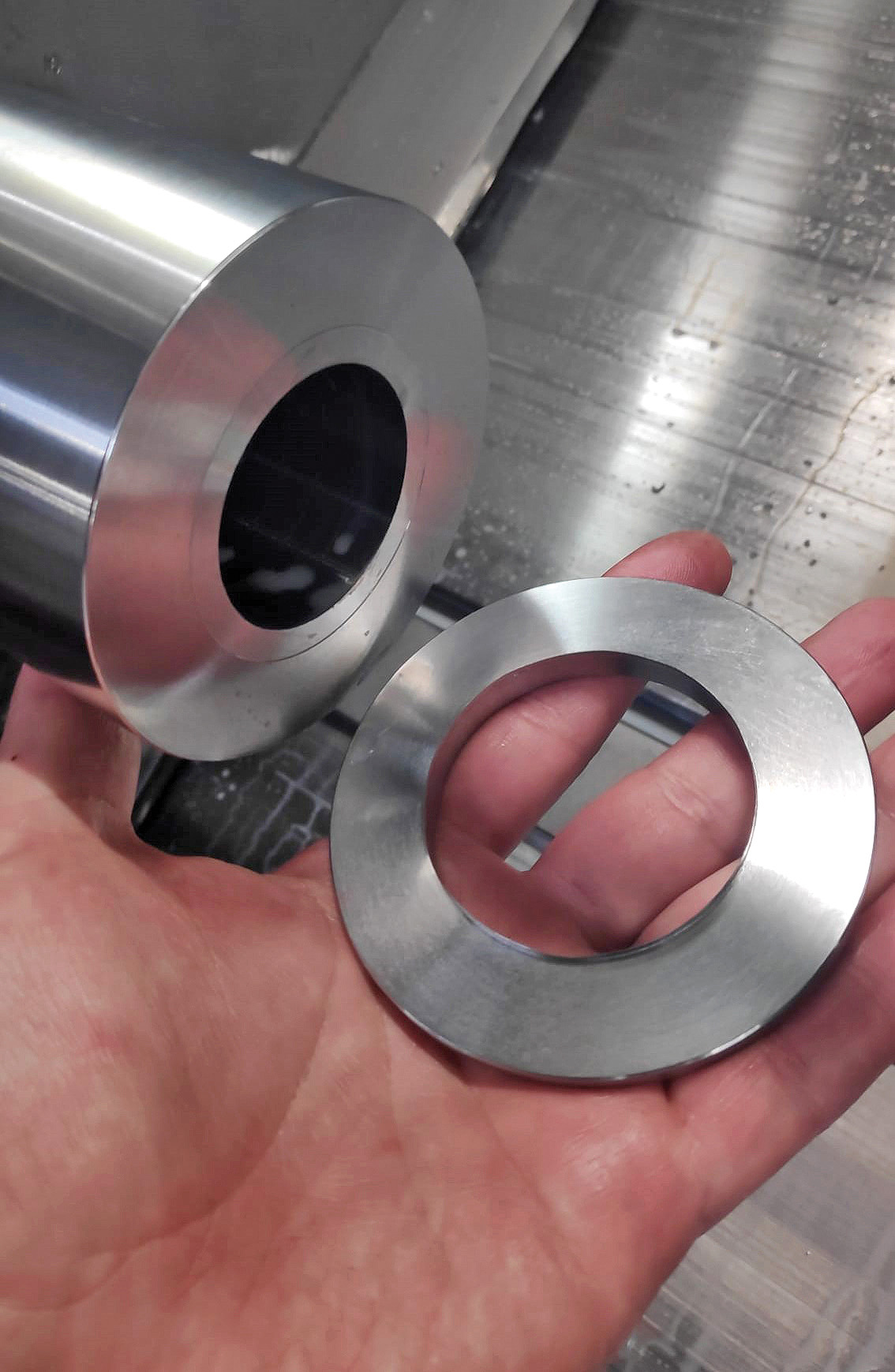
Das Abstechen mit dem CutSFeed erzeugt saubere Oberflächen, die nicht mehr nachbearbeitet werden müssen.
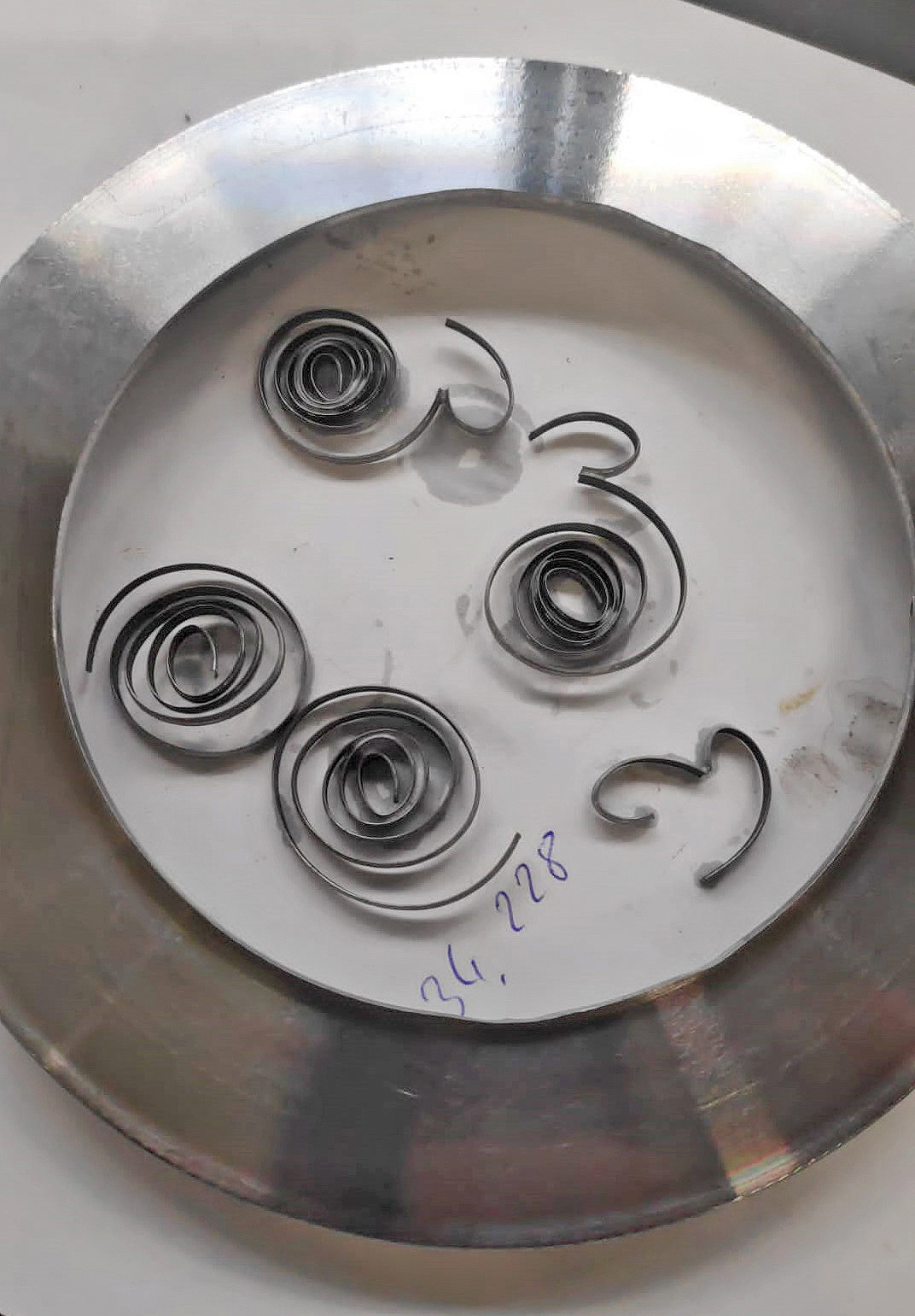
Im Zusammenspiel mit der Kühlung sorgen optimal eingestellte Schnittwerte für eine exzellente Spankontrolle.
Kühlung auf verschlungenen Wegen
Die Blades der Versionen SFTB und TGTB sind mit drei Plattensitzen ausgestattet. Auch bei der Kühlung des Werkzeugs geht INGERSOLL neue Wege: additive Fertigung macht innenliegende Kühlkanäle möglich. Die gezielte Freiflächenkühlung von unten dient dazu, Späne aus dem Arbeitsraum herauszuspülen. Eine zweite Düse kühlt die Schneide von oben. Jeder der drei Plattensitze kann gekühlt werden. Das Kühlmittel wird durch Halter und Schwert zu den Schneidplatten geleitet. Die Kühlkanäle müssen dabei um Ecken und Bohrungen herumgeführt werden.
„Mit konventioneller Technik hätten wir das nicht realisieren können, solche Kurven lassen sich nur mit 3D-Druck herstellen“, erklärt Michael Reifenrath. INGERSOLL stellt die Schwerter im Rahmen seines Programms CUBE 3D im additiven Fertigungsverfahren am Standort Vaihingen-Horrheim her. Das Laserschmelzen von Werkzeugstahlpulver liefert Ergebnisse, die konventionellem Material in nichts nachstehen. Nach dem 3D-Druck werden die Plattensitze noch nachgearbeitet und das Blade geschliffen, um eine exakte Plananlage zu bekommen.
Als Problemlöser hat Weikmann die dreieckigen Blades zunächst im Durchmesser von 120 mm eingesetzt. Von Prozesssicherheit und Produktivität überzeugt, legte sich das Unternehmen daraufhin weitere Größen für verschiedene andere Anwendungen zu. INGERSOLL bietet sie in den Durchmessern 52, 82 und 120 mm in Schnittbreiten ab 2 mm an.
Der Werkzeughersteller betreut den Kunden nicht nur vor Ort, wie Maximilian Kristen berichtet: „Wenn ein neues Bauteil vorliegt, von dem wir uns nicht sicher sind, ob wir das fertigen können, haben wir die Möglichkeit, die Daten auch in die Anwendungstechnik von INGERSOLL nach Haiger zu schicken. Hier erhalten wir auch eine Taktzeitberechnung. Ohne dass wir unsere Produktion für Tests unterbrechen müssen, werden Prozesse ausgelegt und das Bauteil gegebenenfalls auf einer der Maschinen im Tech-Center eingefahren.“ Dort ist oft auch Michael Reifenrath dabei, der das Tech-Center als seine Home Base bezeichnet.
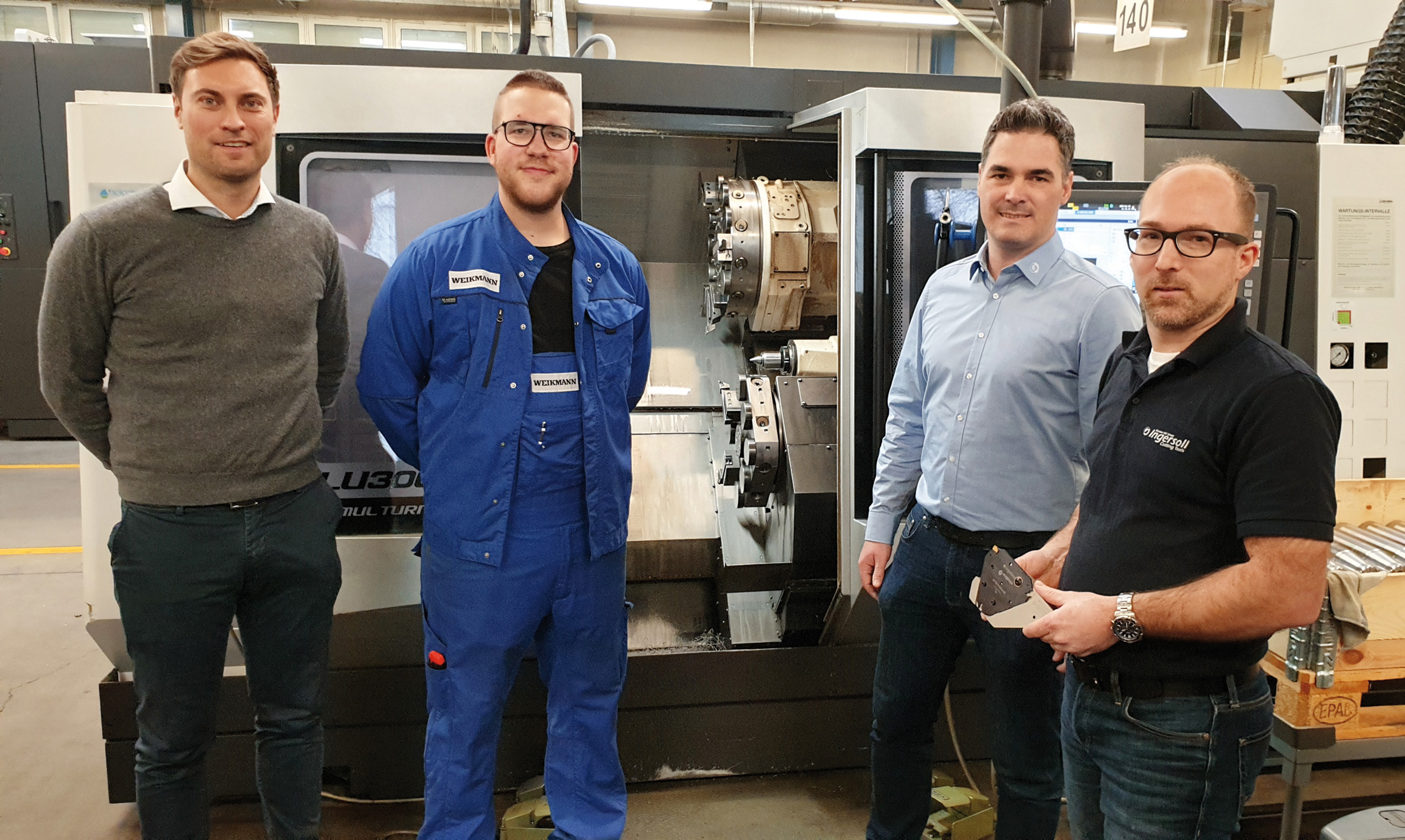
Konnten die Probleme der Produktion in Illertissen gemeinsam lösen (v.l.): Maximilian Kristen (Geschäftsführer Weikmann), Fabian Jutz (Schichtleiter Weikmann), Markus Wiedemann (Vertrieb INGERSOLL) und Michael Reifenrath (Anwendungstechnik INGERSOLL).
