Kombination von Hartdrehen und Steinbearbeitung
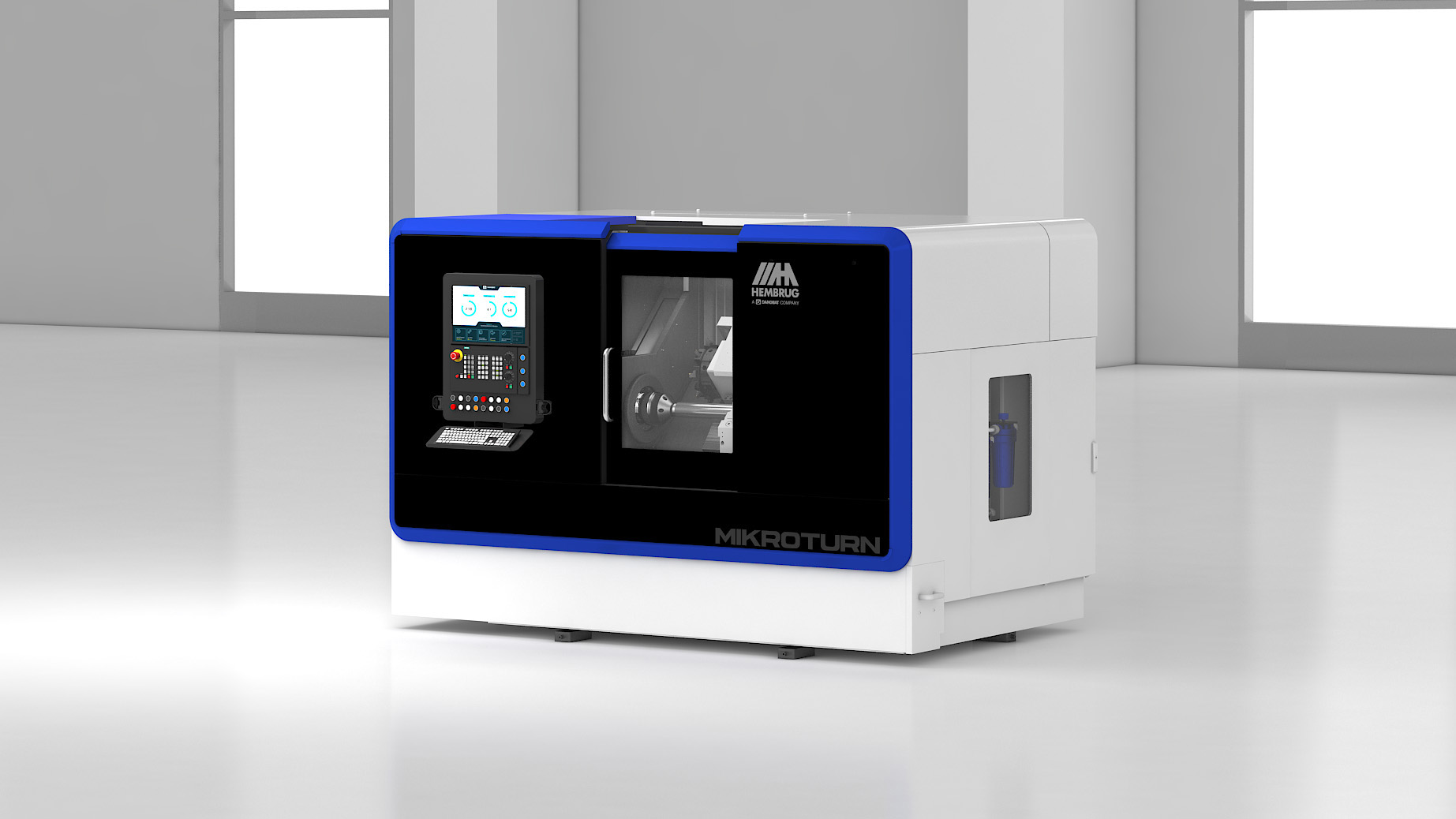
Durch die Kombination von Stein-Finish und Hartdrehen in einer Anlage setzt Hembrug Machine Tools auf Flexibilität und kurze Takt- und Umrüstzeiten. In einer Aufspannung können Anwender hervorragende Ergebnisse in Bezug auf Oberflächenstruktur und Rauheit erzielen.
Das Honen ist eine bekannte und weit verbreitete Bearbeitungstechnik, bei der die Innenseite einer Bohrung mit einem oder mehr Steinen bearbeitet wird. Die Verwendung von Stein für die hochpräzise Endbearbeitung eines Werkstücks ist jedoch nicht nur für Bohrungen geeignet. Die Steinbearbeitungstechnik eignet sich ebenso gut für die Bearbeitung von ebenen, zylindrischen oder konischen Flächen und sogar von kugelförmigen Strukturen.
„Diese Schlichttechnik wird noch interessanter, wenn man sie mit dem Hartdrehen in einer Maschine kombinieren kann“, sagt Bert de Veer, Leiter der Technik bei Hembrug Machine Tools. „Mit der neuen KombiFin-Technologie in unserer Mikroturn-Maschine haben wir das realisiert, und Sie können Ihre Werkstücke in einer Aufspannung drehen und bearbeiten. Während bisher die Prozesse oft auf zwei separaten Maschinen durchgeführt werden mussten, haben wir sie zusammengeführt, wodurch die Spannzeiten entfallen. Das ist einer der größten Vorteile der Integration: Man ist schneller, macht weniger Umrüstfehler und spart so Kosten“.
Irrtum
Mit dem KombiFin-Modul will Hembrug auch mit einem hartnäckigen Missverständnis aufräumen. Experten der Schleiftechnik zögern oft, Hartdrehverfahren einzusetzen. „Sie vertrauen nicht darauf, dass man damit die gleichen Ergebnisse erzielen kann“, hat De Veer festgestellt. Wir bei Hembrug sagen schon seit Jahren, dass man mit der Hochpräzisionsdrehtechnik oft sehr weit kommen kann, aber es gibt immer noch viele Unternehmen, die sich davor scheuen.
Für Anwender, die nicht nur drehen lassen wollen, bietet Hembrug jetzt die Option KombiFin an. Diese Kombi-Maschine gibt ihnen die Möglichkeit, die ohnehin schon hochwertigen Drehteile noch ein wenig präziser zu bearbeiten.
Sie müssen dann nicht eine oft teurere Schleifmaschine und eine separate Finishing-Maschine kaufen, um die gewünschte Oberflächenstruktur zu erreichen. Mit KombiFin erreichen wir eine Rauigkeit von Ra = 0,02 µm.
Dreistufenplan
Schauen wir uns den Prozess der Steinbearbeitung genauer an. Grob gesagt, besteht ein Hohnstein aus kleinen, zusammengepressten Körnern und einem Bindemittel. Die Wirkung dieser Körner auf das Werkstück hängt von der angewandten Kraft, der Drehgeschwindigkeit und der Schwingungsbewegung ab. Ohne den Stein zu wechseln, können Sie anhand dieser Parameter die effektive Rauheit des Steins bestimmen. Die Wahl der Parameter ist eine Frage der Erfahrung oder das Ergebnis eines kurzen Versuchs.
„Im ersten Arbeitsschritt wählt man eine niedrige Drehzahl, die die Körner im Stein zum Ausbrechen bringt. Dadurch entsteht eine grobe Struktur mit großen Schneidkanten, so dass eine relativ große Menge Material vom Werkstück abgetragen wird. In diesem Modus werden die größten Unebenheiten, wie z. B. die Drehspuren, entfernt“, erklärt De Veer.
Im zweiten Schritt wird die Drehgeschwindigkeit erhöht. Jetzt brechen die Steinkörner weniger aus und werden teilweise abgesplittert. Dies führt zu kleineren Schneidkanten und damit zu einer geringeren Zerspanungsleistung und weniger tiefen Spuren. Das Werkstück wird glatter.
Der dritte und letzte Schritt erfordert weniger Kraft. Wenn Sie die Geschwindigkeit hochhalten, aber die Kräfte zwischen dem Honstein und dem Werkstück verringern, nutzen sich die Körner ab. Diese abgeschliffenen Spitzen glätten die letzten Unebenheiten und hinterlassen die feinste Rauheit.
Beim nächsten Werkstück beginnt der Prozess wieder von vorne, also wieder Ausbrechen der Körner, Absplittern und Abstumpfen.
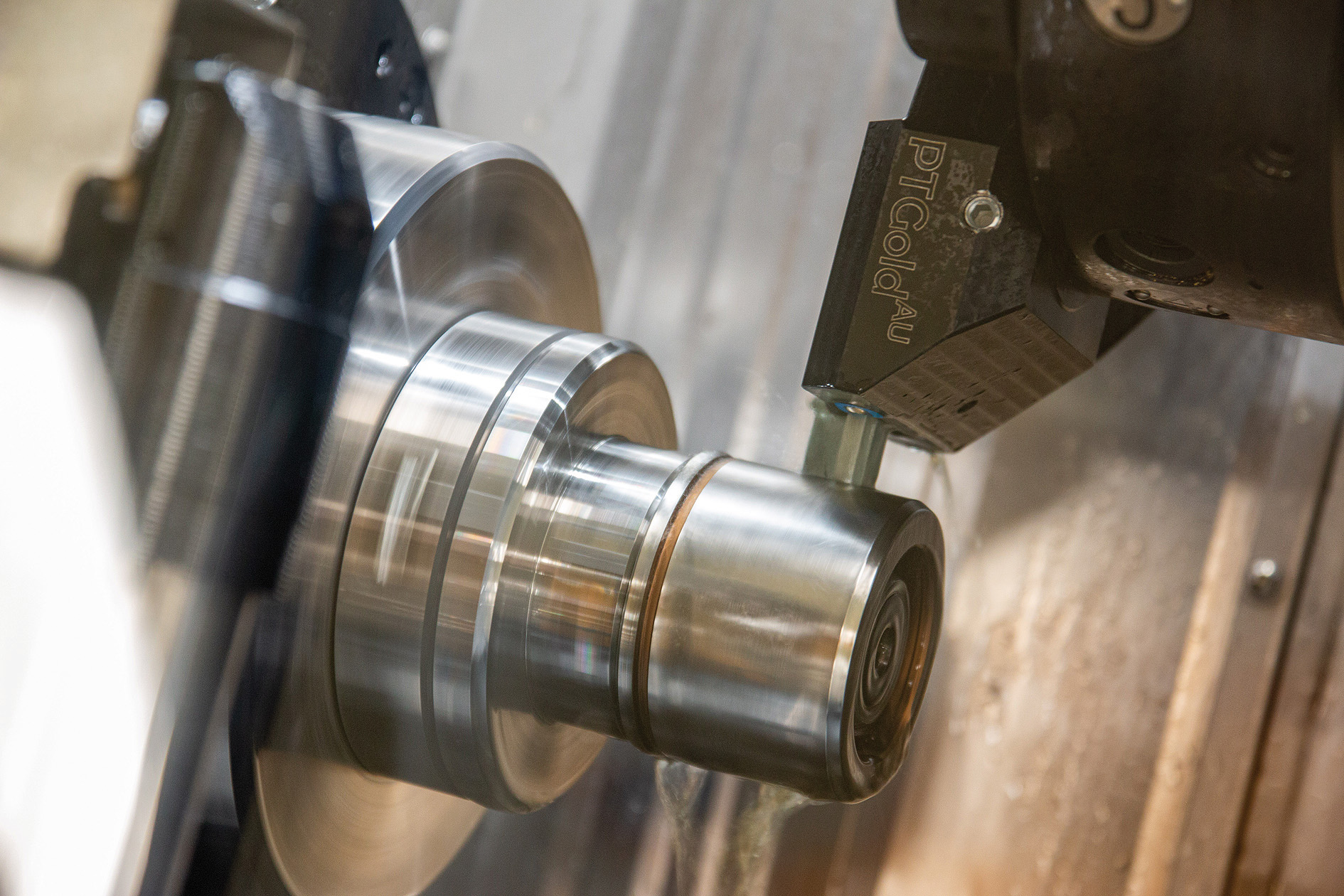
Kombination von Hartdrehen und Steinbearbeitung macht Hembrug-Maschine flexibler und schneller.
Tiefziehstempel
Kraftrückführung
Jeder dieser drei Prozessschritte hat seinen eigenen Kraft-Geschwindigkeitsverlauf. Um ein optimales Ergebnis zu erzielen, muss daher nicht nur die Drehgeschwindigkeit des Objekts gesteuert werden, was bei einer Standard-Drehmaschine natürlich bereits der Fall ist. Auch die Kraft zwischen dem Werkstück und dem Hohnstein muss genau gemessen und geregelt werden.
Um dies zu erreichen, arbeitet Hembrug eng mit Professor Harald Goldau von der Hochschule Magdeburg-Stendal zusammen. „Professor Goldau hat sein ganzes wissenschaftliches Leben der Verbesserung und Optimierung des Hohnprozesses gewidmet“, sagt De Veer. Vor etwa zehn Jahren machte er sich daran, in eine gebrauchte Drehmaschine von Hembrug ein Steinbearbeitungsmodul zu integrieren. Er hat den Prozess bis ins kleinste Detail durchdacht und optimiert.
Wesentlich in diesem Modul sind das Kraftmesssystem und die fortschrittliche Rückführung, die eine genaue Überwachung und Steuerung der Kräfte gewährleisten. „Hembrug hat die Entwicklung in Magdeburg aufgegriffen und industrialisiert, natürlich ohne die Steifigkeit unseres Drehsystems zu beeinträchtigen. Jetzt können wir die Kombinationstechnologie kommerziell anbieten“, sagt De Veer.
Immer der beste Parametersatz
Für jedes Werkstückmaterial gibt es ein optimales Drehwerkzeug mit spezifischen Schnittgeschwindigkeiten und Vorschubgeschwindigkeiten. Beim Stein-Finish ist es nicht anders. Hembrug bietet Schulungen an, um die Kunden in diesem Bereich zu schulen. Auch die Parameter für die gängigen Materialien sind bekannt.
Mit der mitgelieferten Hard- und Software ist es möglich, den Prozess einzusehen. Die verschiedenen Prozessschritte (Ausbrechen von Körnern, Absplittern oder Abstumpfen) können erkannt und somit gesteuert werden. So können die optimalen Parameter für neue Kombinationen von Werkstückstoff und Schneidstoff schnell gefunden werden.
Der Mikrocontroller, der den Prozess steuert, kann mit einer Cloud-Umgebung verbunden werden, was es den Spezialisten von Hembrug ermöglicht, den Prozess aus der Ferne zu verfolgen und den Kunden zu beraten.
„Die Stärke der KombiFin-Technologie besteht darin, dass die Maschine kontinuierlich die Bearbeitungskräfte misst“, sagt De Veer. So kann man sehr genau die richtigen Schnittparameter ansteuern. Ein weiterer Vorteil des Kraftsensors ist, dass wir ihn auch im Drehprozess einsetzen können. So kann man zum Beispiel direkt erkennen, dass das Drehwerkzeug verschleißt und Maßnahmen ergreifen.
Bierdosen
Hembrug hat eine KombiFin-Erweiterung an ein amerikanisches Unternehmen verkauft, das Werkzeuge für das Tiefziehen von Softdrink- und Bierdosen herstellt. De Veer erklärt, warum sich der Kunde für die KombiFin-Technologie entschieden hat: „Es werden sehr hohe Anforderungen an die Qualität dieser Formen gestellt. Was die Größe anbelangt, so beträgt der Spielraum 2 µm und sie müssen extrem glatt sein, mit einem Rz von 0,3 µm“. Das ist auf einer Schleifmaschine nur sehr schwer zu erreichen, und durch reines Drehen ist es schon gar nicht möglich. Mit der Kombination aus Drehen und Stein-Finish erreicht dieser Kunde das gewünschte Ergebnis.
„Wie bereits erwähnt, ist die Reduzierung der Umrüstzeiten und der Spannzeiten ein wichtiger Vorteil des Kombi-Fin-Konzepts. Das Umrüsten einer Drehmaschine ist bei einer Kleinserie üblicherweise innerhalb einer Stunde möglich. Bei höheren Stückzahlen ist die Kombination von Drehen und Schleifen in einer Maschine weniger verbreitet. Man darf hier nicht nur schwarz-weiß sehen“, sagt De Veer: Ein Kunde, ein deutscher Automobilzulieferer, führt derzeit ein Projekt durch, bei dem er die KombiFin-Technologie zur Herstellung von Elektromotorwellen für die neuesten Elektroautos einsetzt. Um die höchste Qualität zu erreichen, wird Drall (die rotierende Spirale noch dem Drehen) aus dem Sitz eines Dichtungsrings entfernt. Obwohl es sich in diesem Fall um eine Massenproduktion handelt, ist es dennoch interessant, die beiden Verfahren miteinander zu verbinden. Denn diese Wellen werden blitzschnell bearbeitet. Das Drehen dauert etwa eine Minute, das Finishen zehn bis fünfzehn Sekunden. Es ist sehr praktisch, wenn man das in der gleichen Anlage machen kann. Jetzt muss man nur noch einmal laden und entladen.
„Diese Zeitersparnis kann auch ein entscheidender Faktor für die Massenproduktion sein. Es hängt wirklich vom Werkstück und den Qualitätsanforderungen ab, welche Produktionstechnologie oder Kombination am besten geeignet ist“, sagt De Veer.
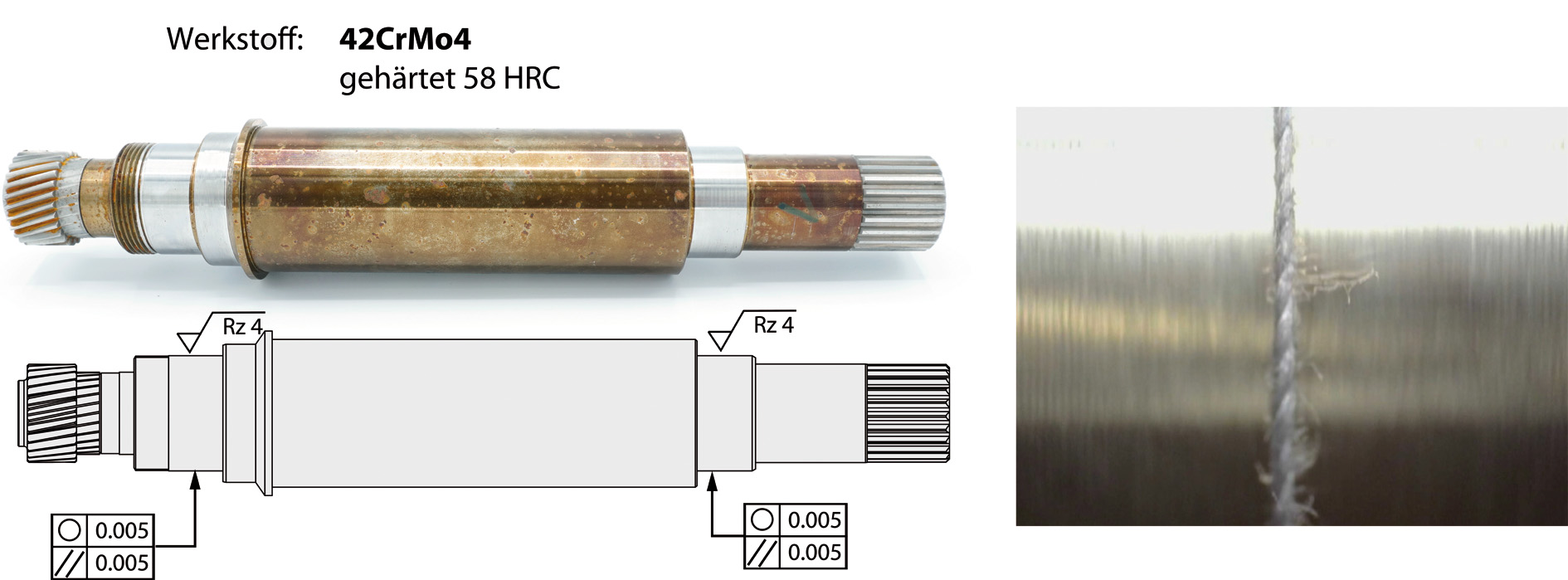
Welle eines Elektromotors eines lektroautos, das Foto unten rechts zeigt die Messung, die das Fehlen eines Dralls beweist; dieser 40-µm-Draht bleibt an seinem Platz, wenn es keine rotierende Spirale gibt.
Balligkeit
Ein drittes Beispiel für die Anwendung der Steinbearbeitung ist die Herstellung von Lagerringen. „Die Rauheitsanforderung liegt hier oft bei einem Rz von etwa 1 µm“, sagt De Veer. Das kann man sehr gut auf einer Drehmaschine erreichen, aber viele Lagerhersteller schreiben vor, dass eine hartgedrehte Lageroberfläche auch nachbearbeitet werden muss. Mit der KombiFin-Technologie können wir das anbieten.
Die Oberfläche eines Lagerrings ist oft nicht ganz gerade. Sie hat eine kleine Wölbung, die sogenannte Balligkeit, die die Kräfte auf die Rollen besser verteilt. De Veer: „Diese Form kann man auf einer Drehmaschine perfekt erreichen. Und durch die Wahl des richtigen Steins und der richtigen Bearbeitungseinstellungen bleibt sie bei der Endbearbeitung erhalten“.
Hohe Erwartungen
Hembrug hat hohe Erwartungen an sein KombiFin-System. „Viele Teile, die von unseren Drehmaschinen kommen, werden anschließend in einer Endbearbeitungsstation weiterverarbeitet. Wir haben diese Prozesse zusammengeführt, was für viele Anwendungen sehr interessant ist“, sagt De Veer.
Das Wesentliche an der Maschine ist die Kraftrückführung, die es uns ermöglicht, alle Bearbeitungsschritte der Steinbearbeitung präzise zu steuern, den Verschleiß des Hohnwerkzeugs genau zu überwachen und den Drehprozess noch besser zu steuern. „Mit diesem Regelkreis hat man seinen Prozess perfekt unter Kontrolle“, so De Veer abschließend.
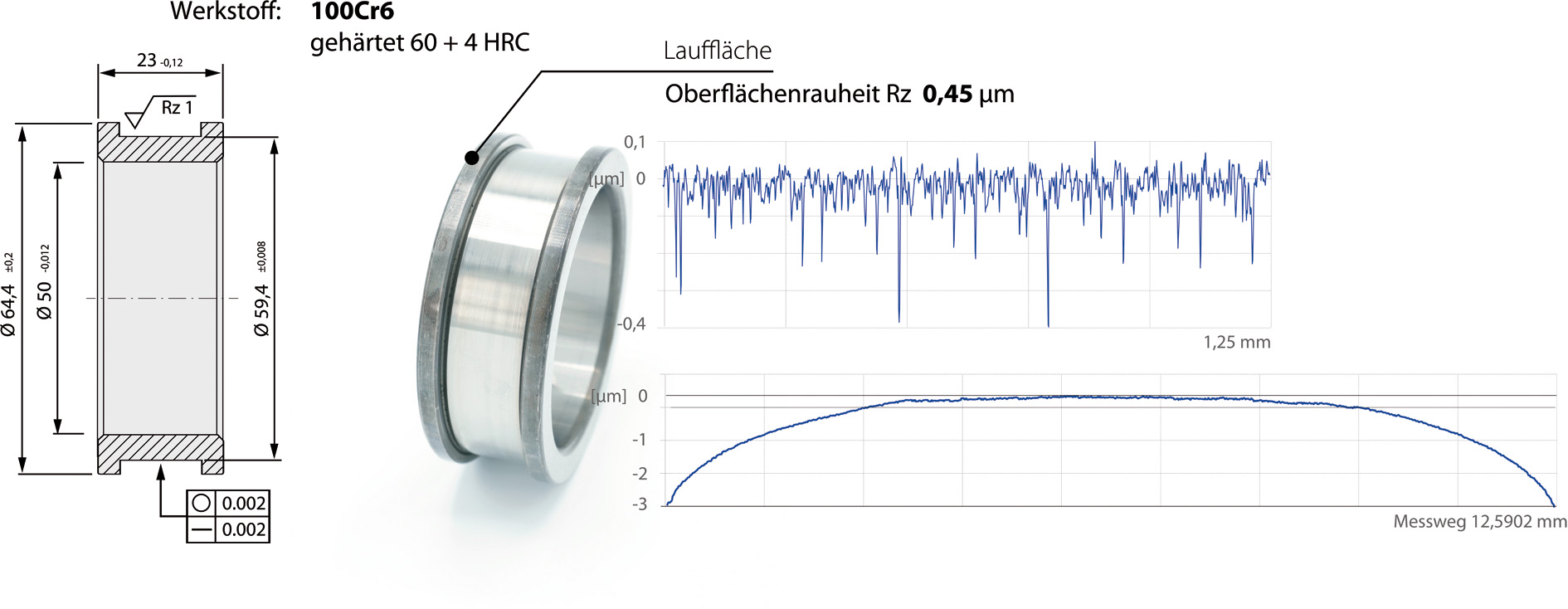
Balliger Lagerring
