Höchste Präzision für Keramik-Bauteile
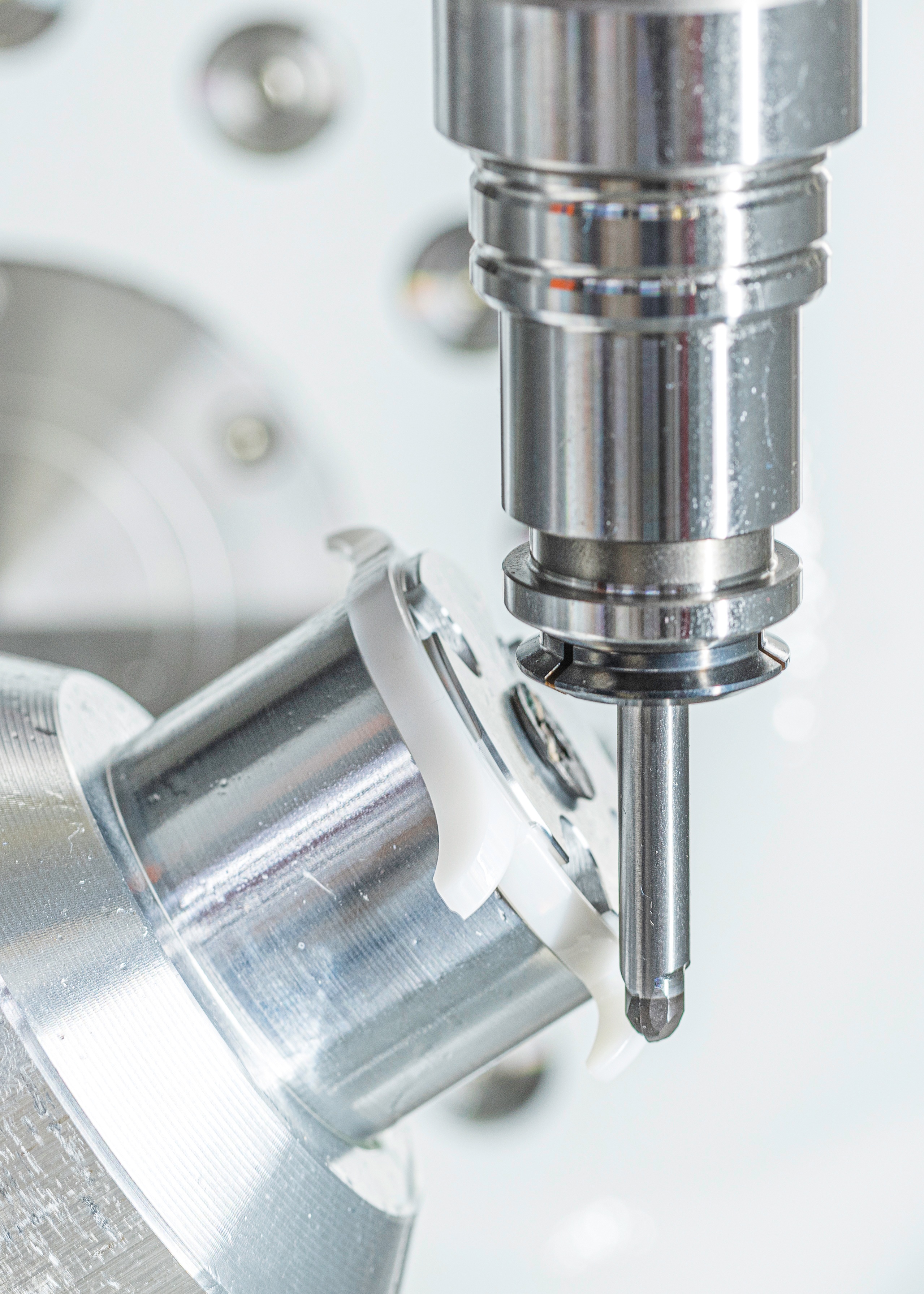
Duktiler Schnittmodus auf Kern Micro HD im Praxiseinsatz Seit Mitte 2021 produziert die Auftragsfertigung der Kern Microtechnik GmbH diverse Keramikbauteile, die beispielsweise in der Analytik zum Einsatz kommen. Der von Kern entwickelte duktile Schnittmodus spielt hierbei eine bedeutende Rolle. Den Ingenieuren und Technikern des Unternehmens gelang es in enger Zusammenarbeit mit den Auftraggebern, einen stabilen Prozess zu generieren, der höchste Qualität und eine Ausschussquote von Null zum Ergebnis hat.
Unternehmen der Analytik-, Chemie- und Halbleiter-Branche haben ebenso darauf gewartet wie Hersteller von hochpräzisen Bauteilen für Messmaschinen, Uhren/Schmuck, Satellitentechnik und vielem mehr. Die Rede ist von der prozesssicheren Bearbeitung technischer Keramik wie Siliziumcarbid, Aluminiumoxiden etc. Die extreme Härte, Steifigkeit, Wärme- und chemische Beständigkeit dieser Werkstoffe sowie deren gute Temperaturleitfähigkeit machen technische Keramik für viele Einsätze interessant.
Ihre vielfältigen Vorteile stellen aber gleichzeitig ein Problem dar: Die Bearbeitung ist hochanspruchsvoll. Auch, weil keramische Produkte makellos gefertigt sein müssen. Risse, Abplatzer und Beschädigungen des Materials würden zum Bauteilversagen führen, da eine Rissausbreitung nicht – wie in Metallen – gehemmt ist. Zudem müssen die Teile mit höchster dimensionaler Präzision gefertigt werden.
Als traditionelle Bearbeitungsprozesse haben sich Läppen, Honen und Schleifen bewährt. Damit verbunden ist allerdings eine große Einschränkung in der wählbaren Form der Bauteile. Zudem besteht eine erhebliche Prozessunsicherheit, sobald diverse Konturen einzubringen sind. Genau hier setzt der von Kern-Ingenieuren entwickelte duktile Schnittmodus an, der inzwischen zunehmend in der Praxis Einzug hält. Spezielle Fräswerkzeuge mit geometrisch bestimmter Schneide erlauben es damit, spröde Keramik mit fließendem Span abzutragen.
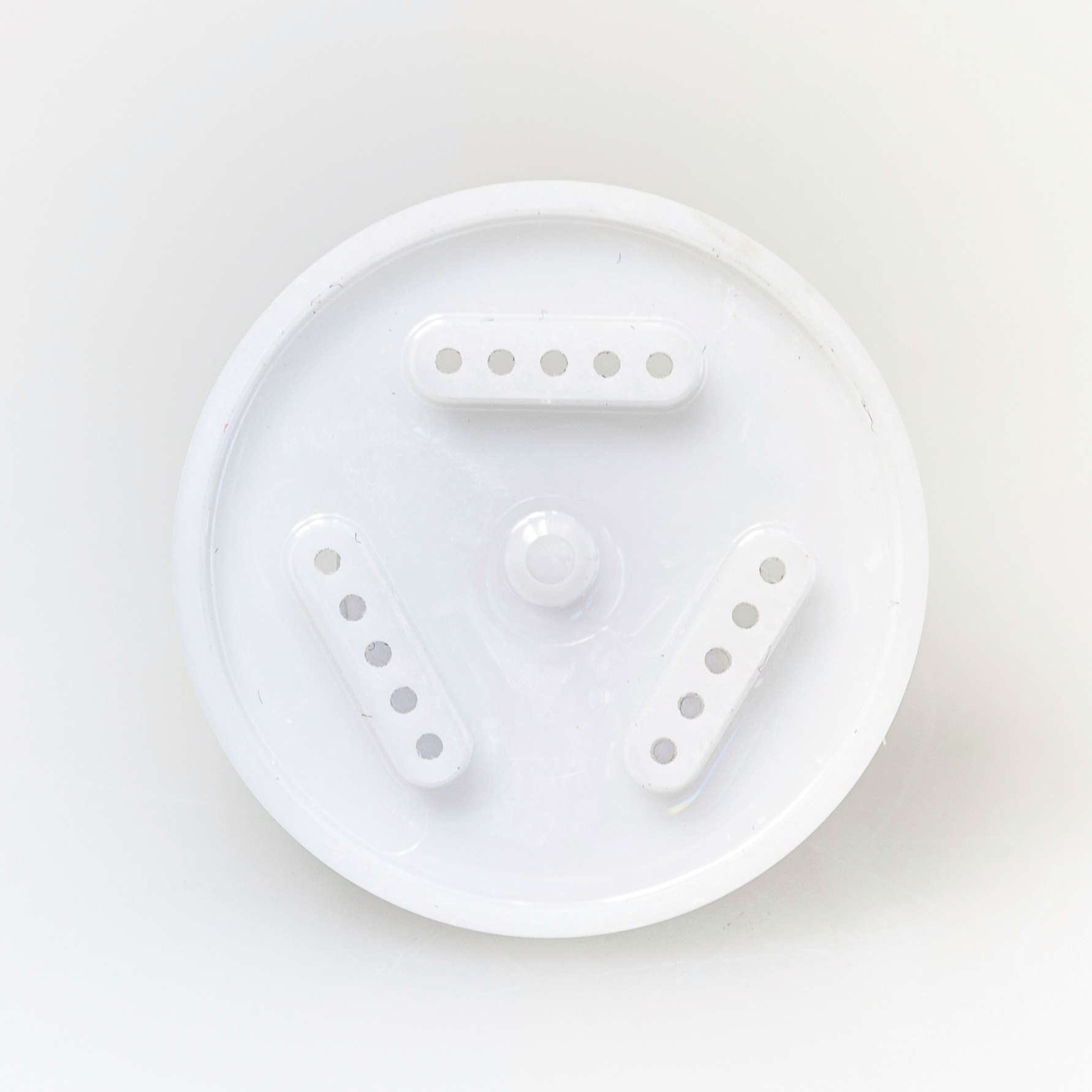
Das abgebildete Musterteil aus Zirkonia Oxide wurde komplett durch Bohren und Fräsen mit Voll-PKD-Werkzeugen und duktilem Schnittmodus hergestellt.
Keramikbearbeitung mit prozessstabiler Qualität
Alexander Stauder, Leiter Anwendungstechnik, erklärt dazu: „Wir erzielen damit in der Praxis vielfältige Vorteile. An oberster Stelle steht die deutlich höhere und prozessstabile Qualität – in punkto Bearbeitungsgenauigkeit ebenso wie im Hinblick auf die Oberfläche.“ So lassen sich etwa in Abhängigkeit der Keramikgüte Rauheiten Ra/Sa im Bereich einiger 10 nm erzeugen und Bearbeitungsgenauigkeiten im unteren Micrometerbereich erreichen.
Häufig gelingt es zudem, die Bearbeitungszeit deutlich zu reduzieren, was letztlich zu höherer Wirtschaftlichkeit führt. Hier gibt es jedoch Einschränkungen. Als Faustformel gilt: Je größer die Werkstücke bzw. die einzubringenden Bohrungen und Nuten sind, desto sinnvoller ist es, den ersten, größeren Materialabtrag mit preisgünstigen Schleifstiften zu erledigen. Dann bleibt fürs Fräsen mit teuren Werkzeugen, die meist mehrere hundert Euro kosten, nur das wichtige Finish. Je kleiner die Werkstücke bzw. die einzubringenden Bohrungen und Nuten sind, desto produktiver ist es, direkt mit dem duktilen Schnittmodus zu fräsen.
Für beide Verfahren ist eine extrem prozessstabile Maschine wichtig, die höchste Genauigkeiten erzielt. Hohe Steifigkeit und Laufruhe, eine schnell drehende Spindel und Beständigkeit gegen den abrasiven Keramikabtrag sind Grundvoraussetzungen für die Bearbeitung im duktilen Schnittmodus wie auch für das Präzisionsschleifen.
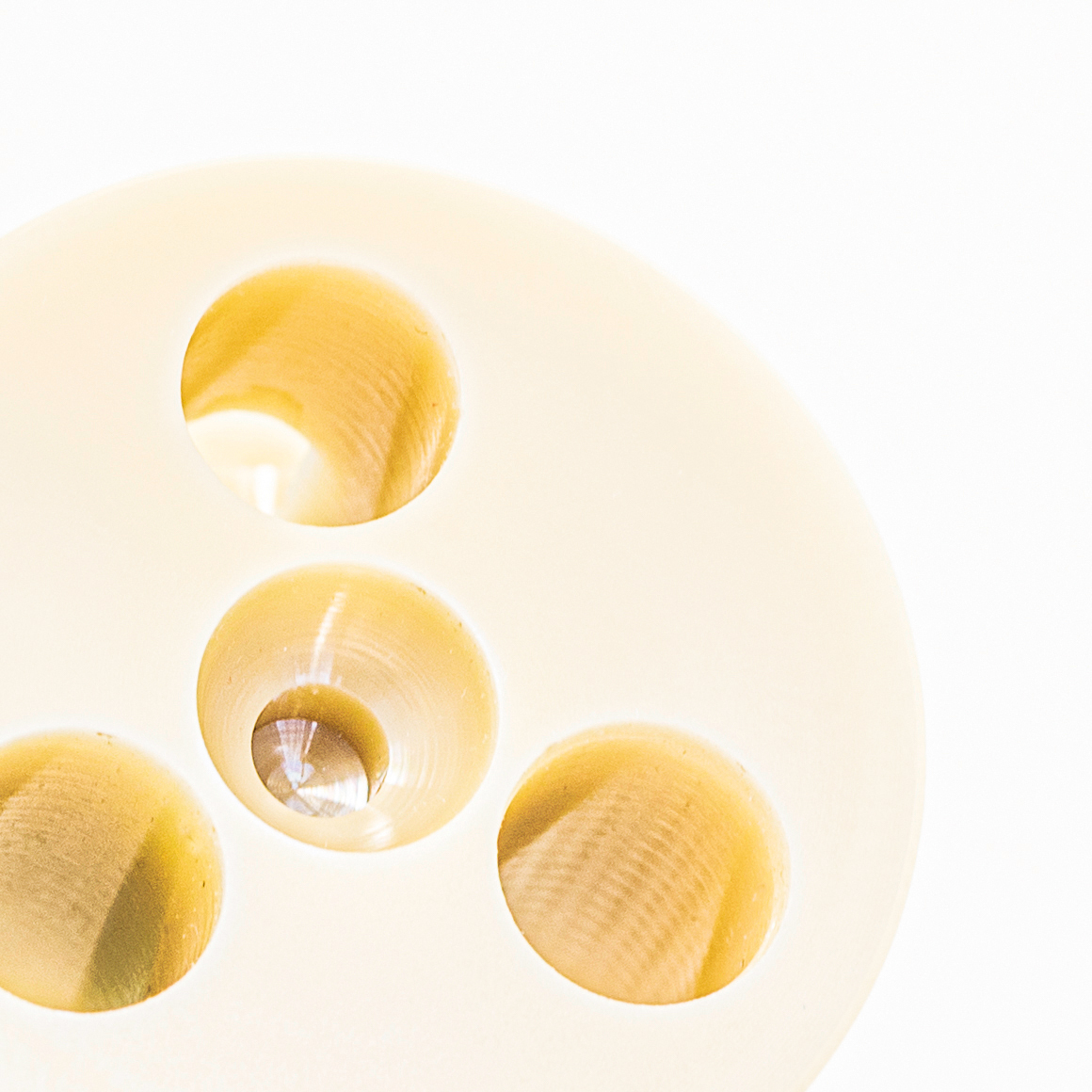
Dieses Bauteil aus „Aluminiumoxid verstärktem Zirkoniumoxid“ wurde auf der Kern Micro HD in einer Aufspannung gefertigt. Entscheidend dafür: Sie beherrscht das Koordinatenschleifen ebenso perfekt wie das Fräsen mit duktilem Schnittmodus.
Vielfältige Anforderungen an Bearbeitungszentrum
Entsprechend gut für diese Bearbeitung eignet sich die Kern Micro HD. Durch eine clevere Achsanordnung ist die Mechanik dieses Highend-Fünfachsfräszentrums perfekt vor dem abrasiven Keramikstaub geschützt. Der Maschinenaufbau sowie die einmalige Mikrospalthydrostatik sorgen für höchste Steifigkeit. In Kombination mit der 15 kW-starken Hochgeschwindigkeitsspindel, die Drehzahlen bis zu 42.000 min-1 erreicht und mit HSK 40 Schnittstelle ausgestattet ist, garantiert das Bearbeitungszentrum höchste Laufruhe sowie einen wirtschaftlichen Materialabtrag.
Den technischen Merkmalen entsprechend, beherrscht die Kern Micro HD das Koordinatenschleifen ebenso perfekt wie das Fräsen mit duktilem Schnittmodus. Bei Bedarf kann also ohne umzuspannen erst geschliffen und dann final gefräst werden. Ein Vorteil, der sich durch den Gewinn von Zeit und Genauigkeit doppelt positiv auswirkt.
Entscheidend für den Erfolg in der Praxis sind laut Alexander Stauder jedoch noch weitere Faktoren. Neben dem prozesssicheren und leistungsfähigen Fünfachsfräszentrum steht vor allem die Kommunikation zwischen allen Beteiligten weit oben auf seiner Prioritätenliste: „Keiner kennt das herzustellende Keramikprodukt und dessen Anforderungen so gut wie unser Auftraggeber, der oft auch der Entwickler ist. Andererseits kennt niemand die Maschine so gut wie wir in der Anwendungstechnik und der Auftragsfertigung. Dieses Know-how muss zusammenkommen.“
Genau in dieser Weise wurden inzwischen erste Projekte erfolgreich umgesetzt. Dabei sind die Anteile an Schleifbearbeitung und duktilem Fräsen sehr unterschiedlich. Da etwa die Bauteile und Bearbeitungsaufgaben in der Uhren- und Schmuckindustrie immer sehr klein sind, wird hier häufig direkt gefräst.
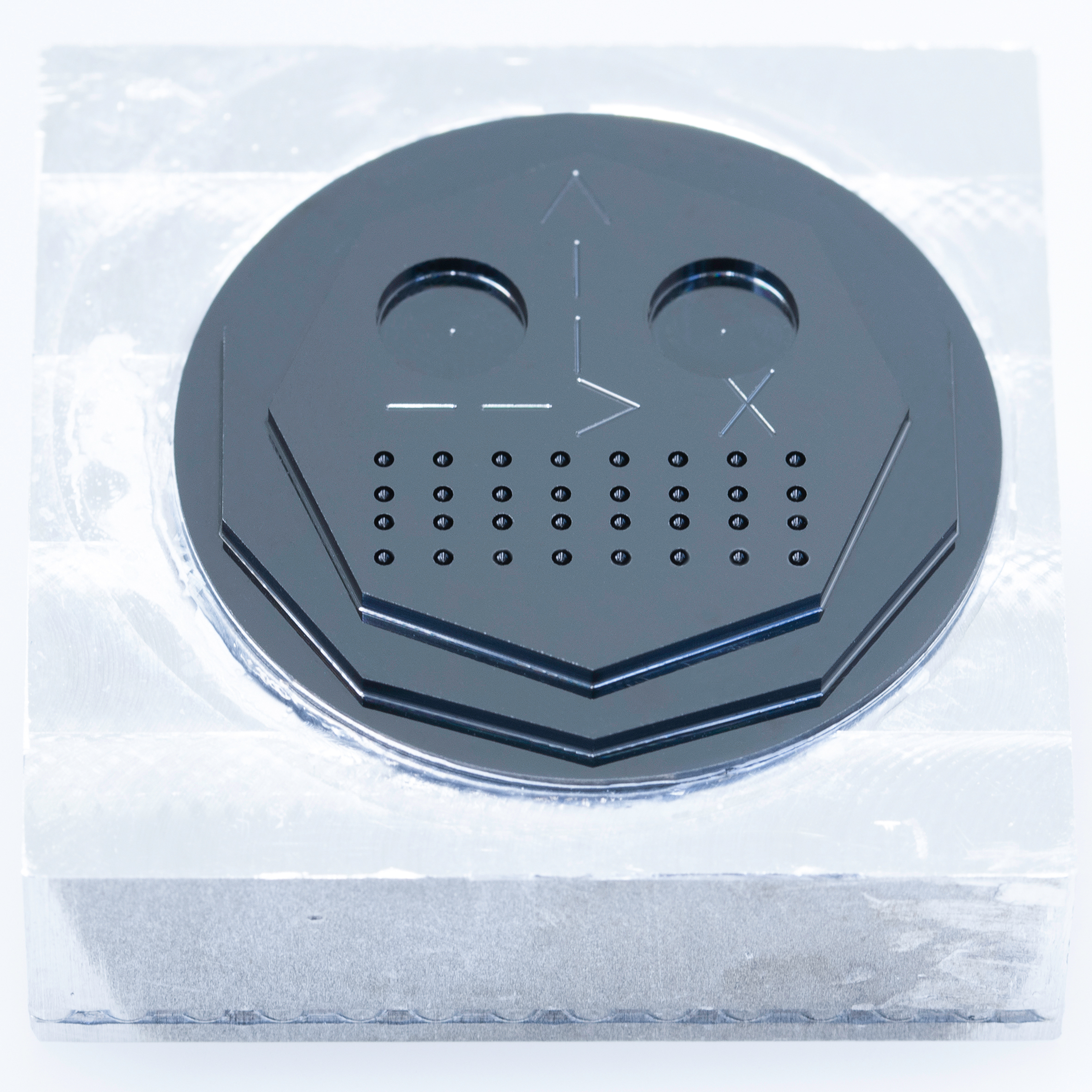
Das Fräsen von Keramik mit dem von Kern entwickelten duktilen Schnittmodus ist umso produktiver, je kleiner die Werkstücke bzw. die einzubringenden Bohrungen und Nuten sind.
Praxisbeispiel: Ausschussquote Null erreicht
In einem aktuellen Auftrag stellt Kern diverse Keramikbauteile her, die in der Analytik zum Einsatz kommen. Diese wurden früher von einem anderen Lohnfertiger durchgängig durch Schleifbearbeitung produziert. Stauder dazu: „Wie uns der Kunde erzählt hat, war ein Hauptproblem, dass kleine Ungenauigkeiten und feinste Kantenbrüche der Einzelteile immer wieder zu Ausfällen der Baugruppe führten. Diese Ausschussquote konnten wir durch den Wechsel zu unserer Auftragsfertigung in Murnau komplett eliminieren.“
Hier werden nun in acht Technologieschritten – vom Pulver bis zum Fertigteil – alle Fertigungsaufgaben aus einer Hand erledigt. Die letzten beiden Bearbeitungsschritte erfolgen auf der Kern Micro HD. Auf ihr werden die ersten Abtragraten durch Koordinatenschleifen mit Schleifstiften erledigt. Danach – und entscheidend für den großen Erfolg – kommt das Finish mit duktilem Frässchnittmodus. In aufwändigen Tests ermittelte das Anwendungstechnik-Team von Kern gemeinsam mit dem Auftraggeber die perfekte mittlere Spandicke, die notwendig ist, um den Keramikspan sauber fließen zu lassen. „Das enge Prozessfenster muss zuverlässig eingehalten werden“, erklärt Stauder, „da sonst die Teilequalität leidet und eine hohe Abnutzungsrate der teuren Werkzeuge die Folge sind.“
Nachdem die passenden Prozessparameter für die Bearbeitung des verwendeten Keramikwerkstoffes ermittelt wurden, galt es, diese zu 100 Prozent prozessstabil auszuführen. Eine Aufgabe, die in Murnau die Kern Micro HD perfekt erfüllt. Seit gut einem Jahr läuft das Projekt. Heißt: Die gewünschten Oxidkeramik-Bauteile werden vollautomatisiert 24/7 in Serie zerspant – ohne Ausschuss und mit einer Bearbeitungsgenauigkeit von < 2 µm.
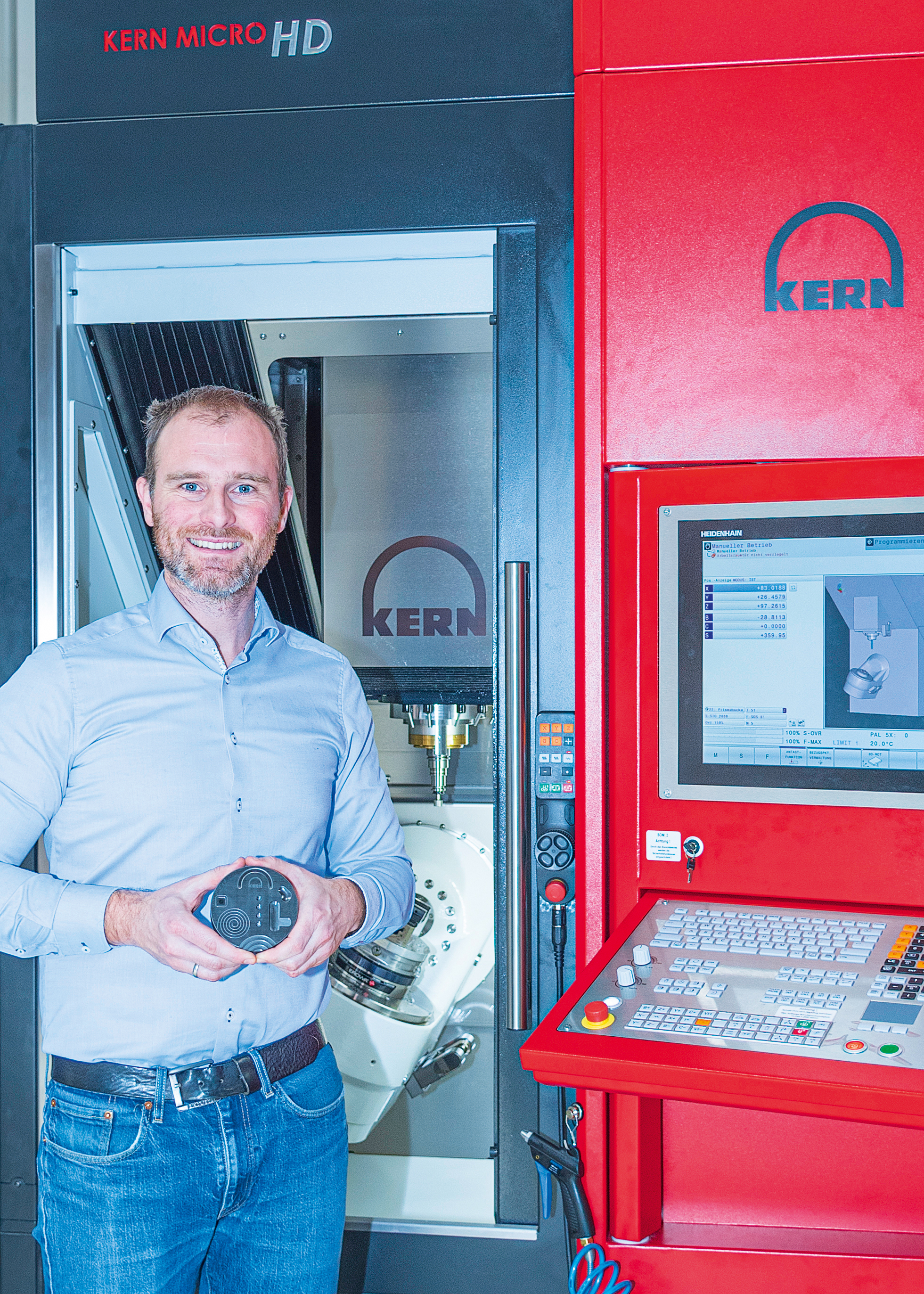
Alexander Stauder, Leiter Anwendungstechnik der Kern Microtechnik GmbH: „Bei Keramikbauteilen, die in der Analytik zum Einsatz kommen, ist es uns gelungen, die Ausschussquote auf Null zu senken.“
