Tiefe Kavitäten mit dem richtigen Werkzeug
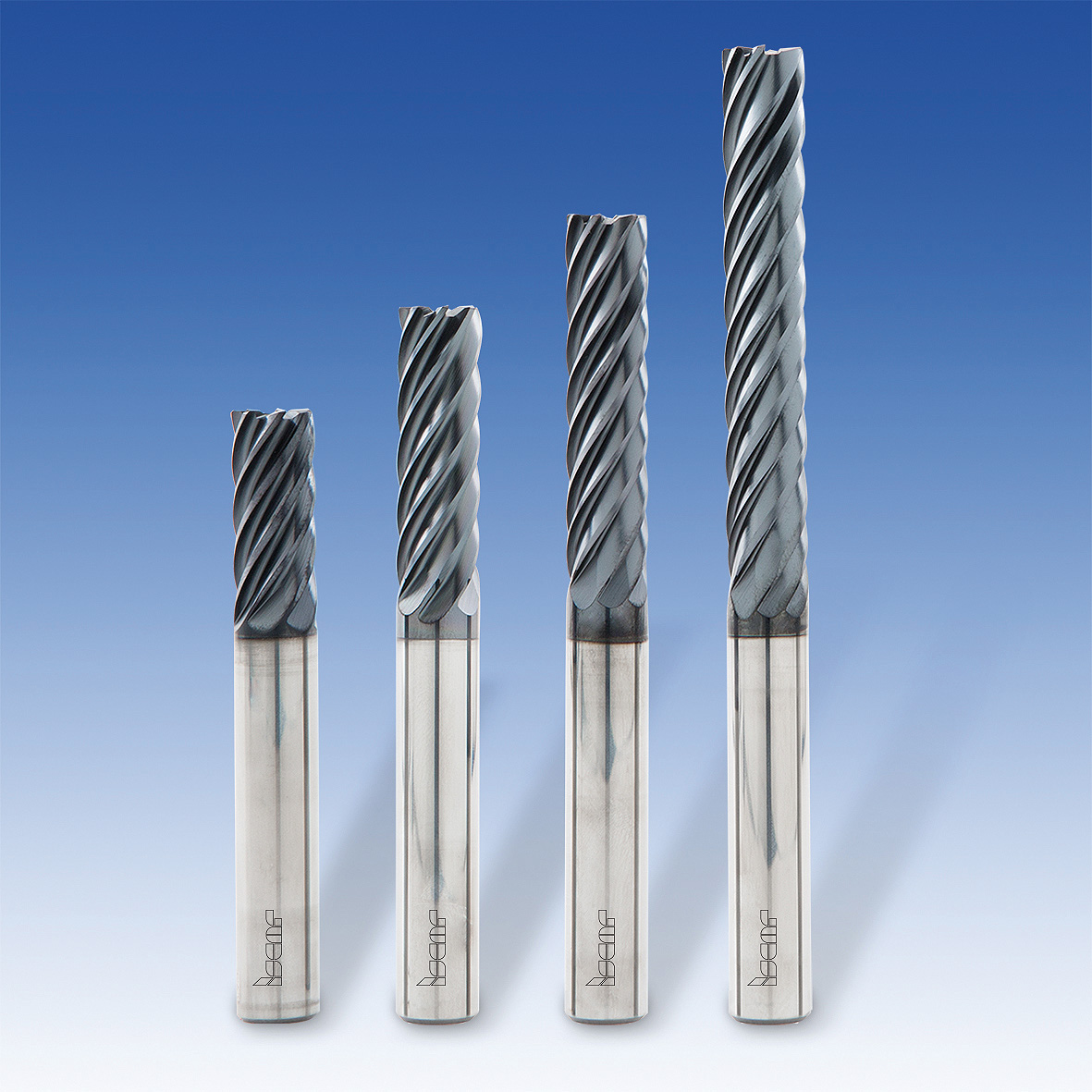
Hochgeschwindigkeitsbearbeitungen wurden erst durch die Entwicklung von Werkzeugmaschinen mit hohen Dreh- und Lineargeschwindigkeiten möglich. Heute sind sie aus der Zerspanung nicht mehr wegzudenken. Bearbeitungsmethoden wie das Schälfräsen kombinieren die Vorteile großer Schnitttiefen (bis zu 5xD) mit einer geringen Schnittbreite (bis zu 0,2xD). Erforderlich dafür ist das geeignete Werkzeug.
Der Erfolg des Schälfräsens beruht auf mehreren Vorzügen. Zum einen reduziert die geringere Schnittbreite die Wärmebelastung an der Schneidkante. Im Vergleich zu herkömmlichen Fräsmethoden kann der Anwender damit Schnittgeschwindigkeit und Vorschub deutlich erhöhen. Zum anderen verringert sich die radiale Schnittkraft, die für Biegekräfte und Vibrationen verantwortlich ist. Dadurch besticht die Fräsmethode mit einer hohen Prozessstabilität und großen Schnitttiefen.
Ein solches Verfahren steigert die Produktivität. Es begünstigt beispielsweise einen gleichmäßigen Verschleiß entlang der gesamten Schneidkante, wodurch sich die Standzeit spürbar erhöht. Aufgrund der geringen Eingriffsbreite kann der Anwender einen hohen Vorschub fahren, um die optimale Spandicke zu erhalten.
Das Schälfräsen kommt beim Erzeugen tiefer Schultern und Kavitäten oder beim Restfräsen zum Einsatz. Bei diesem Prozess werden verschiedene schwer zugängliche Bereiche wie Hohlraumecken mit einem kleineren Werkzeug ausgearbeitet.
Geringer Verschleiß durch trochoidales Fräsen
Fortschritte in der CNC- und CAM-Technik führten zu einer weiteren Zerspaninnovation: Beim trochoidalen Fräsen ist das Werkzeug schmaler als der eigentliche Schnitt. Es bewegt sich entlang einer spiralförmigen Bahn anstelle einer linearen Vorschubbewegung und trägt aufgrund der geringen Eingriffsbreite vergleichsweise dünne Späne ab. Dadurch wirken kleinere Zerspanungskräfte auf das Werkzeug, die sich auf die gesamte Schneidenlänge verteilen. Das spart Zeit bei der Bearbeitung und minimiert den Verschleiß.
Diese Fräsvariante ist fester Bestandteil der Bearbeitung von harten und schwer zerspanbaren Werkstoffen, insbesondere Titan und hoch hitzebeständige Superlegierungen. Durch die deutlich geringere Werkzeugbelastung eignet sich das Verfahren auch in der Kleinteilebearbeitung und verbessert die Fräsleistung unter instabilen Bedingungen – beispielsweise an labilen oder dünnwandigen Werkstücken oder Werkstückaufspannungen.
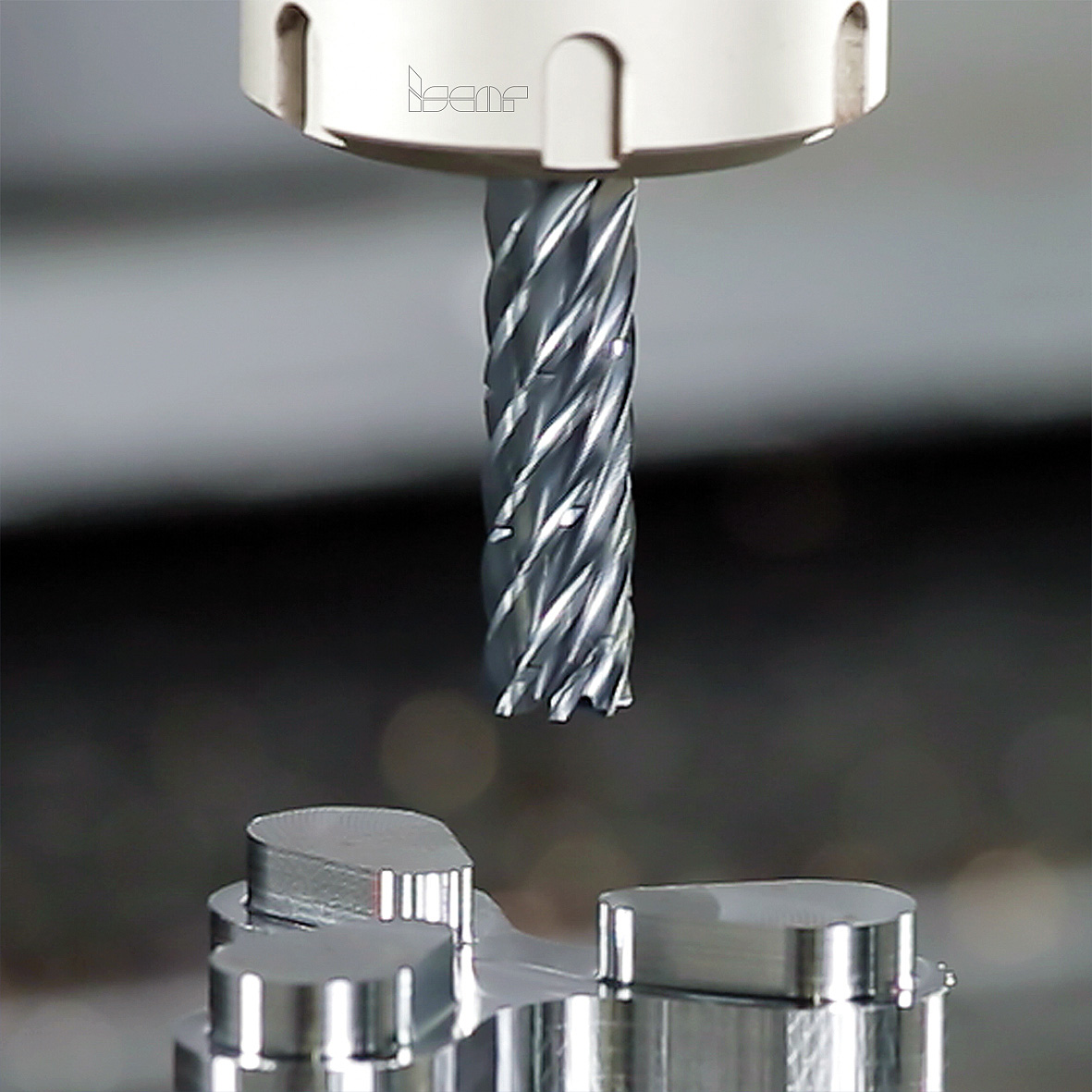
Eine Schneidkante mit Spanbrecher verbessert die Spanabfuhr und sorgt für eine sehr hohe Oberflächengüte.
Das Werkzeug macht den Unterschied
Die größten Herausforderungen beim Trochoidalfräsen sind die Steuerung der Werkzeugmaschinen und die adäquate Bahnprogrammierung. Oft übersehen wird dabei allerdings eine weitere wesentliche Komponente: Ohne das richtige Werkzeug führen alle Bemühungen, die genannten Vorzüge des trochoidalen Fräsens vollumfänglich auszuspielen, nicht zu den gewünschten Ergebnissen.
Um den spezifischen Anforderungen des Trochoidalfräsens Rechnung zu tragen, gilt es für Werkzeughersteller mehrere Faktoren bei der Produktentwicklung berücksichtigen: Um den Trochoidalfräser für die Hochgeschwindigkeitsbearbeitung auszulegen, müssen unter anderem die Schnittparameter für eine präzise Bearbeitung, die Wuchtgüte sowie die Sicherheit für einen Betrieb mit hohen Drehzahlen stimmen.
Tiefe Frässchnitte erfordern Werkzeuge mit hohen Auskragungen. Bei der Bearbeitung können diese vibrieren und damit das dynamische Verhalten des Fräsers beeinflussen. Dieses ist jedoch für die Anwendungsstabilität entscheidend. Bei geringer Schnittbreite greift jeweils nur ein Zahn in das Material des Werkstücks ein. Für einen stabilen Prozess ist hier eine optimierte Kontaktfläche sowie der ideale Schneidkantenwinkel gefragt. Im Fräser ist für eine effektive Abfuhr der schmalen Späne hingegen keine große Spannut erforderlich.
All diese Kriterien erfüllen mehrschneidige Vollhartmetall (VHM)- oder modulare Fräser mit austauschbaren VHM-Köpfen, wie sie in der neuesten ISCAR-Produktlinie zu finden sind. Die Werkzeuge zeichnen sich durch drei entscheidende Merkmale aus: Erstens sorgen unterschiedliche Spiralwinkel und die ungleiche Zahnteilung für einen vibrationsarmen und stabilen Lauf während der Arbeit mit langen Werkzeugauskragungen. Zweitens erlaubt die speziell geformte Spannut einen größeren Kerndurchmesser, der die Werkzeugstärke beim dynamischen Fräsen weiter erhöht. Drittens lassen die Fräser genügend Platz am Werkstück für eine reibungslose Spanabfuhr.
Entsprechend arbeiten die ISCAR-Vollhartmetallfräser präzise und mit maximaler Zerspanungsleistung bei gängigen Werkstoffen. Sie sind mit Durchmessern von zwei bis 25 Millimetern erhältlich.
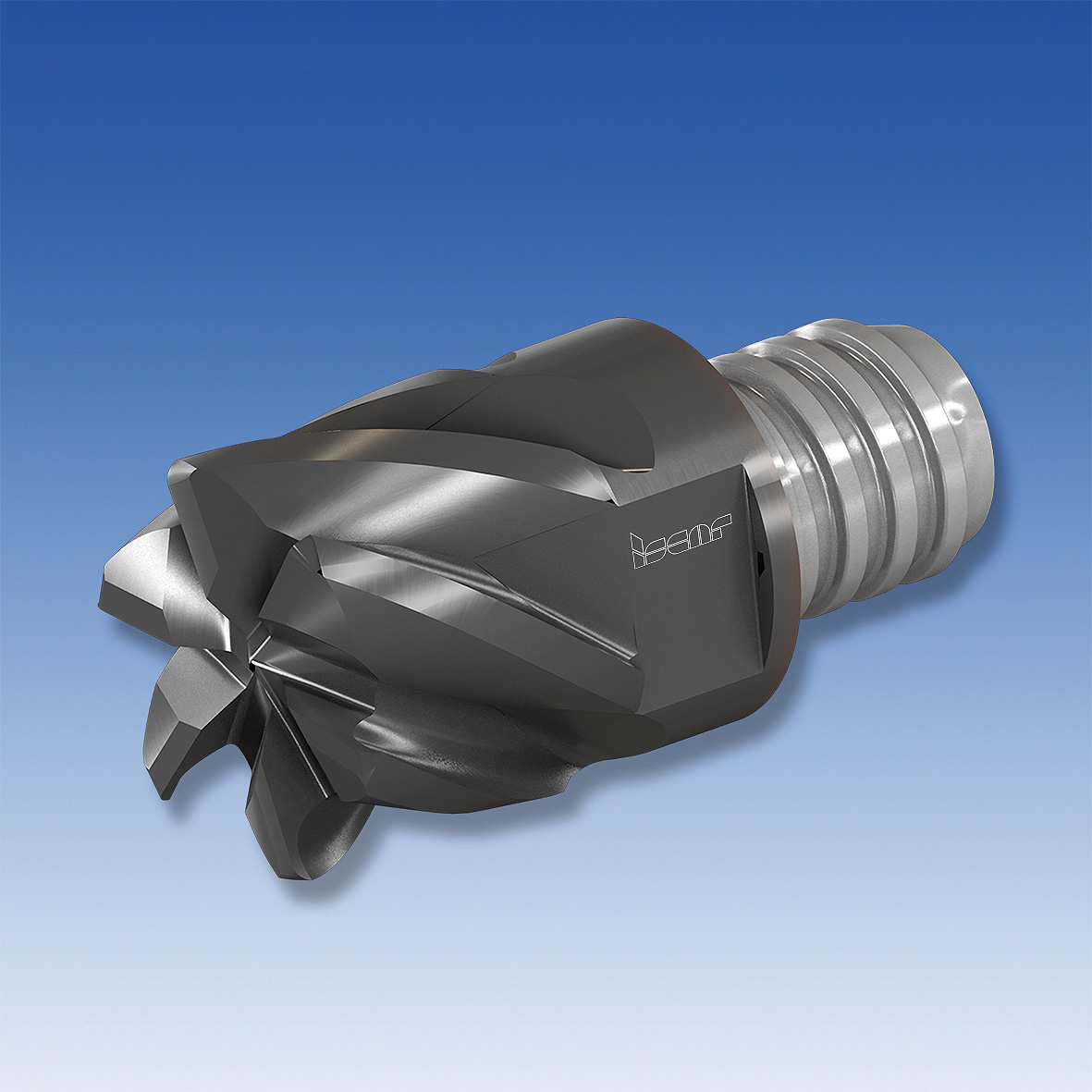
ISCARs auswechselbarer MULTI-MASTER-Fräskopf ist speziell für trochoidales Fräsen von schwer zerspanbaren Titanlegierungen entwickelt worden.
Fräser für alle Einsatzgebiete
Die CHATTERFREE EC-E7/H7-CF-VHM-Schaftfräser aus der PVD-beschichteten Feinstkornsorte IC902 bieten sieben Schneiden, unterschiedliche Eckenradien und sind in den Größen 2xD, 3xD, 4xD und 6xD erhältlich.
Die siebenschneidige Schaftfräserausführung ECP-H7-CF überzeugt durch seine Schneidengeometrie mit Spanbrecher. Diese verbessert die Spanabfuhr bei tiefen Taschen und Kavitäten. Der Spanbrecher stellt zudem eine hohe Oberflächengüte sicher.
Bei den ECK-H7/9-CFR, Ti-TURBO handelt es sich um sieben- und neunschneidige Vollhartmetallfräser, die Iscar speziell für die Hochgeschwindigkeitsbearbeitung von Titanlegierungen mit Bearbeitungslängen von circa 2xD entwickelt hat. Dank der Vibrationsdämpfung und optimierter Schneidengeometrie zeigen diese Werkzeuge beispielsweise exzellente Ergebnisse beim Fräsen von Flugzeugkomponenten wie etwa Titan-Blisks.
Speziell für das trochoidale Fräsen flacher Nuten oder Ecken von Titanbauteilen hat ISCAR die sechsschneidigen, auswechselbaren MULTI-MASTER-Fräsköpfe entwickelt. Mit den robusten Fräsköpfen kann der Anwender schwer zerspanbare Titansorten wie Ti-10V-2Fe-3Al und Ti-5Al-5Mo-5V-3Cr effizient bearbeiten.
Und noch eine oft vernachlässigte Komponente wirkt sich maßgeblich auf den Erfolg des trochoidalen Fräsens aus: der Werkzeughalter. Die Bearbeitungspraxis zeigt, dass Fräser, die in Hydraulik-, Kraftspann- oder Schrumpffuttern zum Einsatz kommen, die besten Ergebnisse liefern.
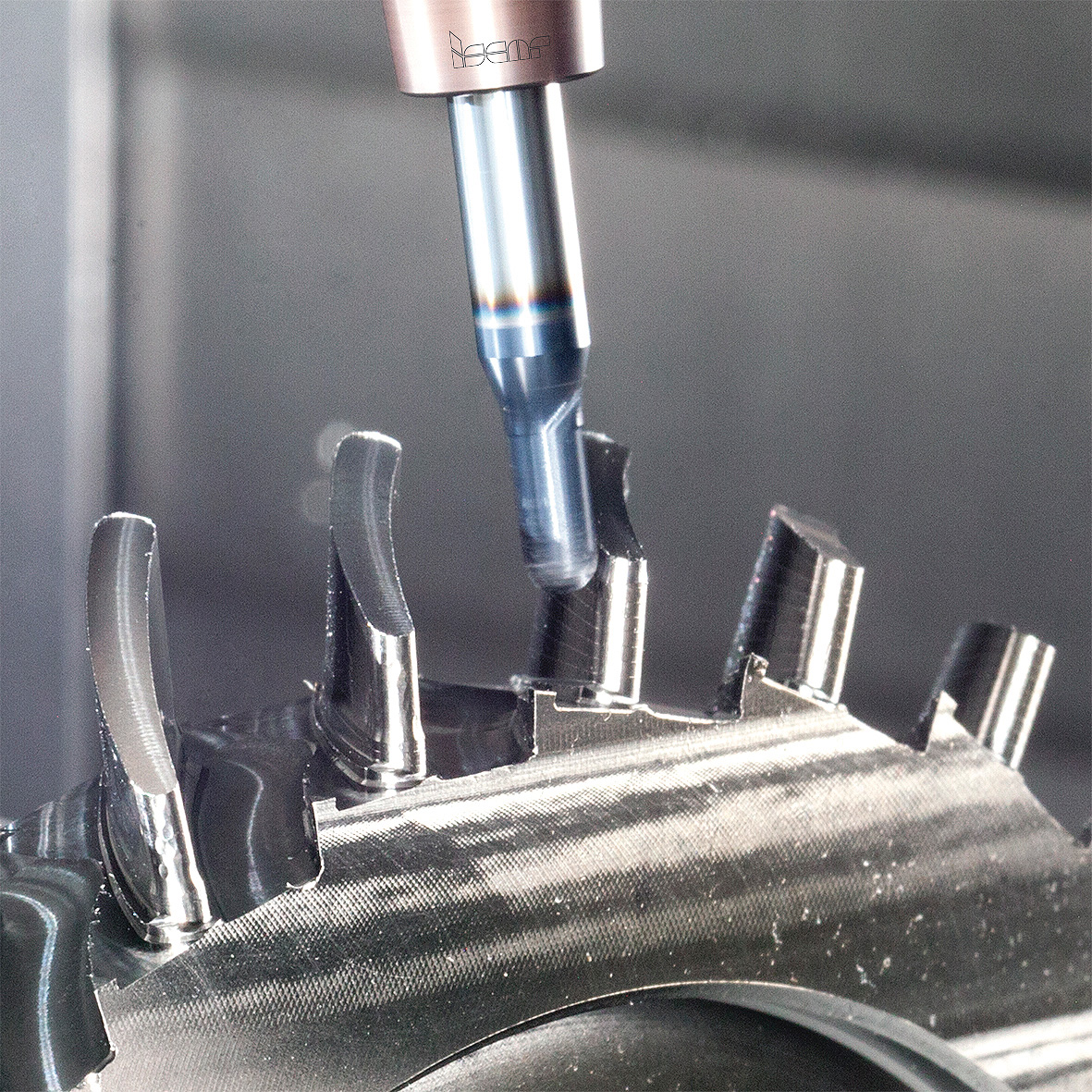
Für sehr gute Ergebnisse beim trochoidalen Fräsen eines Blisk-Schaufelblatts kann der mehrschneidigen VHM-Schaftfräser in einem Schrumpffutter gespannt werden.
