Creating a chain reaction with precision spindle heads
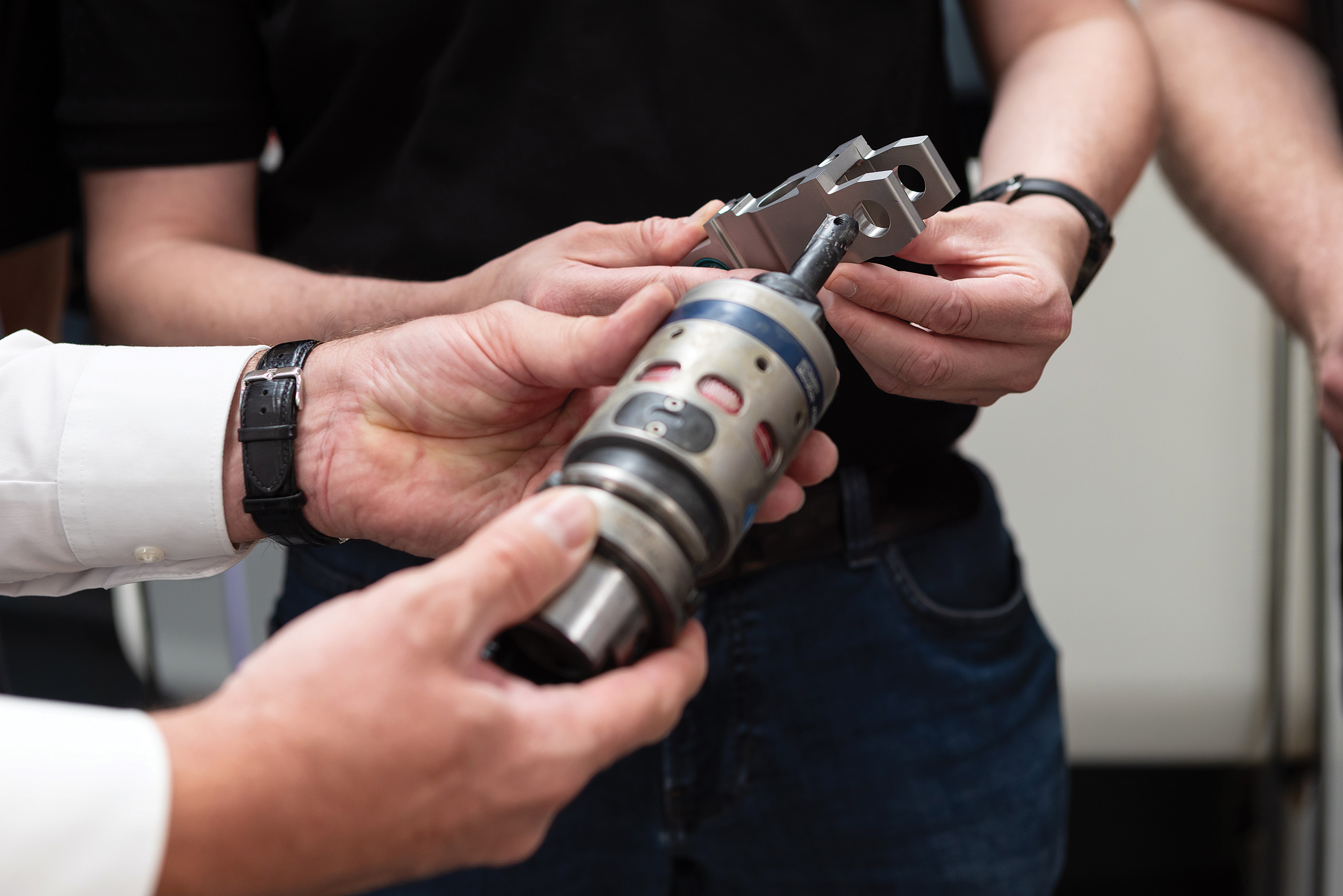
Without furniture, a room is just an empty room. Once filled with couches, desks, chairs and desks, however, these spaces transform into a place of work, a place of comfort or leisure and living areas. But it’s this blank canvas dynamic that presents a tricky design and manufacturing challenge for the furniture industry. Thanks to customized production systems from IMA Schelling Group, production processes are streamlined for ease and efficiency. A major contributing factor to IMA Schelling’s success is the KOMflex precision spindle head from CERATIZIT, which ensures drive chains, an essential component of these production systems, can be manufactured automatically.
From rooms to yachts and motorhomes: attractive interior fittings and furnishings play a key role in turning customer wishes into reality and creating a feeling of home in any space. Just as key are efficient, sustainable industrialized manufacturing processes. It’s here where the specialists at IMA Schelling Group come into play as pioneers in the development and manufacture of modularized special systems and processing solutions for the wood, metal and plastics industries.
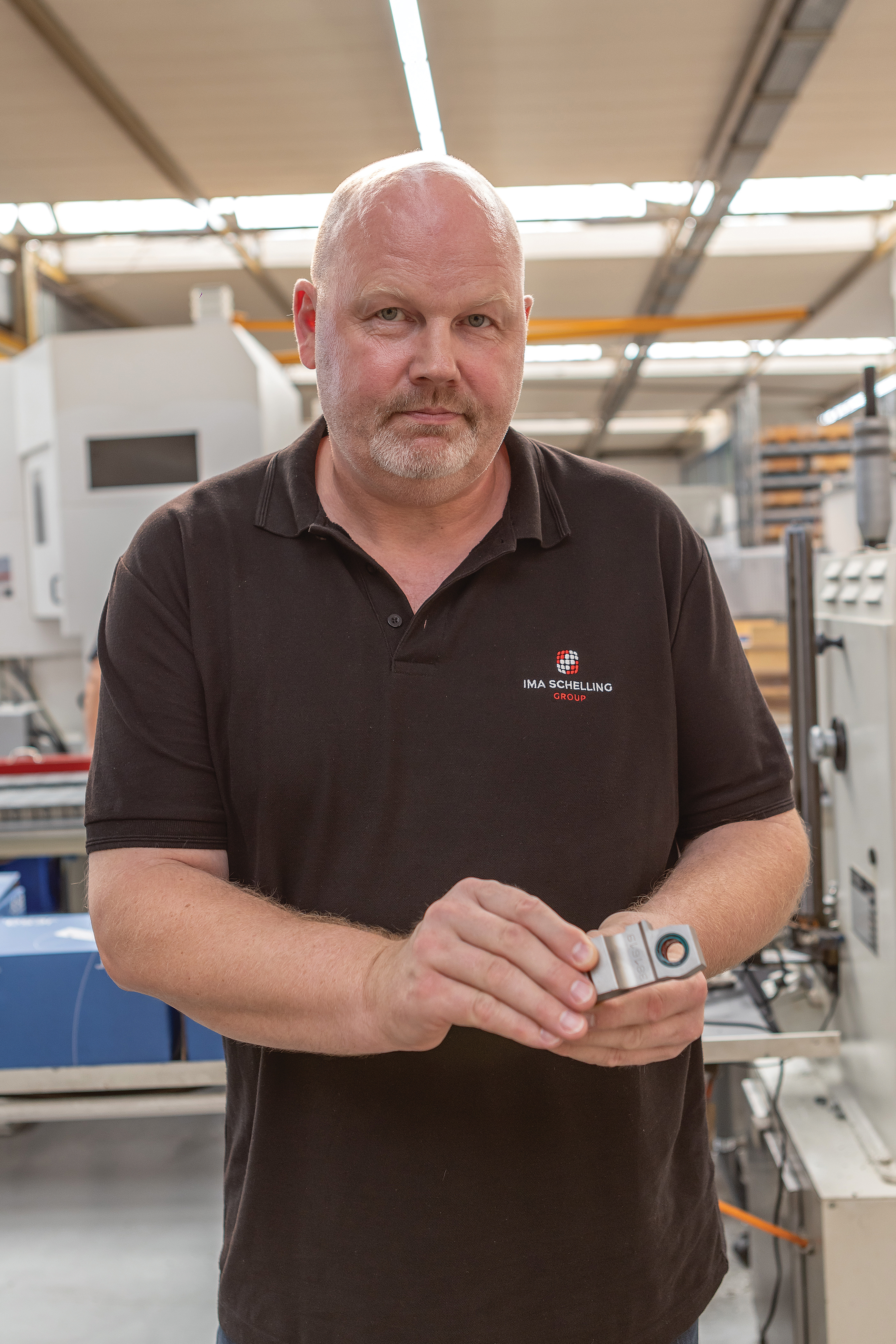
Dietmar Tiemann, Head of Chain Construction at IMA Schelling, with an chain link for IMA Schelling machines produced with the newly automated manufacturing process.
Holistic solutions – no matter the industry
IMA Schelling Group provides unparalleled solutions and expertise to wood, metal and plastics processing industries all over the world. With a product range including systems for the entire process chain, from storage, cutting, handling and transportation to complex processing steps such as edge banding, CNC processing, drilling and sorting, IMA Schelling Group designs and manufactures both standard machines and customized special solutions, including fully automated batch size 1 systems.
One of the key challenges – and one that not only applies to the woodworking industry – is to provide customers with a full-service package. “That’s why we not only offer customizable and highly specialized machines, but also comprehensive services and digital solutions,” says Dietmar Tiemann, Head of Chain Construction at IMA Schelling. “In doing so, customers can reap the benefits of automated workflows and efficient production processes.”
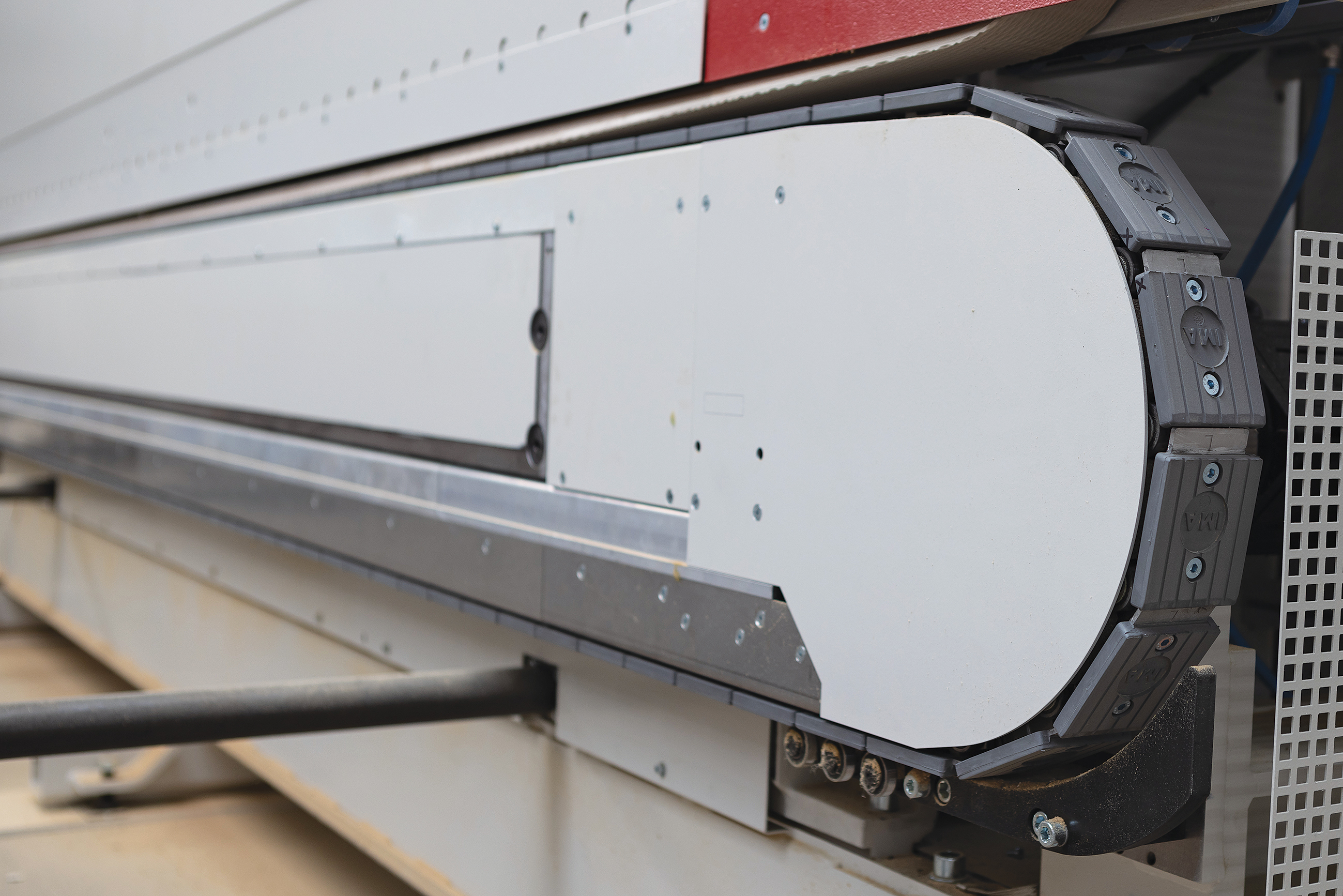
Chain links are fundamental elements in an IMA Schelling machine used for the furniture industry.
One-stop shopping for machining
IMA Schelling has the enormous advantage over the competition in that it handles nearly the entire process itself – from sales to project planning, design, production, assembly and in-house machine control. “When it comes to machining, we have a high level of vertical integration; only a few parts have to be machined externally, says Tiemann. “And in those rare instances that we must machine something externally, for example with special solutions, we work closely with nearby companies so that we can remain agile and maximize our sustainability.”
Another major contributor to a successful machining strategy are the tools used. For nearly 4 decades, IMA Schelling has relied on tools and services from CERATIZIT. “Sales representatives from CERATIZIT regularly visit and advise us on all questions concerning tools and the corresponding machining parameters. We use solid drills, spindle tools, reamers, solid carbide milling cutters – the entire range,” says Dietmar Tiemann.
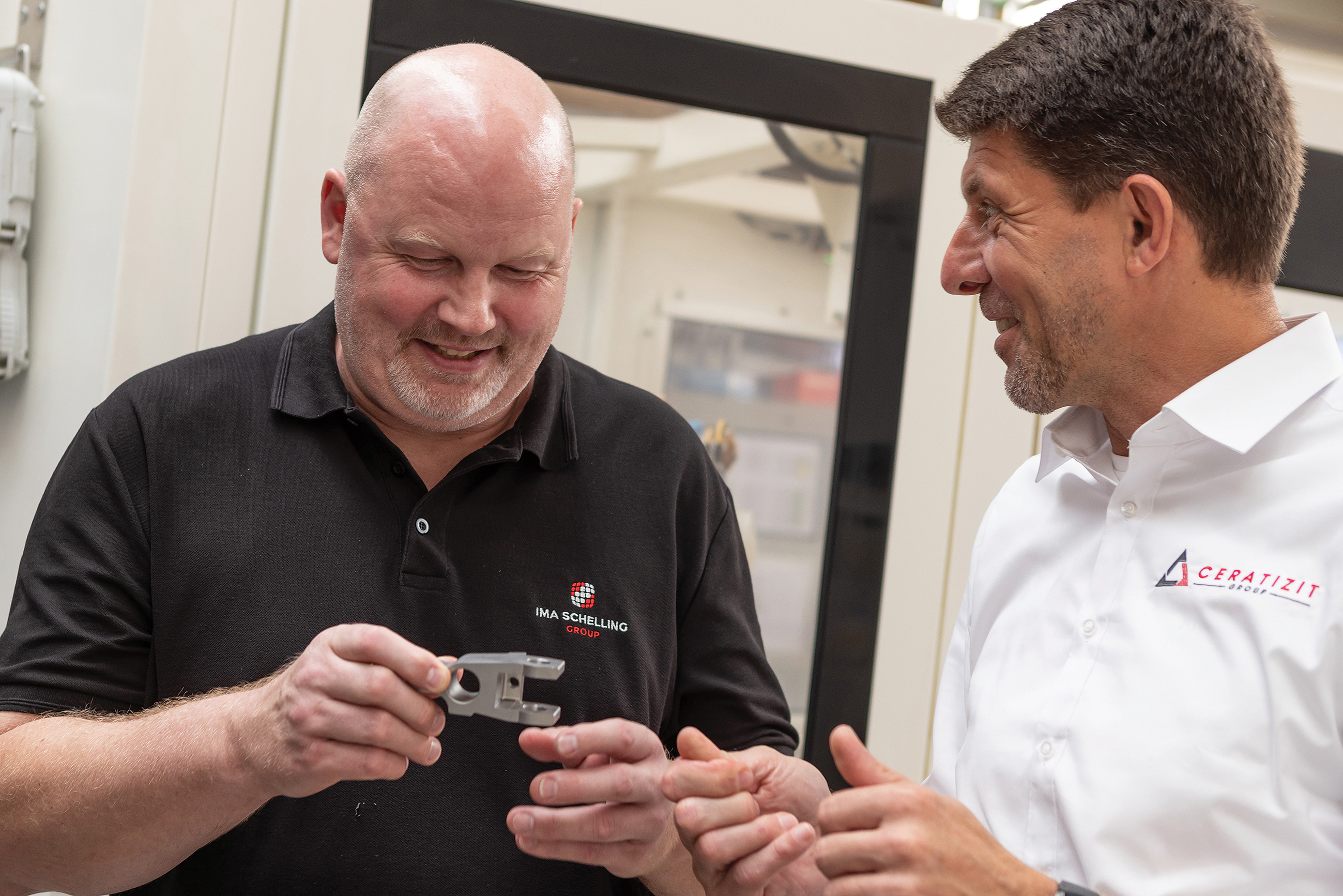
Reflecting on a job well done (from left): Dietmar Tiemann and Heiko Reimann, Sales Representative at CERATIZIT.
Moving the chains together
CERATIZIT sales representative Heiko Reimann was also there to help IMA Schelling and Tiemann automate production of drive chain links. “When Mr. Tiemann told me about the need for a reliable solution for their automation plans, we quickly identified the KOMflex fine spindle head as being an ideal fit. Thanks to the integrated radio unit, it communicates directly with the machine control system via the universal RC66 radio receiver from BLUM Novotest GmbH. This enables a closed-loop system where the KOMflex and the BLUM measuring probe communicate to measures and adjusts the cutting edge position, thus automatically correcting the diameter of the fine spindle tool.”
The biggest task in implementing the KOMflex spindle head was to ensure that it could be used reliably by the machines and programs already in place and, of course, by the production technicians. “In our mechanical production, we are always incorporating new technologies and processes to become leaner. For example, instead of only producing chain links in the early shift as we previously did, we sought to run the chain link production process on the late shift, as well – with as few people as possible,” says Tiemann.
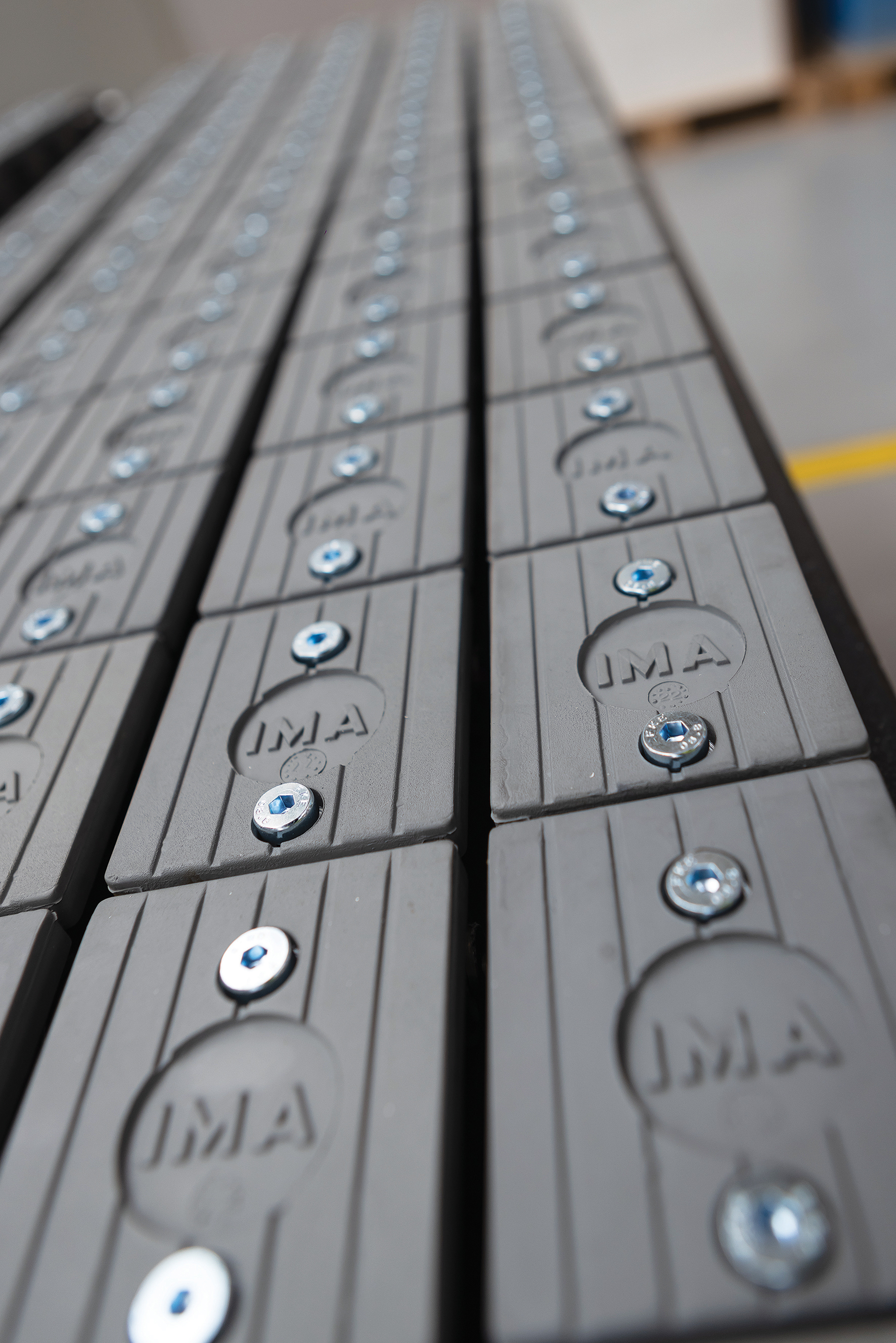
Each machine uses several chain links Fast throughput times and unmanned production processes are essential for efficiency and competitiveness.
Robust, efficient, game-changer: KOMflex
Thanks to close collaboration with CERATIZIT, IMA Schelling quickly mastered these challenges successfully – due in large part to the properties and technical specs of the KOMflex fine spindle head. It’s capable of speeds of up to 4000 min-1 and guarantees an adjustment positioning of 2 µm in radius. Depending on the tool, the KOMflex can spindle bores with diameters between 6 mm and 120 and is very robust thanks to its maintenance-free drive.
Initially, IMA Schelling was a bit sceptical as to the tool’s practical feasibility. “But once the staff saw the automation potential in KOMflex, those concerns were quickly allayed. What’s more, the expectations placed on the system were not only met, but exceeded,” says Tiemann. That statement is by no means solely based on a subjective gut feeling, but backed up by hard data. “With the KOMflex fine spindle head, we were able to increase the production of some standard items for throughfeed technology by up to 70 percent,” says Tiemann. “As a result, we have not only increased efficiency, but also improved our company’s competitiveness.”
Shared motivation – and success
Heiko Reimann: “We are seeing more and more customers seeking direct contact with manufacturers. By working closely with the application technology, we are able to solve some issues much faster. As customers expect service and support, that’s precisely what we strive to deliver.” Dietmar Tiemann is also a proponent of the partnership. “From CERATIZIT, we receive information based on practical experience – even from other industries and applications where similar challenges needed to be solved. This know-how and experience is very helpful and helps make it a win-win situation for everyone involved.”
The decisive factor for the project with the KOMflex spindle head was that IMA Schelling wanted a reliable and high-quality solution. “Looking at the result, all of our expectations have been met in their entirety. In fact, there is a very good chance that we’ll automate further machines in the future using KOMflex from CERATIZIT and thus further optimize our total efficiency,” says Tiemann.
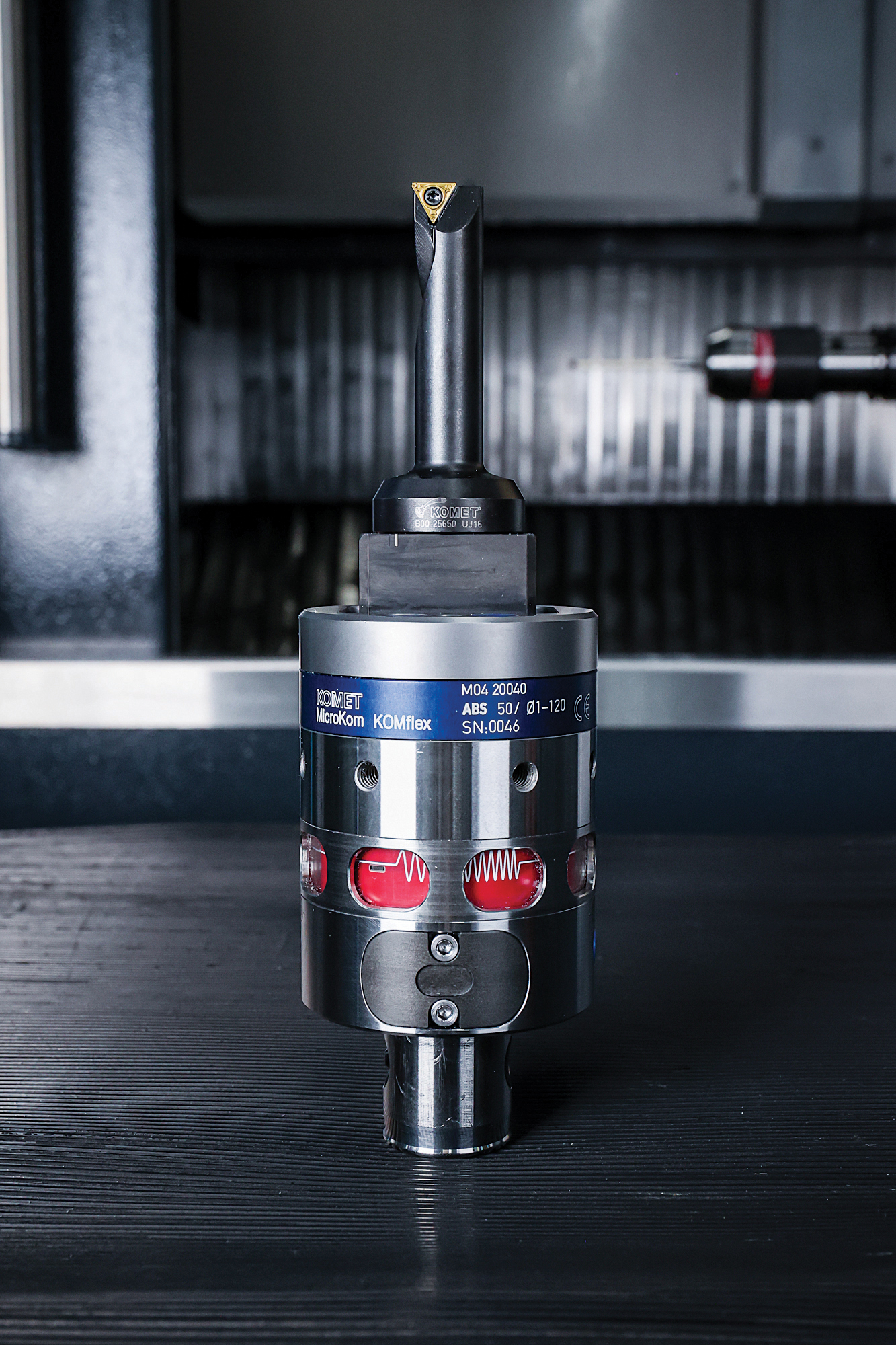
The KOMflex spindle head from CERATIZIT.
