Broaching reduces production time and cuts costs!
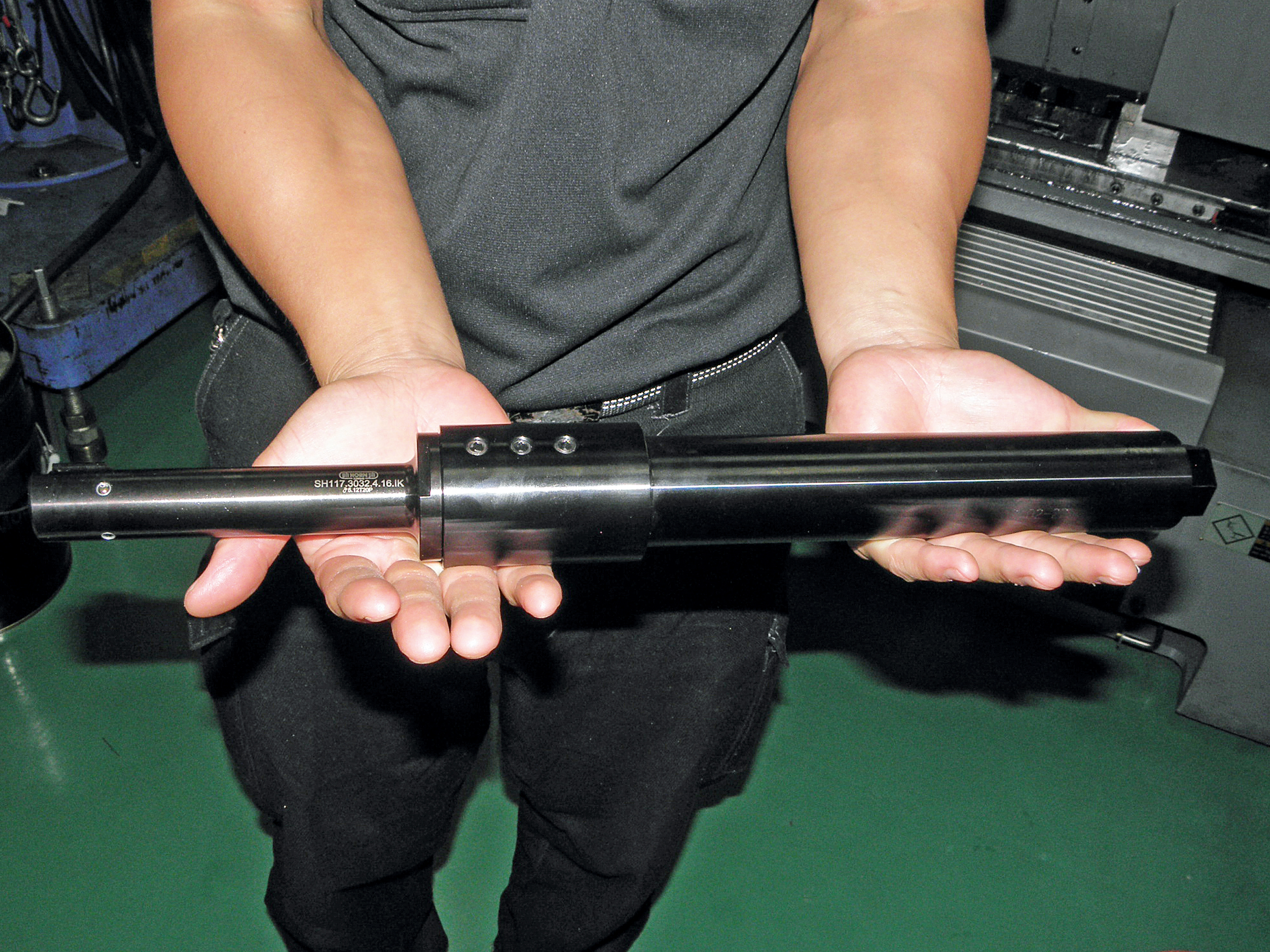
Broaching keyways in a machining centre saves production time and increases the accuracy of the workpieces. At the same time, slot broaching shortens throughput times, saves additional manufacturing processes and machines, and reduces tool costs. This is confirmed by a Japanese gear manufacturer who has switched the machining of internal keyways in gears to grooving tools from Paul Horn GmbH.
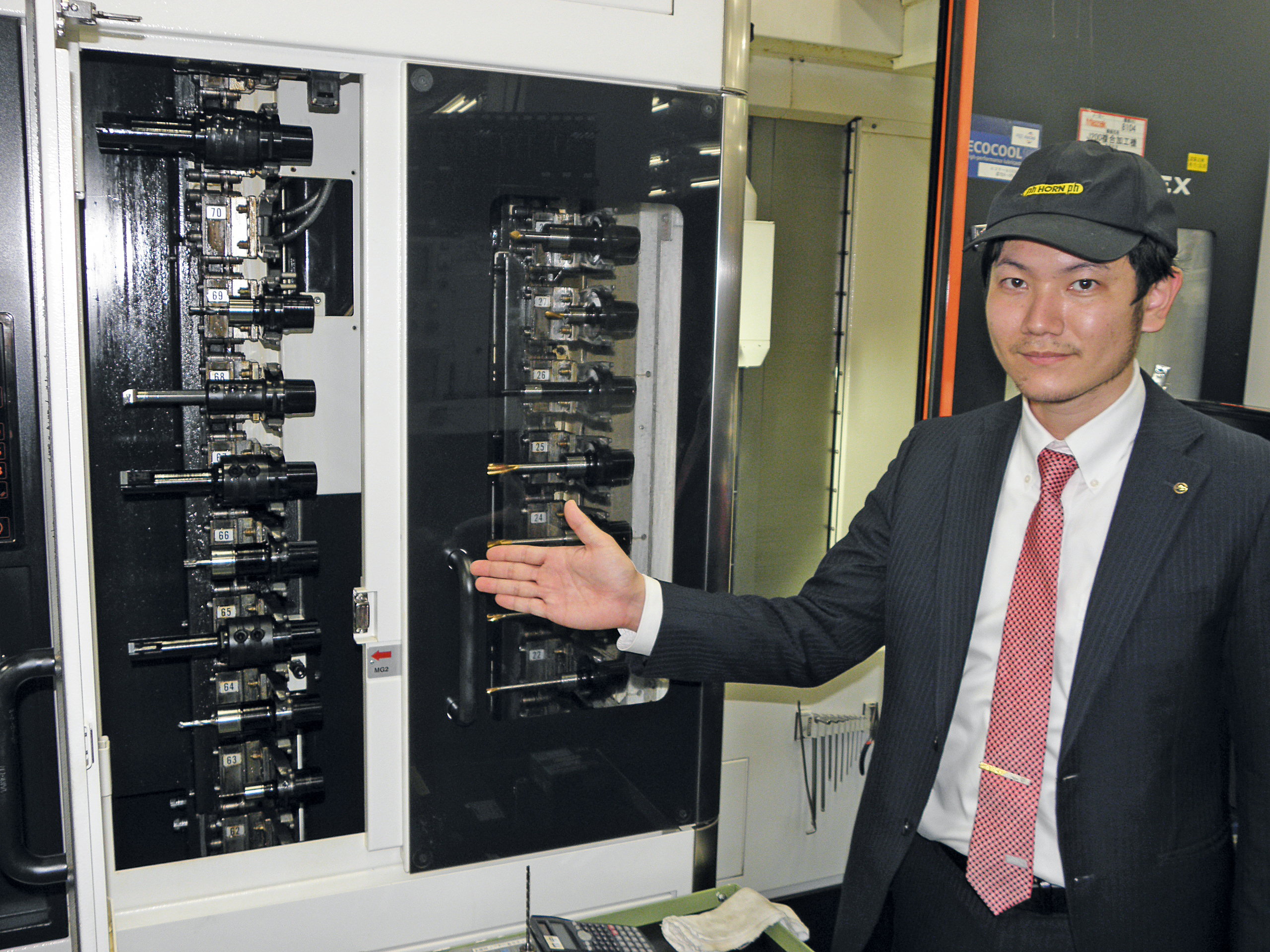
The Horn consultant T. Mori from Izushi responsible for Kohara shows the tool magazine in a machining centre filled with Horn broaching tools.
KHK Kohara Gear Industry Co. Ltd in Saitama (Japan), near Tokyo, is a user of Horn tool systems. Founded in 1935, the manufacturer of stationary gears produces products worth around 33 million euros annually. About 30 percent of these are custom-made products and 20 percent of the products are exported. The company is aiming for growth in the export market. KHL Kohara’s gears are straight, helical and spiral. There are external gears as well as internal gears. In addition, the KHK Kohara programme includes racks and worm gears. Steels, mild and stainless, titanium, aluminium and other metals are machined, as are fibre composites and Bakelite. As in Europe, the number of variants is increasing in Japan. This inevitably leads to ever smaller production batches. The production plants are confronted with major issues, not only because more sizes have to be produced in ever shorter timescales, but also due to set-up times as well as organisational and logistical effort lengthening procedures and driving up costs.
In the case of KHK Kohara, the entire process chain of the company was even called into question. After all, it is hardly worthwhile to produce expensive broaches for keyway machining when batch quantities are small and to set up a separate broaching process for one or a few internal grooves. In Kohara’s series production, there are now numerous batch sizes of fewer than 100. In some cases, quantities of only 10 to 30 are produced on the machining centres. With such small batch sizes, the grooves were often spark eroded. However, this costs time and money and leaves rough surfaces that wear out sooner than had they been machined.
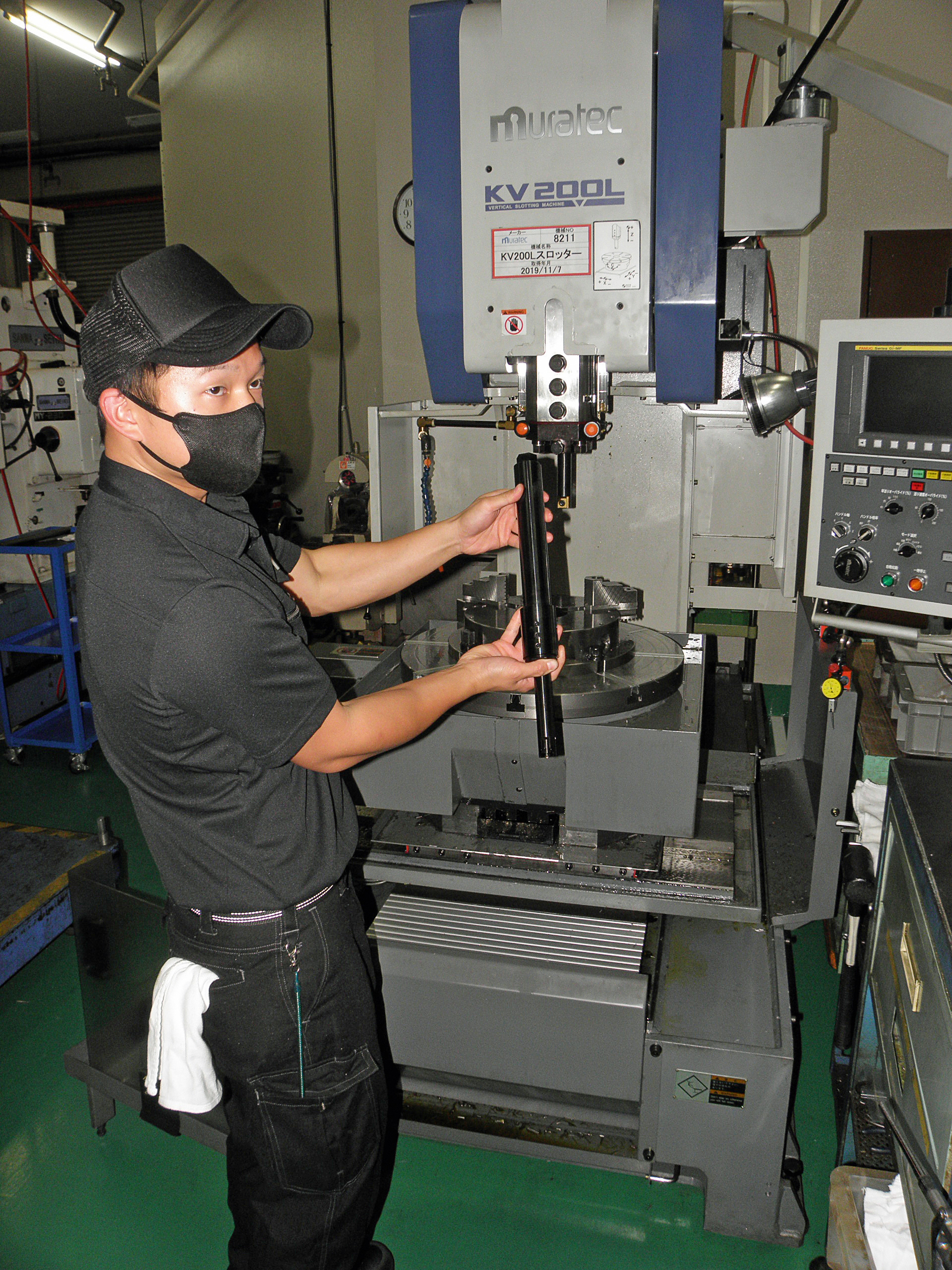
Horn’s broaching tools are used in special broaching machines as well as in machining centres.
That is why KHK Kohara is now moving towards installing more and more large machining centres instead of process-oriented production equipment. Process-oriented, multi-stage production is being replaced by continuous, complete machining on one platform, including broaching of the keyways. For this purpose, the tool magazines of the machining centres have been equipped with Horn broaching tools for all widths across flats of the respective product family. Now these components can be completely produced on the machining centres, including broaching, without subsequent keyway machining. This enables much more flexible production, especially of smaller batch sizes. In this way, the company was able to significantly increase its ability to deliver quickly without accumulating large inventories. At the same time, production throughput time was reduced by nearly 60 percent.
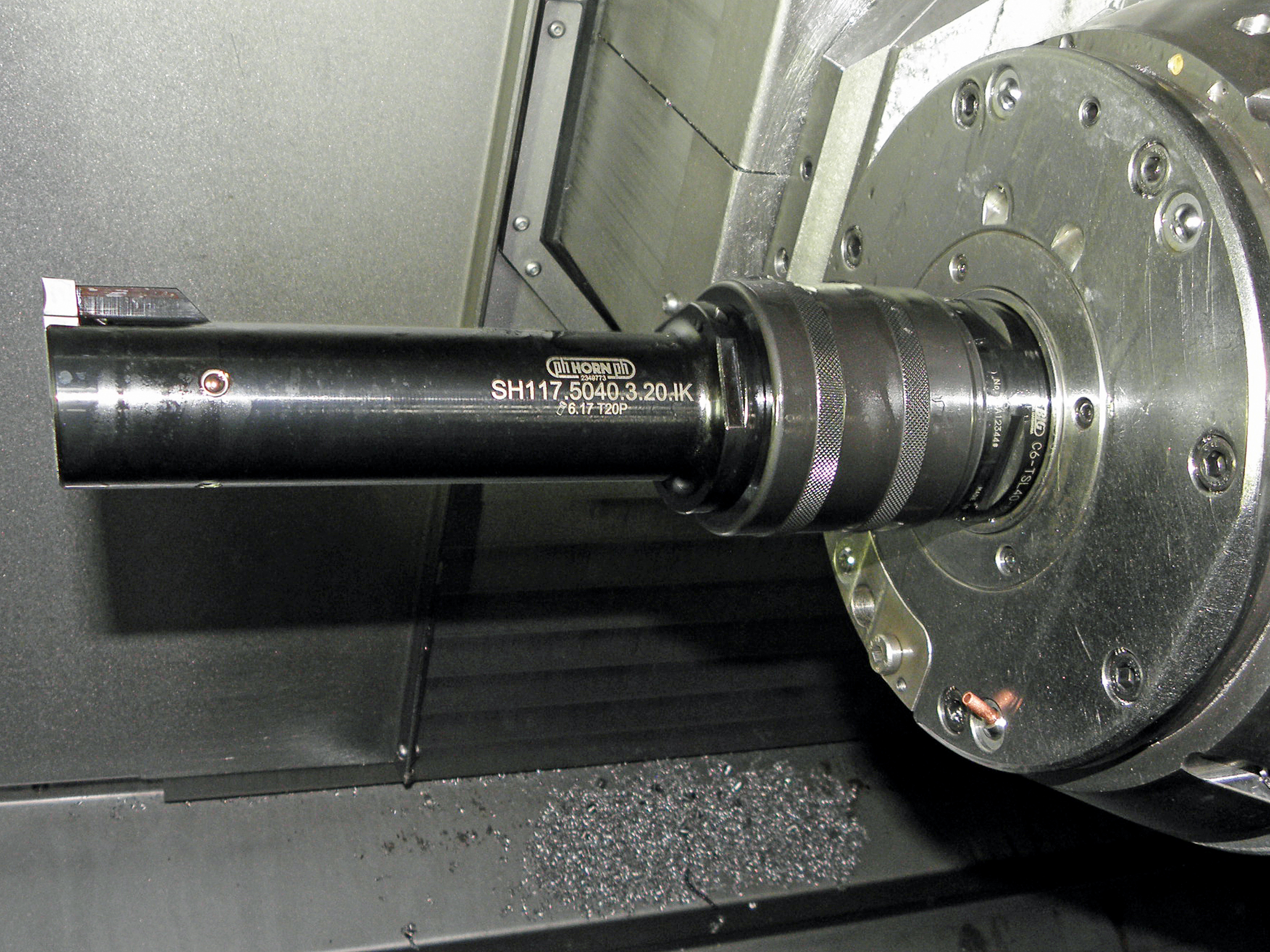
The broaching tool is used in the spindle of a machining centre.
The groove production process itself is also quicker and easier. Set-up times are eliminated after the tool has been set in the magazine. Costly test workpieces and time-consuming adjustments on the broaching machines are also no longer necessary. The production time for each individual groove has been significantly shortened. Machine operator T. Hayashi at KHK reports: “Previously, we needed 9 minutes and 30 seconds of machine time to create a keyway. With the Horn broaching tools, we now only need 4 minutes and 8 seconds for the same keyway. That’s almost a 60 per cent time saving per workpiece.”
“For our customers, accuracy in the bore is very important,” says operations manager Y. Niikura, who continues: “Here we work down to tens of microns when turning and single-figure microns when grinding. Bore accuracy is H7 or H6, depending on customer requirements.” These accuracies have resulted in investment in grooving tools from Horn. Traditional machining with broaches always resulted in an uneven groove base and wedge-shaped flanks, especially in long grooves. Again and again, the processes had to be laboriously adjusted and aligned, which took a lot of time. “We were able to integrate the Horn broaching tools into the new machining centres and noticeably increase our productivity. We were particularly impressed by the rigidity of the tools. There is no longer a wedge shape and all dimensions are within tolerance, whether groove width or groove depth. The groove base is smooth,” explains T. Hayashi.
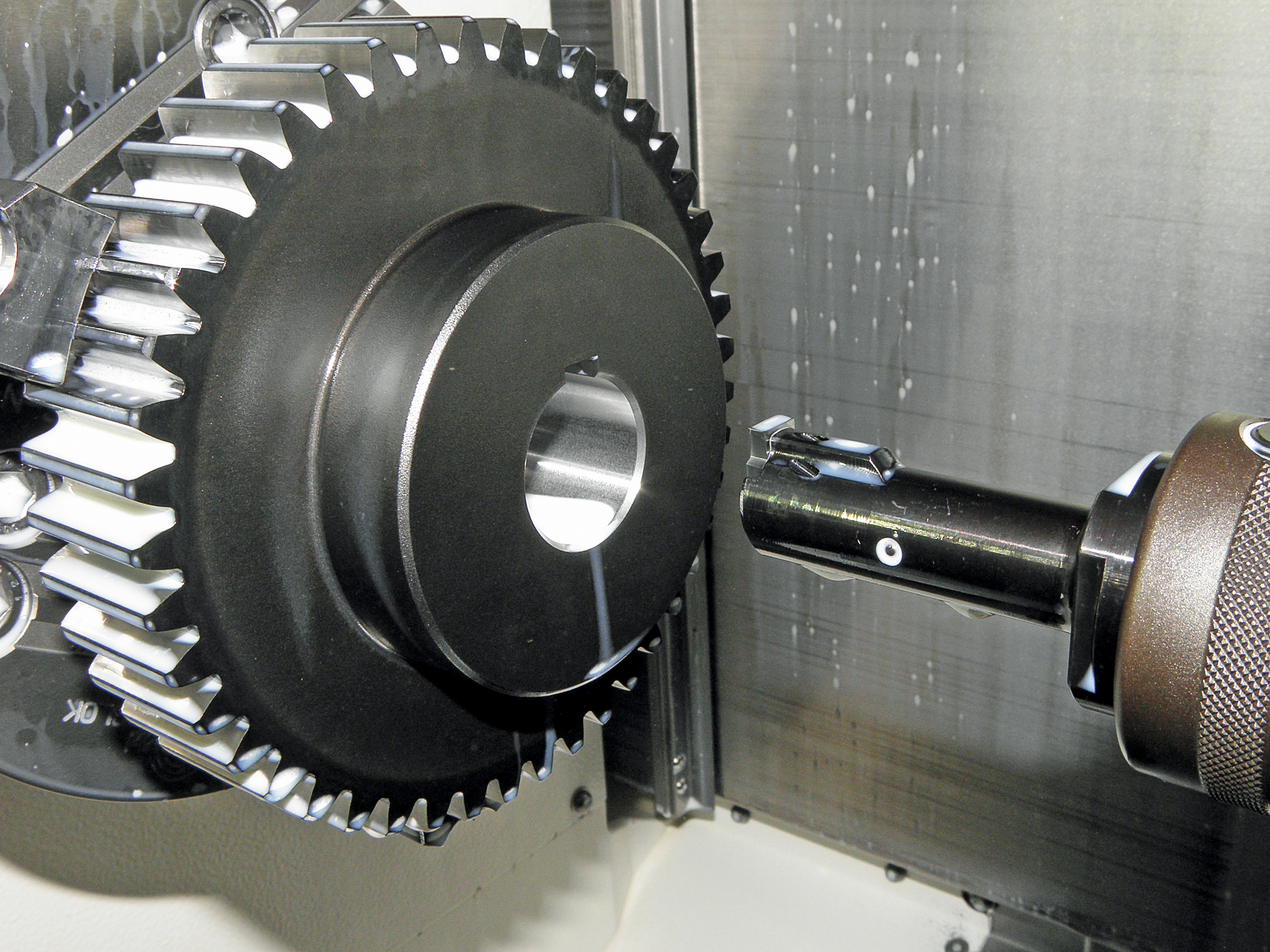
The gear receives its precise keyway while in the correct orientation.
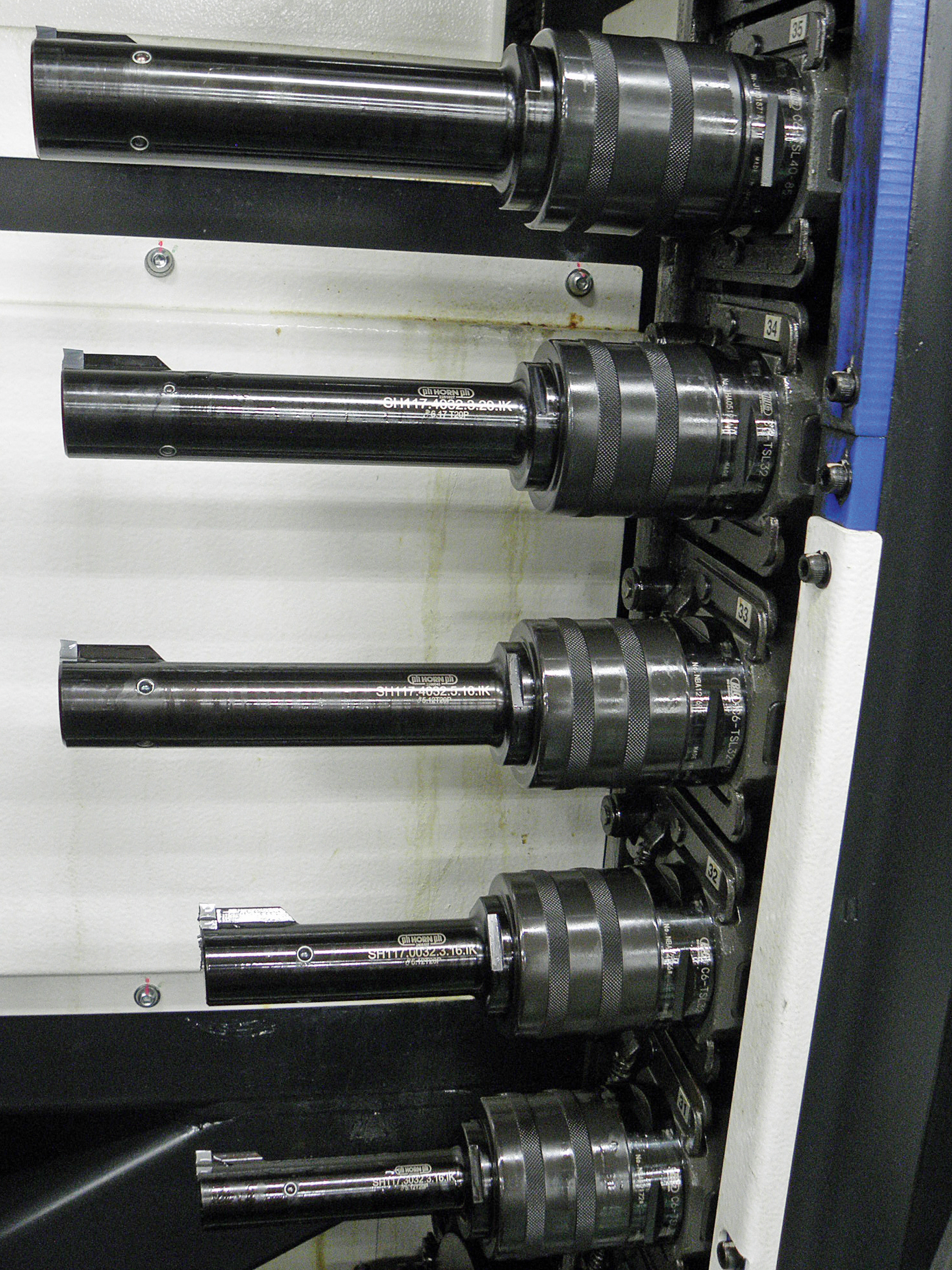
At Kohara, many widths across flats are produced in small to medium quantities during complete machining.
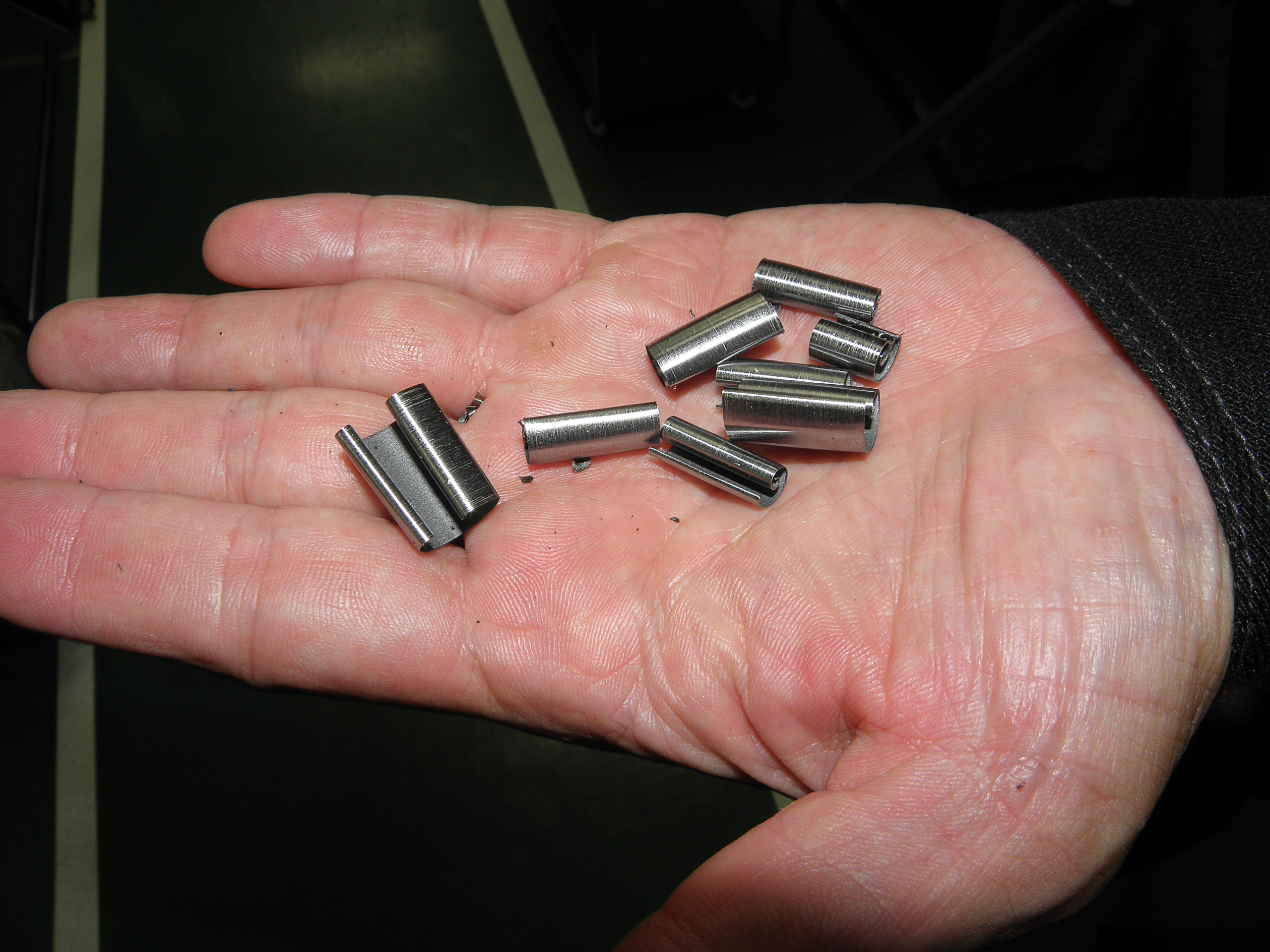
Smooth chips indicate the trouble-free process and the straight contours.
Broaching not only shortens the manufacturing process itself, but also eliminates the need for separate processes and additional work, thus enabling integrated complete machining on a single platform. This shortens production throughput time at KHK Kohara by nearly 60 percent. Kohara already uses 15 broaching tools from Horn for different groove widths, with further widths of 24, 32, 36 and 40 mm to follow. Each tool is available in multiples so that the machines on the shop floor can be used flexibly.
Tooling costs have also been significantly reduced through the use of inserts. KHK Kohara reports that the cost of a single insert has fallen by 41 percent. With a broad product programme and good utilisation of capacity, this is reflected in the profitability. In addition, the company greatly appreciates the fact that Horn supplies special tools very quickly. Those responsible at Kohara have carried out a detailed cost comparison and confirm that investment in the new Horn broaching process was fully amortised within just eight months.
Author:
Karl-Heinz Gies, Stuttgart
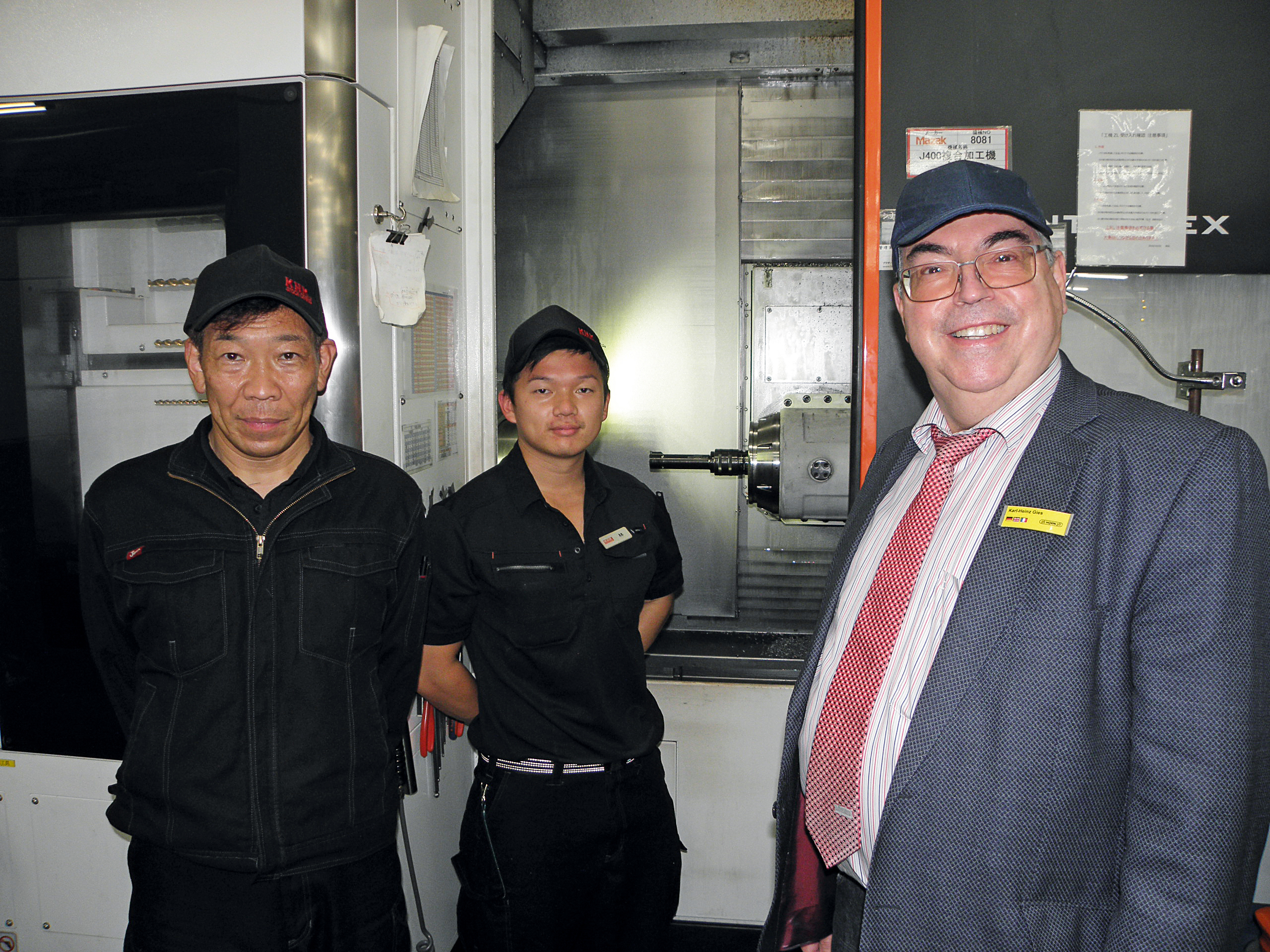
Karl-Heinz Gies, Horn’s Japan Coordinator, is also a welcome guest and advisor at Kohara’s production facility.
