Carbide in focus: The right choice for a precision tool
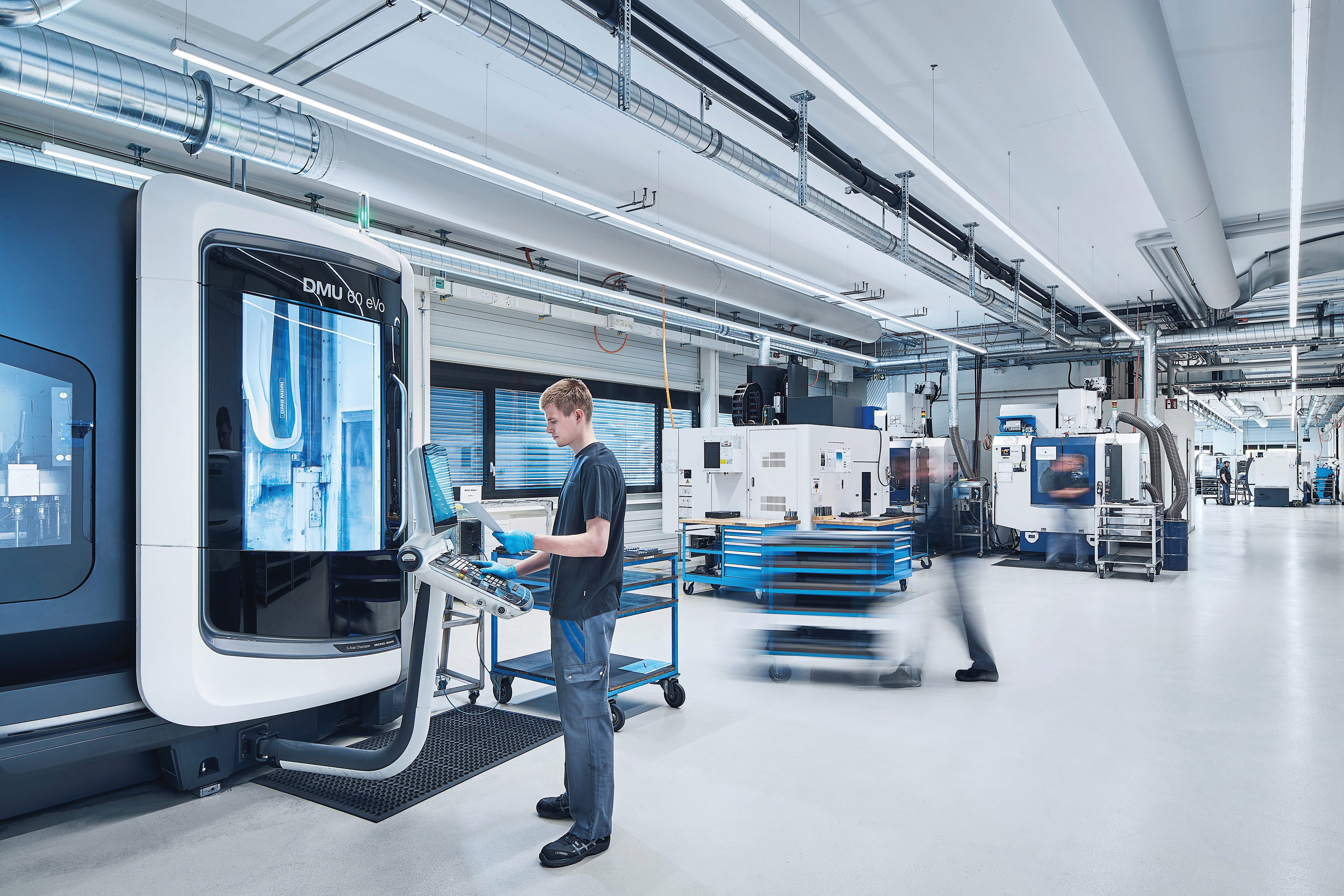
Complex products and modern high-tech materials are placing ever greater demands on precision tools. Carbide tools have numerous advantages over HSS tools: They are harder, more wear-resistant, more heat-resistant and, with a few exceptions, have a longer service life. They enable high-precision machining and higher cutting speeds. The prerequisite for this is the perfect combination of substrate, geometry and coating. The carbide as the basis is of particular importance here. CemeCon and EXTRAMET have been working together for many years to develop the best combination.
Carbide has extremely good properties for cutting tools: such as hardness, compressive strength, impact resistance, flexural strength, corrosion resistance and more. Over the past 30 years in particular, enormous progress has been made in manufacturing, and the relationship between hardness and toughness has been significantly optimized. Today, carbide tools have replaced HSS tools in almost all areas,” describes Bruno Süess, former director and current member of the supervisory board of EXTRAMET AG, board member of the Swiss Powder Metallurgy Association as well as expert in carbides and their production and advantages.
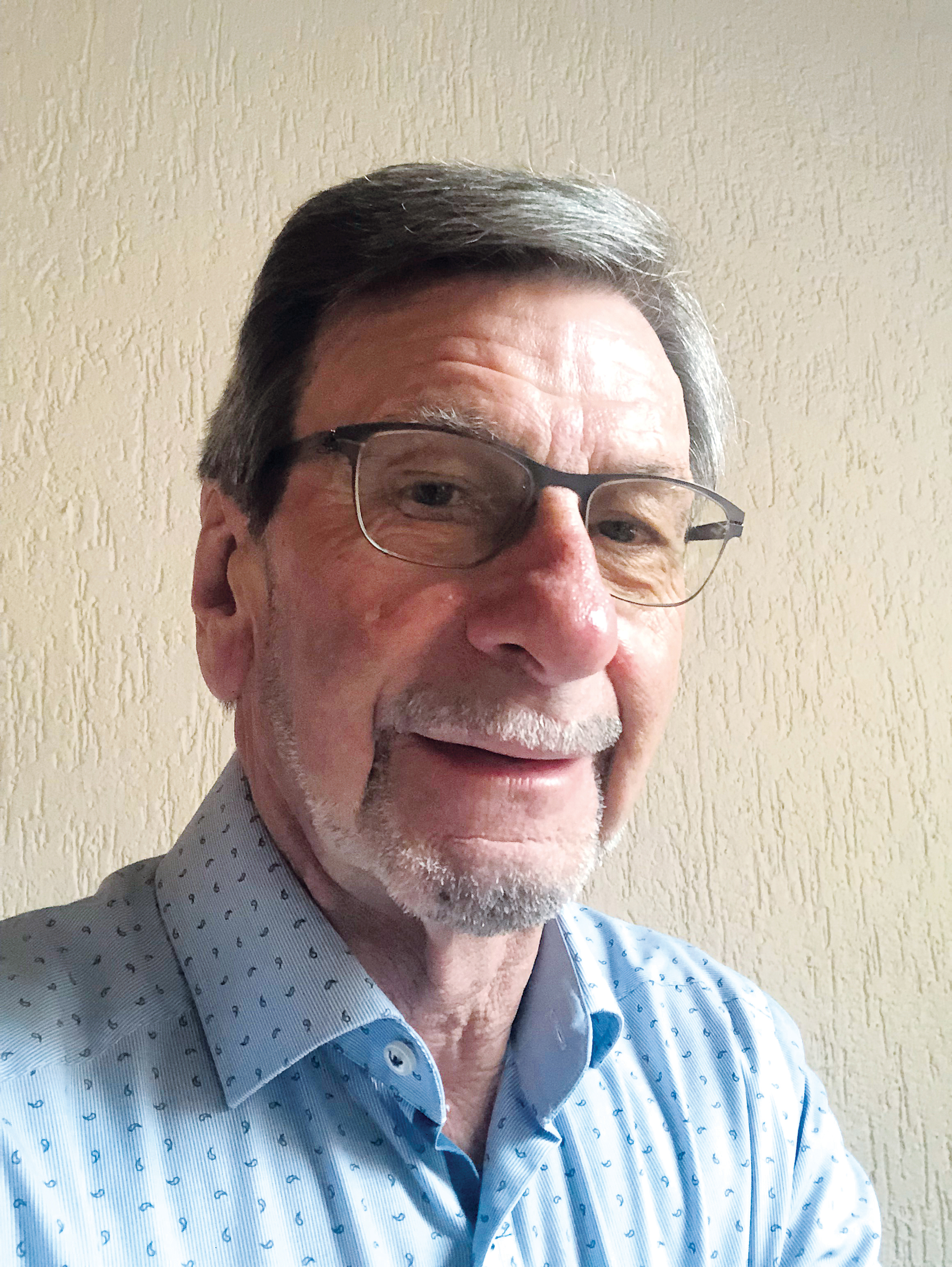
Bruno Süess, former director and current member of the supervisory board of EXTRAMET AG.
It all depends on the composition
Carbide for cutting tools consists mainly of tungsten carbide (WC) as the hard material and a binder metal, usually cobalt (Co). The tungsten carbide provides the hardness and the cobalt provides the toughness. This combination enables the best physical and mechanical properties to be achieved. The exact composition and the addition of other alloy components are very flexible and depend on the requirements of the application.
The hardness of a carbide is primarily regulated by the WC grain size: the finer the grain, the harder the carbide. In machining, carbides with ultra-fine grain (0.2 – 0.5 µm) and micro grain (0.5 – 0.8 µm) are now standard. Nano grain (<0.2 µm) has not yet been able to establish itself and is only used for very special purposes. Production is far too costly compared to the benefits that the extremely small grains bring in comparison.
“But hardness isn’t everything: The wear resistance also depends on how well the hard tungsten carbide grains are embedded in the cobalt binder metal, how well they are wetted and how well they have bonded there. If the cobalt is not well distributed and the WC grains are therefore directly adjacent to each other, they simply detach from the matrix, resulting in increased wear,” says Bruno Süess. “To achieve high wear resistance, you have to find the perfect balance between grains and binder so that the tungsten carbide is still well bonded but the cobalt content is not too high. This ratio can be easily controlled today, so that many high-performance carbide grades are now available on the market.”
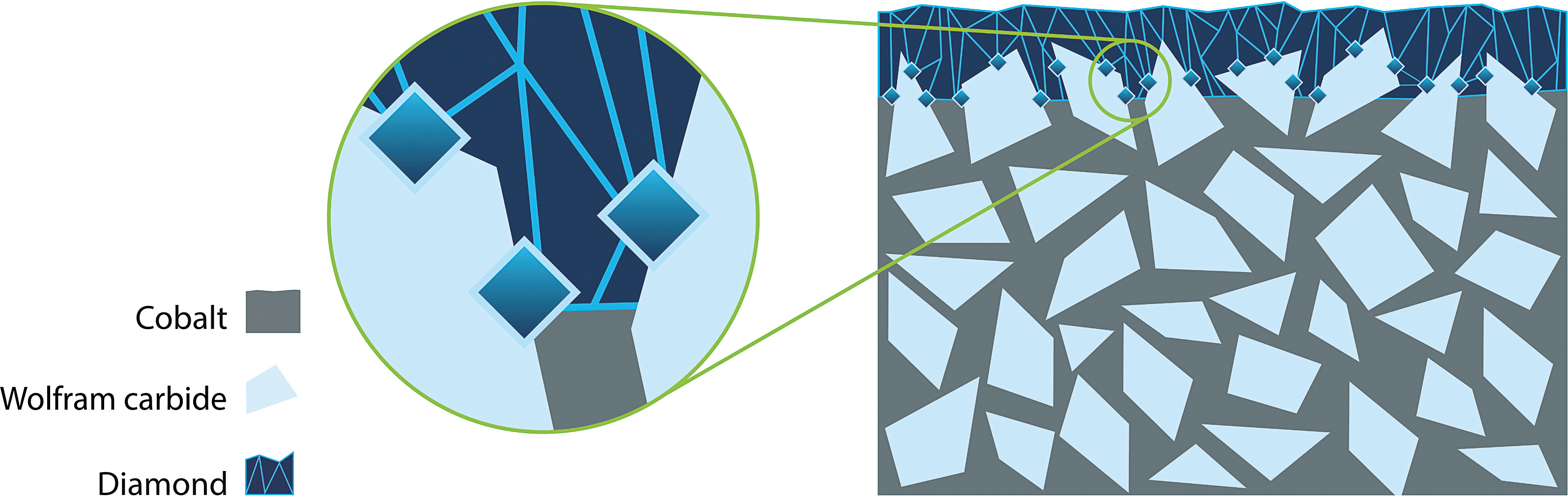
When coating with diamond, the proportion of cobalt in the carbide is of particular importance. It must neither be too large nor too small. CemeCon is happy to advise tool manufacturers on the selection of a suitable carbide on request. Photo: CemeCon AG
Diamond coatings for carbide tools
The composition of a carbide is decisive for its coatability with diamond coatings. “In the past, the adhesion of the diamond coating to the carbide was not as good as it is today. That’s why we – CemeCon and EXTRAMET – worked closely together back in the 1990s to adapt the composition of the carbide and thus improve adhesion. For example, we developed a special carbide grade for diamond coating with selected alloy components. In a trilateral working group, particularly with regard to the requirements of the aviation industry, we were able to achieve great progress for diamond tools together with the Technical University of Hamburg-Harburg (TUHH),” recalls Bruno Süess.
Precise, durable and sustainable carbide solutions for the high-tech industry are EXTRAMET’s core competence. The high-quality carbide tool blanks are the basis for the production of high-precision rotary cutting tools for demanding applications. Since its foundation in 1980 in Plaffeien, Fribourg (Switzerland), EXTRAMET has developed from an original three-man operation into a broadly diversified and internationally active company with over 200 employees worldwide. In the production of extruded carbide, the experts focus on innovation, precision and high technology and offer customized solutions for individual requirements. Maximum precision combined with top-quality carbide makes the family-run company the ideal partner for the highest demands in high-tech industries. EXTRAMET carbide is used in the aerospace and automotive industries, dental and medical technology, precision and micromechanics, as well as in food and packaging technology.
For good coatability, it is important that the grain is not too fine and that the carbide does not contain too much cobalt. “My personal favorite for diamond coating is a micro-grain carbide with a WC grain size of 0.8 to 0.9 µm and 6 percent cobalt,” adds Süess.
The cobalt content is particularly important when it comes to coating with diamond, as the cobalt is dissolved from the surface of the carbide during the coating process. Manfred Weigand, Product Manager Round Tools at CemeCon, explains: “If the proportion is too small and too much cobalt is dissolved, the WC grains no longer hold together. The carbide becomes too brittle and good adhesion is no longer possible. If the proportion is too large, too much cobalt remains, which reacts with the carbon during the coating process. This results in a graphitic phase (sp2) instead of the hard diamond coating (sp3).”
For this reason, CemeCon carries out appropriate suitability tests in which the carbide is tested for its coatability.
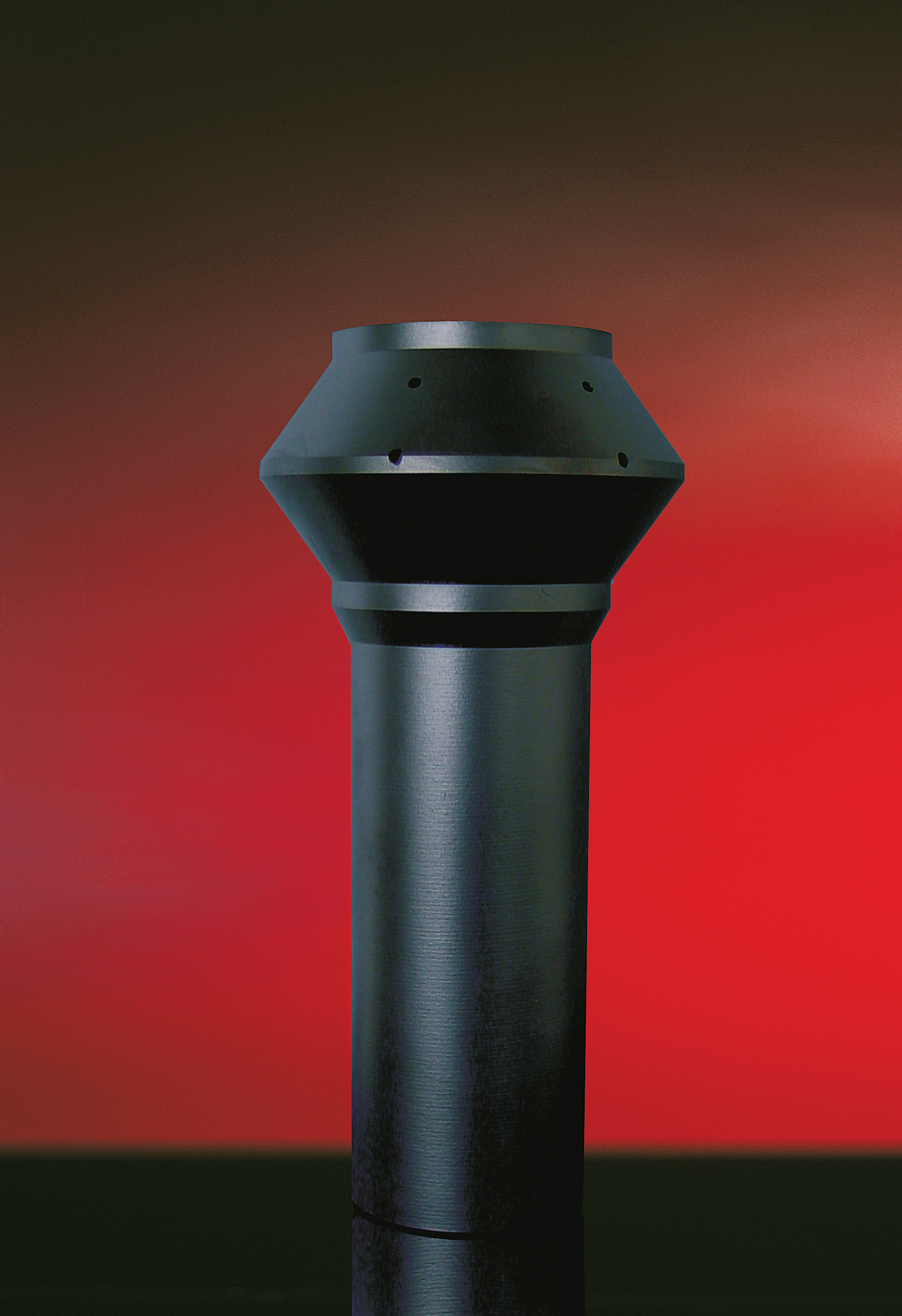
Carbide part from EXTRAMET. Photo: EXTRAMET AG
Only high-quality carbide ensures premium coatings
The homogeneity and therefore the quality of a carbide has a significant influence on the coating result and therefore also on the performance of the precision tool. High-quality carbides achieve both good adhesion and a uniformly coated surface. “Purity in the carbide manufacturing process and consistently high quality are inextricably linked. This starts with the mixing of the powder. It should be exposed to an oxygen atmosphere for as short a time as possible to prevent oxidation. It is therefore important to process the powder quickly, as the material oxidizes if it is stored for a long time. However, as soon as the powder is pressed and the green compact is pre-sintered, not much more happens in this respect,” explains Bruno Süess.
Another factor for the quality – even within a batch – is the sintering process. If some of the green compacts are exposed to a higher carbon concentration than others, the carbon content varies in the carbide blanks and ultimately also in the ground tool. These differences can lead to poor and/or uneven adhesion of the diamond coating.
Almost no difference in quality compared to recycled carbide
Resource conservation, environmental protection and the CO2 balance are becoming increasingly important in carbide production, as in all industries. The recycling of worn carbide tools is also becoming increasingly important in view of the mining areas and the conditions prevailing there. Processes have made great progress in this area, with the result that the proportion of recycled carbide has risen steadily in recent years. Using chemical processes, all components of the carbide can be separated into their constituent parts – tungsten carbide, cobalt, etc. – and transferred back into the raw products – with less energy input.
“Many carbide manufacturers, including EXTRAMET, now use a mixture of new and recycled material. There are no longer any differences in quality between high-quality recyclate and new powder,” says Bruno Süess. Hard metal made purely from recycled material has hardly been available on the market to date, but corresponding developments have already been initiated. “At CemeCon, we have already tested tools made from 100 percent recyclate for their suitability for diamond coating. We have also tested the concentricity before and after coating. We were able to give the green light after all the tests,” adds Manfred Weigand.
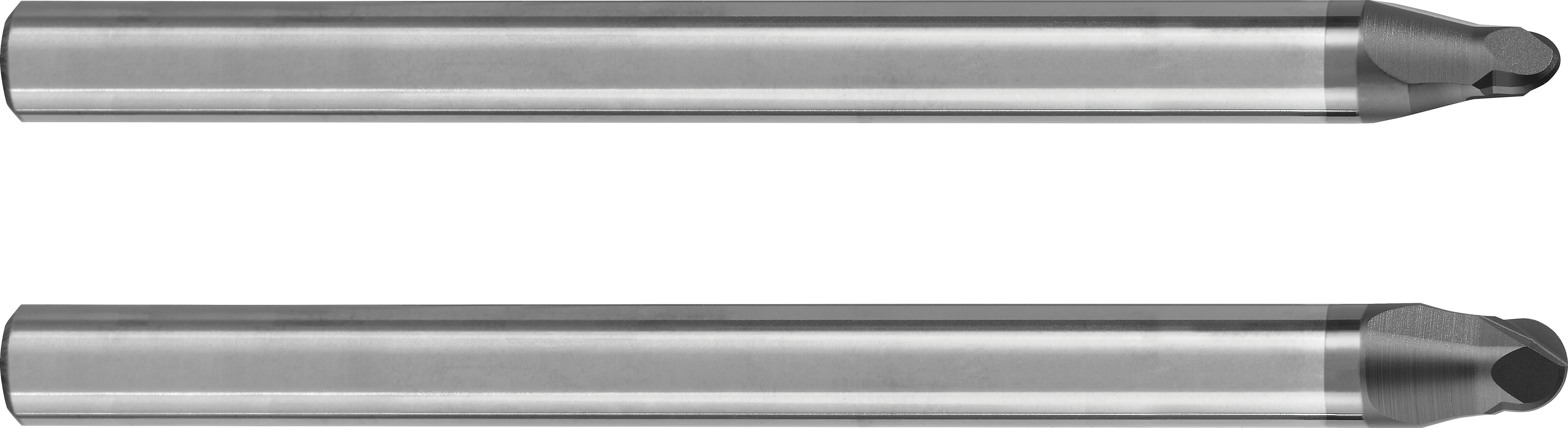
End mill with diamond coating. Photo: CemeCon AG
Major challenges for the future
In addition to the declining demand for carbide due to the switch to alternative drive systems in the automotive industry, the effects of the REACH Regulation (European Chemicals Regulation on the Registration, Evaluation, Authorization and Restriction of Chemicals) are certainly among the major challenges facing the carbide industry. REACH has also placed cobalt (Co) and nickel (Ni) on the red list. Manufacturers are therefore forced to minimize or completely replace cobalt and nickel in the composition of hard metals without changing their positive properties. Research has already achieved encouraging results in recent years, but the new carbides do not yet meet the desired mechanical requirements, especially when it comes to solutions for cutting tools.
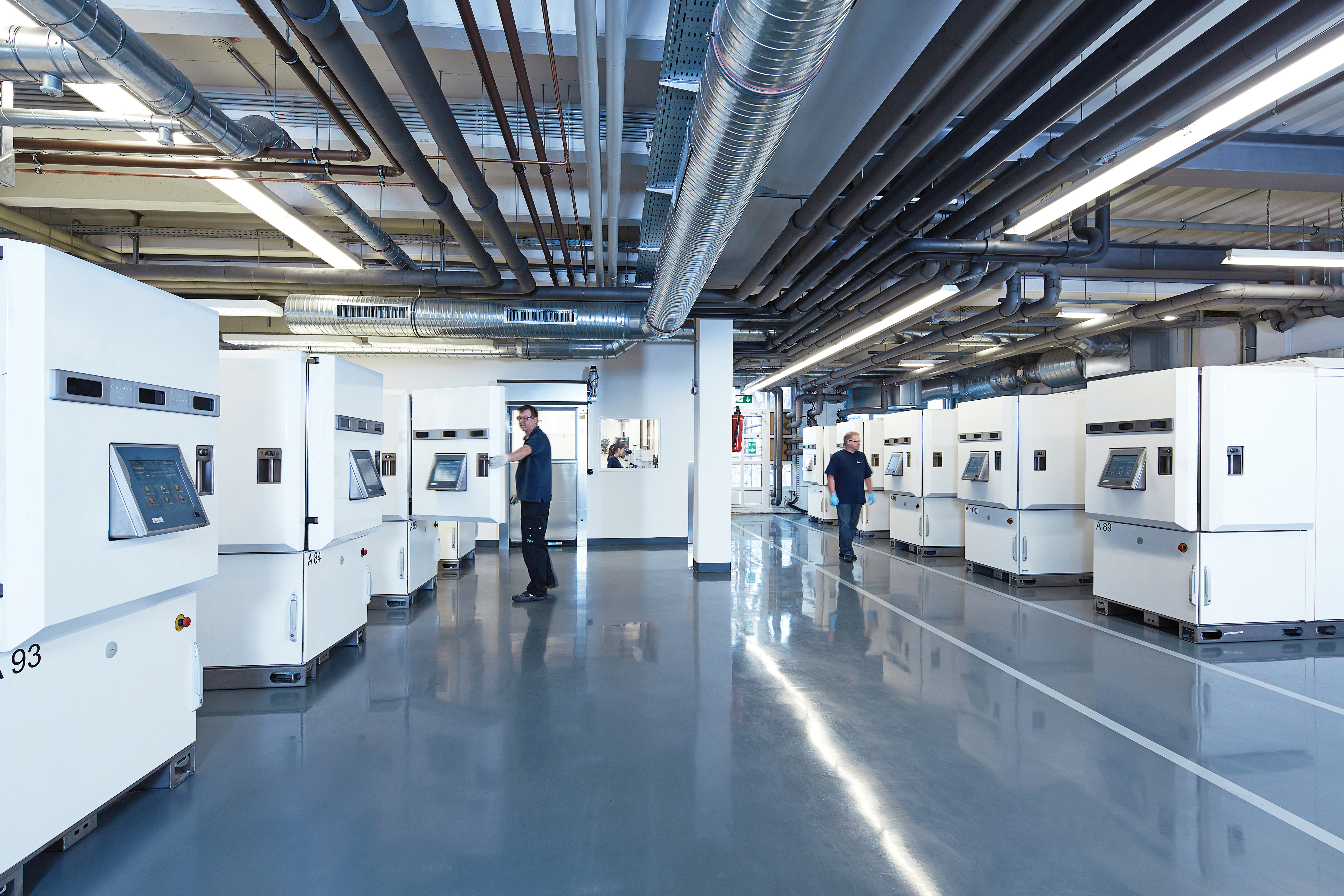
CemeCon operates the world’s largest diamond coating center in Würselen. Photo: CemeCon AG
