Insert manufacturing made easy
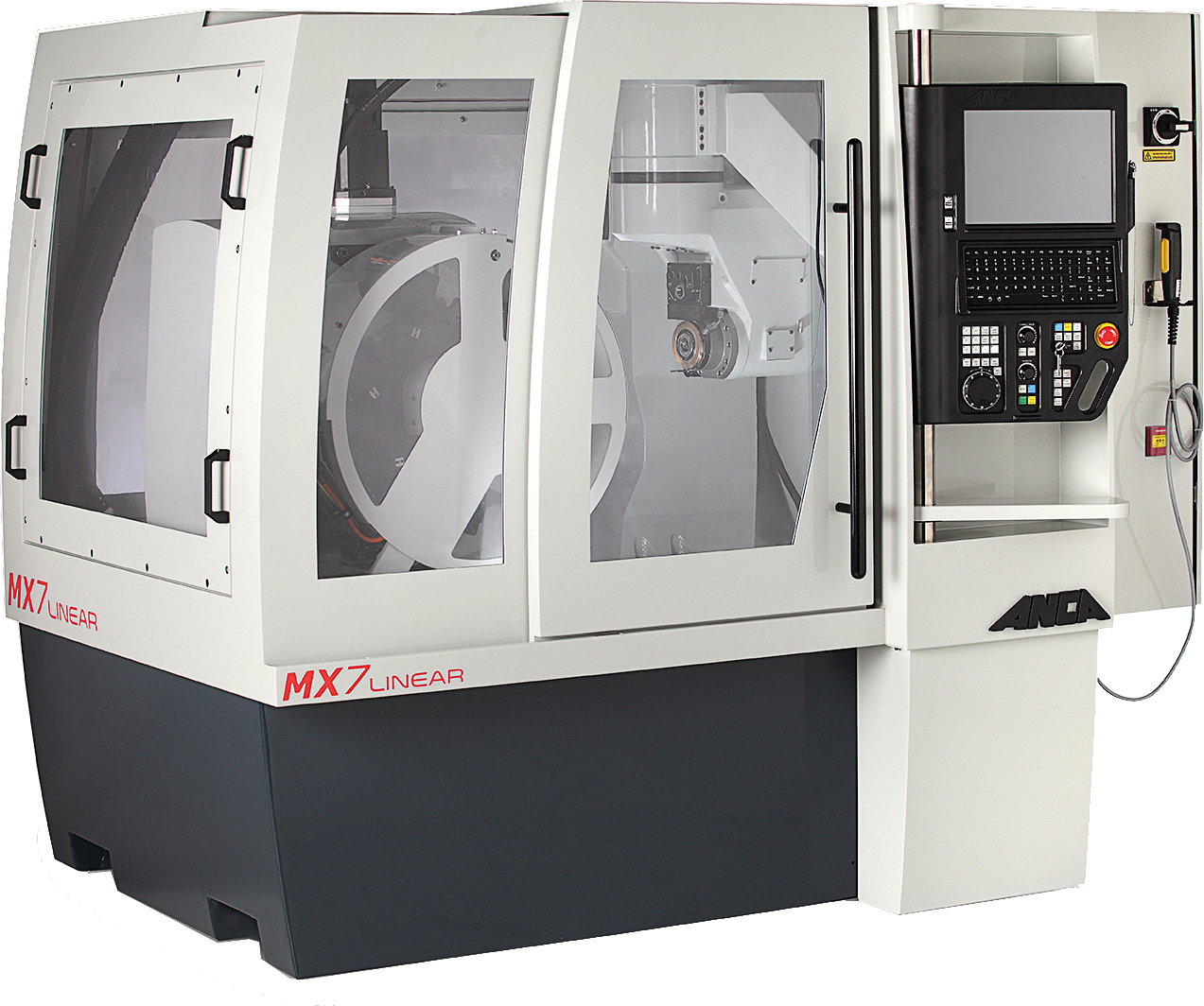
Solid endmill and drill production is a highly competitive market, making it challenging for manufacturers to differentiate themselves from their competitors. Inserts for milling and drilling applications offer various advantages over solid carbide tools, but present unique challenges in manufacturing. For those that successfully master the production of insert tools, new market opportunities can be theirs. ANCA’s insert grinding solutions may just be the answer they need to take this step.
Inserts appeal to users of tools, firstly because one tool body can take a variety of inserts, making them very versatile. Additionally, the cost of replacing just the insert is significantly less than an entire solid carbide tool. For insert manufacturers however, the challenge is automated production of these uniquely shaped parts.
The ANCA Insert Solution, based on the MX tool grinding machine platform, offers work-holding, automation and supporting tool programming software to produce a diverse range of rotary endmill and drill inserts. Inserts that feature common locating datums and clamping features are an ideal fit for the ANCA Insert Solution.
ANCA’s unique insert chuck provides the foundation of insert grinding capability
Its versatile design means one chuck can hold a variety of inserts with precise repeatability and necessary rigidity during the grinding operation. Onto the standard chuck, interchangeable jaws are fitted in minutes. These jaws are custom designed based on the insert datum and holding features, as well as considering wheel clearance for necessary grinding operations. ANCA will work with customers to design jaw sets that cover their complete insert design and size range.
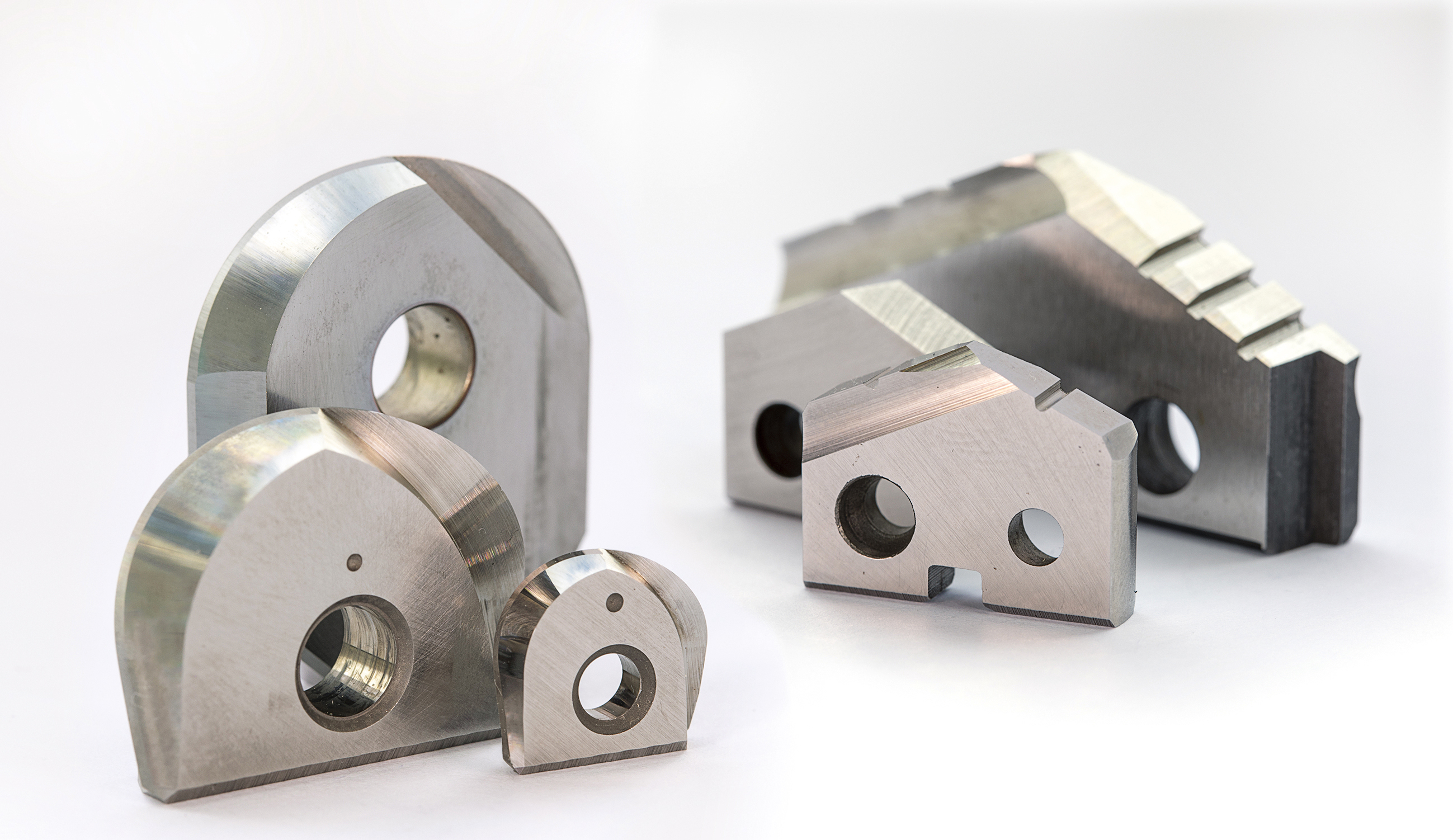
Samples of inserts manufactured on ANCA machines.
Economical production requires automation
For insert grinding, the RoboMate robot loading system is kitted up with the dedicated pallets and grippers for unattended manufacturing. As with the chuck jaws, ANCA will collaborate with you to design a range to pallets and grippers that suit your inserts.
Comprehensive and flexible programming software is the final element needed for insert grinding. As always, ANCA has it covered with iGrind – the industry-leading tool programming software, that caters for various special endmill and drill insert geometries. In addition, special digitising routines will determine the datum location and exact position of the insert before commencing the grinding operation. This ensures the insert production batch remains accurate and consistent, delivering quality results expected in the market.
Finally, with production flexibility in mind, the insert grinding system can be easily switched over to solid carbide tool production, meaning a given grinding machine is not locked into production of just one tool type. By switching the Insert Chuck for PremierPlus collet system, and replacing RoboMate pallets and grippers, the transition to solid tool production can be done quickly and efficiently, ensuring that the machine’s productive grinding time is maximised and adaptable to market demands.
The insert grinding solution is offered not only on new machines, but can equally be retrofitted on existing MX machines. Setting up for diversifying cutting tool product portfolio to include inserts has never been easier. Having alternate production capabilities that can quickly be adapted to meet customer demands is a winning long-term strategy for the success of any tool grinding business.
Application example:
A custom solution for AB Tools
MX7 Linear autoloads and grinds Shear Hog Carbide Inserts with ANCA’s MX7 with RoboMate.
ANCA has a focus on the market to inspire and guide product and portfolio development. Rather than only offer a standard product range, custom solutions are frequently addressed. ANCA’s Engineering team can custom design mechanical, electrical, software and process solutions to enhance the standard product range and meet unique customer requirements. Recently, AB Tools, Inc. – a US based specialist tool manufacturer, requested a solution to manufacture special carbide inserts. They were seeing a growing demand for this product and asked ANCA to supply a solution based on an MX7 Linear for autoloading and grinding special inserts as existing machinery and processes were not versatile enough for them to successfully meet their demands. Alfred Lyon, AB Tools Shop Supervisor said: “We were extremely impressed with the whole process. From our own testing to ANCA’s product managers helping to scope out our needs and what we wanted to accomplish to the incredible Customer Solutions team who then took our requirements and ran with it.”
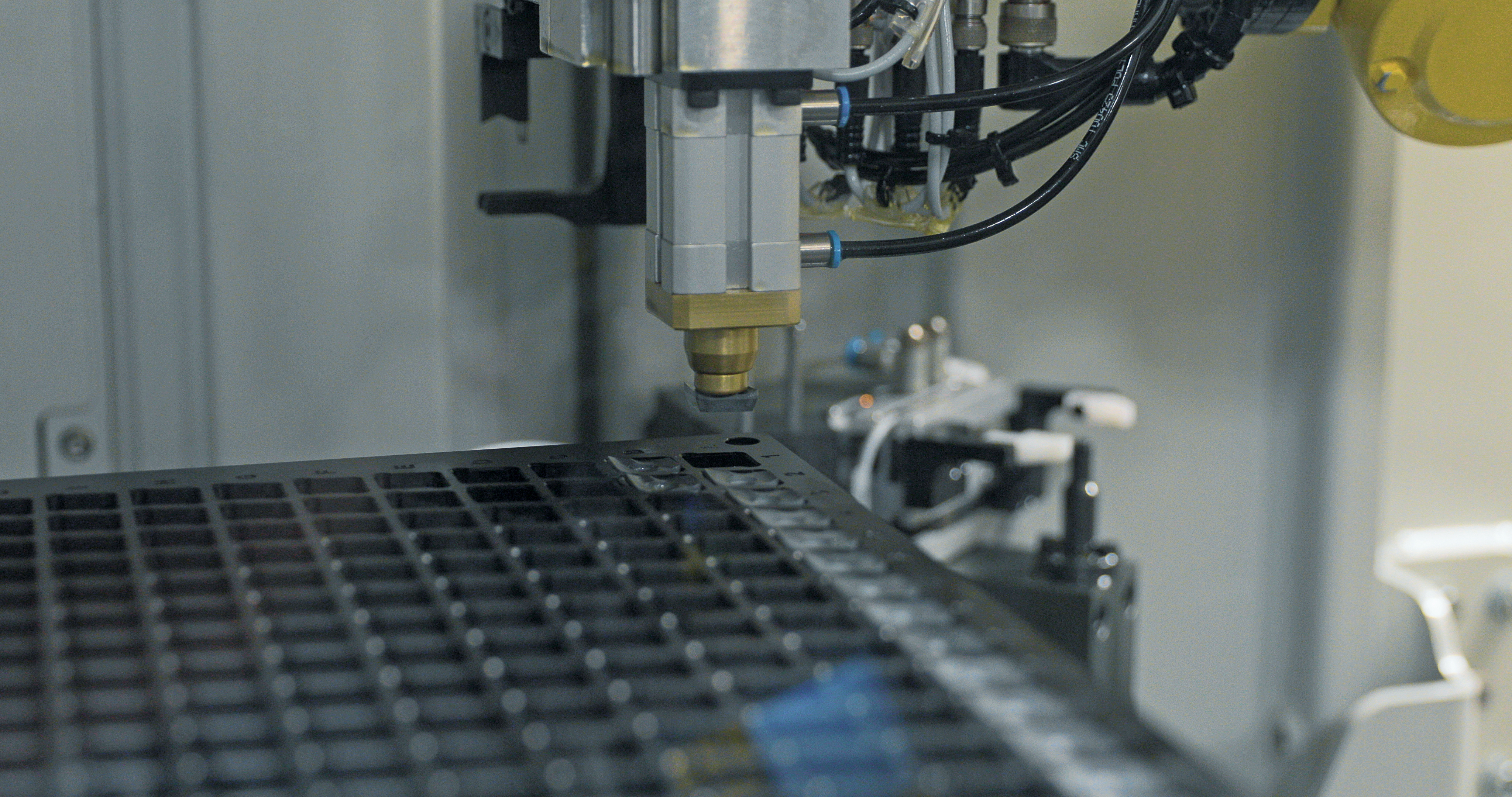
Gripper head – magnet for picking and placement of the insert
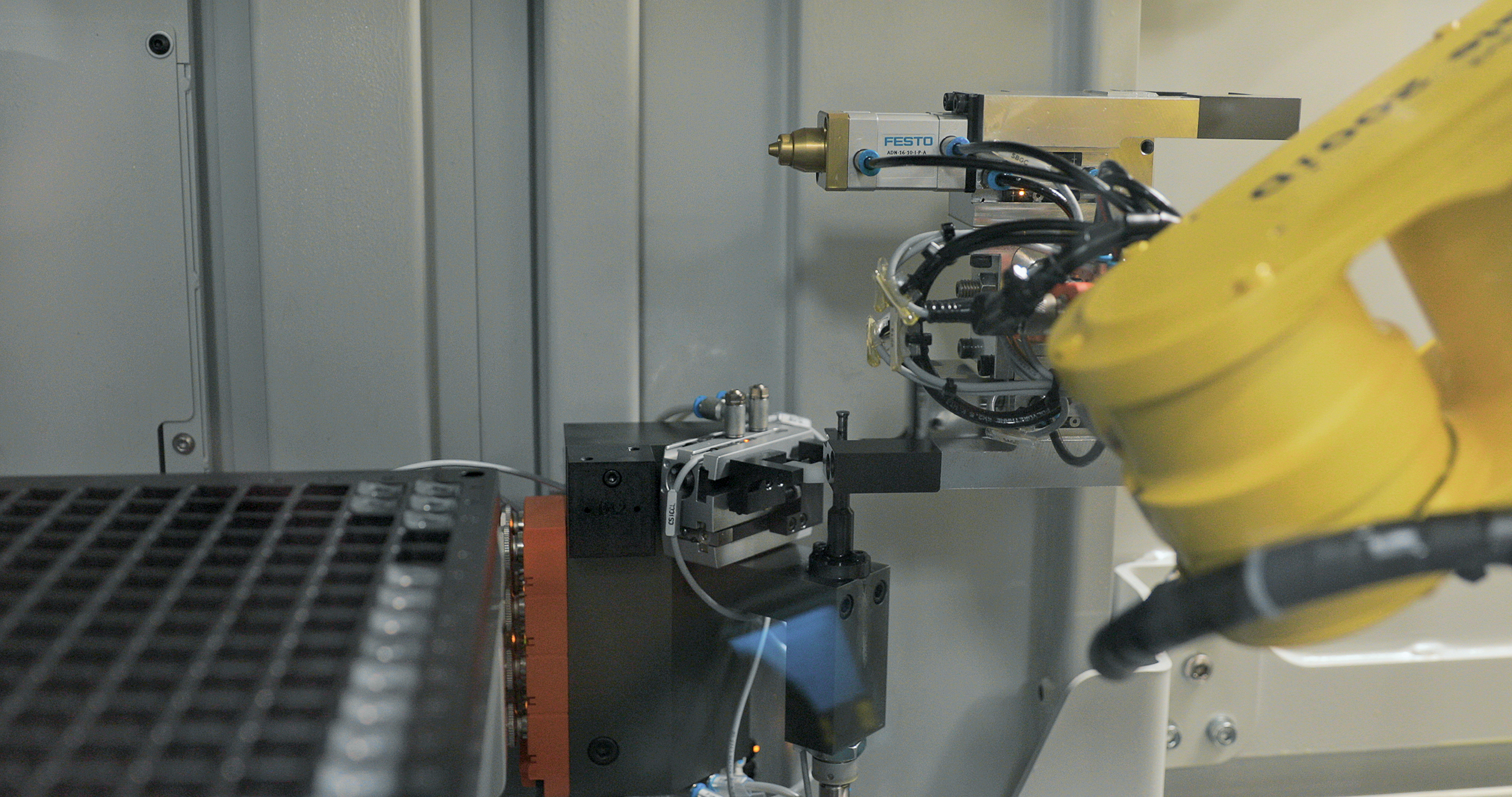
Interchange station for loading the nail into the insert.
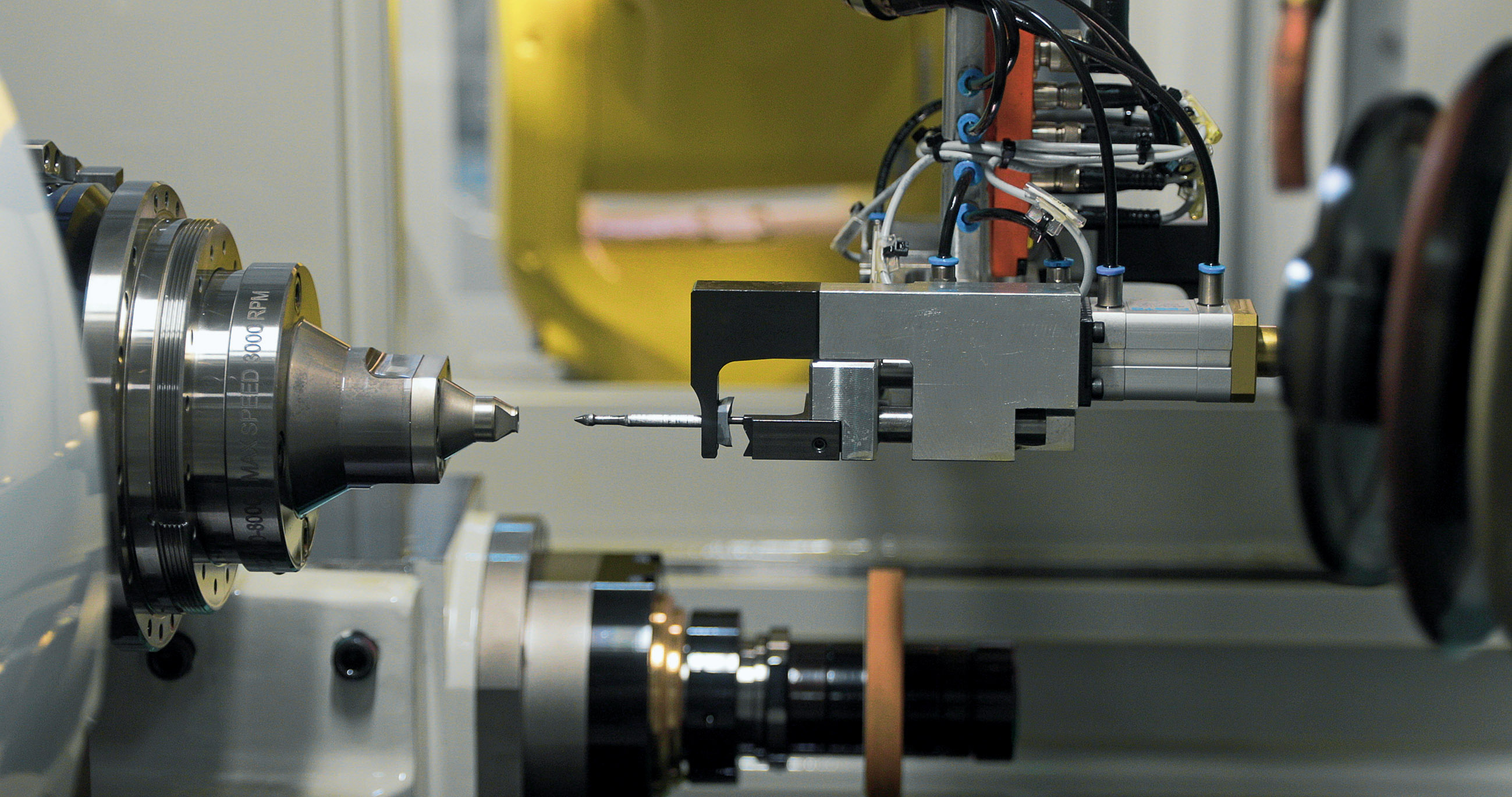
Gripper fingers securely hold the inserts and nail.
The engineering team was requested to deliver a solution that was able to:
- Autoload and grind a range of AB Tools shear hog inserts
- Perform grinding operations in one setup
- Meet cycle time requirements
The custom solutions engineering team delivered an enhancement to the ANCA MX7 with Robomate. New designs developed included:
- A modification to the loading system with custom pallets to suit the inserts. The custom pallets can hold up to 442 inserts, this capacity can easily be increased by ordering the four pallet upgrade option available on the MX7 Robomate.
- A modification to the robot gripper head allows the robot to pick up and handle the insert/nail combination. Robot loading software was developed to enable to the machine to pick up the insert and load and unload the nail via an interchange station.
- Custom anvil nose work holding to clamp the inserts, with the added benefit of a variable force drawbar system. This drawbar allows flexibility to grind different sized inserts and to effectively clamp different sized tooling.
- A software interface to allow for the adjustment of specified insert parameters including – corner radius, periphery relief angle and rake face dimensions. Digitising software also verifies the insert orientation prior to grinding.
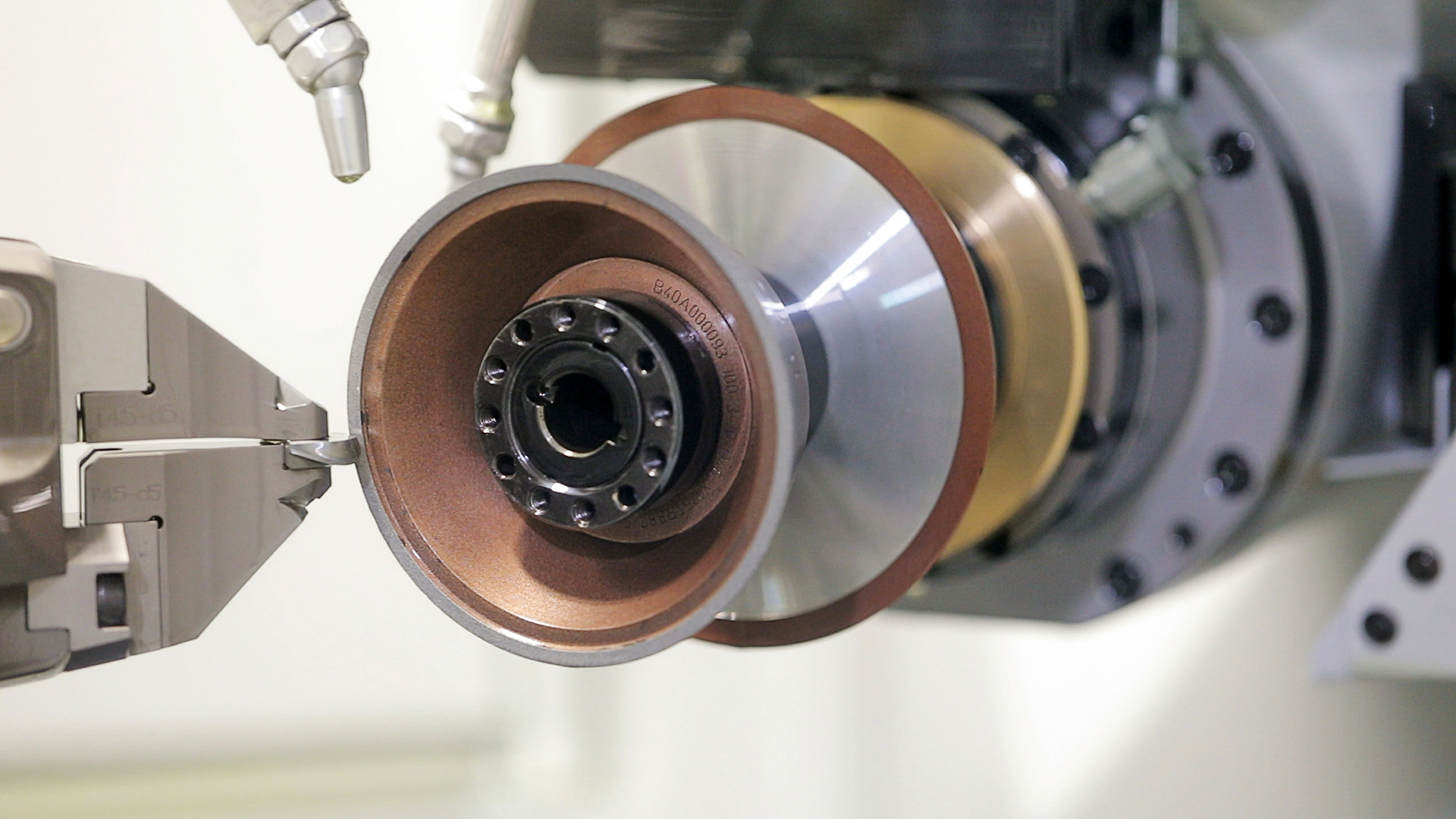
MX7 Linear in action.
The grinding and loading process is running within the customers parameters. Inserts can be ground in a cycle time of currently less than six minutes. Alfred concluded “ANCA impressed me from day one. Creating basically a whole new type of machine for AB Tools, Inc. is not merely impressive, it is extraordinary. We could have purchased another machine just like the one we were using but we asked ANCA for help because we wanted to expand our capabilities and simplify our process. This new machine has exceeded both desires.”
?wmode=transparent">