Perfect Surface Finishes and Very Short Cycle Times Enable Electric Mobility
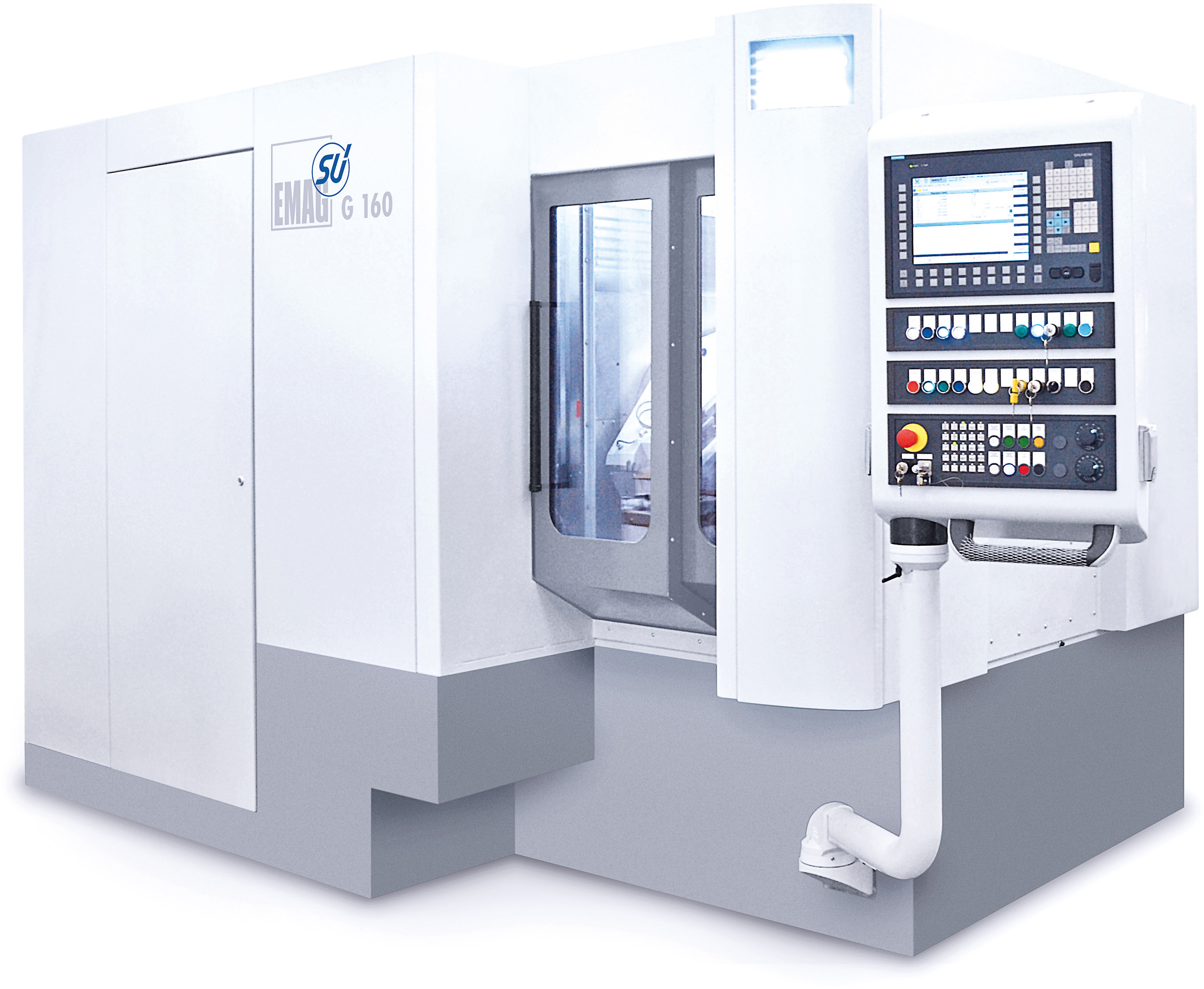
Gear grinding is currently attracting a lot of attention, especially in the production of components for electric drives. Production planners are demanding new solutions for a perfect surface that assures their necessarily smooth running at high speeds and heavy torque loads. To see how a high-tech niche machine builder implements these requirements, one need look no further than EMAG SU “tooth flank grinding” machines. The gear grinding machine specialist, based near Bologna Italy, developed the G 160 model, for example, which features a special “virtual” axis concept for microscopically near-perfect surfaces. At the same time, the integrated material handling technology keeps the cycle times down to a minimum. Take a look at the concept details that makes EMAG SU such an outstanding gear tooth flank grinding solution, as well as their many other winning designs.
Electromobility is booming and the competition to have the best solution is accelerating. Almost all automotive manufacturers launched new EV models in 2022. What does this mean for the production planning by OEMs and suppliers? “On the one hand, they have to effectively deal with growing production quantities, yet, still have to guarantee an ever-increasing level of quality, because the high torque load of an EV electric motor results in special requirements for tight tolerance dimensions and surface finish,” explains Alexander Morhard, Technical Gear Support Specialist with EMAG SU. “This development is particularly noticeable in the machining of tooth flanks…Abonnenteninhalt
Abonnieren Sie, um auf alle Inhalte
von Werkzeug Technik zuzugreifen
Bereits abonniert ? Einloggen
