The new gold standard for turning
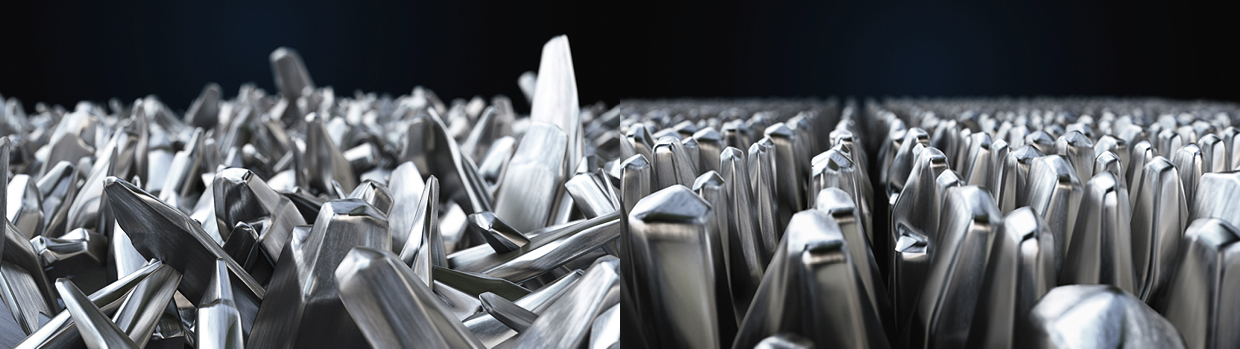
50% longer tool life with Walter Tiger·tec® Gold.
The machining experts from Tübingen are launching Tiger·tec® Gold indexable inserts for turning. Compared to Walter Tiger·tec® Silver, the previous top-level indexable inserts for this application, the new grade offers up to 50% longer tool life when turning steel components and for the machining of ferritic/martensitic stainless steels, grey cast iron and ductile cast iron.
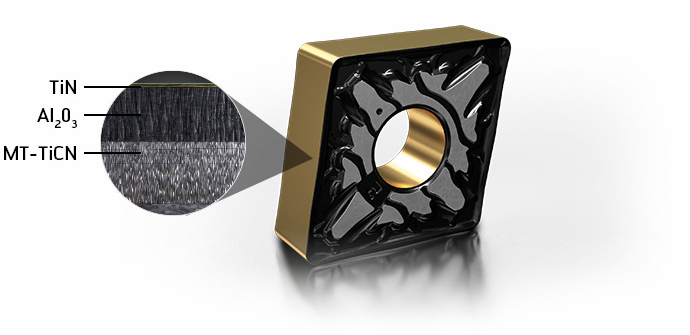
On top of the gradient carbide substrate, there is layer of highly structured, multi-layer MT-TiCN, a layer of highly structured Al2O3 and a gold-coloured top coat. Image: Walter AG
Innovations for increased productivity
Turning makes up approximately 25% of metal machining operations. Increases in the tool edge life and process reliability offer significant savings per component, especially in mass and series production with its high cost pressure, for example in the automotive industry. If different materials need to be machined, as is the case in general mechanical engineering, a turning tool that can be used universally reduces set-up times, tool costs and the risk of errors. Combining both sets of requirements has previously seemed virtually impossible. Physical limitations mean that perfection is unachievable, and yet machining experts like the team led by Jörg Drobniewski, Head of Cutting Material Development, and Gerd Kussmaul, Senior Product Manager for Turning at Walter, are continually striving to get closer to this goal. Aside from rising to the engineering challenge, the potential benefits for customers take top priority for such projects. Jörg Drobniewski explains the process: “At Walter, products that have been on the market for no more than five years make up a share of around 30% of sales. When it comes to cutting tool materials, we strive to launch a new generation that will enable significant productivity gains every six to seven years. We aim for an increase of 30 to 40%. With the new Tiger·tec® Gold cutting tool material generation for turning applications, we have now achieved 50% longer tool life. And not just in our own tests. More than 130 customers are already using the new indexable inserts in real-life production conditions and confirm that they are achieving a significantly higher efficiency.”
Walter did not simply change individual parameters of the previous Tiger·tec® Silver cutting material grade or adapt the already existing Tiger·tec® Gold cutting tool materials to develop the new turning cutting tool material generation. Instead, the Tiger·tec® Gold family for turning is a completely new development. The only thing it has in common with the milling tool is its name and the underlying concept: Tiger·tec® Gold is the name given to the most powerful cutting material grades in the Walter range. The most important parameter for the significant tool life improvement offered by the new turning insert grades is the newly designed coating.
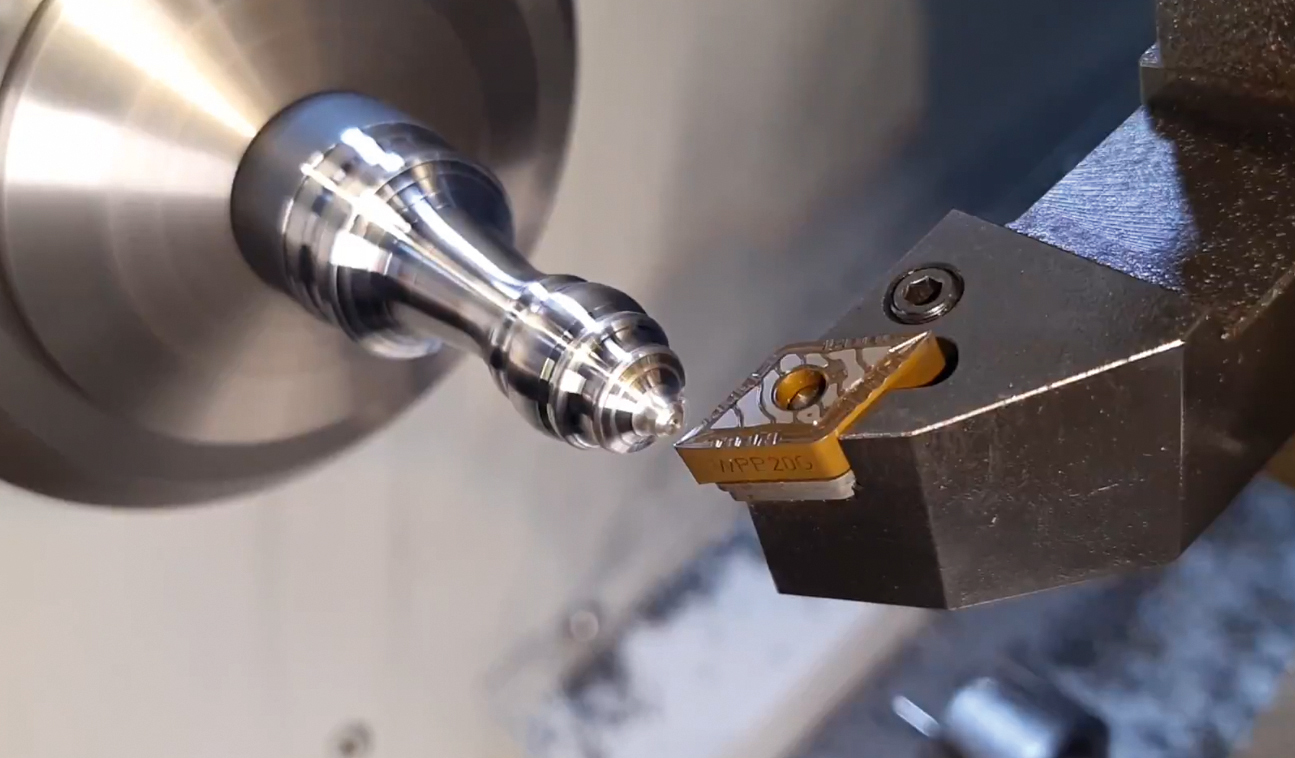
Tiger·tec® Gold indexable inserts can be used for mass production, but also for general mechanical engineering as shown in this example. Image: Walter AG
Outstanding wear resistance and toughness thanks to innovative new coating structure
At first glance, it looks like a classic CVD coating consisting of titanium carbonitride (TiCN) and aluminium oxide (Al2O3). CVD stands for chemical vapour deposition. The crucial difference to the classic coating also used by other suppliers is the special structure and alignment of the TiCN layer. For a CVD coating, it is normally only the aluminium oxide layer that is highly textured. For the Walter Tiger·tec® Gold turning coatings, this is also true for the titanium carbonitride layer. This means the both the crystallites of the aluminium oxide and the titanium carbonitride layer are aligned crystallographically. This very pronounced, pillar-like structure significantly increases the homogeneity and therefore the stability of the entire coating. In practice, this results in a significant reduction in flank face wear and wear caused by craters forming. In order to make the new Tiger·tec® Gold turning indexable inserts even more crack-resistant and tough, Walter has also designed the TiCN structure with several layers. Under a scanning electron microscope, it becomes evident that the last third of the layer features three small transitions between layers. These make the entire layer more elastic and improve the residual stress characteristics. The result is a damping effect when the cutting edge meets the material. This has proven particularly beneficial in cases where the tool needs to enter the component repeatedly, for example for face machining gearwheels or for machining forged wheel hubs. Walter has filed a patent for the completely new, innovative TiCN layer structure.
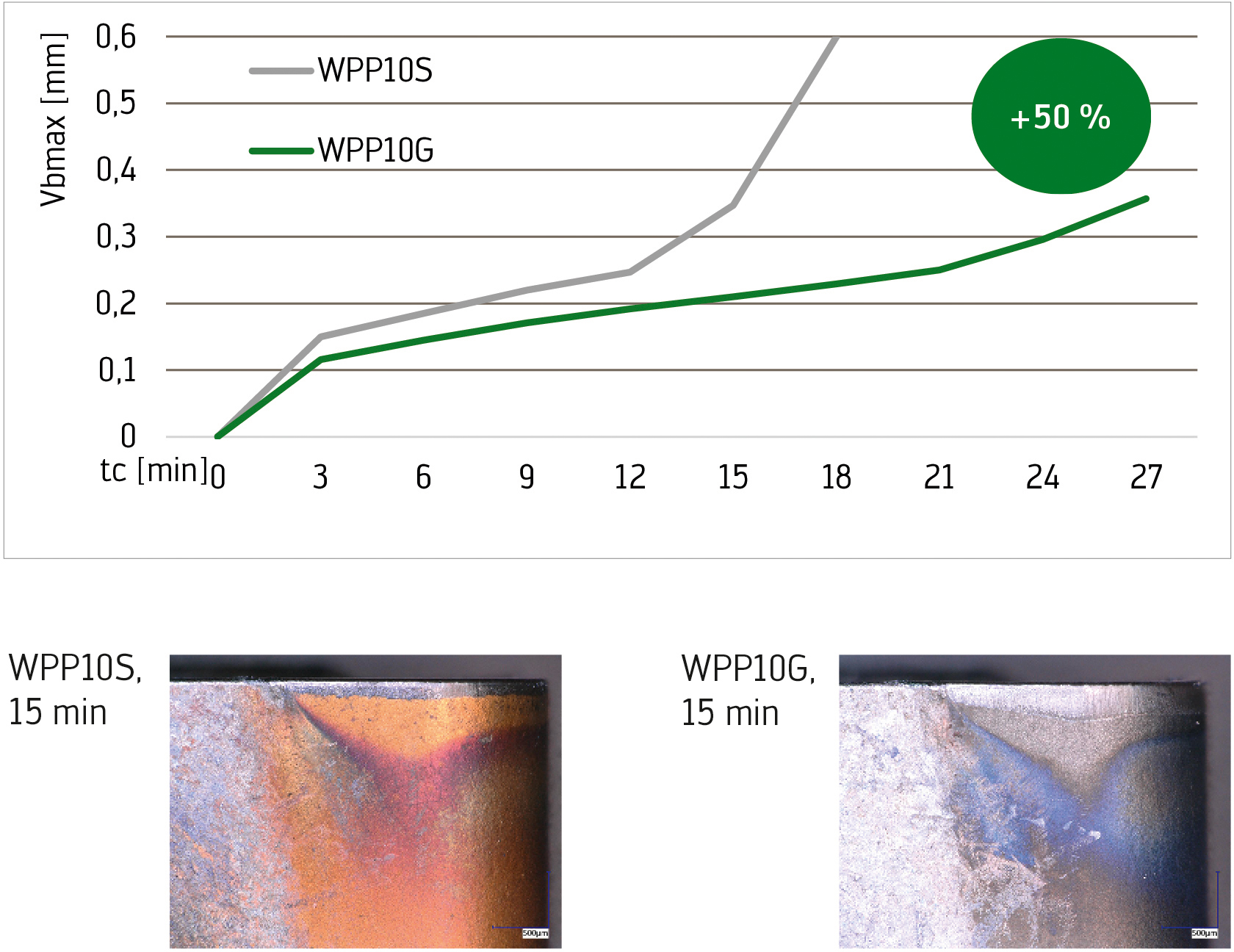
The new Tiger·tec® Gold CNMG120412-RP5 WPP10G indexable inserts demonstrates a 50% longer tool life in 56NiCroMoV7 [1.2714] with a tensile strength of Rm 1020 N/mm2. Cutting data: Vc : 250 m/min, f: 0.3 mm, ap: 2.5 mm. Image: Walter AG
The new three-stage post-treatment process for the coated indexable inserts is what lets customers utilise the full potential of the new CVD coating. There are three different stages for the new Tiger·tec® Gold inserts: First, the insert contact surfaces are ground. This improves the positive-locking seat, making it more secure and reducing the vibrations that develop during turning or are transferred to the insert. In the second treatment step, the insert is blasted at high pressure. This ensures that the coating and the edge zones of the carbide substrate build up a residual stress, which further improves the crack resistance and toughness. The last step is the abrasive wet-blasting of the rake face and cutting edge. This further improves the residual stress characteristics and removes the TiN, which negatively impacts the friction characteristics mainly for cast iron machining. As a result, the flank face of the indexable inserts retains its golden colour. That not only looks good. The gold colour of the unworn surfaces also provides an easily visible contrast to the dark, already worn cutting edges, especially in machine areas with poor visibility. The risk of reusing an already used cutting edge or not utilising all cutting edges is significantly reduced as a result.
Walter launched three Tiger·tec® Gold indexable insert grades in November 2021: The WPP10G, WPP20G and WPP30G mainly cover typical steel turning applications in automotive series production, such as machining drive shafts, wheels or flanges. The inserts can be used in both wet and dry machining. The WPP30G grade is particularly suitable for interrupted cuts. In addition, the grades can also be used for machining ductile graphite iron (GGG), grey cast iron (GG) and for roughing ferritic/martensitic stainless steel. There will be 21 different geometries available, including special geometries for optimal chip breaking in long-chipping, low-carbon steel (MP3) or geometries developed specially for interrupted cuts (RP7).
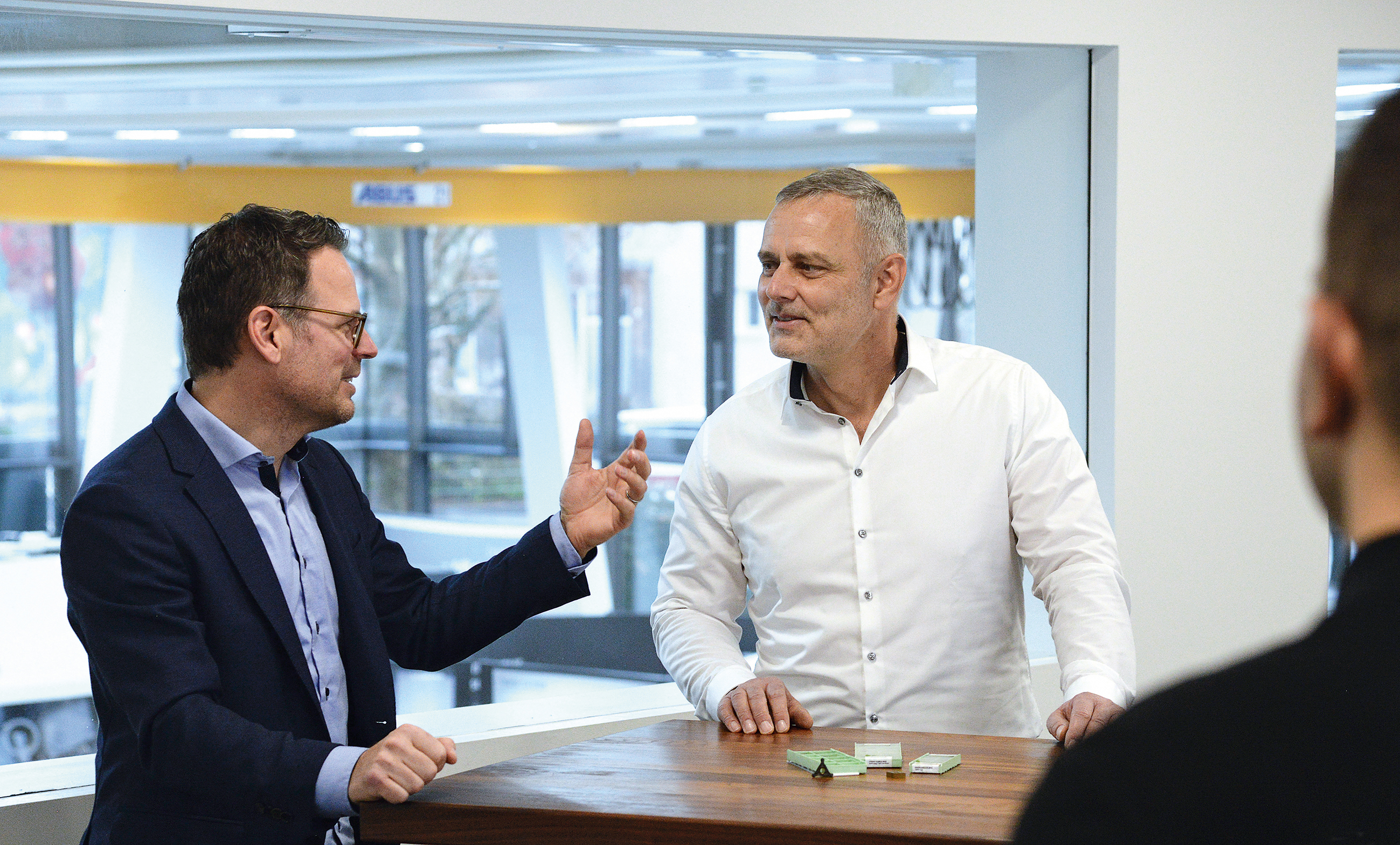
Gerd Kussmaul, Senior Product Manager for Turning, and Jörg Drobniewski, Head of Cutting Material Development at Walter (from left to right). Image: Walter AG
