Komplementäre Automation
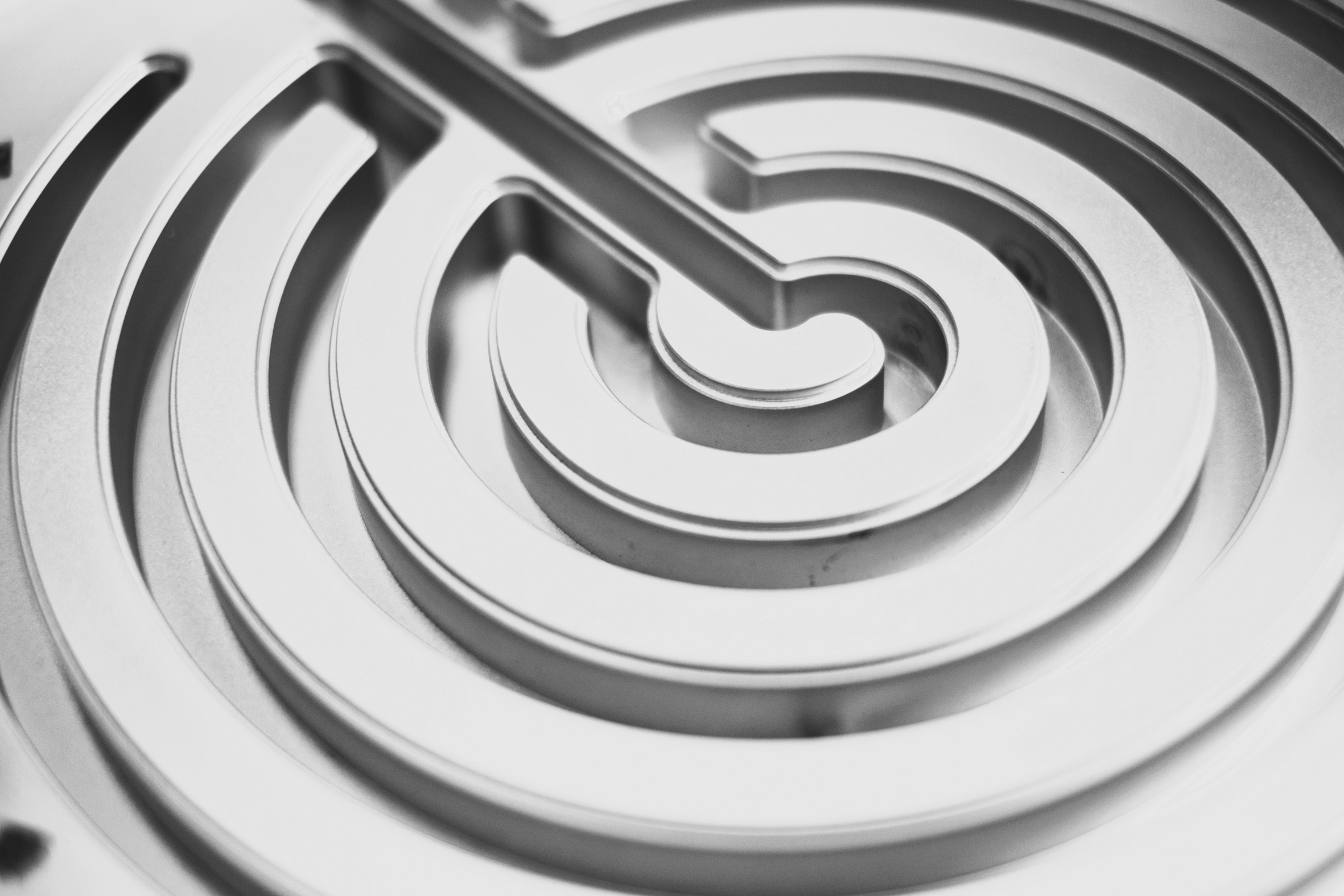
Unscheinbar lag nach dem Besuch von Andreas Brunhofer, Produktspezialist Automation bei Gressel, ein kleiner Flyer in der Fertigung von FMV aus Keltern-Dietlingen. Für Till Würtemberger, einen der Geschäftsführer des Lohnfertigers, wurde das Überfliegen zum Initial für eine massiv laufzeiterweiternde Automationslösung.
Die Maschinen in Fertigungsbetrieben müssen laufen. Und das umso dringender, je höher das Invest ist. Fertigungszellen gehören in diese gehobene Kategorie, zumal oft Roboter, Handling- und Speichersysteme, Spannmittelbahnhöfe und Teilewagen integriert sind. Bei FMV kommen noch ein Tauchbecken und ein Trockner für die Teilereinigung hinzu. Damit war die Fertigungszelle von FMB Maschinenbau aus Faulbach auf die Bearbeitung von Kühlplatten für den Halbleitermarkt zugeschnitten worden. Ein Geschäft, das Boomzeiten und Flauten kennt. Was aber, wenn wieder ein Rückgang zu verzeichnen war? Stand dann die Anlage? An diesem Punkt kam der Flyer von Gressel ins Spiel, der – wechselseitig zum teilespezifischen, seriellen Handling in der Zelle – eine Automation für beliebig geformte Teile in kleinen und mittleren Losgrößen beschreibt.
Zur richtigen Zeit am richtigen Ort
Seit 2009 fertigt FMV Kühlplatten für den Halbleitermarkt. 2016 erreichten diese als erste Produktgruppe des Unternehmens einen Umfang, der eine Automatisierung wirtschaftlich erscheinen ließ. Was sich heute auf bis zu 10.000 Stück pro Jahr beläuft, war damals, als die Entscheidung für eine Automatisierung fiel, zwar weniger, zeigte aber bereits: Mit den Stückzahlen ist die geplante Anlage die nächsten Jahre ausgelastet. Bis dahin waren die Kühlplatten mit einer 5- und einer 3-Achs-Maschine gefertigt worden, die rund um die Uhr liefen. „Uns war klar, dass wir die bestehenden Prozesse nicht einfach hochskalieren und für doppelt so viele Teile einfach doppelt so viele Maschinen betreiben konnten. Schon aus Platzgründen war das nicht möglich. Auch vom Personal her nicht, mit dem wir nicht ohne Weiteres ein Zweischichtmodell einführen konnten.“ Allerdings war mit der Entscheidung für die Automatisierung auch klar: Die Anlage sollte nach Abarbeitung der Kühlplattenaufträge auf keinen Fall stehen. Vielmehr sollten sich alternativ zu den Kühlplatten weitere Teile bearbeiten lassen. Das war der Spagat, vor dem FMV beim Besuch von Brunhofer stand. „Als ich mir dann die kleine Broschüre ansah, wusste ich sofort: Das brauchen wir“, so Würtemberger.
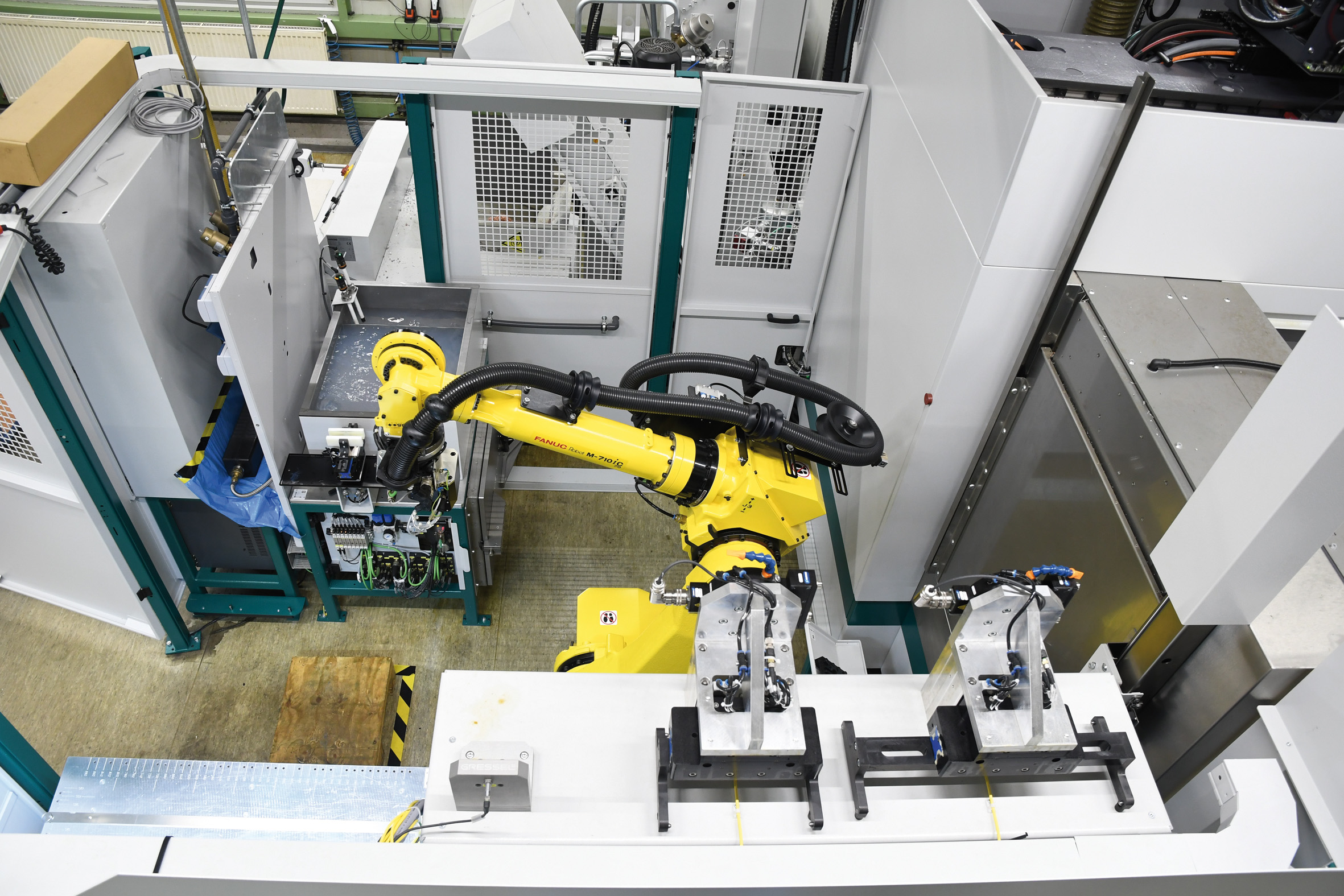
Eine „Fehlmann Versa 825“ wurde von FMB Maschinenbau zu einer Fertigungszelle mit teilespezifischer Automation ausgebaut. (Bild: Gressel)
Spezialist für NE-Metalle und Kunststoffe
FMV, 1976 als Werkzeugbau für die um Pforzheim angesiedelte Stanzindustrie gegründet, steht heute auf drei Standbeinen: Neben der Kühlplattenfertigung inklusive Zerspanung, Schweißen, Löten und abschließender Druck- und Dichtigkeitsprüfung ist das zweite die Lohnfertigung von Frästeilen für den Maschinenbau, wo auch Leistungen wie das Härten, Schleifen, Erodieren oder die Oberflächenveredlung erbracht werden. Die Kernkompetenz von FMV liegt hier in der Bearbeitung von NE-Metallen wie Aluminium und Kupfer, aber auch Kunststoffen, was die Prototypenphase mit Stückzahlen von 1 bis 10 und die Kleinserienfertigung umfasst. „Unser drittes Standbein ist die Fertigung von Sensorgehäusen, die ein breites Spektrum von Produkten mit hohen Stückzahlen abbildet“, erzählt der Geschäftsführer. „Für einen Sensorhersteller fertigen wir zum Beispiel aus Aluminium Gehäuse für Lichtschranken. Die Stückzahlen belaufen sich hier auf mehrere Tausend im Jahr, bei Dutzenden von verschiedenen Typen.“
Teilespezifische Automatisierung
Für die Automatisierung der Kühlplattenfertigung kam aufgrund der Teilegröße, der Spannsituation und des Anfangsinvests von Beginn an nur ein Teilehandling infrage. Das werkstückspezifische Vorgehen begründet sich zudem daraus, dass FMV hier mit Vakuumspannvorrichtungen arbeitet, die sich nicht palettieren lassen. Während das Handling somit auf die Kühlplatten zugeschnitten wurde, waren für die alternativen Teile weder die genauen Abmessungen noch die Spannsituation bekannt. „Wir brauchten daher ein System, mit dem wir mit wenig Aufwand auf unterschiedliche Aufspannsituationen und Teilegrößen reagieren konnten. Irgendwie mussten sich Mengen zwischen 10 und 50 beim Handhaben, Teachen und Rüsten wirtschaftlich abdecken lassen“, betont Würtemberger. „Die Lösung zeigte uns der R-C2-Flyer. Es war klar: Mit dieser Schraubstockautomation per Roboter und R-C2-Modul lassen sich 50 % plus unserer Arbeiten abdecken, weil maschinenseitig immer alles gleich ist. Ich muss mich nur um das Einfuttern kümmern, brauche aber schon mal nur für die Hälfte der Teile eine Lösung. Die Lösung, die wir dann mit FMB und Gressel erarbeitet haben, erfordert auch kaum Rüstaufwand.“
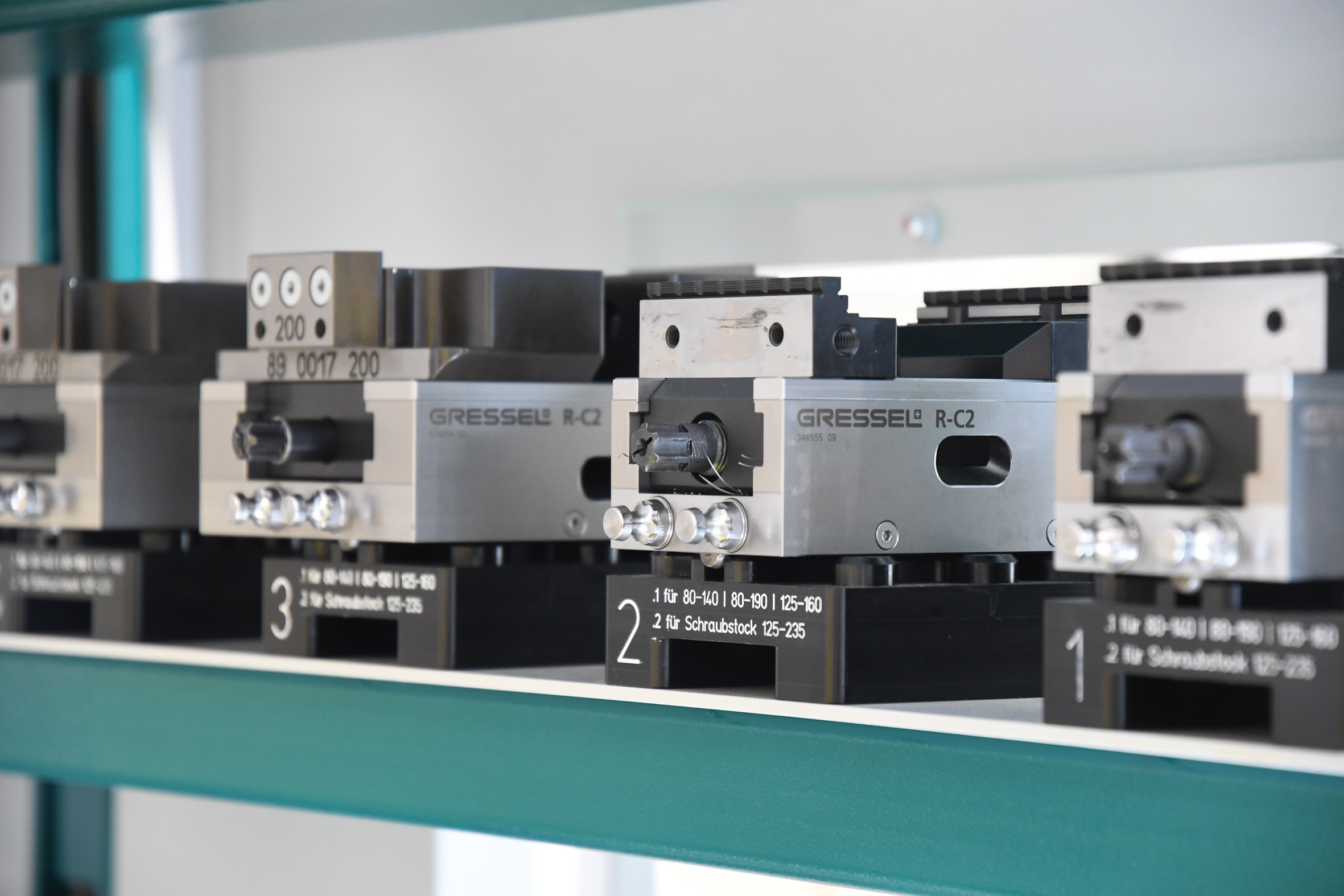
In der Schraubstockgarage können sechs gleiche Zentrischspanner oder drei Paare mit je zwei gleichen geparkt werden. (Bild: Gressel)
Werkstückbezogene Abläufe
Die Handhabung der verschiedenen Teilegruppen ist heute in Keltern-Dietlingen klar getrennt. Bei den Kühlplatten beginnt sie mit der Bereitstellung auf einem Wagen, der sich in der Zelle befindet. Von hier holt sich ein Pneumatikgreifer ein Bauteil ab und lädt es in die Maschine. Nach der Bearbeitung wird die Platte entnommen und gereinigt. Dafür taucht sie der Roboter in ein Reinigungsbecken, das in die Zelle integriert ist. Anhaftende Späne werden so entfernt, um das Bauteil in der nachfolgenden Wendestation nicht zu beschädigen. In dieser Station wird das Teil erst geparkt, um dann erneut eingelegt und bearbeitet zu werden. Ist dieser Schritt beendet, folgen wiederum Entnahme, Reinigung, Wenden und Einlegen. Schließlich wird die bereits bearbeitete Seite gefinisht. Während der Roboter die Maschine mit dem nächsten Bauteil bestückt und das Teil den ersten Arbeitsschritt durchläuft, wird das fertige Bauteil ausgiebig gereinigt und getrocknet sowie auf dem Wagen abgelegt.
„Bei der Arbeit mit dem R-C2 nutzen wir eine Schraubstockgarage, in der wir sechs Zentrischspanner vorhalten können“, berichtet Würtemberger. „Das können sechs gleiche sein oder drei Paare mit je zwei gleichen. Als Größen haben wir den R-C2 80 L-140 und den R-C2 125 L-160 im Einsatz, wobei wir 80 % unseres Teilespektrums mit dem Zentrischspanner 80 L-140 abdecken. Die Teile, die wir typischerweise bearbeiten, besitzen Abmessungen von 40x40x80 mm.“ Die Anlage selbst ist konzipiert für Geometrien von 12 x 20 mm bei beliebiger Länge bis 220x150x400 mm. Der Roboter kann bis zu 70 kg handeln, was aber abhängig vom Abstand zur sechsten Achse ist. Das R-C2 System ist ausgelegt für das Schraubstockhandling mit 30 kg und für Paletten mit 50 kg.
Fertigung in 15 Minuten vorbereiten
Die Anlagenbedienung erfolgt über zwei Oberflächen. „Auf dem ersten Bildschirm definiere ich alles, was mit dem Teil zu tun hat: Welchen Grundkörper vom Schraubstock möchte ich verwenden? Was für Schraubstockbacken habe ich drauf? Wie hoch ist das Teil? Auf welches Maß muss der Schraubstock greifen?“, erzählt Würtemberger. Mit diesen vier Informationen hat er schon einmal alles definiert, was das Teil anbelangt. „Am zweiten Bildschirm gebe ich dann die Informationen zum Teilewagen ein. Hier muss ich nur definieren, in welchem Rastermaß X und Y die Teile liegen, an welcher Position ich sie abholen möchte. Dann drücke ich Start, und los geht‘s. Mit ein bisschen Übung dauert das eine Viertelstunde. Sollte ein Backentausch nötig sein, dauert es eben ein wenig länger. Durch den großen Greifbereich im Vergleich zu einem pneumatischen Greifer sind manuelle Eingriffe aber deutlich seltener nötig.“
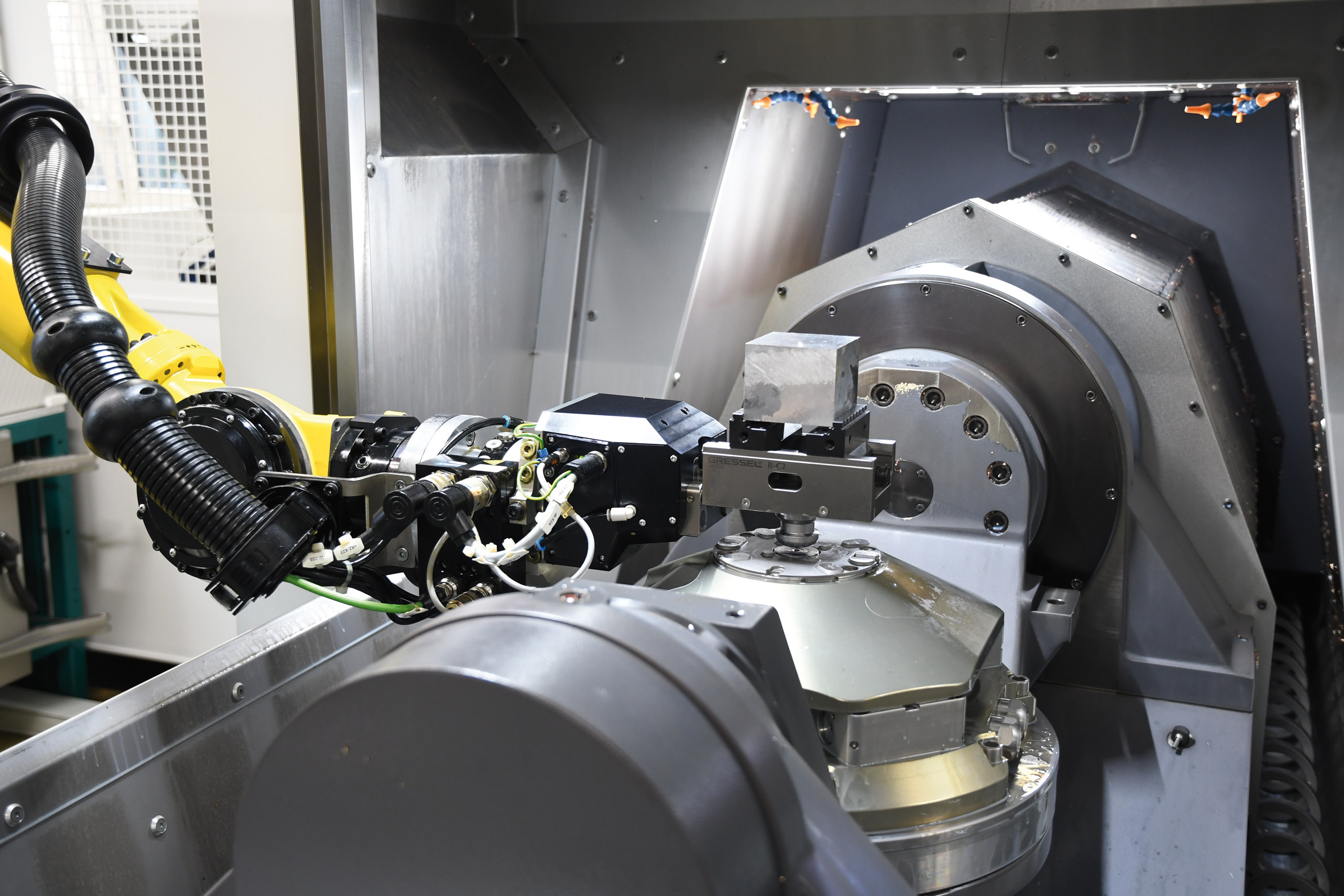
Der Roboter setzt das Bauteil via R-C2-Modul auf das Nullpunktspannsystem der Maschine. (Bild: Gressel)
Sobald die bauteil- und wagenspezifischen Angaben vereinbart und Start gedrückt wurde, fährt der Roboter die Schraubstockgarage ab und scannt, ob der richtige Grundkörper am korrekten Platz sitzt. Ist sichergestellt, dass keine Kollision auftreten kann, holt er sich den Grundkörper, bestückt diesen und wartet damit vor der Maschine, bis er ihn einlegen kann. Danach fährt der Roboter wieder aus dem Maschinenraum. „Bei uns ist die Maschine der Master, sie steuert die Zelle und gibt dem Roboter das Signal, das nächste Bauteil vorzubereiten. Während das erste Bauteil in Bearbeitung ist, holt sich der Roboter den zweiten Schraubstock und das zweite Teil, um sie dann in der Vorlegestation aufzulegen. Nun erfolgt ein permanenter Wechsel aus dieser Station.“
Brücken schlagen
„Der entscheidende Effekt der R-C2-Automation ist heute der beabsichtigte: Wir verhindern damit Maschinenstillstandzeiten“, resümiert Würtemberger. „Über eine Talsohle, die im Halbleitermarkt schon mal ein halbes oder dreiviertel Jahr anhalten kann, schlagen wir die Brücke, weil das System perfekt zu unseren anderen Kunden und deren Teilespektrum passt.“ Gleichzeitig ermöglicht die Schraubstockautomation das wirtschaftliche Fertigen verschieden großer Serien. „Wir können teilespezifisch auch noch die letzte Sekunde optimieren, was uns besonders bei größeren Losen wettbewerbsfähig macht.“ Natürlich müsse der Roboter mit einem gewissen Aufwand programmiert werden. Weil FMV mit FMB jedoch viel Arbeit in die Bedienoberfläche gesteckt hat, lohne sich dieser Mehraufwand schon ab geringen Stückzahlen. Ohnehin sei es wirtschaftlich, gleichartige Teile automatisiert in den Abend oder die Nacht hineinlaufen zu lassen. „Unterschiedliche Teile können wir nachts nicht abarbeiten, was nicht am R-C2, sondern an unserer Anlage liegt“, ordnet Würtemberger ein. „Wir haben keinen übergeordneten Job-Shop-Manager, mit dem sich wechselnde Teile realisieren lassen. Das ist aber nur sinnvoll für eine Anlage, die ausschließlich mit der R-C2-Automation arbeitet, um alles abzudecken und die maximale Laufzeit herauszuholen.“
Komplett mannlos bearbeiten
Womit der Geschäftsführer bereits nach vorn blickt, denn eine 6-Seiten-Station ist ein zentraler Punkt der weiteren Zusammenarbeit von FMV und Gressel. Im Moment prüft FMV hier zwei grundlegende Ansätze: Der erste ist die Automation einer nächsten Maschine ausschließlich mit dem R-C2-System und einer 6-Seiten-Station, womit die mannlose 6-Seiten-Bearbeitung möglich wird. „Das ist der wahrscheinlichere Schritt, weil die bestehenden Anlagen in den nächsten Jahren wohl vorwiegend mit den Kühlplatten ausgelastet sein werden“, schätzt Würtemberger ein. „Alternativ könnten wir die 6-Seiten-Station an einer Bestandsanlage in Betrieb nehmen. Zum Beispiel am Ende eines Produktlebenszyklus, wenn klar ist, dass die Teile, für die die Zelle konzipiert wurde, nicht mehr oder nicht mehr in dem Umfang kommen.“ Sobald eine Zelle 70 % der Zeit mit dem R-C2 arbeitet, sei eine 6-Seiten-Station sinnvoll. Wenn die Zelle so umgenutzt wird, könne auch noch mehr auf das R-C2 hin optimiert werden, zum Beispiel, was das Vorhalten unterschiedlicher Teile betrifft. Wie genau die Lösung aussehend wird, wird sich erweisen. „In jedem Fall ist das R-C2 für uns perfekt“, urteilt der Geschäftsführer. Aufgrund der überzeugenden Qualität, der Langlebigkeit der Produkte und einer Ersatzteilversorgung, die der Langlebigkeit angepasst ist, arbeitet FMV im Übrigen schon seit den 1980er mit Gressel zusammen. Zur Automation war es jedoch das erste gemeinsame Projekt. Deshalb hatte Würtemberger ja auch noch keinen Flyer…
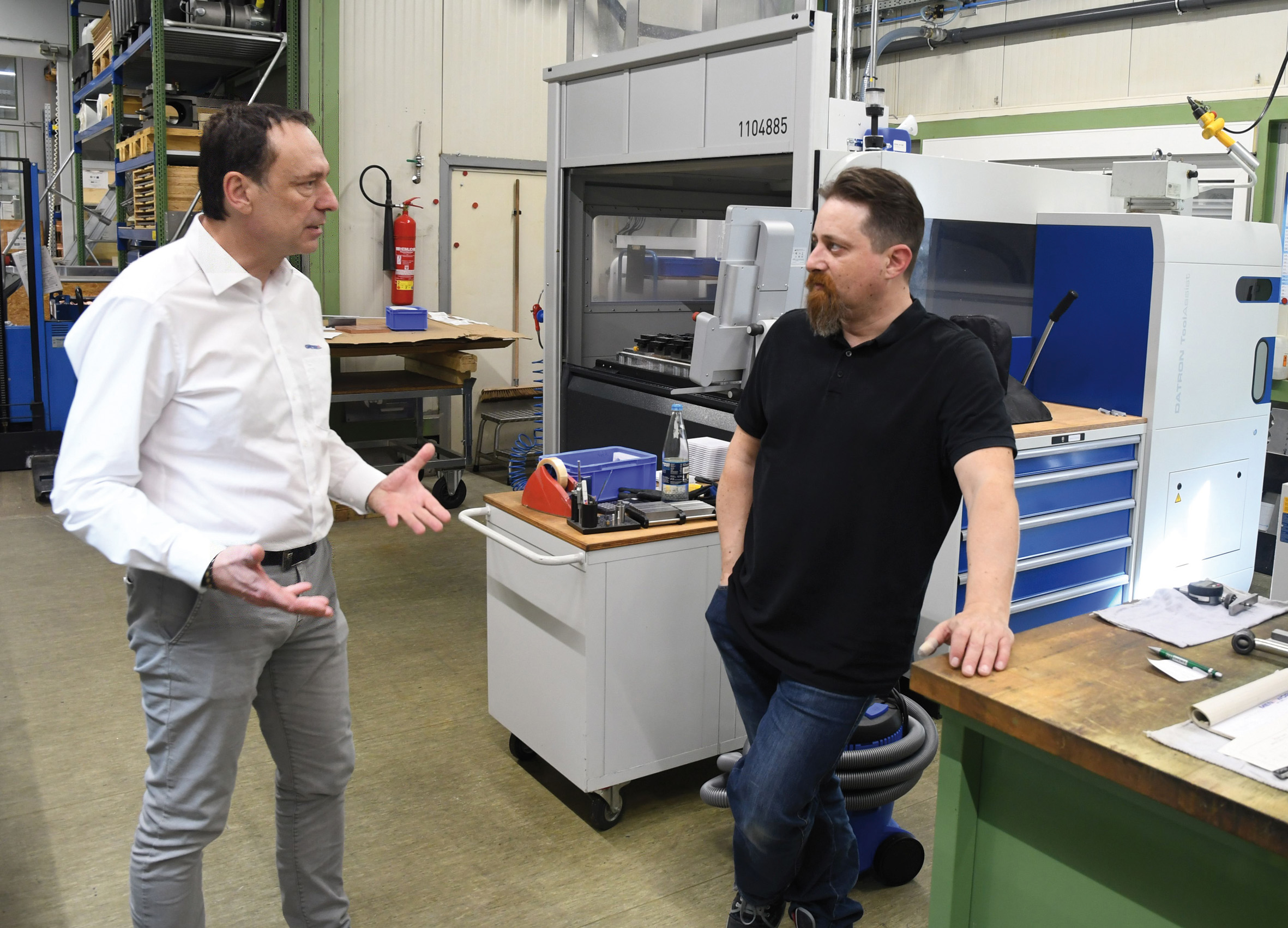
Andreas Brunhofer (links) und Till Würtemberger denken derzeit über das Konzept zur Nutzung einer 6-Seiten-Station von Gressel für die mannlose Bearbeitung nach. (Bild: Gressel)
