Discover High-Performance Inserts
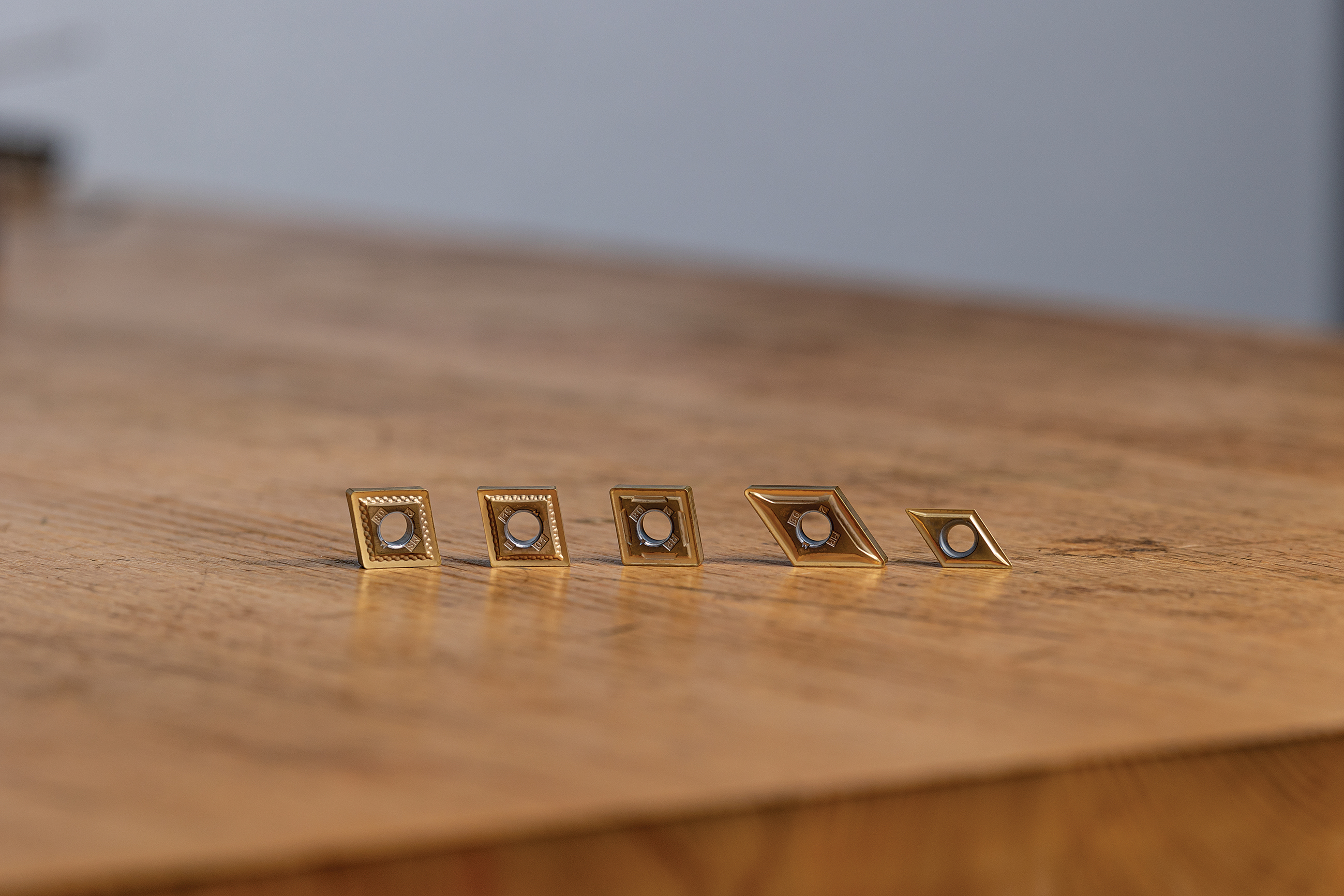
Kennametal is an industry leader in insert technology, using strong tungsten carbide-based materials to both ensure accuracy and extend the life of each insert we make. Having the right equipment for metalworking keeps your business competitive in your sector.
With Kennametal inserts, you have access to the correct performance inserts for precise and low vibration cutting, allowing you to achieve true and consistent results every time. Explore a few of our inserts below. Let’s take your manufacturing to the next level.
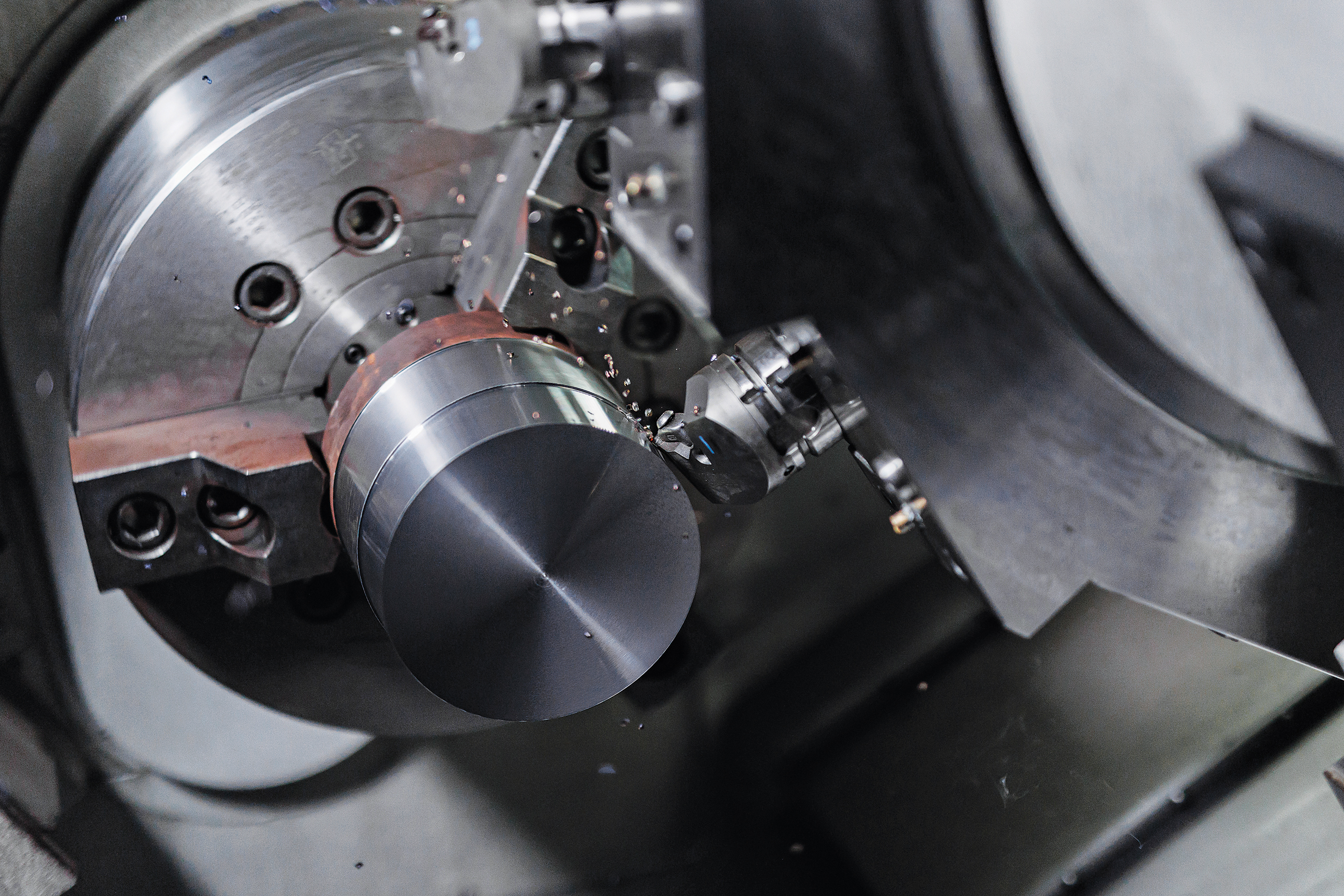
Kennametal’s KCP25C.
KCP25C
KCP25C is a steel turning grade with KENGold™ CVD coating technology that’s delivering the most reliability for enhanced edge protection in turning applications. KENGold is the next generation of CVD coating technologies featuring uniform layers that resist abrasion, provide a strong thermal barrier, improve edge toughness, and allow for easy detection of wear due to its gold flank.
Leveraging advanced pressing and honing technologies, Kennametal has achieved consistently tight tolerance levels with KENGold and has applied the advanced coating to the KCP25C grade. The grade is extremely versatile when machining steel in a wide range of turning applications. It offers improved toughness and resistance to abrasion and chipping.
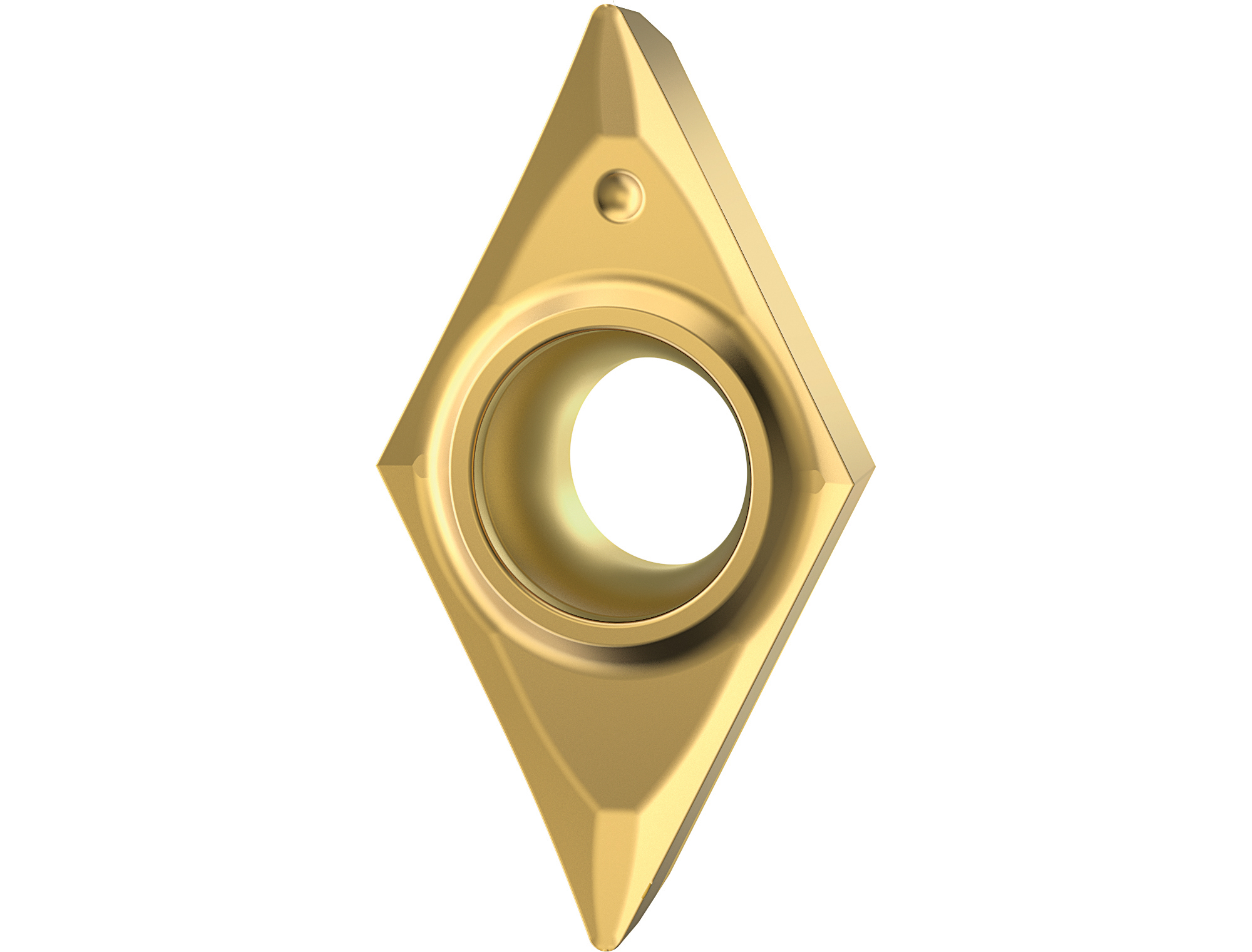
Kennametal’s KCU10B.
KCU10B
KCU10B upgrades Kennametal’s existing KCU10 with a newly engineered KENGold™ PVD, multilayer coating that makes machining from one material to another easy while also achieving consistency in cutting. The nano-composite coating has an enhanced coating adhesion that delivers better flank and chipping resistance. Upgrade your multi-material projects and beat deadlines when working on steels, stainless steels, cast iron, high-temp alloys and non-ferrous materials.
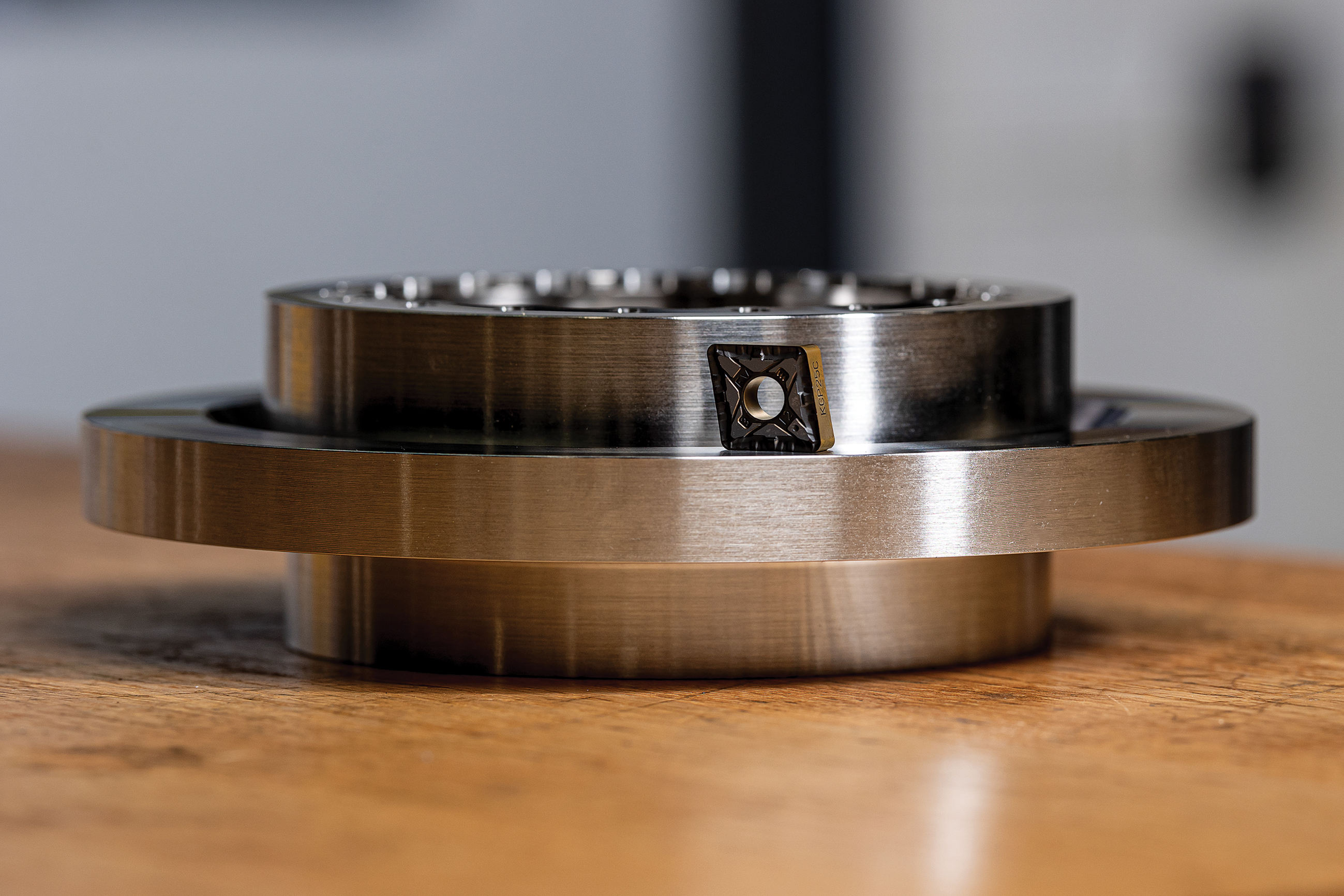
Kennametal’s FV Geometry 1.
FV Geometry
The high-performance FV geometry turning inserts feature a unique chip breaker design, sharper edge and built in coolant channels, offering improved surface roughness and chip formation. These inserts are best suited for shops working in transportation and general engineering and bring a flexibility to operations, supporting consistent chip control in low or medium depths of cut and requiring less process interruptions for tool changes.
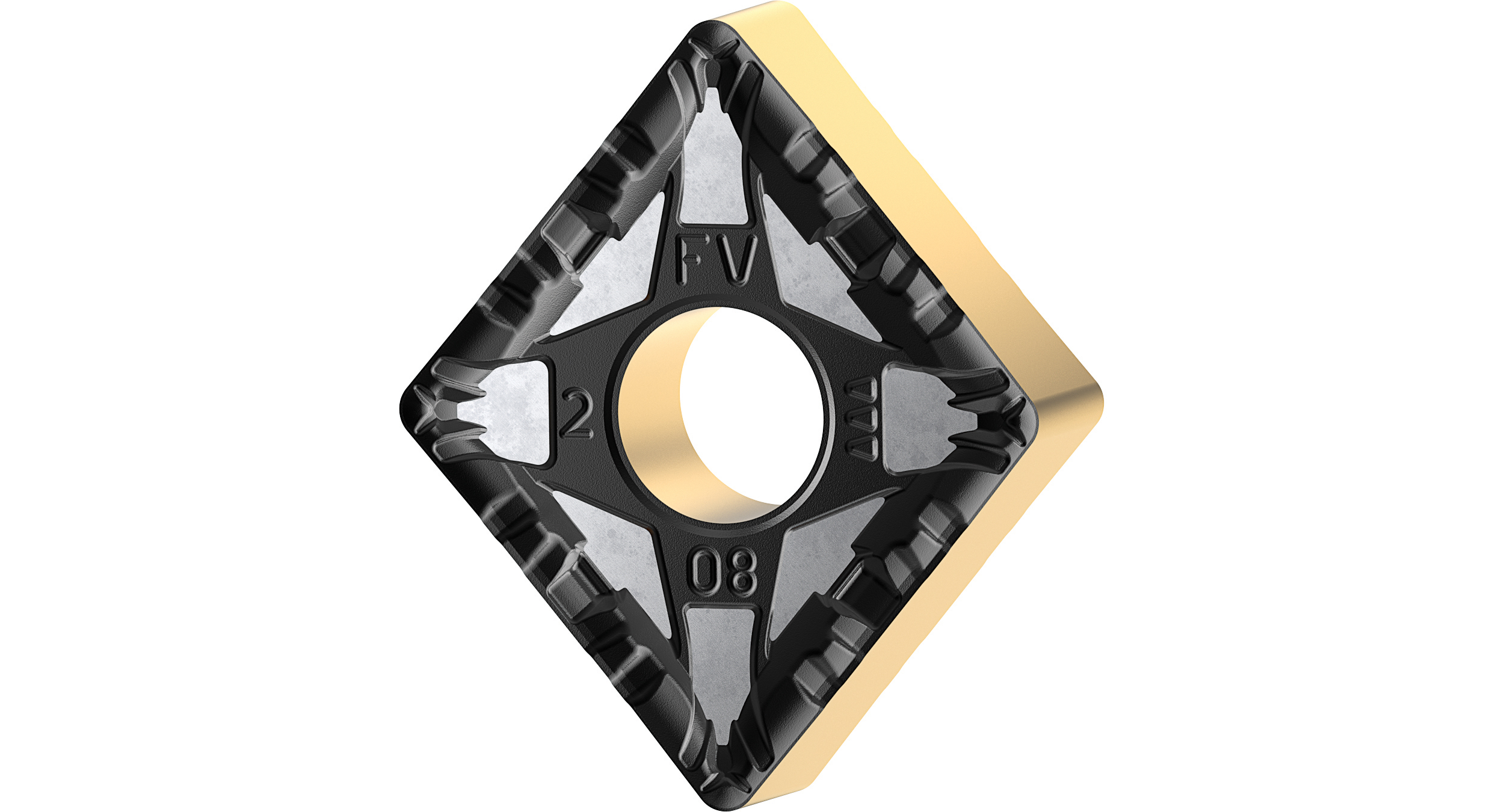
Kennametal’s FV Geometry 2.
