Parted off, but looks like it was faced on a lathe
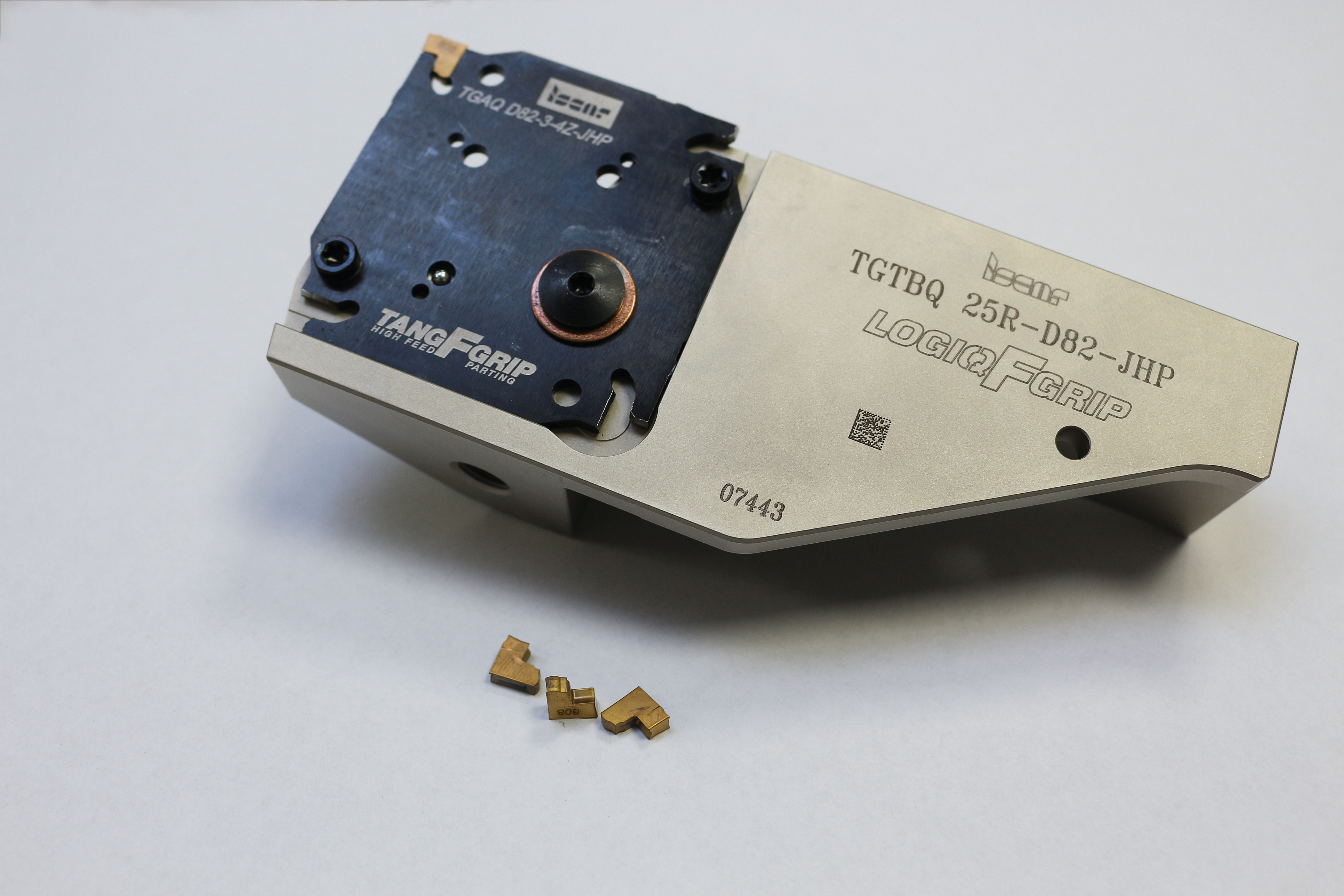
Analyses during the Covid-19 pandemic pointed out a way in which the company Haberland Zerspanungstechnik could optimize the parting of spacers made of unalloyed steel. The solution: tools from ISCAR’s MULTIFGRIP series. Haberland now benefits from excellent surface quality, long tool lives and lower tooling costs.
Since its establishment 30 years ago, Haberland Zerspanungstechnik, based in Melle, Lower Saxony, has gained an outstanding reputation as a subcontractor and full-service manufacturer. The team of 135 employees led by business manager Dirk Haberland operates 70 state-of-the-art CNC machines on an area of 8,000 square meters. The company mainly produces heating and cooling rollers, plus highly precise turned and milled parts. Its customers include some 250 machine and plant manufacturers from Germany and other EU countries, most with global operations. Haberland largely processes stainless steel and non-corroding materials, but it also offers products made of cast steel and aluminum. “Our strong suit is manufacturing special parts in small to medium-sized batches,” says the company’s business manager. “The key demand here is for precision, and we must also be flexible in order to offer a large variety of components.”
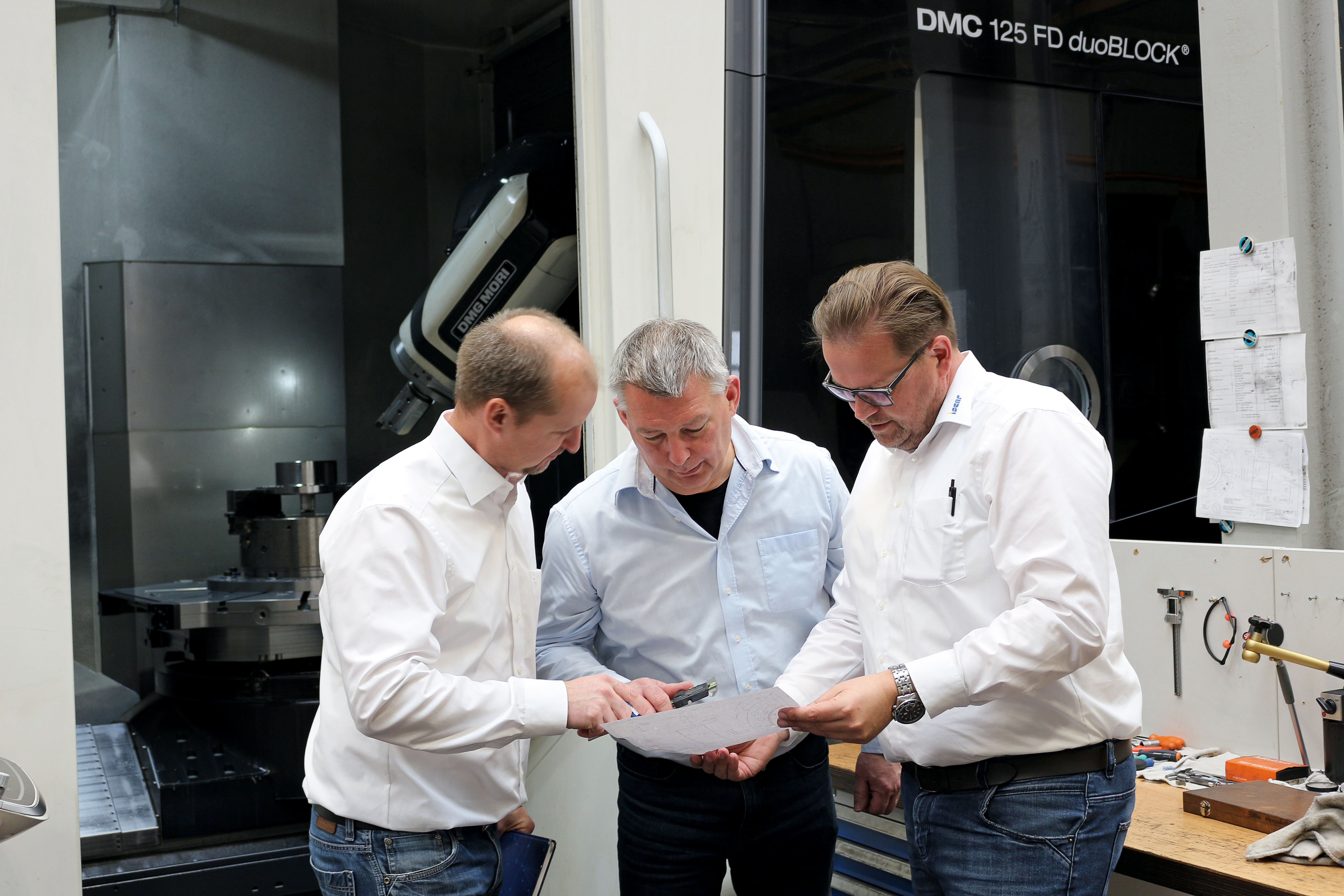
Daniel Höinghaus from support and sales at ISCAR (left), Andreas Föst, technical production director at Haberland, and Christian Buck, responsible for technical support and sales at ISCAR (right) discuss operation of the MULTIFGRIP.
To ensure flexibility and be ready for unforeseen requirements, Haberland Zerspanungstechnik and ISCAR have maintained a close partnership for 15 years. The ISCAR team includes Martin Berlin, regional sales manager north, Christian Buck, technical support and sales, and Daniel Höinghaus, support and sales. All are highly familiar with the machines and processes at Haberland and are able to provide it with the best possible tools, support and expertise. Additional support recently came from an unexpected source: the Covid-19 pandemic.
Analysis during the pandemic revealed potential for improvement
“As strange as it may sound, the lockdown during the pandemic had a good side to it,” says Christian Buck. “It gave us time to analyze the processes and tools of our customers and find ways to make improvements. At Haberland we discovered that its parting processes could be significantly improved.” One of Haberland’s specialties is the parting of spacers from unalloyed bar stock. Until that time, the company had used a tool from an ISCAR competitor that had only one tool pocket. “Our analysis quickly showed that Haberland would fare much better with our parting tool,” explains Daniel Höinghaus. The tool consists of a MULTIFGRIP tool holder and a TANGFGRIP blade with four tool pockets. It is equipped with single-ended TANG-GRIP inserts.
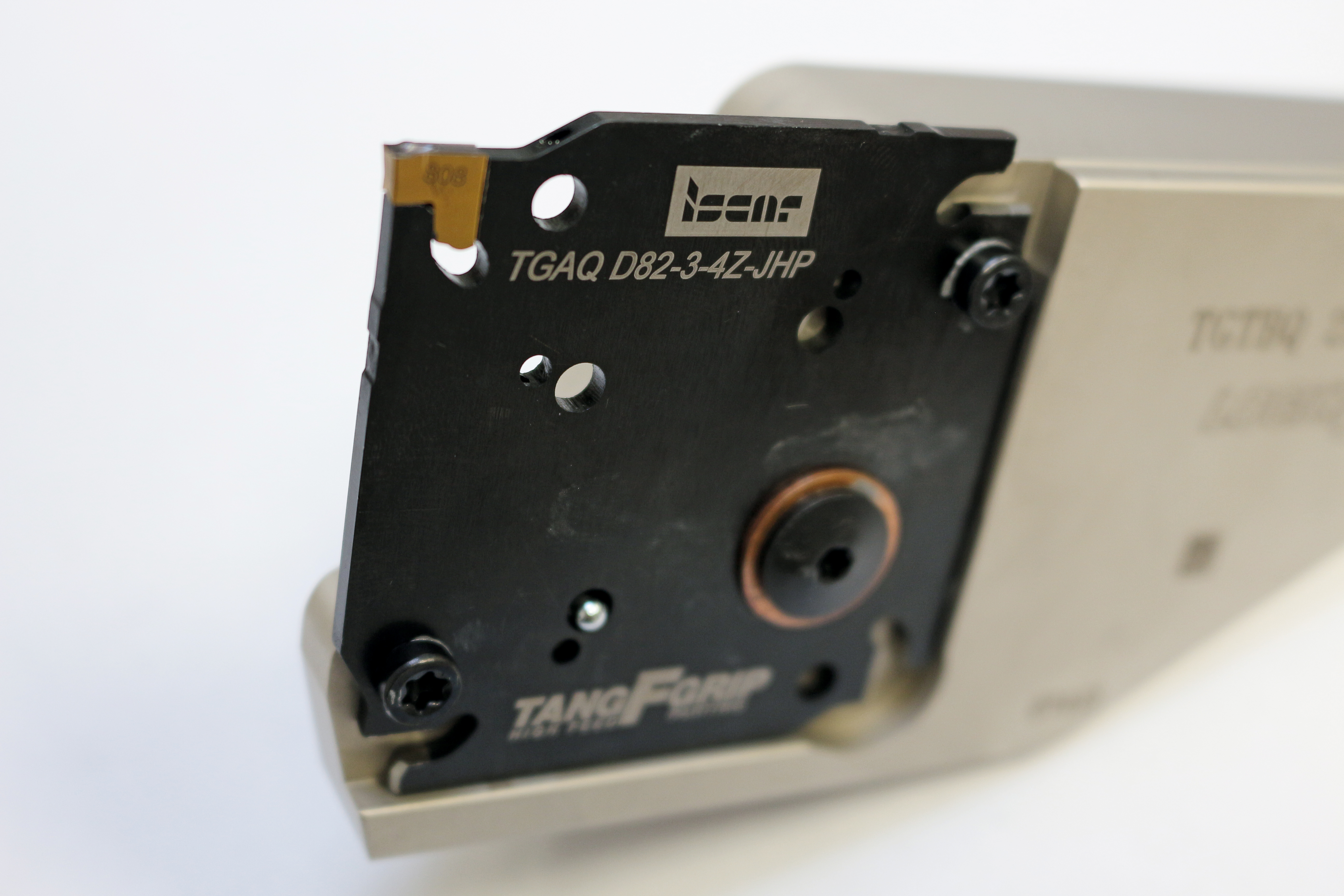
The fast-feed geometry of the TANG-GRIP inserts, with cutting widths of three and four millimeters, enables Haberland to achieve feed rates of 0.35 to 0.4 millimeters per rotation – 20 to 25 percent more than in the past.
The MULTIFGRIP tool holder is a sturdy parting system for the TANG-GRIP and DO-GRIP series. “Thanks to its robust design, the MULTIFGRIP can part rods up to 120 millimeters in diameter on the X axis, with no vibrations and high feed rates,” says Martin Berlin. “The inserts have a longer tool life, the component surfaces are of better quality and the faces are very flat.” The MULTIFGRIP is designed for JET-CUT cooling at up to 140 bar. It aims a precisely controlled coolant stream at the cutting edge of the insert. Different adapters can be attached to a single base support, allowing the use of single-ended TANG-GRIP or double-ended DO-GRIP cutting systems with two or four tool pockets. “When the pandemic subsided, it finally became possible for us to visit Melle in order to present our suggestion,” says Höinghaus. The idea met with considerable interest on the part of Dirk Haberland and technical production director Andreas Föst. Tests on Haberland’s machines confirmed ISCAR’s prediction.
MULTIFGRIP produces surfaces of excellent quality
“The new system makes parting more economical, and it also improves performance,” says Buck. The rugged design of the MULTIFGRIP is a particular advantage in machining. It makes processes much more reliable and permits longer tool lives. Moreover, the fast-feed geometry of the TANG-GRIP inserts, with cutting widths of three and four millimeters, enables Haberland to achieve feed rates of 0.35 to 0.4 millimeters per rotation – 20 to 25 percent more than in the past. “And even when a clamped workpiece protrudes a long way, there is almost no vibration. We get perfectly smooth surfaces, as if the component had been faced on a lathe instead of parted,” says Andreas Föst. “Remachining is not even necessary. That means we save a process step, gain valuable production time and free our machinery for other work.” The chip former and the coolant jet also contribute to this outstanding result. The chip former splits the chips and the jet sprays coolant onto the cutting edge for effective chip evacuation. This prevents scratching of the machined surface.
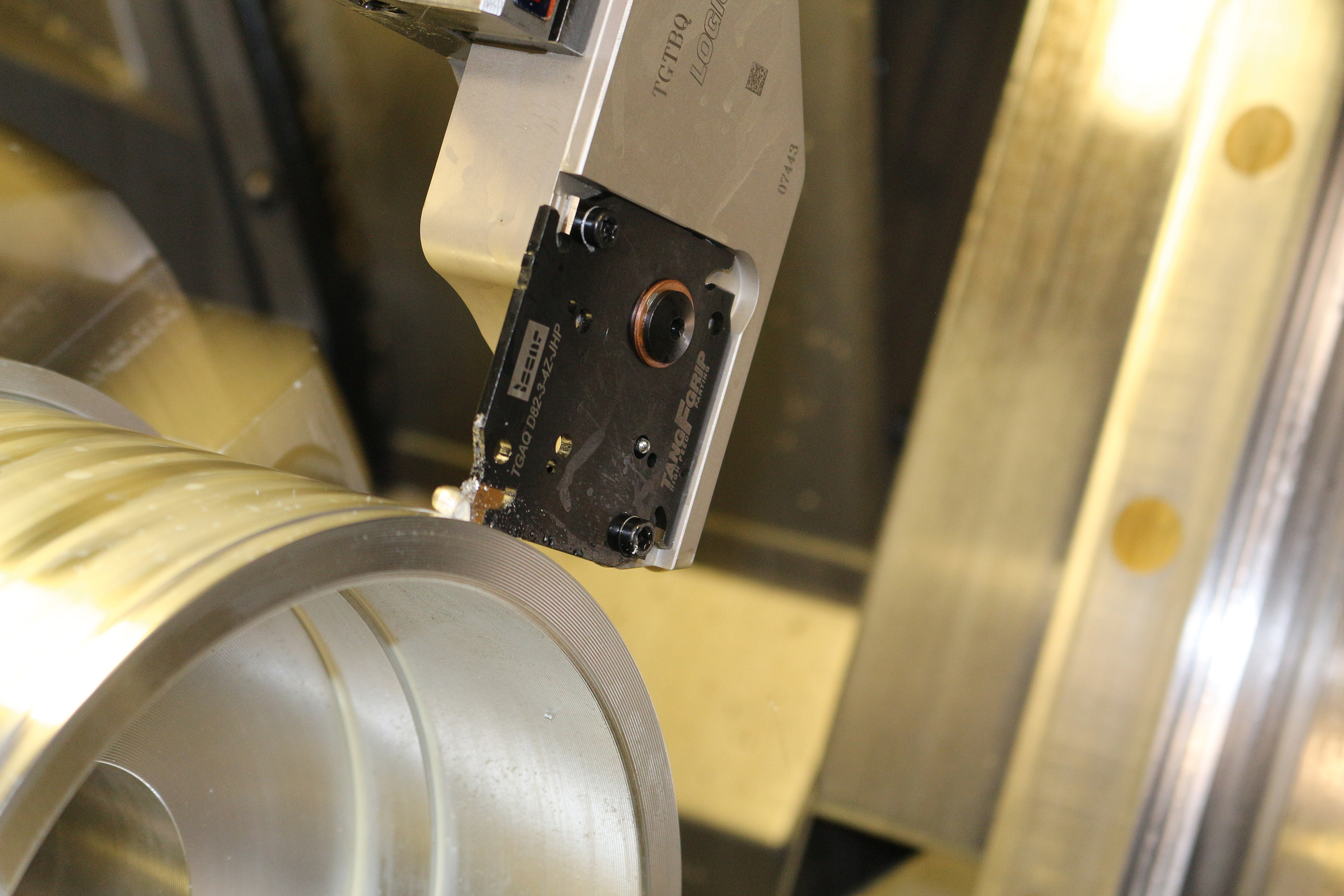
Haberland Zerspanungstechnik uses the MULTIFGRIP to part off spacers from unalloyed bar stock.
However, Haberland has not yet pushed the new solution as far as it can go. “At the start, we operated the tool with our previous cutting values and were amazed at the good results,” says the production director. “In the meantime we’ve stepped up the output, but we haven’t yet brought the tool to its limits. We know we still have room for greater performance, and that gives us confidence.”
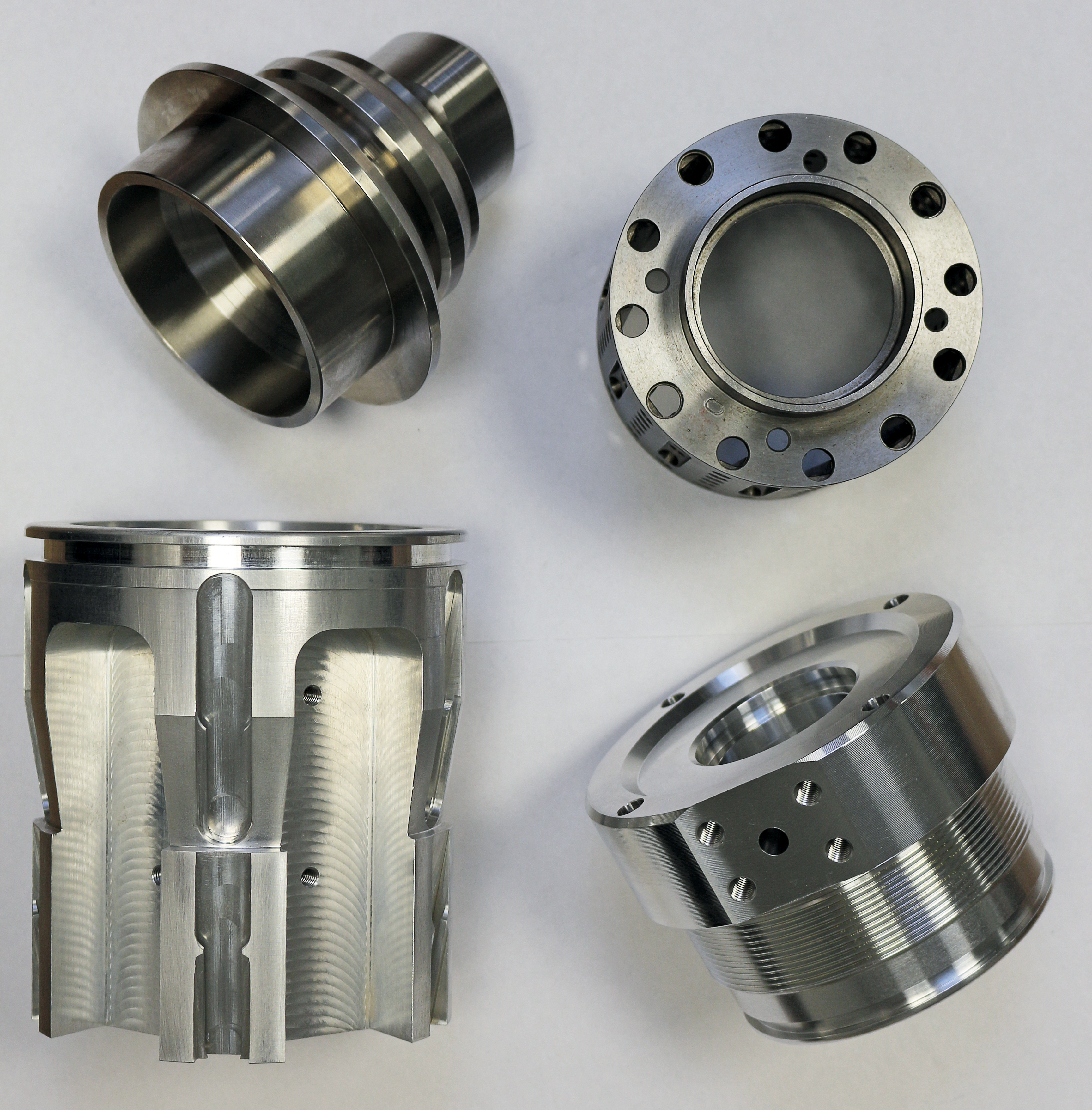
Haberland Zerspanungstechnik mainly produces heating and cooling rollers, plus highly precise turned and milled parts. It processes stainless steel and non-corroding materials, but it also offers products made of cast steel and aluminum.
An impressive tool and excellent cooperation
Haberland has now been using the new solution for over a year and a half. “We’re more than satisfied with the tool and its performance. For that reason, we’ve now equipped over 75 percent of our machines with the MULTIFGRIP system,” says Föst. “This has only been possible because the tool is perfectly reliable and very user-friendly as well.” One advantage is that the tool can stay in the machine when a cutter is replaced. “We don’t have to remeasure anything, and the set-up time is negligible,” says Höinghaus. However, another important factor for Haberland is its cooperative relationship with ISCAR. “Other manufacturers also offer good tools. But what’s even more important is our close cooperation,” says Dirk Haberland. “With this partner we can always rely on solid support, efficient solutions and a high degree of flexibility. We haven’t had a comparable relationship with any other supplier.”
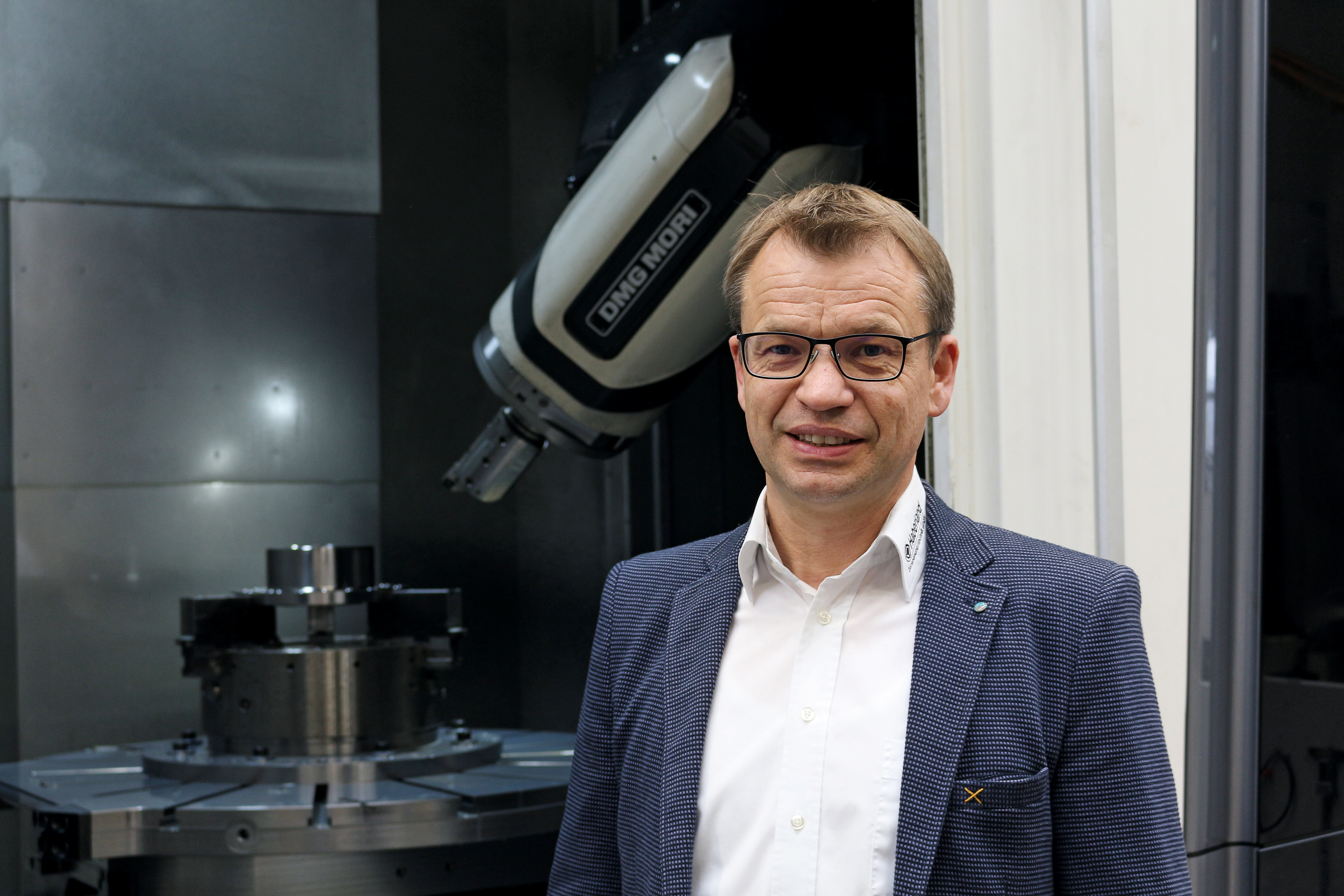
“Other manufacturers also offer good tools. But what’s even more important is our close cooperation,” says Dirk Haberland. “With this partner we can always rely on solid support, efficient solutions and a high degree of flexibility. We haven’t had a comparable relationship with any other supplier.”
