Mitwachsende Werkstück-Spanntechnik stützt dauerhaften Erfolg
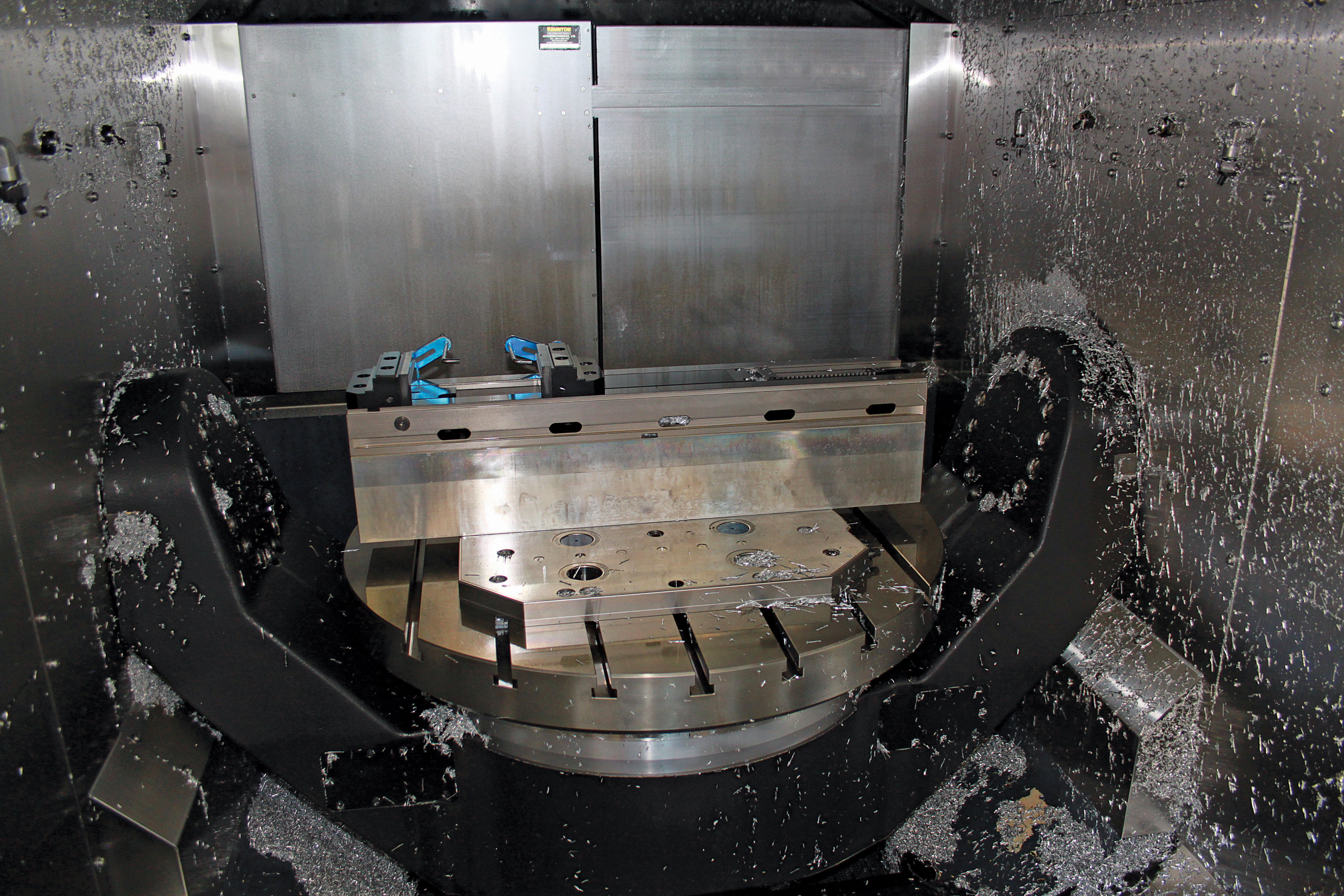
Vom einfachen Maschinenschraubstock über Mehrfachspannsysteme zum robotergestützten Spannen und Handhaben von Werkstücken – wie der Präzisionsteile-Fertiger Kratschmayer GmbH mit Spann- und Automatisierungs-Lösungen von Gressel AG in der täglichen Praxis die steigenden Anforderungen an Produktivität, Qualität und Wirtschaftlichkeit bewältigt.
Bereits im Jahr 1992 entstand bei Günter Kratschmayer und einem Kollegen die Idee, sich neben der Arbeit in einem Unternehmen für Gartengeräte und Gartenbewässerung zunächst im Zusatzerwerb mit der Auftragsfertigung von Drehteilen zu befassen. Das Geschäft ließ sich gut an, und weil die Kunden die Leistungsbereitschaft und die Qualität der gelieferten Teile mehr und mehr zu schätzen wussten, stiegen die beiden Praktiker schon 1993 in die Fräsbearbeitung ein. Dass sich daraus einmal ein überregional tätiger Zuliefer-Spezialist für spanend bearbeitete Präzisionsteile entwickeln würde, war damals wohl kaum abzusehen. Heute sind im mittelständischen Unternehmen Kratschmayer GmbH, DE-89182 Bernstadt, gut 13 Mitarbeiter damit beschäftigt, dem breiten Kundenstamm aus den Industriebereichen Lebensmittel-, Verpackungs-, Feuerwehr-, Halbleiter- und Automatisierungs-Technik sowie dem allgemeinen Maschinenbau termingerecht und in allen Stückzahlen unterschiedlichste Präzisionsteile zu liefern. Gestartet mit zwei konventionellen Drehmaschinen, stehen den Fachkräften dafür zurzeit u.a. 12 CNC-Fräsmaschinen bzw. CNC-Bearbeitungszentren und 7 CNC-Drehmaschinen zur Verfügung. Für die Programmierung der CNC-Programme wird das Alpha CAM/CAD-System angewendet und zur Qualitätssicherung sind 2 CNC-Koordinaten-Messmaschinen im Einsatz. Verbunden mit einem Qualitätsmanagementsystem, welches im Jahr 2010 nach DIN EN ISO 9001:2008 zertifiziert wurde, ist man jederzeit in der Lage, den wachsenden Anforderungen der anspruchsvollen Kundschaft umfassend gerecht zu werden.
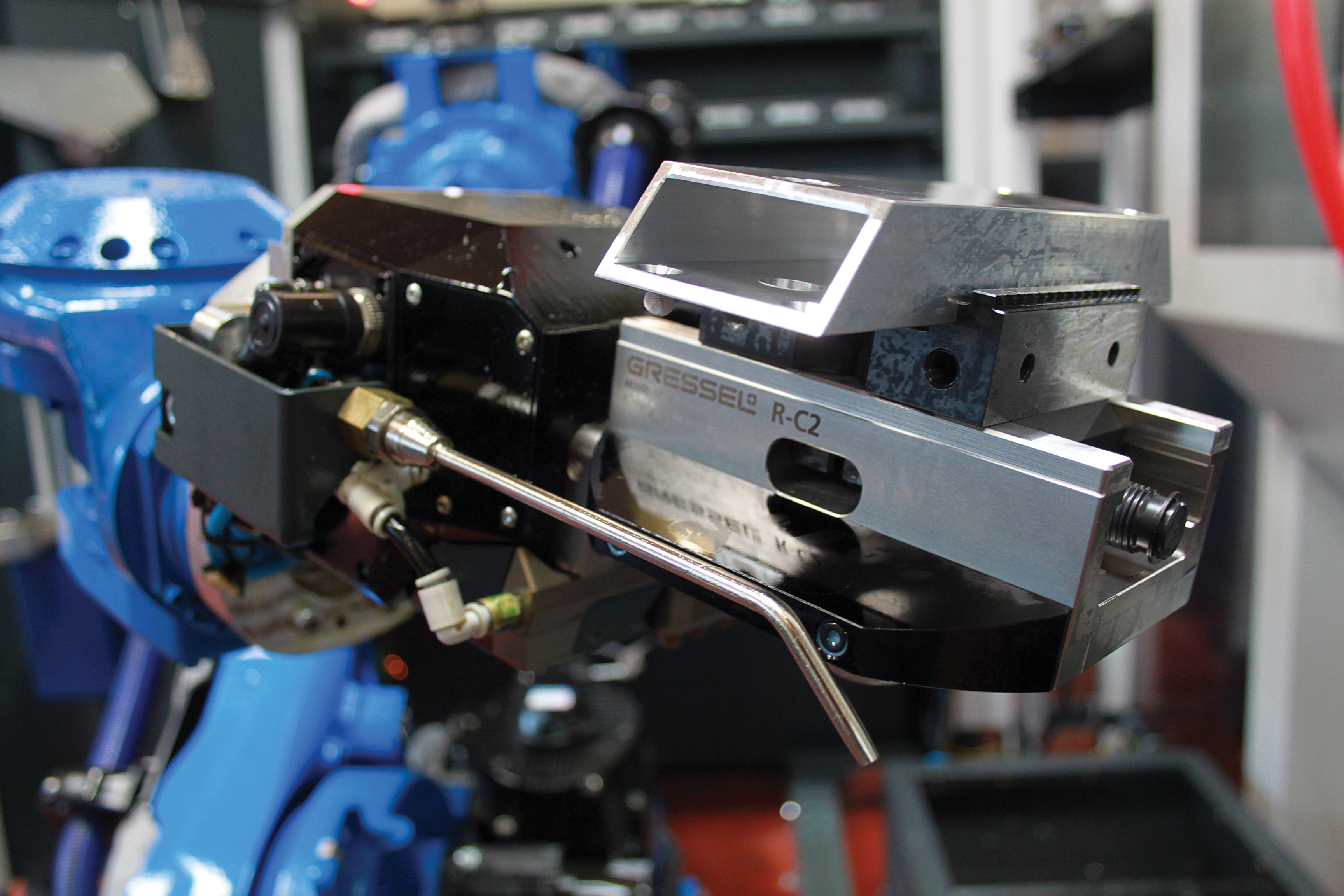
Der Roboterkopf, an den der „greifende Zentrischspanner“ R-C2 angedockt ist, der wiederum mit einem Zentrischspanner R-C2 80 L-140 bestückt ist.
Stepp by Stepp zu mehr Produktivität und Effizienz
Zur nachdrücklichen Sicherstellung der Produktivität und Wirtschaftlichkeit setzten und setzen Günter Kratschmayer und seine Mitarbeiter aber nicht nur auf einen leistungsfähigen Maschinenpark, sondern auch auf effiziente Werkstück-Spanntechnik. Über den langjährigen Lieferanten für die Maschinen und das relevante Fertigungstechnik-Equipment, die Firma Nagel Werkzeugmaschinen GmbH aus Ulm, kam man mit den Produkten des Schweizer Spezialisten für Werkstück-Spanntechnik und Produktionsautomatisierung Gressel AG, CH-8355 Aadorf, in Kontakt. Daraus entwickelte sich in der Folge eine nun schon über 20 Jahre anhaltende Zusammenarbeit. Die Entwicklungen der Fertigungstechnik und die Etablierung der 3- bis 5-Achsen-Komplettbearbeitung aktiv begleitend, kamen für die Fräsmaschinen und Bearbeitungszentren zunächst Standard-Maschinenschraubstöcke vom Typ gripos 100 und Einfachspanner grefors 125 zum Einsatz. Und um den zunehmenden Werkstückvarianten bei gleichzeitig schwankenden Stückzahlen gerecht zu werden, folgten später Mehrfach- Spannsysteme vom Typ multigrip 90 und Zentrischspanner der Baureihe centros². Für die weitgehende 3- bis 5-Achsen-Komplettbearbeitung wurden dann konsequenterweise div. 5-Achsen-Kraftspanner grepos-5X angeschafft. Den nächsten Technologie-Stepp bildeten die Mechanischen Nullpunkt-Spannsysteme gredoc NRS 10-fach und gredoc NRS 6-fach, die u. a. wiederum mit Einfachspannern der Größe S2 125 L-740 bzw. mit Doppelspannern der Größe D2 125 L-530 bestückt werden. Inklusive dem jeweils systemkompatiblen Zubehör an einfach und schnell zu wechselnden Spannbacken, ergibt sich bereits aus der vorhandenen „Spanntechnik-Bibliothek“ eine breit nutzbare Anwendungs-Flexibilität, die sich bis heute in der täglichen Praxis bewährt.
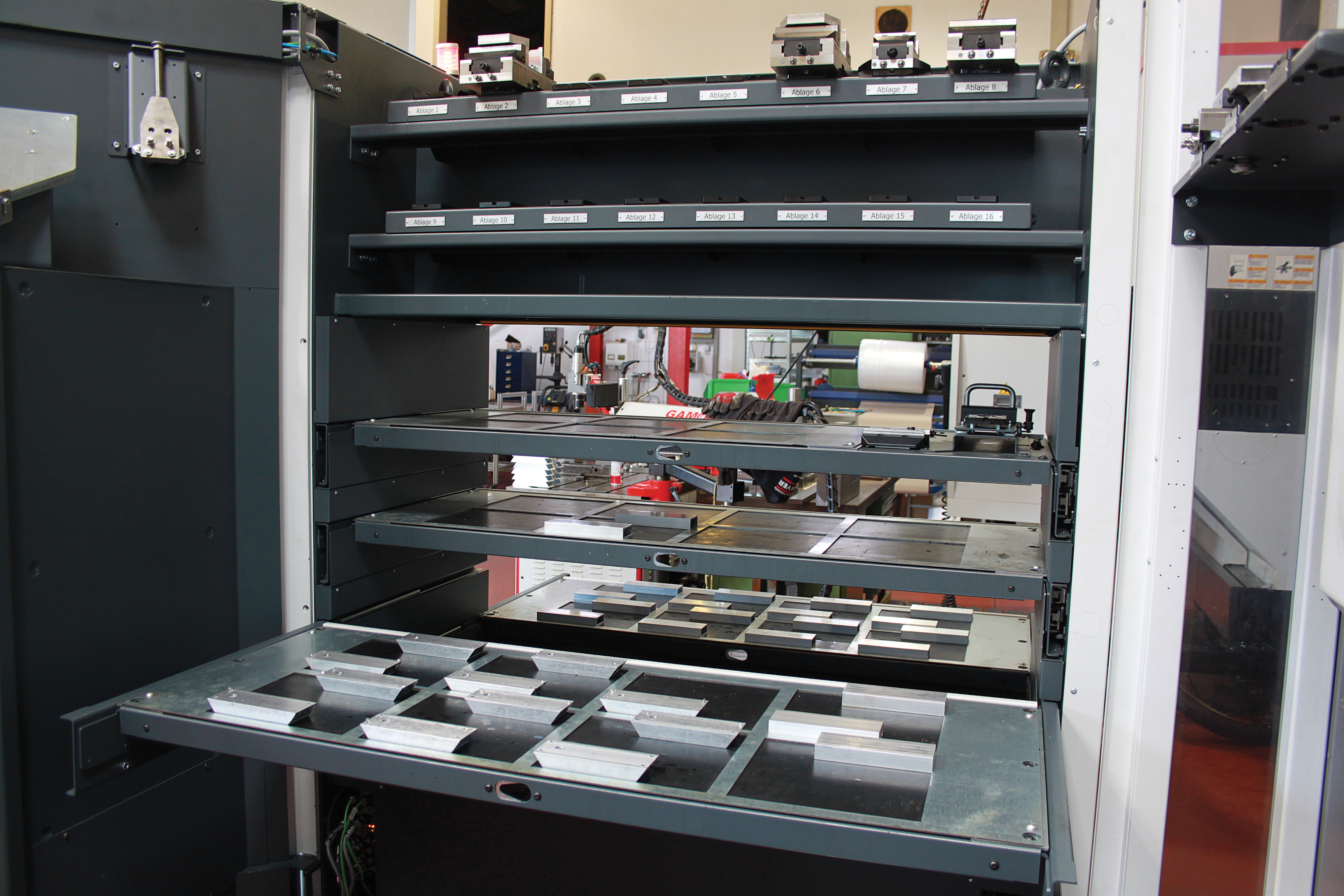
Das Werkstück- und Spannmittel-Magazin des neuen Automatisierungssystems PROMRO UD 50 zur Beschickung eines CNC-5-Achsen-Bearbeitungszentrums POSmill H800U.
Das erklärte Ziel: Vollautomatische Teilefertigung
Mit diesen Spannsysteme-Erfahrungen bestens gewappnet, wagten sich die beiden heutigen Geschäftsführer Günter und Sven Kratschmayer – zusammen mit ihrem Produktions- und Prozessprofi Bernhard Meinekke – im Frühjahr 2023 an das nächste „Leuchtturmprojekt“, nämlich die Automatisierung des Werkstück-Handlings an einem im Jahr 2022 beschafften CNC-5-Achsen-Bearbeitungszentrum. Die klar formulierte Aufgabe lautete, mit einem kombinierten Werkstückspann- und Beschickungsprozess die Rüstzeiten sehr deutlich zu verringern, die Flexibilität sicherzustellen, und in Summe höhere Maschinen-Laufzeiten und damit mehr Produktivität zu erreichen. Und auch hier konnten die Spezialisten von Gressel weiterhelfen, in dem Fall mit der Ausrüstung des Roboters mit dem kombinierten Werkstück-Greif- und Spannsystem R-C2. Dieser „greifende Zentrischspanner“ bildet praktisch die Schnittstelle zwischen dem vorhandenen CNC-5-Achsen- Bearbeitungszentrum POSmill H800U und dem Industrieroboter des Werkstück-Magazin- und Handlingsystems PROMRO DU-50, das mit einer Übergabestation des Typs 6S von Gressel ausgerüstet ist. Der Lieferumfang, bezüglich des Werkstück-Greif- und Spannsystems, umfasst somit zum einen die Übergabestation 6S, den Greif- und Spannkopf R-C2 und schließlich jeweils 3 Zentrischspanner vom Typ R-C2 80 L-140 bzw. R-C2 125 L-235 plus Backenzubehör für die Roh- und Fertigteil-Spannung. Zur Aufnahme der Zentrischspanner ist der Maschinentisch mit einem Nullpunkt-Spannsystem VERO-S Konsole (mit Medienübergabe und Zwischenflansch spezial) ausgestattet.
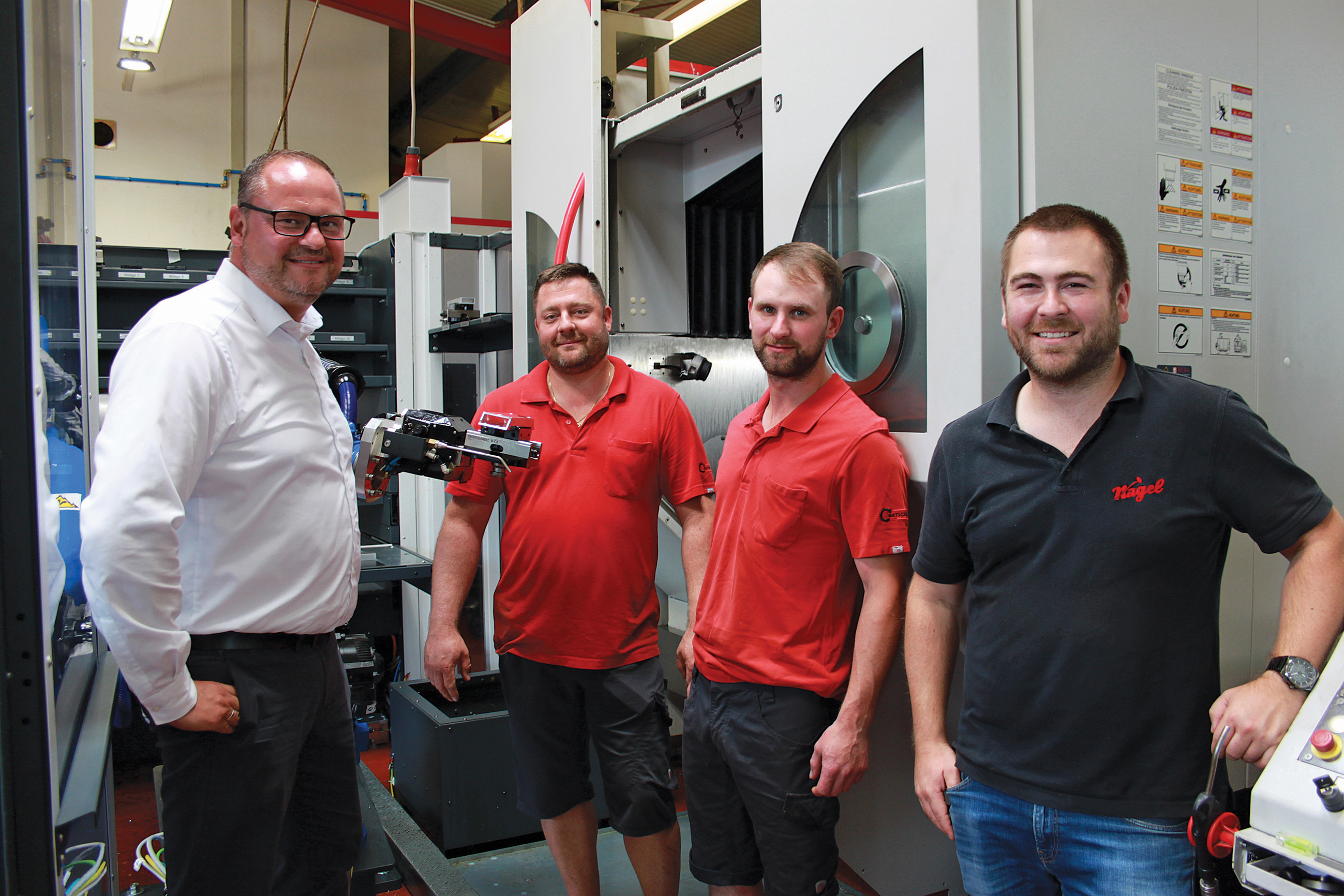
Von links nach rechts Frank Scheurer, Vertriebstechniker Deutschland Süd bei Gressel AG, Sven Kratschmayer, Geschäftsführer, und Bernhard Meinekke, Produktions- und Prozessspezialist, beide von Kratschmayer GmbH, und Alexander Leger, Vertrieb Außendienst von Nagel Werkzeugmaschinen GmbH.
Im Zentrum des Prozesses: Der greifende Zentrischspanner
Selbstredend ging der Beschaffung des Werkstück-Magazin- und Handlingsystems eine intensive Evaluierungsphase voraus. Letztendlich gab der Besuch bei den Automatisierungs-Tagen 2022 von Gressel im Stammhaus in Aadorf den Ausschlag. Denn dort konnten sich Sven Kratschmayer und Bernhard Meinekke anhand der Spannmittel-Produktion vor Ort von der Prozessfähigkeit der vollautomatischen Teilefertigung ein Bild machen. Folglich wurde das Projekt Produktions-Automatisierung im Januar 2023 gestartet und kam im Frühsommer zum Abschluss. In seinem Resümee führte Sven Kratschmayer aus: „Wir sehen uns als Universal-Fertiger und bearbeiten Fräswerkstücke in den max. Dimensionen L = 900 × B = 450 × H = 400 mm aus allen zerspanbaren Materialien. Wir bearbeiten bei ca. 100 Aufträgen pro Woche mit hoher Flexibilität ein sehr breites Teilespektrum und produzieren an 5 Tagen pro Woche im 1,5-schichtigen Betrieb sowie bei Bedarf auch am Samstag. Wir sind für die gebotene Produktivität und Wirtschaftlichkeit auf eine hohe Effizienz angewiesen und haben uns deshalb für das Investment in die Automatisierung entschieden. Heute sehen wir nicht ohne Stolz, dass wir zusammen mit unseren Partnern die Zielvorstellungen sogar übertroffen haben. Denn aktuell verzeichnen wir mit dem Fertigungssystem einen Produktivitätszuwachs von gut 70 %. Bezüglich der Frässtrategien und auch der Nutzung moderner Spannmittel war und ist zwar ein Umdenken unerlässlich, aber wenn man den Automatisierungs-Prozess erst einmal verinnerlicht hat, stellt sich der Erfolg umgehend ein.“

Die Übergabe des mit einem Werkstück versehenen Zentrischspanners R-C2 80 L-140 auf das Nullpunkt-Spannsystem VERO-S Konsole, welches auf dem Maschinentisch positioniert ist.
