Quality through roll testing
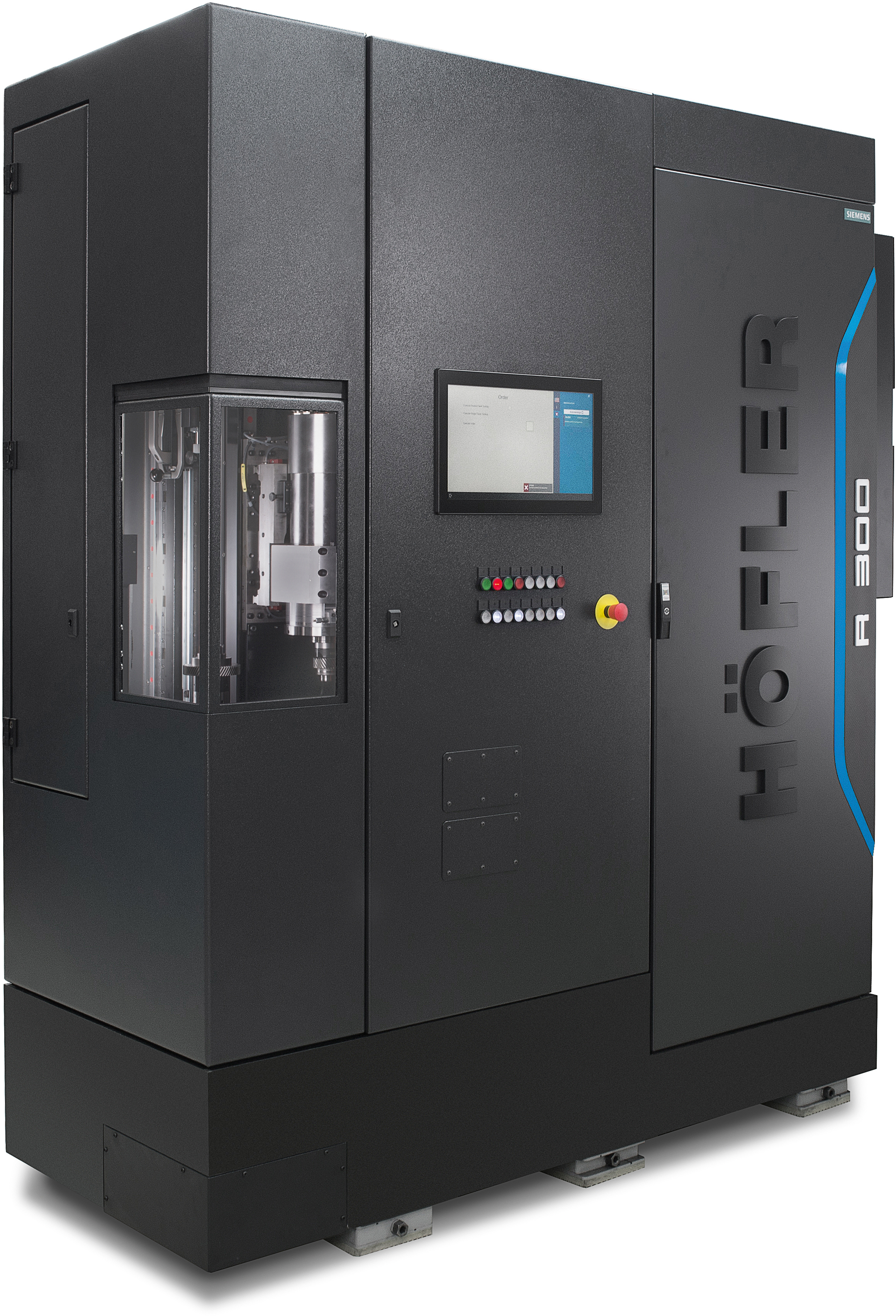
The different roll testing methods have various strengths and weaknesses. But they all have one thing in common: they are indispensable for quality control!
For decades, roll testing has been used for quality inspection of gears in mass production. Compared to other measurement and test methods, roll testing provides important information in a very short time about the function of a gear, which is ultimately the determining quality criterion. In roll testing, however, the functionally critical geometrical production deviations can only be inferred indirectly. But this knowledge is relevant as a basis for determining corrections for the production process and thereby achieving the quality objective. Three-dimensional (3D) coordinate measurement technology bridges this gap. This is clear evidence that roll testing and 3D coordinate measurement technology are indeed complementary, rather than competing, measurement and test methods.
Overview of the Test Methods
Roll testing of cylindrical gears comprises five different roll testing methods: the double flank test (DFT), helix test (HXT), and single flank test (SFT), as well as structure-borne noise test (SBNT), and torsional acceleration (TAT). Each of these five roll test methods differs in the test rotation speed, and thus also in the test duration. Moreover, each test method is meaningful in a different way in terms of its correlation with the geometrical and functional characteristics of a gear (see Figure 2 for the various evaluation criteria used in the roll test methods). In general terms, it can be stated that the test methods in double flank contact are suitable only for testing geometrical characteristics, whereas the test methods in single-flank contact also provide information on the functional characteristics, such as rotational transmission precision and noise excitation.
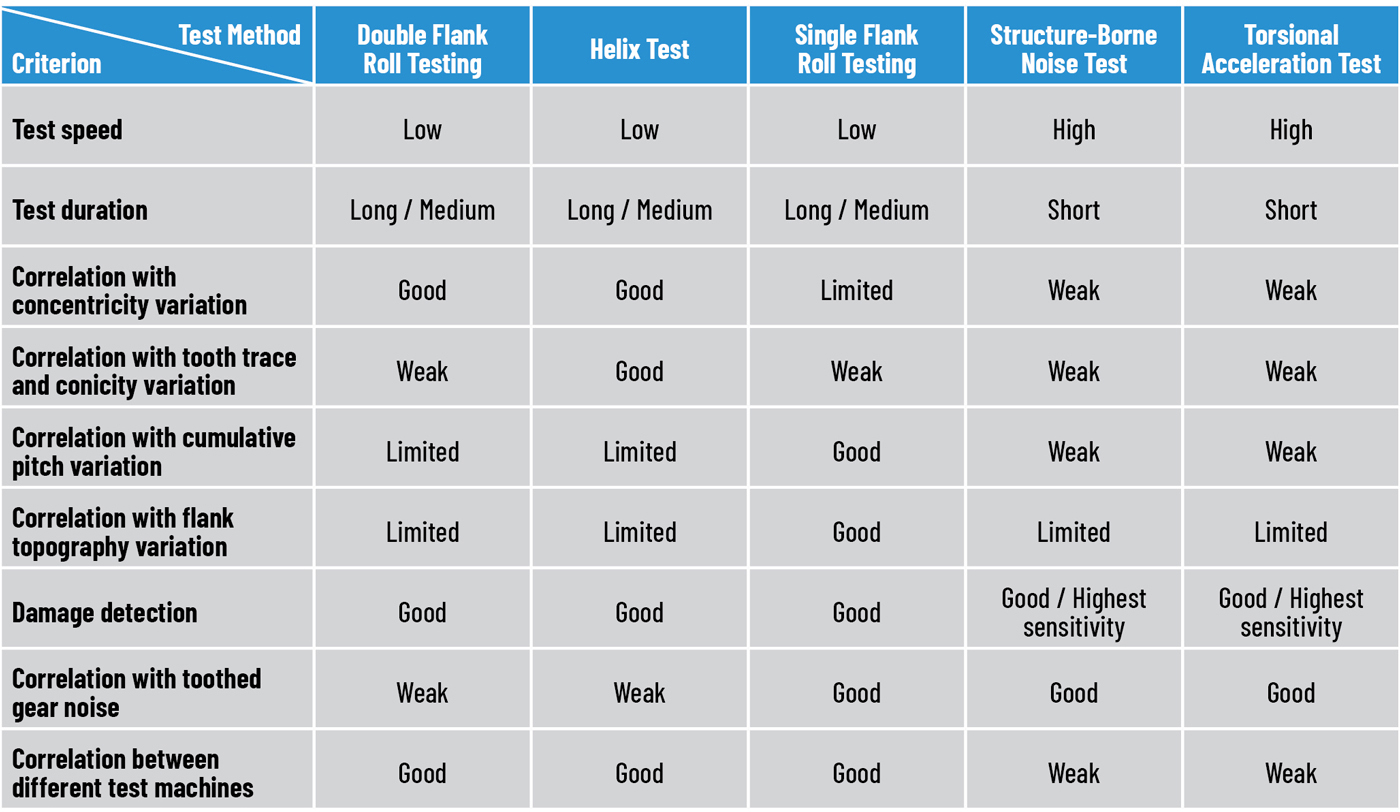
Fig. 2: Characteristics of the five roll test methods.
Particularity of the Helix Test
In the DFT and the HXT, the rolling motion of the workpiece and master gear takes place in double flank contact, and the center distance, which varies during the rolling motion, is measured and analyzed as the main measurement variable. The DIN standard has corresponding parameters for evaluating the result of the DFT. Particular to the HXT is the fact that the master gear is gimbaled, and not only the varying center distance but also the spherical motion of the HXT master gear is measured during the test (see Figure 1). When the measured values are evaluated, they are divided into the helix angle and conicity variation portions. In real-world applications, the DFT is traditionally used in the process chain of shaved and hardened cylindrical gears to check concentricity variations and identify damage introduced into the gear prior to hardening. The HXT is used primarily to monitor and check heat treatment distortions.
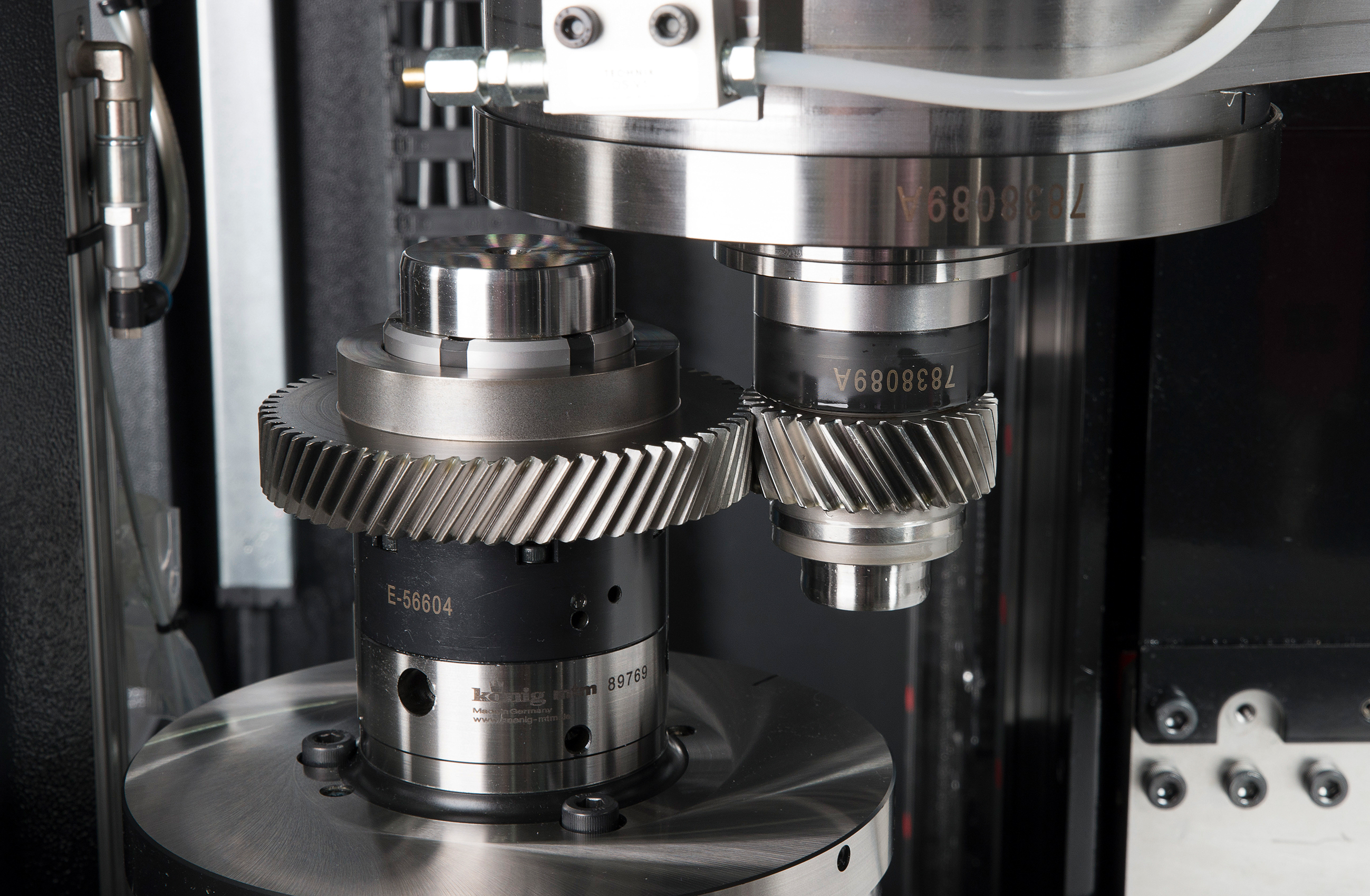
Fig. 1: Helix test.
Single Flank Test Methods: SFT, SBNT, and TAT
In today’s passenger car transmissions, however, ground gears are increasingly being used. Because there is typically no damage from soft cutting remaining after gear grinding, the focus of quality control is on the running performance and noise behavior of the gears. In this case, the single flank test methods (SFT, SBNT, and TAT) are used. The quasi-static SFT measures the gear ratio fluctuation – also known as transmission error – resulting from the gear geometry. Based on the transmission error, averaged rotation patterns and the associated order spectra are calculated. The order spectrum is used to identify individual orders that may subsequently lead to noise anomalies in the transmission. The structure-borne noise and torsional acceleration measurement are dynamic test methods. Although the mounting position during the test is identical to that used in the SFT, the test rotation speed is significantly higher. As with the SFT, the averaged rotation patterns and associated order spectra are calculated from the measured signals of the SBNT and TAT, and are used as a basis for evaluating the noise behavior.
Conclusion: Each Roll Test Has Its Strengths
The advantage of the SFT is that there are only minimal dynamic effects in the measuring result due to the quasi-static nature of the method; consequently, the reproducibility of the absolute values of characteristic values is very good on the same test machines, as well as on different test machines. The advantage of the SBNT and the TAT, by contrast, is the short test duration. In addition, the measurement signal is closer to the noise than the transmission error. In particular, this allows higher orders in the noise excitation spectrum to be identified more easily than in the SFT, although the reproducibility of the absolute values is poorer. The ideal position to be in is to have flexible access to all five known roll test methods – preferably combined on a machine such as the R 300.