Fahrzeugemissionen reduzieren
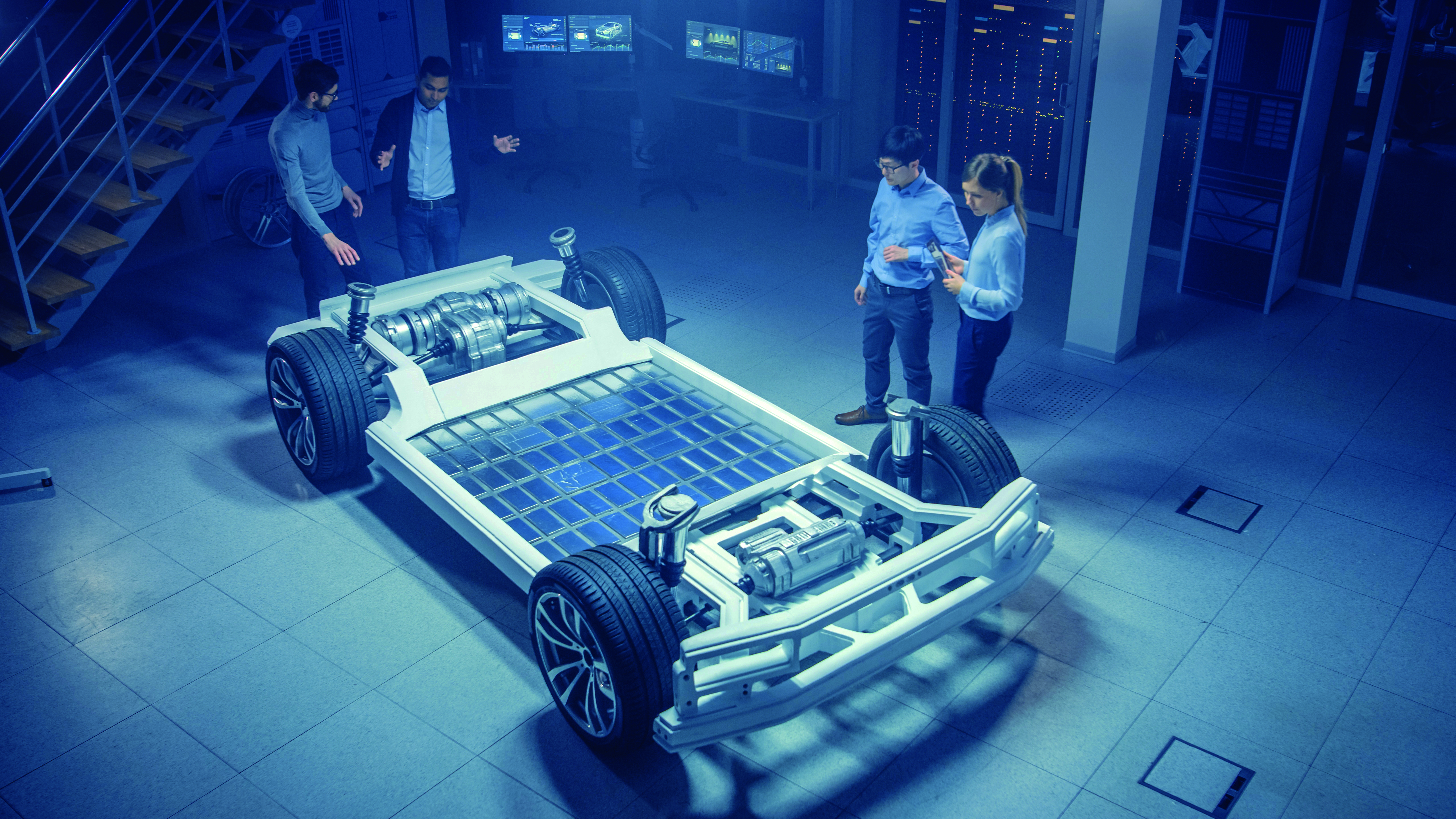
„Gewichtsreduzierung ist ein wirksames Mittel, um die Emissionen eines Fahrzeugs zu senken“, heißt es im Fact Sheet des International Council of Clean Transportation (ICCT): Report Europe. Die Automobilhersteller stehen damit in der Verantwortung, gewichtseffizientere Bauteile zu produzieren. Schweres Gusseisen und Schmiedestahl sind jedoch nach wie vor beliebt, und die Hersteller müssen diese „schweren“ Metalle so konstruieren, dass sie gewichtseffizient sind. Sangram Dash, Product Application Manager für das Wendeschneidplattenfräsen bei Sandvik Coromant, zeigt auf, wie diese Herausforderung durch leichteres und präziseres Eck- und Planfräsen gelöst werden kann.
Der McKinsey-Bericht Lightweight, heavy impact, der auf den Ergebnissen des ICCT aufbaut, rechnet detailliert vor, wie leichtere Fahrzeuge weniger CO2 ausstoßen: „Leichtbaumaßnahmen können dazu beitragen, die CO2-Emissionen bis zu einem gewissen Grad zu reduzieren (etwa 0,08 g CO2 pro eingespartem Kilogramm)“. Weiter heißt es in dem Bericht: „Gelingt es einem OEM, das Fahrzeuggewicht um 100 kg zu reduzieren, spart er etwa 8,5 g CO2 pro 100 km.“
Als Reaktion auf diese Erkenntnisse setzen Automobilhersteller verstärkt auf Leichtbaulösungen, d.h. sie bauen immer leichtere Pkw und Lkw, um den Kraftstoffverbrauch und die Fahrleistungen zu verbessern. Dabei kann der Einsatz von Leichtmetallen wie Aluminium und Magnesium eine große Hilfe sein. Leichtbau ist aber mehr als die Wahl eines leichteren Werkstoffs, denn schwerere Werkstoffe wie Schmiedestähle, Kobalt-Chrom, Inconel oder Grau- und Sphäroguss (NCI) sind im Fahrzeugbau nach wie vor weit verbreitet.
Hersteller stehen vor der Aufgabe, „schwere“ Metalle so zu konstruieren, dass sie eine gewichtseffiziente und stabile Alternative zu leichteren Metallen darstellen. Dies bedeutet, dass komplexere, endkonturnahe Teile auf der Grundlage komplexerer Konstruktionen gefertigt werden müssen, was bei der Bearbeitung von schwer zerspanbaren ISO-K-Werkstoffen eine Herausforderung darstellt. Außerdem enthalten alle Gusseisenwerkstoffe Siliziumkarbid (SiC), das an der Schneide sehr abrasiv wirkt. Eine weitere Schwierigkeit für die OEMs besteht darin, diese komplexeren Bauteile mit höchster Qualität, hoher Produktivität und niedrigen Stückkosten herzustellen.
Wenn es darum geht, große Stückzahlen zu fertigen und schnell viel Material vom Werkstück abzutragen, ist das Eckfräsen die beste Lösung. Diese einfache, aber flexible Fräsanwendung sorgt für leichtere Schnitte, was wiederum die Werkzeugbelastung minimiert und sicherstellt, dass das Werkstück in der gewünschten Form bleibt. Das Werkzeug erzeugt hierbei gleichzeitig eine Plan- und eine Schulterfläche.
Es ist wichtig, den richtigen Winkel zu wählen, um unerwünschten Versatz zwischen Fräser und Werkstück zu vermeiden. Ein Winkel nahe 90 Grad ist zu bevorzugen, aber je nach Anwendung können auch andere Winkel verwendet werden.
Neues Fräserkonzept
Auf dem Markt gibt es eine Reihe von Wendeschneidplatten zum Eckfräsen, die für Fräswinkel nahe 90 Grad ausgelegt sind. Normalerweise haben diese Wendeschneidplatten acht Schneidkanten – vier auf der Vorder- und vier auf der Rückseite, um Ecke und Fläche gleichzeitig zu bearbeiten – und für bestimmte Anwendungen nur sechs. Sandvik Coromant war jedoch überzeugt, dass ein neues Eckfräskonzept möglich war. Ein Konzept, das eine höhere Produktivität, verbesserte Werkzeugstandzeiten und wirtschaftliche Vorteile bietet.
Als Antwort auf die genannten Herausforderungen hat Sandvik Coromant den CoroMill® MF80 entwickelt. Dessen Wendeschneidplatten sind speziell für Fräsanwendungen in der Automobilindustrie in ISO-K- und ISO-P-Werkstoffen konzipiert und verfügen über acht Schneidkanten, Spanbrecher und eine optimierte Mikrogeometrie. Die Werkzeuge eignen sich besonders für dünnwandige Bauteile und Maschinenkonfigurationen mit eingeschränkter Stabilität. Die geneigte Schneidkante sorgt für einen gleichmäßigen Schnitt und geringe Schnittkräfte. Dies führt zu erhöhter Sicherheit und Spanabfuhr sowie durch eine Wiper-Schneide zu einer besseren Oberflächengüte.
Der CoroMill MF80 ist kein völlig neuer Fräser, sondern basiert auf einer vergleichbaren Technologieplattform wie der CoroMill 345. Das neue Fräserkonzept bietet einen um 40 Prozent leichteren Fräserkörper mit Zwischenlagenschutz und eine hohe Anzahl an Wendeschneidplatten für eine sichere und stabile Bearbeitung, selbst bei vibrationsanfälligen Auskragbearbeitungen.
Beim Eck- und Planfräsen werden in der Regel Fräswerkzeuge mit einem Einstellwinkel von nahezu 90 Grad bevorzugt, da sie radiale Schnittkräfte erzeugen und vor allem mehr Energie vom Werkstück ableiten. Dies ist vor allem bei der Bearbeitung dünnwandiger oder endkonturnaher Bauteile von Vorteil. Der CoroMill MF80 ermöglicht einen Einstellwinkel von 89,5 Grad, wodurch der Mehrschneidenfräser während der Bearbeitung noch näher an der Spannvorrichtung betrieben werden kann.
Ein Einstellwinkel von fast 90 Grad reduziert zusätzlich die Axialkräfte und verbessert die Fräsbearbeitung von dünnwandigen Bauteilen und bei instabilen Aufspannungen – ohne Vibrationen und Rattern. Die wichtigsten Vorteile sind eine verbesserte Präzision und Maschinenauslastung, aber auch längere Werkzeugstandzeiten mit weniger Ausschuss.
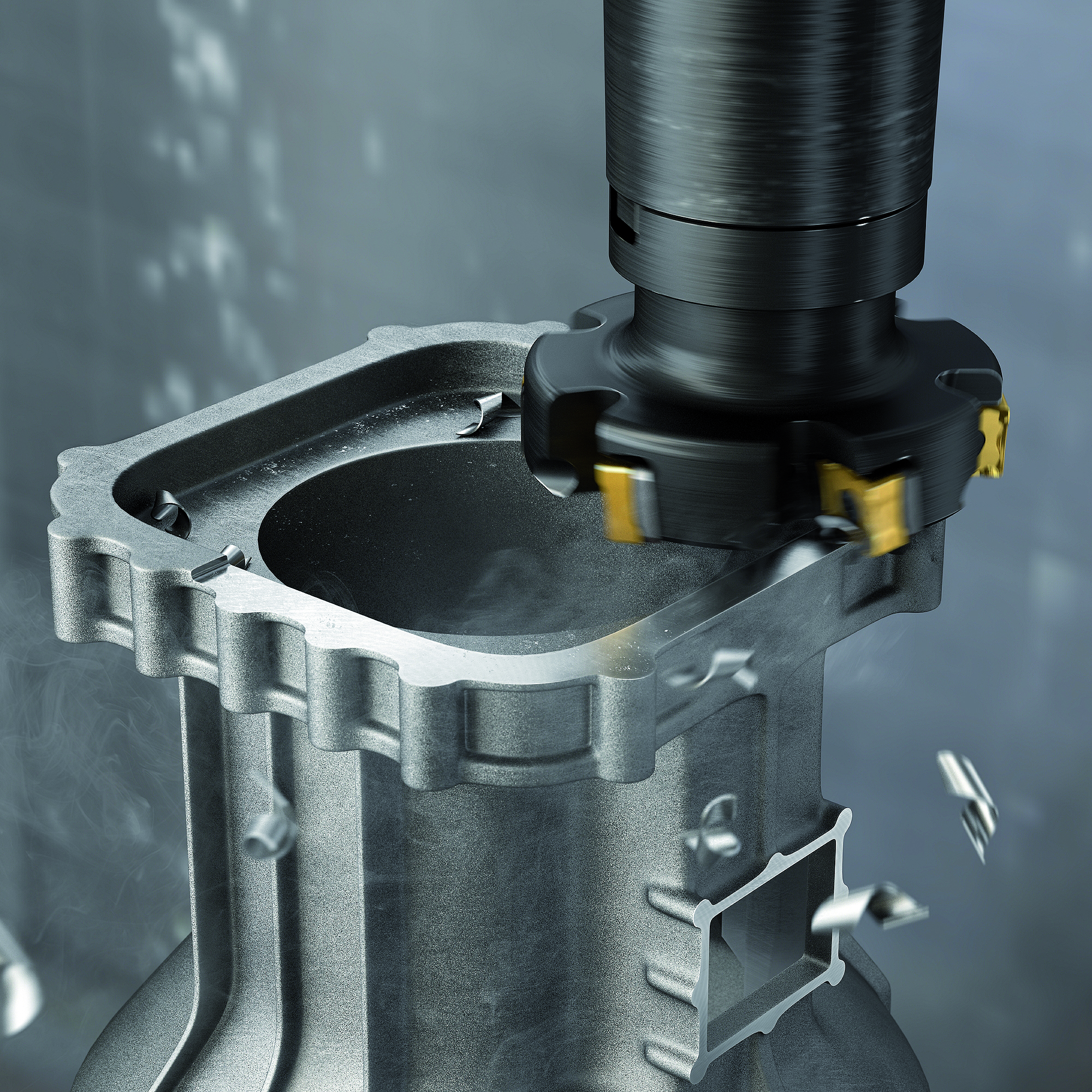
Der CoroMill® MF80 von Sandvik Coromant wurde für das Fräsen von ISO-K- und ISO-P-Werkstoffen in der Automobilindustrie entwickelt.
Überzeugende Leistungstests
In einem Anwendungsfall wurde der CoroMill MF80 beim Schruppfräsen von Pumpen- und Ventilkomponenten aus einem ISO-P-Stahl (DIN 1.0619) im Vergleich zu einer Wettbewerbslösung getestet. Die Fräser arbeiteten mit nahezu identischen Schnittdaten (Spindeldrehzahl, n = 500 U/min; Schnittgeschwindigkeit, vc = 125 m/mm; radiale Schnitttiefe, ae = 15/50 mm; axiale Schnitttiefe, ap = 5 mm; Vorschub pro Zahn, fz = 0,15 mm), jedoch mit unterschiedlichem Vorschub pro Minute, vf: Der Fräser des Wettbewerbers wurde mit 375 mm/min betrieben, der CoroMill MF80 mit 600 mm/min.
Das Ergebnis: Der CoroMill MF80 erzielte eine Produktivitätssteigerung von 60 Prozent. Der Fräser des Wettbewerbers produzierte neun Teile, der CoroMill MF80 15. Hinsichtlich der Werkzeugstandzeit waren am CoroMill MF80 nach einer Bearbeitungszeit von 40 Minuten lediglich Absplitterungen zu erkennen, so dass das Werkzeug eine um 67 Prozent höhere Standzeit aufwies. Der Hauptvorteil für den Kunden bestand darin, dass aufgrund der durch Zwischenlagen geschützten Plattensitze und der hohen Anzahl an Wendeschneidplatten die Kosten pro Werkstück bei Schrupp- und Eckfräsanwendungen gesenkt werden konnten.
In einem weiteren Test wurden der CoroMill MF80 und eine Wettbewerbslösung zum Schruppen eines ISO-K-Werkstücks verwendet. Es handelte sich um Träger und Stützen aus ISO-K-Gusseisen mit Kugelgraphit (GJS400/K3.1.C.UT). Auch hier wurden beide Werkzeuge mit den gleichen Schnittdaten gefahren, einschließlich einer radialen Schnitttiefe von 20-80 mm und einer axialen Schnitttiefe von 2-3 mm. Beide Fräser wurden mit einer Spindeldrehzahl von 1000 U/min, einer Schnittgeschwindigkeit von 250 m/min und einem Vorschub von 1200 mm/min betrieben. Der Vorschub pro Zahn unterschied sich nur geringfügig: 0,24 mm beim Wettbewerbsfräser und 0,3 mm beim CoroMill MF80.
Das Testergebnis zeigte, dass der Kunde mit dem Fräser von Sandvik Coromant eine um 54 Prozent höhere Werkzeugstandzeit erzielte. Während der Fräser des Wettbewerbers in 55 Minuten zehn Bauteile fertigte, bevor er Verschleißerscheinungen zeigte, lief der CoroMill MF80 82 Minuten und fertigte in dieser Zeit 15 Bauteile.
Fazit
Der CoroMill MF80 kann für OEMs bei Leichtbauanwendungen von großem Nutzen sein, da er bei der Bearbeitung von schwereren ISO-K-Werkstoffen wie Sphäroguss (NCI), Inconel oder Grauguss, Schmiedestahl und Kobalt-Chrom längere Standzeiten und eine höhere Produktivität bietet. Und diese Vorteile können entscheidend sein, wenn es darum geht, den Automobilherstellern zu helfen, Fahrzeuge bauen, die den strengen CO2-Emissionsvorschriften entsprechen, und gleichzeitig die Bauteilkosten zu senken.
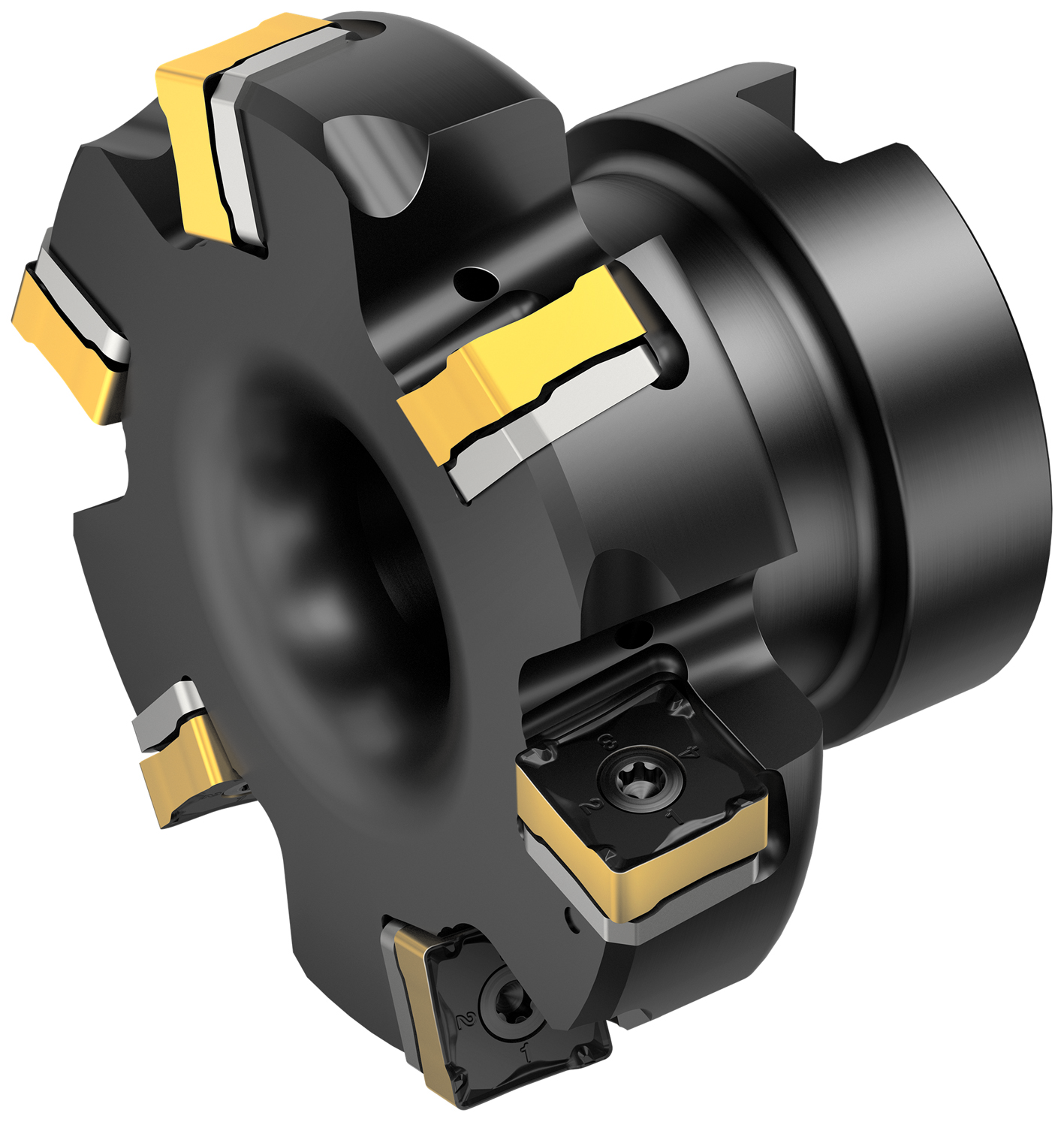
Der CoroMill MF80 kann für OEMs bei Leichtbauanwendungen von großem Nutzen sein.
